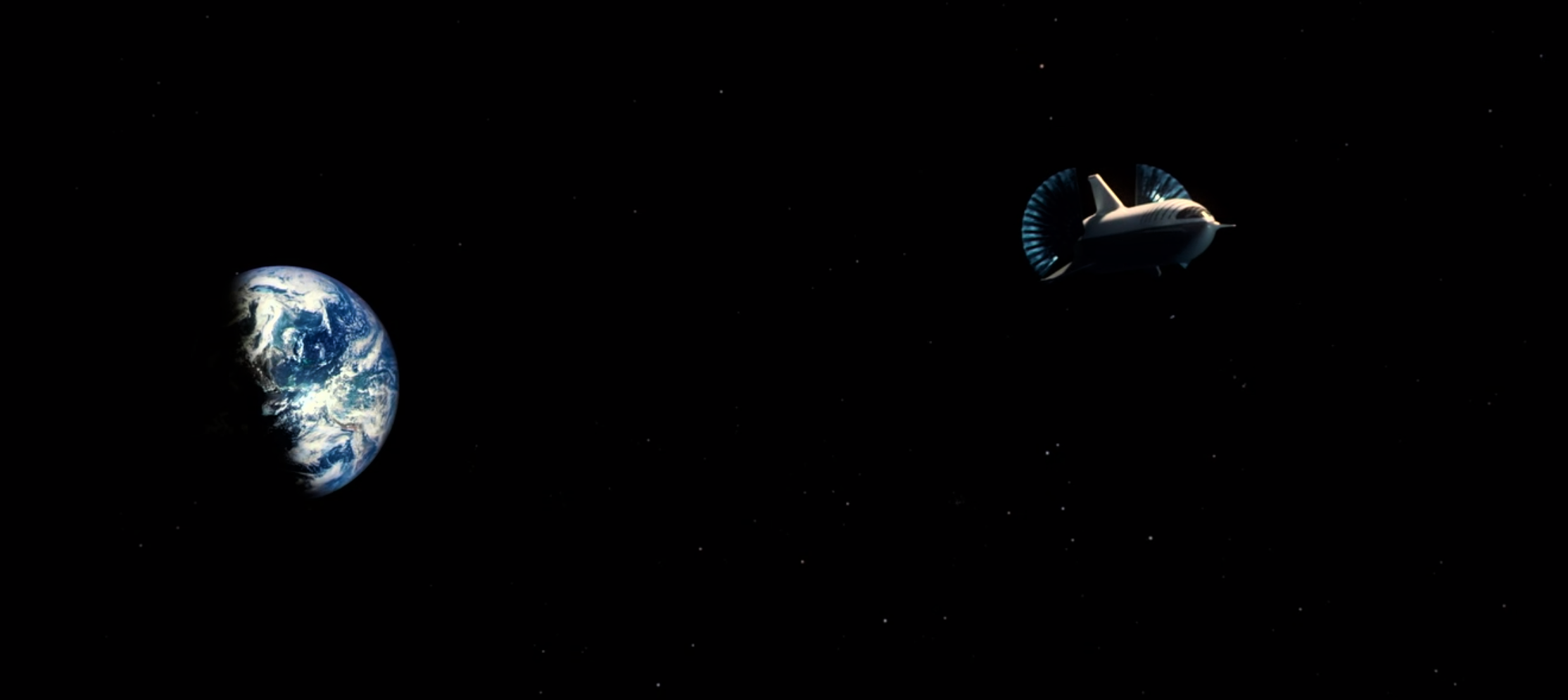
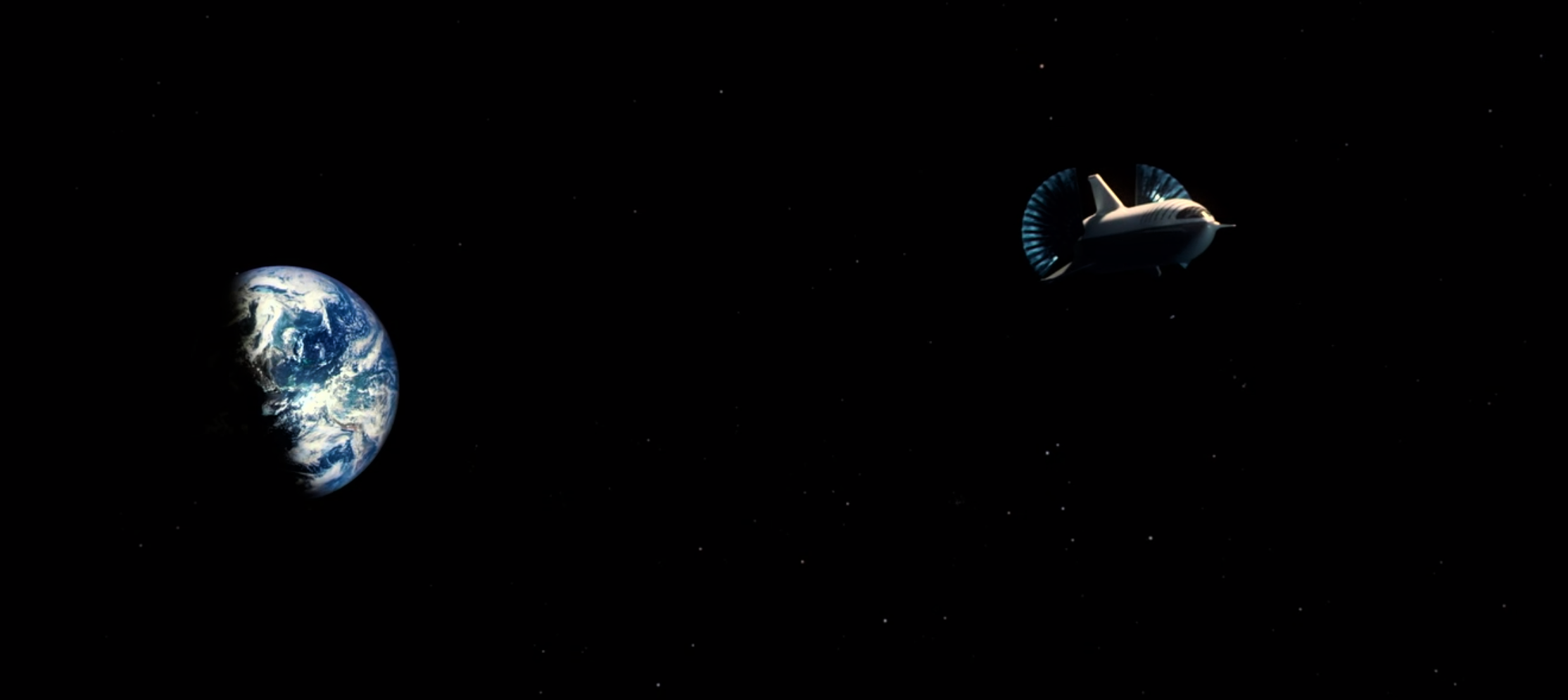
News
SpaceX CEO Elon Musk kills mini BFR spaceship 12 days after announcing it
Less than two weeks after SpaceX CEO Elon Musk announced that Falcon 9’s “second stage [would] be upgraded…like a mini-BFR Ship” to prove lightweight heatshield and hypersonic control surface technologies, Musk took to Twitter to assert that the mini BFR spaceship project was dead, despite having stated that SpaceX was working to launch that test article into orbit as early as June 2019 just 12 days prior.
From a public perspective, the status of SpaceX’s next-gen rocket program (known as BFR) is effectively up in the air after several cryptic and seemingly contradictory statements from the company’s CEO and chief engineer.
No, we’re just going to accelerate BFR
— Elon Musk (@elonmusk) November 20, 2018
On Nov. 17, Musk tweeted that BFR – last updated in September 2018 alongside a statement that “this is [likely] the the final iteration [of BFR] in terms of broad architectural decisions” – had already been redesigned, going so far as to describe it as a “radical change”. What that radical design change might be is almost entirely unclear, although Musk has now twice stated that the purpose of these changes (and the whiplash-inducing cancellation of the mini-spaceship) is to “accelerate BFR”.
Radical change
— Elon Musk (@elonmusk) November 17, 2018
As of now, SpaceX appears to have just completed a massive 9-meter diameter composite tank dome in the company’s temporary Port of Los Angeles tent, where a small but growing team of engineers and technicians are working to realize some version of the company’s next-generation rocket. That group has been working in near-silence for the better part of a year and has accepted delivery of and set up a wide range of custom-built tooling for carbon composite fabrication, and has even managed to get that tooling producing massive composite parts that are expected to eventually make up the structure of a spaceship prototype.
That prototype would eventually be shipped to South Texas, where SpaceX is constructing an entirely new facility from scratch to test the design, technology, and operation of the first full-scale BFR spaceship (BFS). As of a few months ago, the plan was to begin those hop tests before the end of 2019, but it’s no longer clear if SpaceX still intends to build a prototype spaceship to conduct hops and high-speed, high-altitude test flights.
- BFR’s spaceship design, as of 2018. (SpaceX)
- A BFS attempts a Mars landing in this official updated render. (SpaceX)
- SpaceX’s huge Port of LA-based BFR tent, September 18th. (Pauline Acalin)
- SpaceX’s first BFR spaceship prototype is coming together piece by piece. (SpaceX/Pauline Acalin)
Responsibly building giant rockets
One can only hope that the SpaceX employees tasked with bringing an already monumentally difficult idea from concept to reality are learning about these earth-shaking, “radical” decisions and changes through a medium other than Twitter. If those senior engineers and technicians are not extensively forewarned and given some say in these major system-wide decisions, it’s hard to exaggerate the amount of time, effort, and resources potentially being wasted (or at least misdirected).
There is undoubtedly something to be said for getting complex and difficult things as right as possible on the first serious try, especially when the sheer expense of the task at hand might mean that there is only one real chance to try. Still, it’s not particularly encouraging when a three-year-old hardware development program marked by several major design iterations is still experiencing anything close to “radical change”. After multiple years of concerted effort, BFR still appears to be in some sort of design limbo, where a constant and haphazard stream of on-paper changes act as a near-insurmountable hurdle standing in the way of a completed “good enough” blueprint that can begin to be made real.
Ultimately, even if some of the worst-case scenarios described above turn out to be true, there are still many, many reasons to remain positive about SpaceX’s BFR program on the whole. The next-gen rocket’s propulsion system of choice – an advanced engine known as Raptor – is quite mature at this point and may already be nearing initial flight readiness. Regardless of any future changes to BFR’s overall spaceship and booster structures, SpaceX technicians, engineers, and material scientists have likely gained invaluable experience in pursuit of an unprecedented 9-meter diameter rocket built almost entirely out of carbon fiber composites.
Further, it appears that quite a bit of progress has been made over the course of R&D programs related to methane-oxygen RCS thrusters (Falcon uses nitrogen), autogenous tank pressurization with gaseous methane and oxygen (Falcon uses helium), and perhaps even in-situ resource utilization (ISRU) that will be an absolute necessity to generate water, oxygen, and methane that will keep prospective Mars colonists alive and refuel spaceships for the voyage back to Earth.
- SpaceX’s horizontal Raptor test stand is pictured here in April 2018. A prototype Raptor can be seen in the center bay. (Aero Photo/Teslarati)
- A new rocket test-stand takes shape at SpaceX’s McGregor, TX facilities. As of just a few months ago, this site was effectively barren of activity. (April 17, Aero Photo)
- SpaceX’s Boca Chica facilities now sport two massive propellant tanks, meant to support BFR spaceship hop tests. (NSF /u/ bocachicagal, SpaceX)
For prompt updates, on-the-ground perspectives, and unique glimpses of SpaceX’s rocket recovery fleet check out our brand new LaunchPad and LandingZone newsletters!
News
Tesla begins Robotaxi certification push in Arizona: report
Tesla seems serious about expanding its Robotaxi service to several states in the coming months.
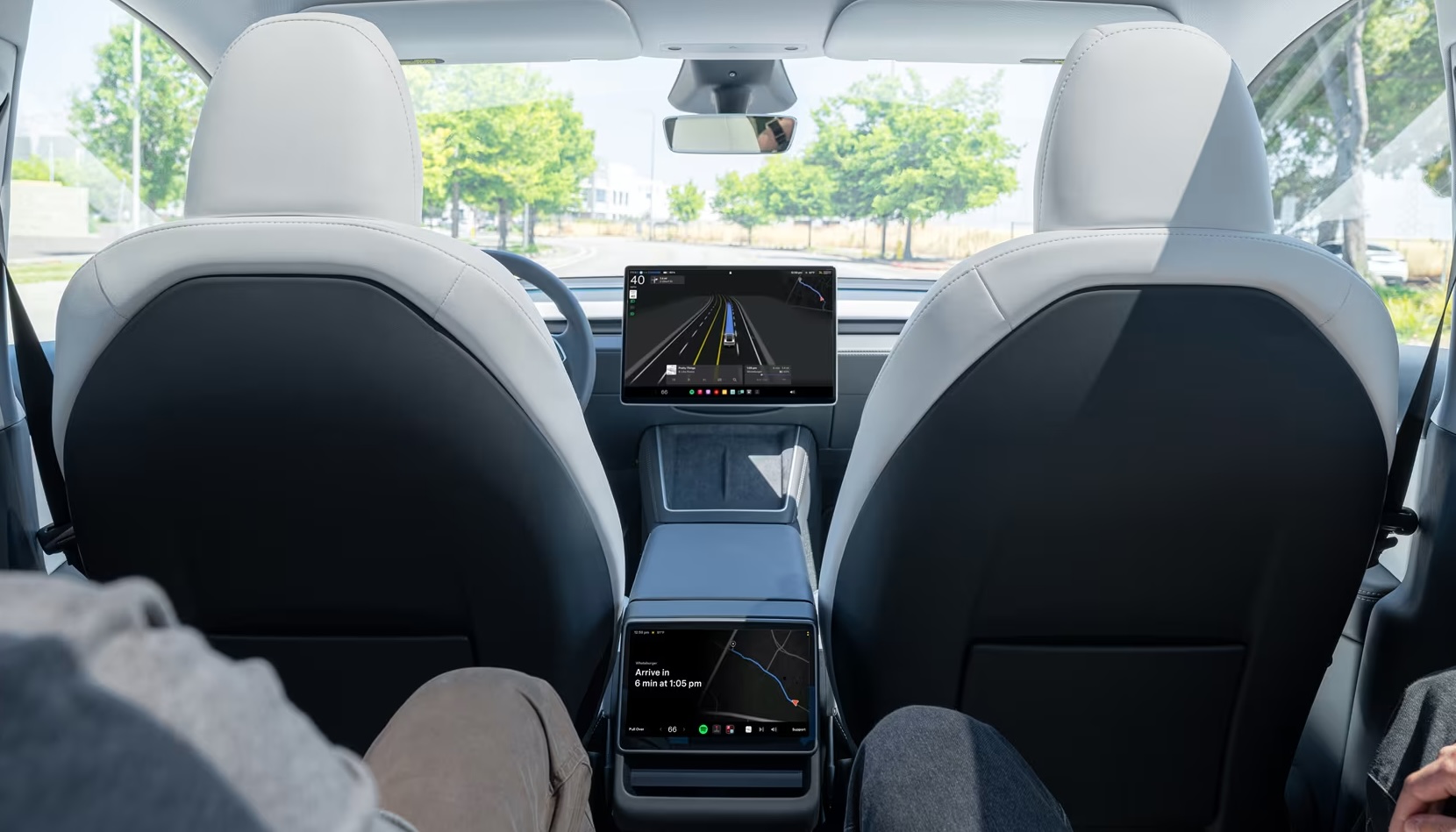
Tesla has initiated discussions with Arizona transportation regulators to certify its driverless Robotaxi service in the state, as per a recent report from Bloomberg News. The move follows Tesla’s launch of its Robotaxi pilot program in Austin, Texas, as well as CEO Elon Musk’s recent comments about the service’s expansion in the Bay Area.
The Arizona Department of Transportation confirmed to Bloomberg that Tesla has reached out to begin the certification process for autonomous ride-sharing operations in the state. While details remain limited, the outreach suggests that Tesla is serious about expanding its driverless Robotaxi service to several territories in the coming months.
The Arizona development comes as Tesla prepares to expand its service area in Austin this weekend, as per CEO Elon Musk in a post on X. Musk also stated that Tesla is targeting the San Francisco Bay Area as its next major market, with a potential launch “in a month or two,” pending regulatory approvals.
Tesla first launched its autonomous ride-hailing program on June 22 in Austin with a small fleet of Model Y vehicles, accompanied by a Tesla employee in the passenger seat to monitor safety. While still classified as a test, Musk has said the program will expand to about 1,000 vehicles in the coming months. Tesla will later upgrade its Robotaxi fleet with the Cyercab, a two-seater that is designed without a steering wheel.
Sightings of Cybercab castings around the Giga Texas complex suggests that Tesla may be ramping the initial trial production of the self-driving two-seater. Tesla, for its part, has noted in the past that volume production of the Cybercab is expected to start sometime next year.
In California, Tesla has already applied for a transportation charter-party carrier permit from the state’s Public Utilities Commission. The company is reportedly taking a phased approach to operating in California, with the Robotaxi service starting with pre-arranged rides for employees in vehicles with safety drivers.
News
Tesla sets November 6 date for 2025 Annual Shareholder Meeting
The automaker announced the date on Thursday in a Form 8-K.
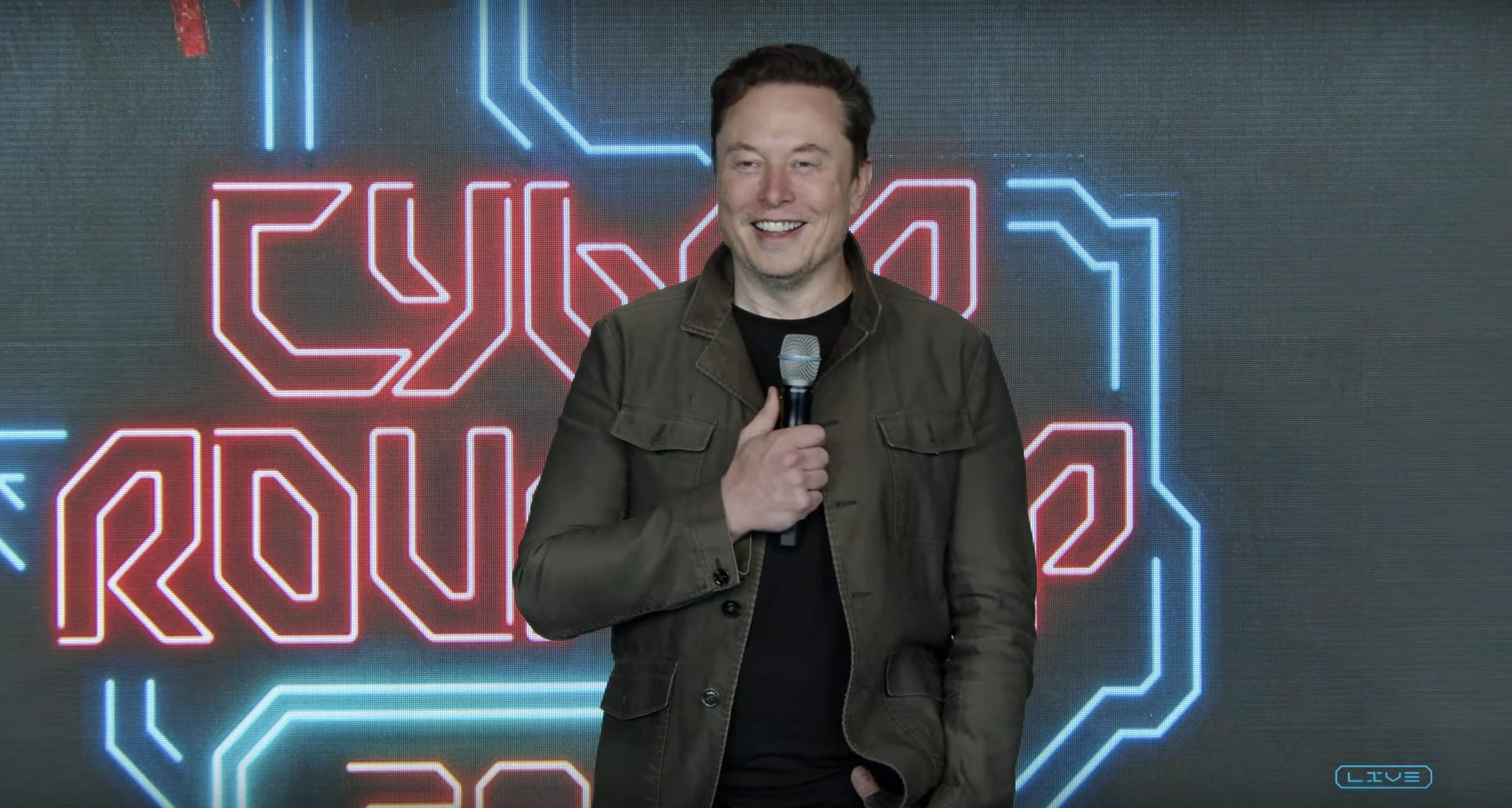
Tesla has scheduled its 2025 annual shareholder meeting for November 6, addressing investor concerns that the company was nearing a legal deadline to hold the event.
The automaker announced the date on Thursday in a Form 8-K submitted to the United States Securities and Exchange Commission (SEC). The company also listed a new proposal submission deadline of July 31 for items to be included in the proxy statement.
Tesla’s announcement followed calls from a group of 27 shareholders, including the leaders of large public pension funds, which urged Tesla’s board to formally set the meeting date, as noted in a report from The Wall Street Journal.
The group noted that under Texas law, where Tesla is now incorporated, companies must hold annual meetings within 13 months of the last one if requested by shareholders. Tesla’s previous annual shareholder meeting was held on June 13, 2024, which placed the July 13 deadline in focus.
Tesla originally stated in its 2024 annual report that it would file its proxy statement by the end of April. However, an amended filing on April 30 indicated that the Board of Directors had not yet finalized a meeting date, at least at the time.
The April filing also confirmed that Tesla’s board had formed a special committee to evaluate certain matters related to CEO Elon Musk’s compensation plan. Musk’s CEO performance award remains at the center of a lengthy legal dispute in Delaware, Tesla’s former state of incorporation.
Due to the aftermath of Musk’s legal dispute about his compensation plan in Delaware, he has not been paid for his work at Tesla for several years. Musk, for his part, has noted that he is more concerned about his voting stake in Tesla than his actual salary.
At last year’s annual meeting, TSLA shareholders voted to reapprove Elon Musk’s compensation plan and ratified Tesla’s decision to relocate its legal domicile from Delaware to Texas.
Elon Musk
Grok coming to Tesla vehicles next week “at the latest:” Elon Musk
Grok’s rollout to Tesla vehicles is expected to begin next week at the latest.
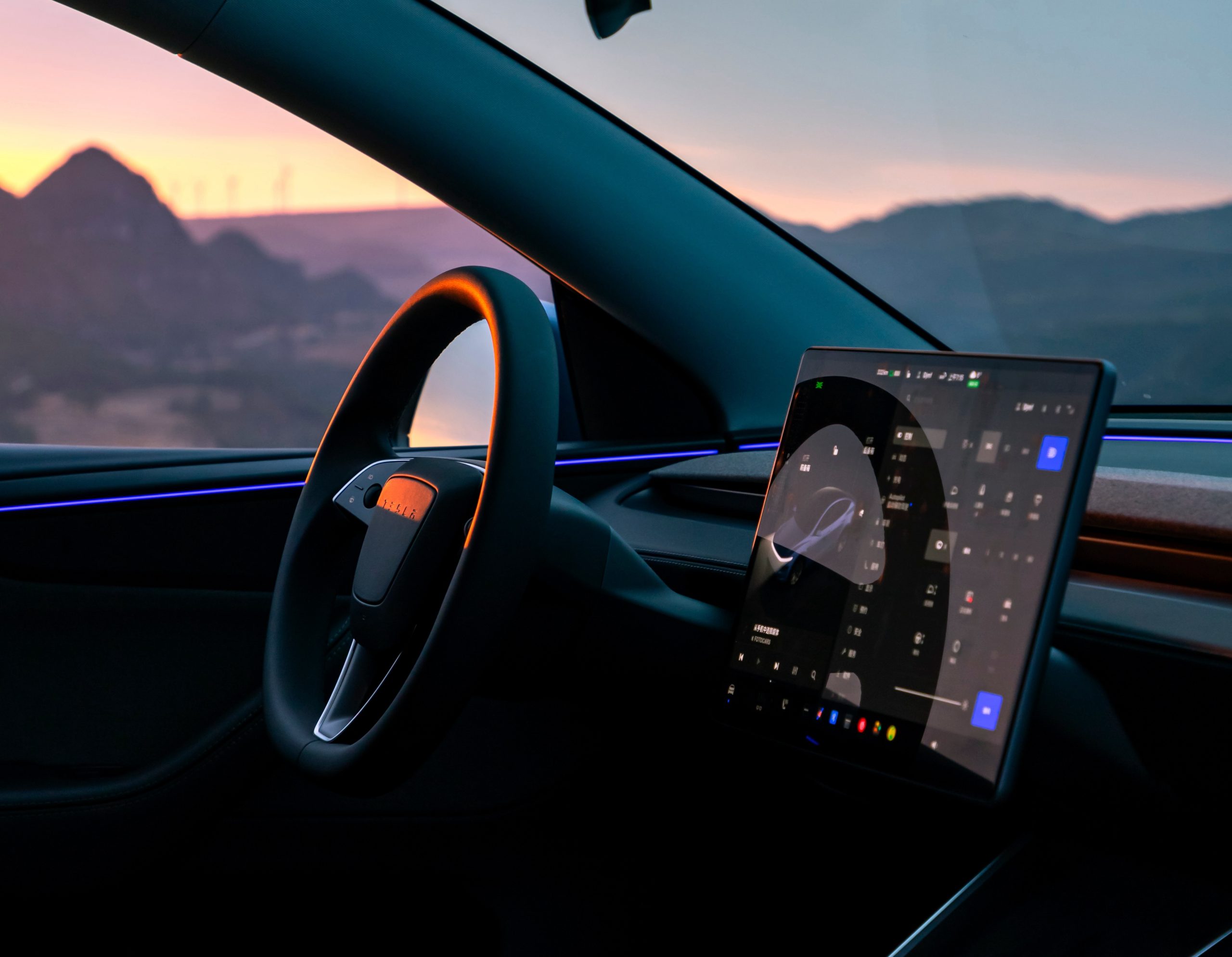
Elon Musk announced on Thursday that Grok, the large language model developed by his startup xAI, will soon be available in Tesla vehicles. Grok’s rollout to Tesla vehicles is expected to begin next week at the latest, further deepening the ties between the two Elon Musk-led companies.
Tesla–xAI synergy
Musk confirmed the news on X shortly after livestreaming the release of Grok 4, xAI’s latest large language model. “Grok is coming to Tesla vehicles very soon. Next week at the latest,” Musk wrote in a post on social media platform X.
During the livestream, Musk and several members of the xAI team highlighted several upgrades to Grok 4’s voice capabilities and performance metrics, positioning the LLM as competitive with top-tier models from OpenAI and Google.
The in-vehicle integration of Grok marks a new chapter in Tesla’s AI development. While Tesla has long relied on in-house systems for autonomous driving and energy optimization, Grok’s integration would introduce conversational AI directly into its vehicles’ user experience. This integration could potentially improve customer interaction inside Tesla vehicles.
xAI and Tesla’s collaborative footprint
Grok’s upcoming rollout to Tesla vehicles adds to a growing business relationship between Tesla and xAI. Earlier this year, Tesla disclosed that it generated $198.3 million in revenue from commercial, consulting, and support agreements with xAI, as noted in a report from Bloomberg News. A large portion of that amount, however, came from the sale of Megapack energy storage systems to the artificial intelligence startup.
In July 2023, Musk polled X users about whether Tesla should invest $5 billion in xAI. While no formal investment has been made so far, 68% of poll participants voted yes, and Musk has since stated that the idea would be discussed with Tesla’s board.
-
Elon Musk1 week ago
Tesla investors will be shocked by Jim Cramer’s latest assessment
-
Elon Musk3 days ago
Elon Musk confirms Grok 4 launch on July 9 with livestream event
-
Elon Musk14 hours ago
xAI launches Grok 4 with new $300/month SuperGrok Heavy subscription
-
News7 days ago
Tesla Model 3 ranks as the safest new car in Europe for 2025, per Euro NCAP tests
-
Elon Musk2 weeks ago
A Tesla just delivered itself to a customer autonomously, Elon Musk confirms
-
Elon Musk1 week ago
xAI’s Memphis data center receives air permit despite community criticism
-
Elon Musk2 weeks ago
Tesla’s Omead Afshar, known as Elon Musk’s right-hand man, leaves company: reports
-
News2 weeks ago
Xiaomi CEO congratulates Tesla on first FSD delivery: “We have to continue learning!”