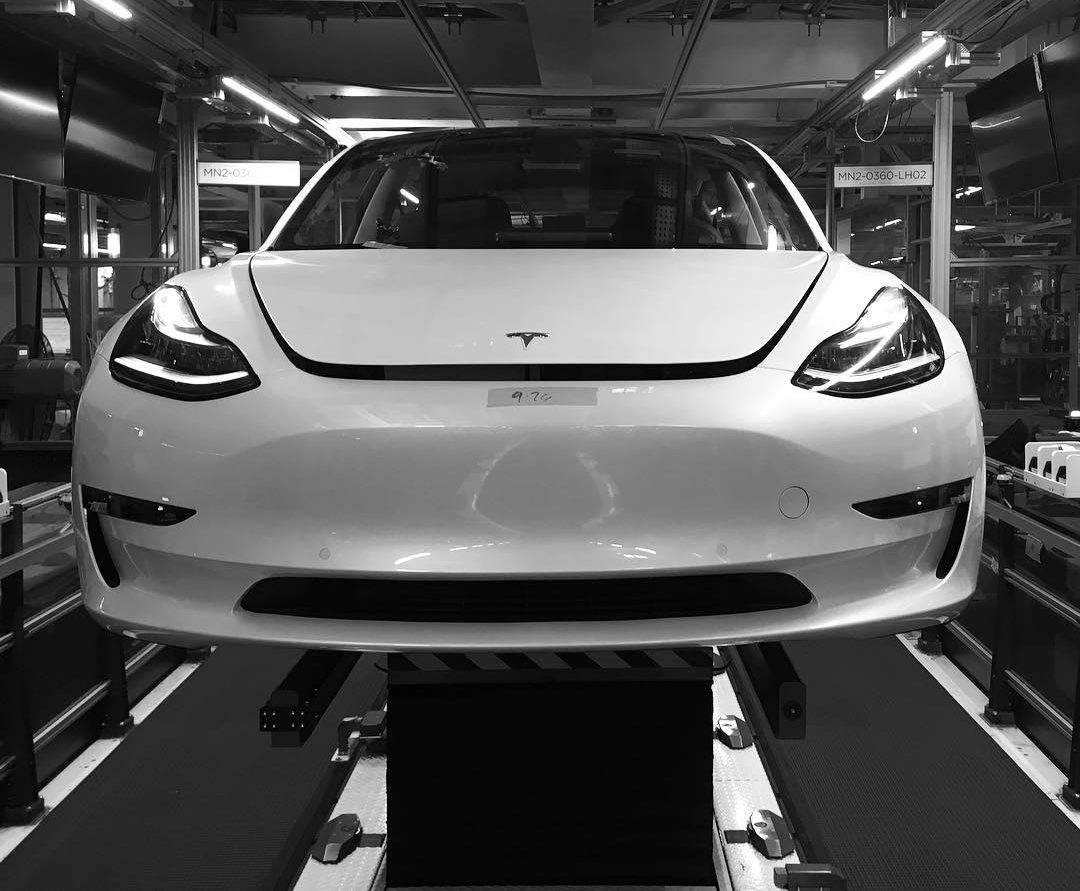
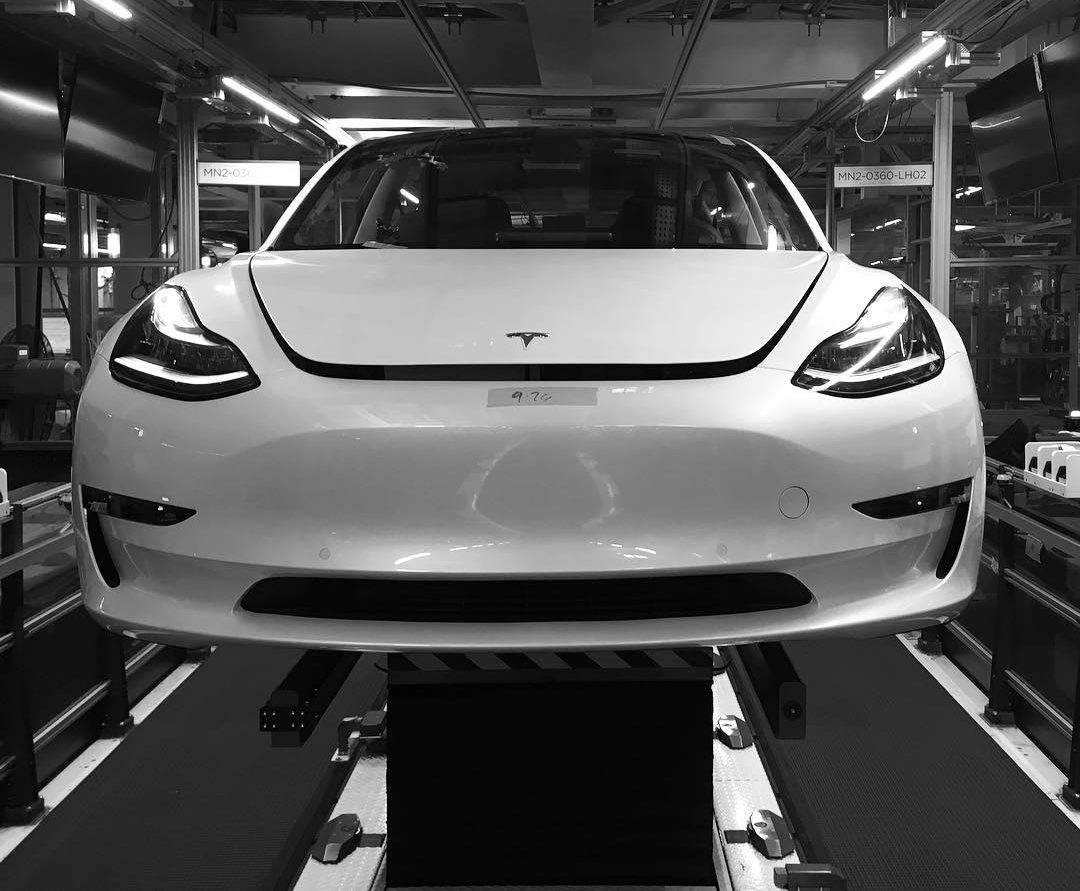
Investor's Corner
Tesla explains oversight on Model 3 production line automation
Following consistent delays in Model 3 production, Tesla is attempting to fine-tune their automation strategy to solve production bottlenecks. As noted in Tesla’s Q1 Earnings Report, the company is currently producing 2,270 Model 3’s per week, less than half of the 5,000/week goal they set for the end of June.
Even after Tesla CEO Elon Musk stated that humans were “underrated” and that “excessive automation at Tesla was a mistake,” Tesla is largely crediting quality improvements to their highly-automated production.
“We are already seeing many benefits from heavily increasing automation as part of the Model 3 production process. Through the vast majority of Model 3 production, including in body welding, general assembly, inverter and drive unit production, our automation effort has been very successful. Based on every measurable metric, Model 3 is already the highest quality vehicle we have ever produced, and this is unquestionably due in large part to automation,” Tesla stated in their Q1 Update Letter.
Despite early success with a large amount of the Model 3’s automated production line, Tesla is dialing back some of the processes. The company stated, “In those select areas where we have had challenges ramping fully automated processes, such as portions of the battery module line, part of the material flow system, and two steps of general assembly, we have temporarily dialed back automation and introduced certain semi-automated or manual processes while we work to eventually have full automation take back over.”
"Vast majority of production system is automated… but we went too far and automated some pretty silly things" Silliest item? "Basically placement 'fluff' on the top of the battery pack was automated with a 'fluff machine'" Super complex, used a vision system $TSLA @Teslarati
— Christian Prenzler (@clprenz) May 2, 2018
7 Hours to make a pack 3 weeks ago, now is 17 minutes – @elonmusk
We are slightly ahead in battery cell and module production, general assembly area is the source of some production delays. $TSLA @Teslarati— Christian Prenzler (@clprenz) May 2, 2018
Model 3 Simplified by Design
Tesla isn’t only banking on automated processes to ramp up production of the Model 3. The company also highlighted that the vehicle was designed to be easily mass-produced. Tesla stated that the vehicle’s assembly line consists of 70% less steps compared to traditional assembly lines.
The Model 3’s assembly line has 50 different steps and the vehicle is built on a singular body frame. By comparison, the Model S has over 80 different body frames. Tesla also cited that the vehicle has lighter wiring and fewer controllers, connectors, and CPUs compared to ‘average vehicles’.
As a result of the Model 3’s simplified design and highly-automated production line, Tesla expects the vehicle to carry a 25% gross margin, much higher than its peers.
“All these elements are rooted in design and critical not only to our ability to reach higher levels of output in a smaller amount of factory space but also to achieve lower levels of
cost,” Tesla stated.
It’s expected that Tesla will optimize the level of automation on the Model 3 line following a planned 10-day shutdown in production in the second quarter. With more people involved in vehicle production, Tesla can dynamically adjust overtime hours and staffing levels to meet line goals.
Investor's Corner
Tesla could save $2.5B by replacing 10% of staff with Optimus: Morgan Stanley
Jonas assigned each robot a net present value (NPV) of $200,000.
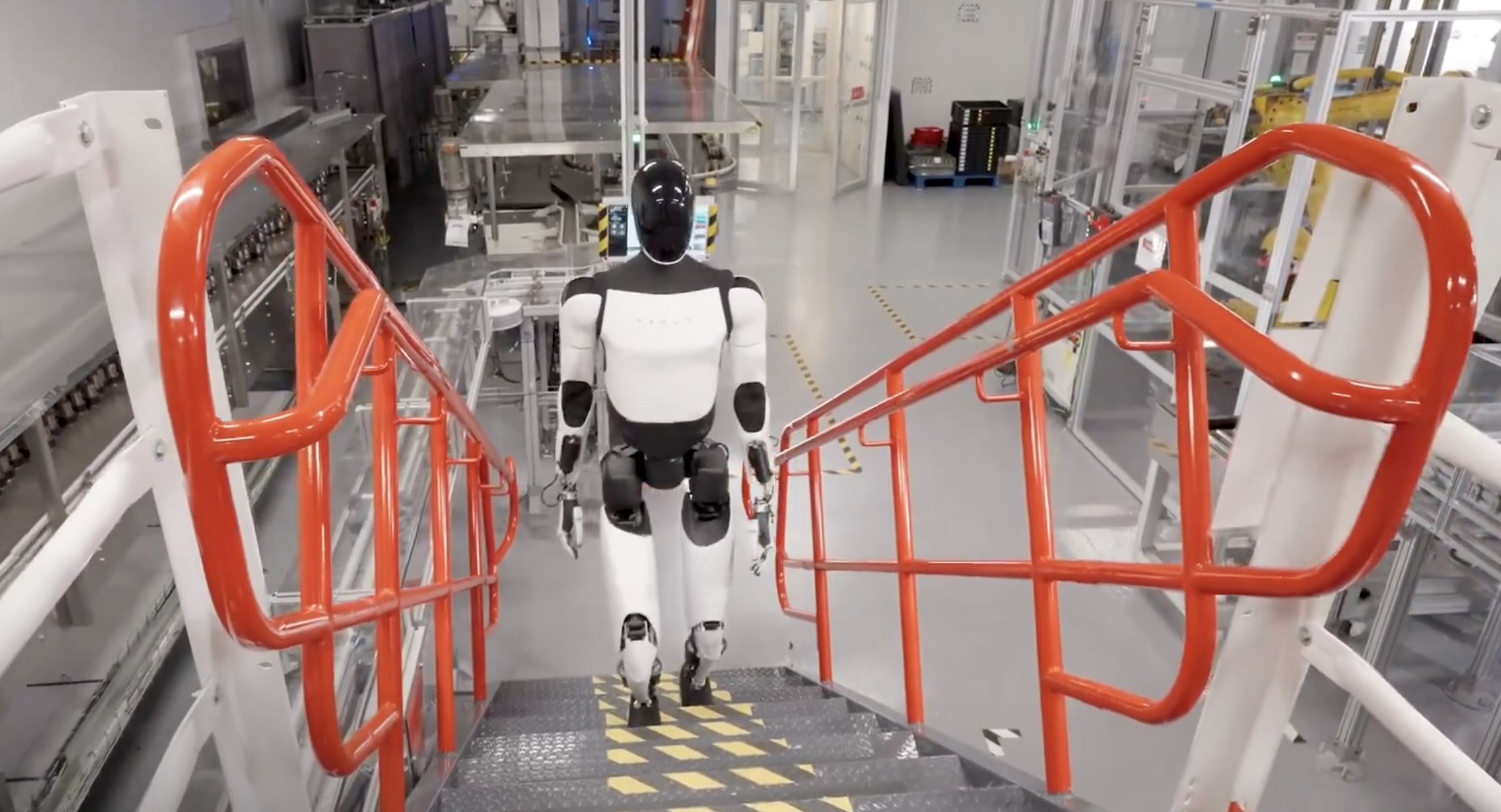
Tesla’s (NASDAQ:TSLA) near-term outlook may be clouded by political controversies and regulatory headwinds, but Morgan Stanley analyst Adam Jonas sees a glimmer of opportunity for the electric vehicle maker.
In a new note, the Morgan Stanley analyst estimated that Tesla could save $2.5 billion by replacing just 10% of its workforce with its Optimus robots, assigning each robot a net present value (NPV) of $200,000.
Morgan Stanley highlights Optimus’ savings potential
Jonas highlighted the potential savings on Tesla’s workforce of 125,665 employees in his note, suggesting that the utilization of Optimus robots could significantly reduce labor costs. The analyst’s note arrived shortly after Tesla reported Q2 2025 deliveries of 384,122 vehicles, which came close to Morgan Stanley’s estimate and slightly under the consensus of 385,086.
“Tesla has 125,665 employees worldwide (year-end 2024). On our calculations, a 10% substitution to humanoid at approximately ($200k NPV/humanoid) could be worth approximately $2.5bn,” Jonas wrote, as noted by Street Insider.
Jonas also issued some caution on Tesla Energy, whose battery storage deployments were flat year over year at 9.6 GWh. Morgan Stanley had expected Tesla Energy to post battery storage deployments of 14 GWh in the second quarter.
Musk’s political ambitions
The backdrop to Jonas’ note included Elon Musk’s involvement in U.S. politics. The Tesla CEO recently floated the idea of launching a new political party, following a poll on X that showed support for the idea. Though a widely circulated FEC filing was labeled false by Musk, the CEO does seem intent on establishing a third political party in the United States.
Jonas cautioned that Musk’s political efforts could divert attention and resources from Tesla’s core operations, adding near-term pressure on TSLA stock. “We believe investors should be prepared for further devotion of resources (financial, time/attention) in the direction of Mr. Musk’s political priorities which may add further near-term pressure to TSLA shares,” Jonas stated.
Investor's Corner
Two Tesla bulls share differing insights on Elon Musk, the Board, and politics
Two noted Tesla bulls have shared differing views on the recent activities of CEO Elon Musk and the company’s leadership.
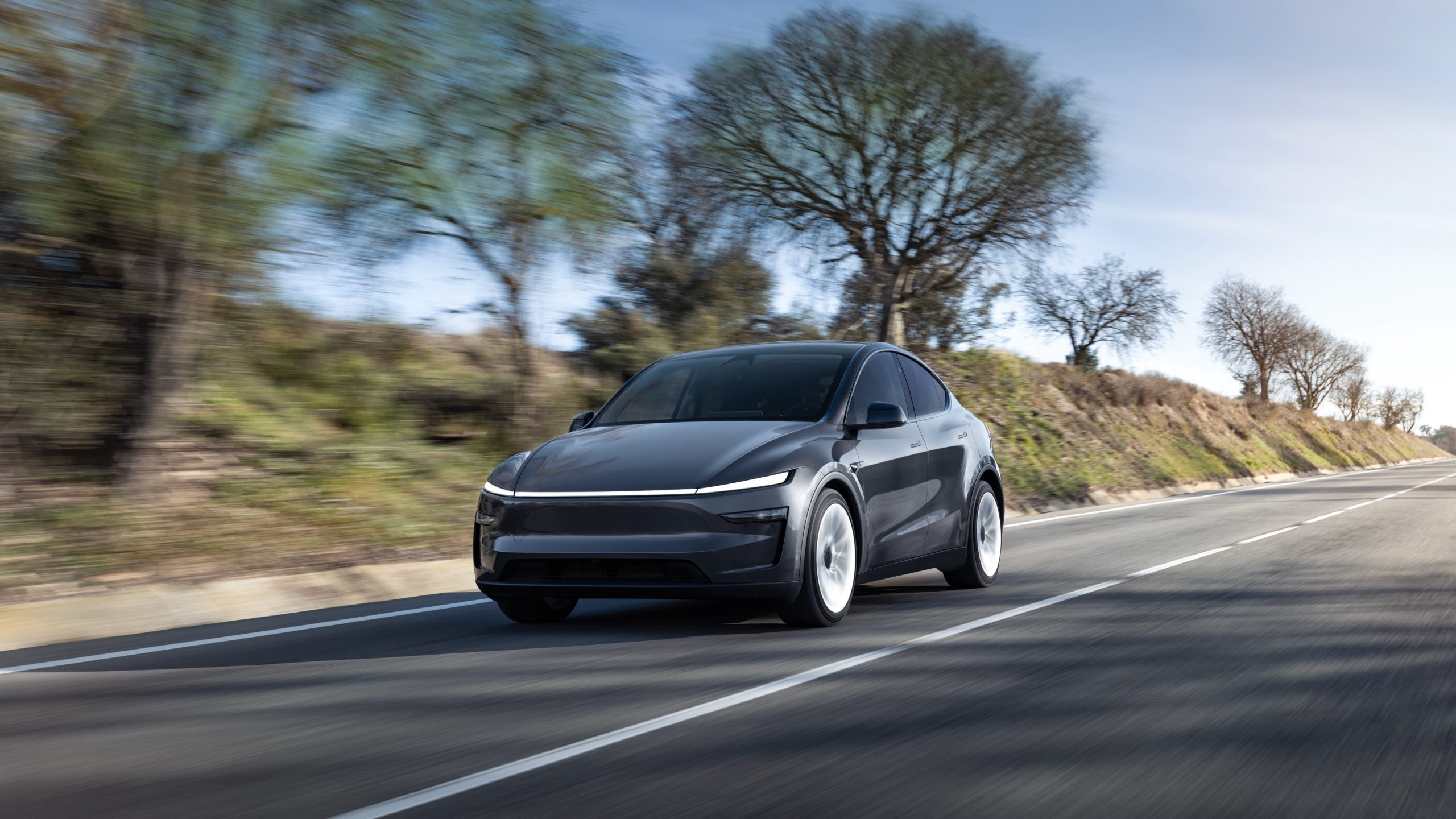
Two noted Tesla (NASDAQ:TSLA) bulls have shared differing views on the recent activities of CEO Elon Musk and the company’s leadership.
While Wedbush analyst Dan Ives called on Tesla’s board to take concrete steps to ensure Musk remains focused on the EV maker, longtime Tesla supporter Cathie Wood of Ark Invest reaffirmed her confidence in the CEO and the company’s leadership.
Ives warns of distraction risk amid crucial growth phase
In a recent note, Ives stated that Tesla is at a critical point in its history, as the company is transitioning from an EV maker towards an entity that is more focused on autonomous driving and robotics. He then noted that the Board of Directors should “act now” and establish formal boundaries around Musk’s political activities, which could be a headwind on TSLA stock.
Ives laid out a three-point plan that he believes could ensure that the electric vehicle maker is led with proper leadership until the end of the decade. First off, the analyst noted that a new “incentive-driven pay package for Musk as CEO that increases his ownership of Tesla up to ~25% voting power” is necessary. He also stated that the Board should establish clear guidelines for how much time Musk must devote to Tesla operations in order to receive his compensation, and a dedicated oversight committee must be formed to monitor the CEO’s political activities.
Ives, however, highlighted that Tesla should move forward with Musk at its helm. “We urge the Board to act now and move the Tesla story forward with Musk as CEO,” he wrote, reiterating its Outperform rating on Tesla stock and $500 per share price target.
Tesla CEO Elon Musk has responded to Ives’ suggestions with a brief comment on X. “Shut up, Dan,” Musk wrote.
Cathie Wood reiterates trust in Musk and Tesla board
Meanwhile, Ark Investment Management founder Cathie Wood expressed little concern over Musk’s latest controversies. In an interview with Bloomberg Television, Wood said, “We do trust the board and the board’s instincts here and we stay out of politics.” She also noted that Ark has navigated Musk-related headlines since it first invested in Tesla.
Wood also pointed to Musk’s recent move to oversee Tesla’s sales operations in the U.S. and Europe as evidence of his renewed focus in the electric vehicle maker. “When he puts his mind on something, he usually gets the job done,” she said. “So I think he’s much less distracted now than he was, let’s say, in the White House 24/7,” she said.
TSLA stock is down roughly 25% year-to-date but has gained about 19% over the past 12 months, as noted in a StocksTwits report.
Investor's Corner
Cantor Fitzgerald maintains Tesla (TSLA) ‘Overweight’ rating amid Q2 2025 deliveries
Cantor Fitzgerald is holding firm on its bullish stance for the electric vehicle maker.
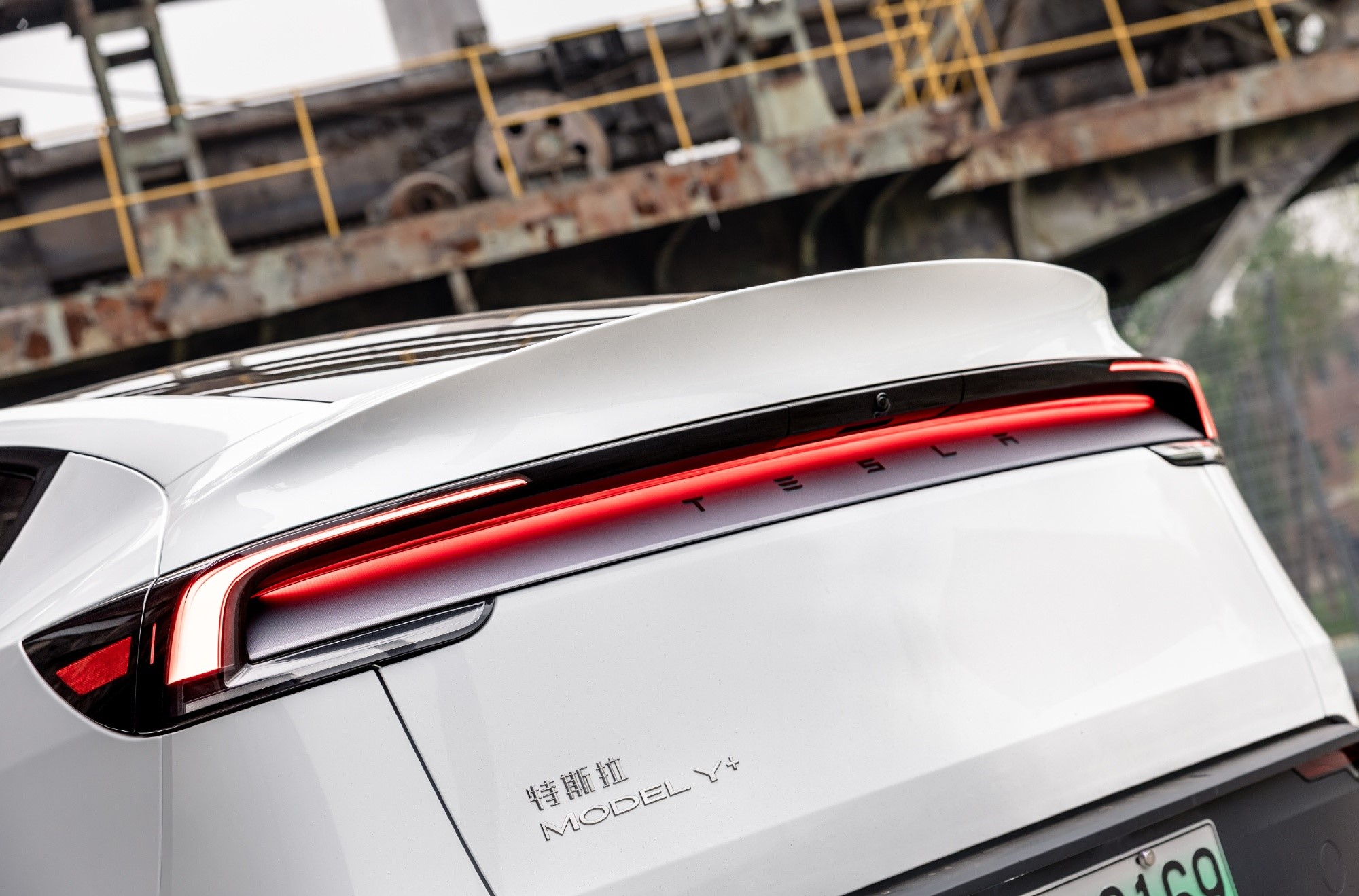
Cantor Fitzgerald is holding firm on its bullish stance for Tesla (NASDAQ: TSLA), reiterating its “Overweight” rating and $355 price target amidst the company’s release of its Q2 2025 vehicle delivery and production report.
Tesla delivered 384,122 vehicles in Q2 2025, falling below last year’s Q2 figure of 443,956 units. Despite softer demand in some countries in Europe and ongoing controversies surrounding CEO Elon Musk, the firm maintained its view that Tesla is a long-term growth story in the EV sector.
Tesla’s Q2 results
Among the 384,122 vehicles that Tesla delivered in the second quarter, 373,728 were Model 3 and Model Y. The remaining 10,394 units were attributed to the Model S, Model X, and Cybertruck. Production was largely flat year-over-year at 410,244 units.
In the energy division, Tesla deployed 9.6 GWh of energy storage in Q2, which was above last year’s 9.4 GWh. Overall, Tesla continues to hold a strong position with $95.7 billion in trailing twelve-month revenue and a 17.7% gross margin, as noted in a report from Investing.com.
Tesla’s stock is still volatile
Tesla’s market cap fell to $941 billion on Monday amid volatility that was likely caused in no small part by CEO Elon Musk’s political posts on X over the weekend. Musk has announced that he is forming the America Party to serve as a third option for voters in the United States, a decision that has earned the ire of U.S. President Donald Trump.
Despite Musk’s controversial nature, some analysts remain bullish on TSLA stock. Apart from Cantor Fitzgerald, Canaccord Genuity also reiterated its “Buy” rating on Tesla shares, with the firm highlighting the company’s positive Q2 vehicle deliveries, which exceeded its expectations by 24,000 units. Cannacord also noted that Tesla remains strong in several markets despite its year-over-year decline in deliveries.
-
Elon Musk2 weeks ago
Tesla investors will be shocked by Jim Cramer’s latest assessment
-
Elon Musk2 days ago
xAI launches Grok 4 with new $300/month SuperGrok Heavy subscription
-
Elon Musk4 days ago
Elon Musk confirms Grok 4 launch on July 9 with livestream event
-
News1 week ago
Tesla Model 3 ranks as the safest new car in Europe for 2025, per Euro NCAP tests
-
Elon Musk2 weeks ago
A Tesla just delivered itself to a customer autonomously, Elon Musk confirms
-
Elon Musk1 week ago
xAI’s Memphis data center receives air permit despite community criticism
-
News2 weeks ago
Xiaomi CEO congratulates Tesla on first FSD delivery: “We have to continue learning!”
-
News2 weeks ago
Tesla sees explosive sales growth in UK, Spain, and Netherlands in June