News
SpaceX Starship outfitted with Tesla battery packs and motors
Following in the footsteps of the late Mk1 vehicle, SpaceX’s latest Starship prototype has been outfitted with several Tesla battery packs and motors over the last few weeks.
CEO Elon Musk has confirmed in the past that SpaceX intends to try to use Tesla batteries to power Starship rockets and Tesla motors to drive the ships’ large aerodynamic control surfaces. By all appearances, a Tesla Model S motor’s appearance on the exterior of a Starship prototype recently moved to the launch pad is a first for SpaceX. However, in 2019, SpaceX at one point planned to use and even installed battery packs on Starship Mk1 components before the ship was prematurely destroyed during testing. The nosecone those battery packs were installed in still sits in the middle of SpaceX’s growing Boca Chica rocket factory.
For Starship SN3, the purpose of its ~200 kWh of battery power is rather self-explanatory. The purpose of the Tesla Model S motor recently installed on its side is much less clear.
SpaceX is in the midst of preparing Starship SN3 for its first tests after assembling the rocket from next to nothing in less than a month. SpaceX transported the building-sized prototype a mile down the road to its Boca Chica launch site on March 29th, where dozens of workers have been poring over it day and night ever since. SpaceX originally wanted to attempt the ship’s first two tests yesterday, April 1st, but the scheduled times have come and gone while work continues. Several backup windows are ready on April 2nd, beginning shortly before this article went live (1am CDT, 06:00 UTC).
Regardless, with any rocket prototype, test schedules can be extremely fluid and are always liable to change. While SpaceX relies heavily on agile development strategies, beginning with a minimum viable product and iterating to something approaching feature-complete, there is some value in not turning the “move fast and break stuff” dial to 100%. In the case of Starship, the equivalent of tens to hundreds of thousands of work hours and several million dollars of hardware go into each prototype – incredibly cheap on the scale of aerospace development norms but still a significant chunk of change and effort. A few days or weeks of delays are an annoyance that can be suffered if it better guarantees a successful test, versus the alternative of potentially rushing and cutting corners.
SpaceX is now up to roughly five days of delays while preparing Starship SN3 for testing. Originally scheduled as early as April 1st, SpaceX has moved a planned Raptor engine static fire test to no earlier than (NET) April 6th, to be followed no fewer than several days later by a 150m (500 ft) hop test. Of course, before it can safely attempt its first static fire (or hop), SpaceX needs to verify that Starship SN3 – finished just days ago – is up to the task.
Enter Tesla hardware. During ground testing, Starship will likely be continuously connected to ground power sources. It’s also possible that SpaceX has chosen to use its Tesla battery packs as the main power source to insulate it from local outages. Either way, if or when Starship SN3 makes it to flight tests, the battery packs would power the ship’s onboard avionics, landing legs, and any other necessary equipment. That latter category may be where Starship’s apparent Model S motor comes in.

While it could simply be an early implementation test of the Tesla motors SpaceX wants to use to actuate Starship flaps and fins, there are no signs that SN3 will be outfitted with updated flaps and aerodynamic control surfaces more generally. For low-velocity testing, they’re simply unnecessary. Instead, it’s more likely that this Tesla motor is somehow involved in Starship’s autogenous pressurization system, a method of pressurizing tanks with the liquids they contain. Autogenous pressurization relies on a small portion of propellant (liquid oxygen and methane for Starship) being siphoned off and heated until it turns to gas. That oxygen or methane gas is then fed back into the tank it came from, keeping it at the pressure needed to feed Starship’s Raptor engines.
Autogenous pressurization is significantly more complex than the far more common use of helium or nitrogen pressurization systems. An electric pump could potentially be useful at several points throughout the process. Pump mystery aside, tune in to LabPadre’s 24/7 livestream below to follow along as SpaceX prepares to put Starship SN3 to the test for the first time.
News
Tesla launches in India with Model Y, showing pricing will be biggest challenge
Tesla finally got its Model Y launched in India, but it will surely come at a price for consumers.
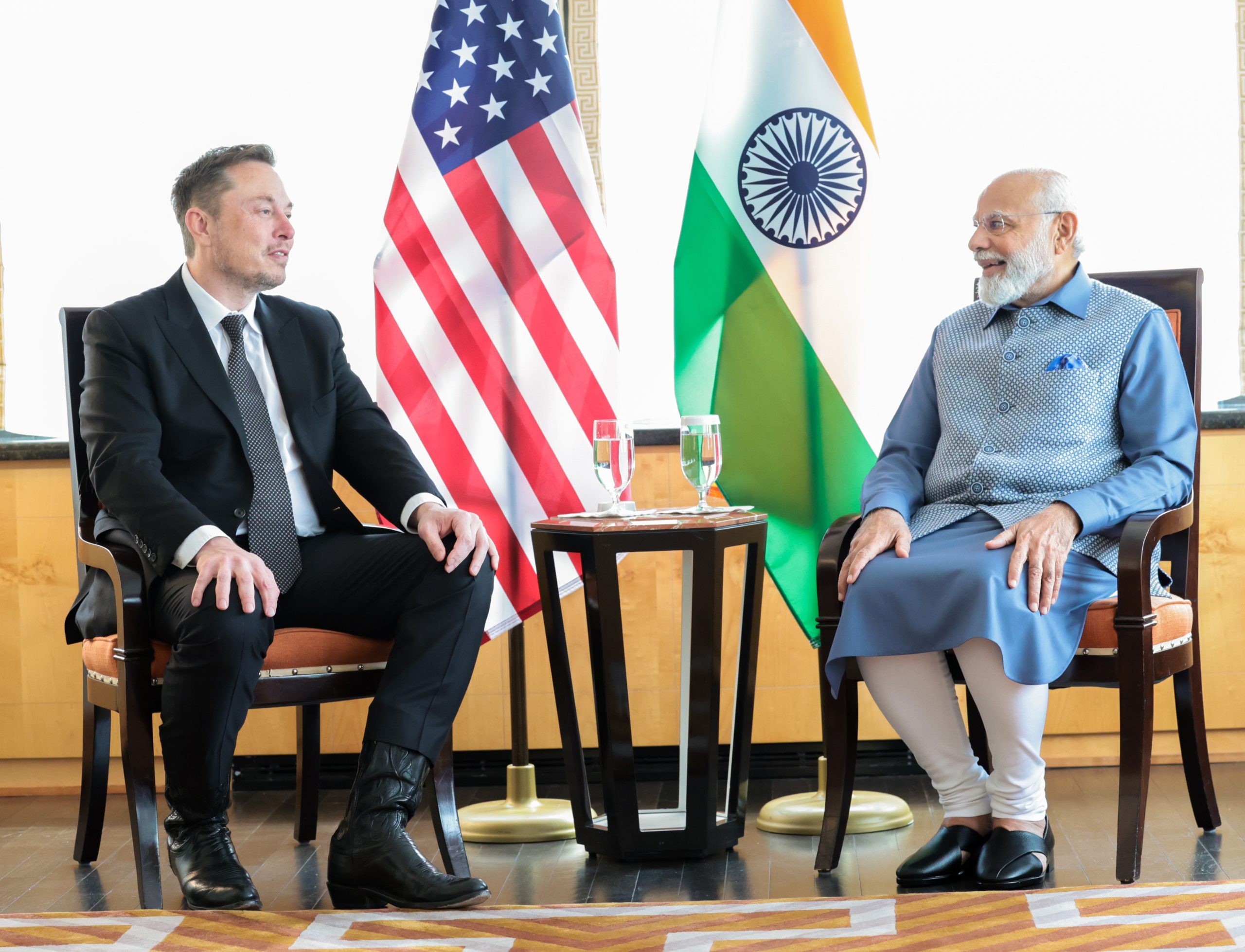
Tesla has officially launched in India following years of delays, as it brought its Model Y to the market for the first time on Tuesday.
However, the launch showed that pricing is going to be its biggest challenge. The all-electric Model Y is priced significantly higher than in other major markets in which Tesla operates.
On Tuesday, Tesla’s Model Y went up for sale for 59,89,000 rupees for the Rear-Wheel Drive configuration, while the Long Range Rear-Wheel Drive was priced at 67,89,000.
This equates to $69,686 for the RWD and $78,994 for the Long Range RWD, a substantial markup compared to what these cars sell for in the United States.
🚨 Here’s the difference in price for the Tesla Model Y in the U.S. compared to India.
🚨 59,89,000 is $69,686
🚨 67,89,000 is $78,994 pic.twitter.com/7EUzyWLcED— TESLARATI (@Teslarati) July 15, 2025
Deliveries are currently scheduled for the third quarter, and it will be interesting to see how many units they can sell in the market at this price point.
The price includes tariffs and additional fees that are applied by the Indian government, which has aimed to work with foreign automakers to come to terms on lower duties that increase vehicle cost.
Tesla Model Y seen testing under wraps in India ahead of launch
There is a chance that these duties will be removed, which would create a more stable and affordable pricing model for Tesla in the future. President Trump and Indian Prime Minister Narendra Modi continue to iron out those details.
Maharashtra Chief Minister Devendra Fadnavis said to reporters outside the company’s new outlet in the region (via Reuters):
“In the future, we wish to see R&D and manufacturing done in India, and I am sure at an appropriate stage, Tesla will think about it.”
It appears to be eerily similar to the same “game of chicken” Tesla played with Indian government officials for the past few years. Tesla has always wanted to enter India, but was unable to do so due to these import duties.
India wanted Tesla to commit to building a Gigafactory in the country, but Tesla wanted to test demand first.
It seems this could be that demand test, and the duties are going to have a significant impact on what demand will actually be.
Elon Musk
Tesla ups Robotaxi fare price to another comical figure with service area expansion
Tesla upped its fare price for a Robotaxi ride from $4.20 to, you guessed it, $6.90.
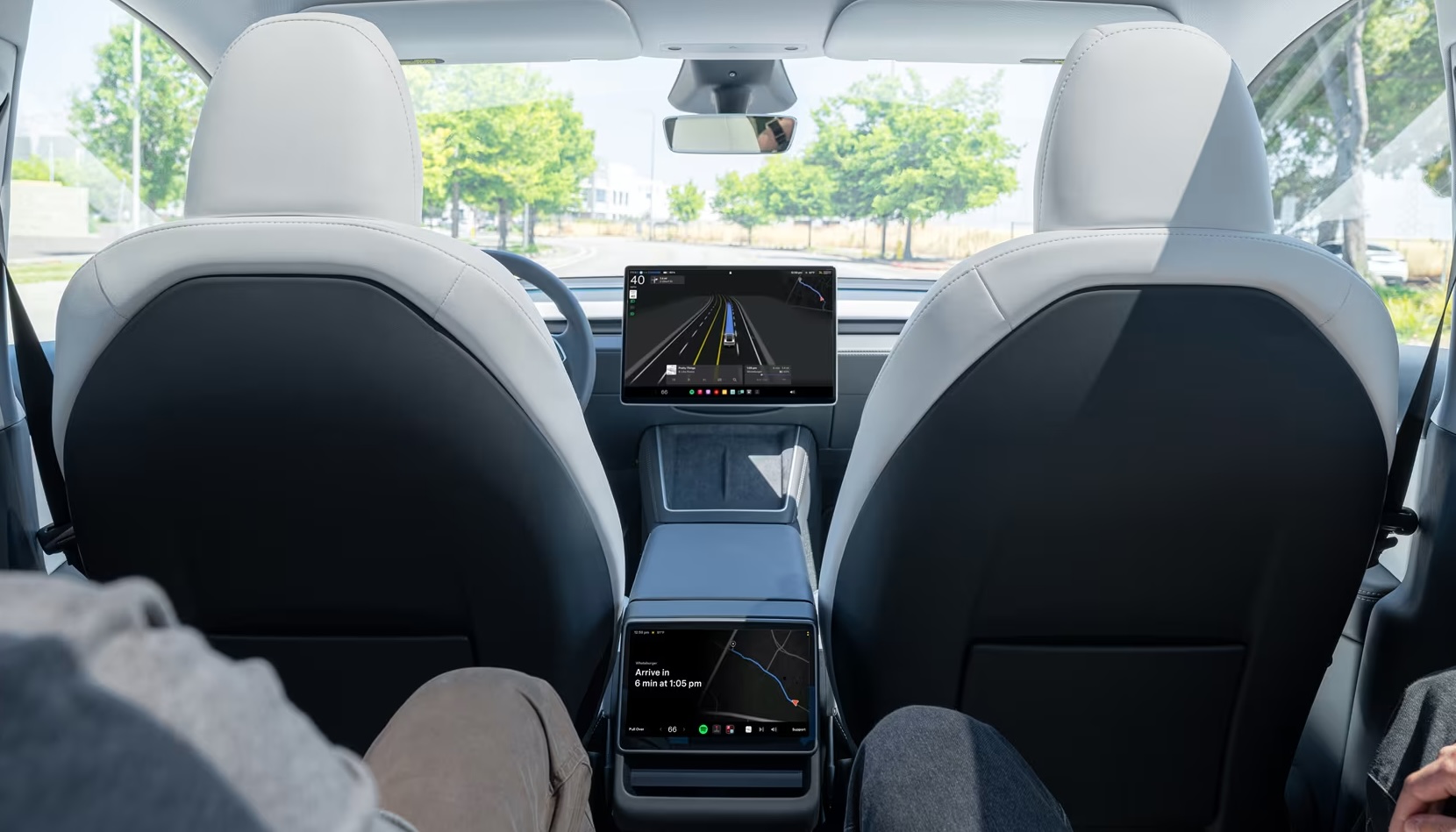
Tesla has upped its fare price for the Robotaxi platform in Austin for the first time since its launch on June 22. The increase came on the same day that Tesla expanded its Service Area for the Robotaxi ride-hailing service, offering rides to a broader portion of the city.
The price is up from $4.20, a figure that many Tesla fans will find amusing, considering CEO Elon Musk has used that number, as well as ’69,’ as a light-hearted attempt at comedy over the past several years.
Musk confirmed yesterday that Tesla would up the price per ride from that $4.20 point to $6.90. Are we really surprised that is what the company decided on, as the expansion of the Service Area also took effect on Monday?
But the price is now a princely $6.90, as foretold in the prophecy 😂
— Elon Musk (@elonmusk) July 14, 2025
The Service Area expansion was also somewhat of a joke too, especially considering the shape of the new region where the driverless service can travel.
I wrote yesterday about how it might be funny, but in reality, it is more of a message to competitors that Tesla can expand in Austin wherever it wants at any time.
Tesla’s Robotaxi expansion wasn’t a joke, it was a warning to competitors
It was only a matter of time before the Robotaxi platform would subject riders to a higher, flat fee for a ride. This is primarily due to two reasons: the size of the access program is increasing, and, more importantly, the service area is expanding in size.
Tesla has already surpassed Waymo in Austin in terms of its service area, which is roughly five square miles larger. Waymo launched driverless rides to the public back in March, while Tesla’s just became available to a small group in June. Tesla has already expanded it, allowing new members to hail a ride from a driverless Model Y nearly every day.
The Robotaxi app is also becoming more robust as Tesla is adding new features with updates. It has already been updated on two occasions, with the most recent improvements being rolled out yesterday.
Tesla updates Robotaxi app with several big changes, including wider service area
News
Tesla Model Y and Model 3 dominate U.S. EV sales despite headwinds
Tesla’s two mainstream vehicles accounted for more than 40% of all EVs sold in the United States in Q2 2025.
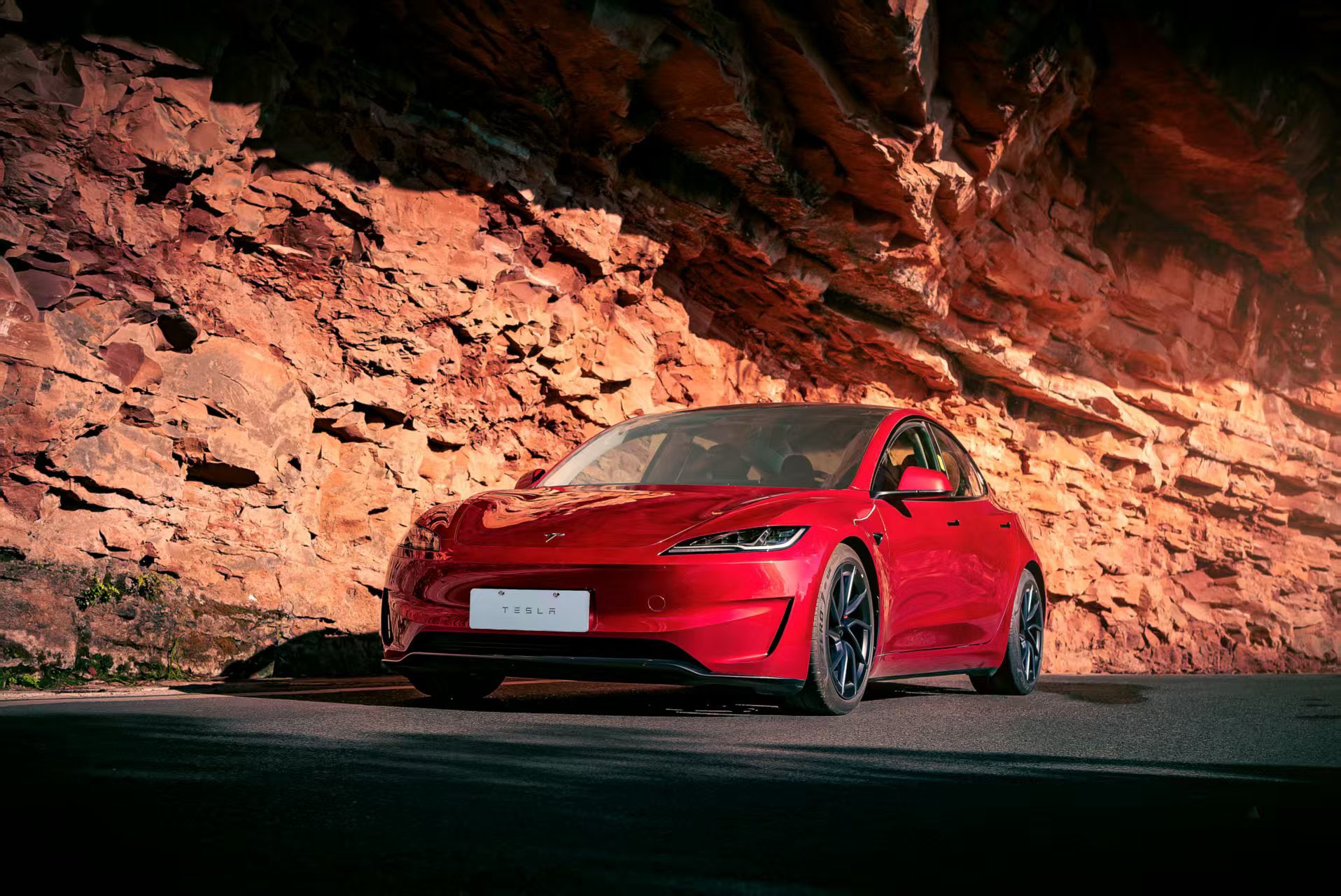
Tesla’s Model Y and Model 3 remained the top-selling electric vehicles in the U.S. during Q2 2025, even as the broader EV market dipped 6.3% year-over-year.
The Model Y logged 86,120 units sold, followed by the Model 3 at 48,803. This means that Tesla’s two mainstream vehicles accounted for 43% of all EVs sold in the United States during the second quarter, as per data from Cox Automotive.
Tesla leads amid tax credit uncertainty and a tough first half
Tesla’s performance in Q2 is notable given a series of hurdles earlier in the year. The company temporarily paused Model Y deliveries in Q1 as it transitioned to the production of the new Model Y, and its retail presence was hit by protests and vandalism tied to political backlash against CEO Elon Musk. The fallout carried into Q2, yet Tesla’s two mass-market vehicles still outsold the next eight EVs combined.
Q2 marked just the third-ever YoY decline in quarterly EV sales, totaling 310,839 units. Electric vehicle sales, however, were still up 4.9% from Q1 and reached a record 607,089 units in the first half of 2025. Analysts also expect a surge in Q3 as buyers rush to qualify for federal EV tax credits before they expire on October 1, Cox Automotive noted in a post.
Legacy rivals gain ground, but Tesla holds its commanding lead
General Motors more than doubled its EV volume in the first half of 2025, selling over 78,000 units and boosting its EV market share to 12.9%. Chevrolet became the second-best-selling EV brand, pushing GM past Ford and Hyundai. Tesla, however, still retained a commanding 44.7% electric vehicle market share despite a 12% drop in in Q2 revenue, following a decline of almost 9% in Q1.
Incentives reached record highs in Q2, averaging 14.8% of transaction prices, roughly $8,500 per vehicle. As government support winds down, the used EV market is also gaining momentum, with over 100,000 used EVs sold in Q2.
Q2 2025 Kelley Blue Book EV Sales Report by Simon Alvarez on Scribd
-
News3 days ago
Tesla debuts hands-free Grok AI with update 2025.26: What you need to know
-
Elon Musk6 days ago
xAI launches Grok 4 with new $300/month SuperGrok Heavy subscription
-
Elon Musk1 week ago
Elon Musk confirms Grok 4 launch on July 9 with livestream event
-
News2 weeks ago
Tesla Model 3 ranks as the safest new car in Europe for 2025, per Euro NCAP tests
-
Elon Musk2 weeks ago
xAI’s Memphis data center receives air permit despite community criticism
-
News5 days ago
Tesla begins Robotaxi certification push in Arizona: report
-
Elon Musk2 weeks ago
Tesla reveals it is using AI to make factories more sustainable: here’s how
-
Elon Musk2 weeks ago
Tesla scrambles after Musk sidekick exit, CEO takes over sales