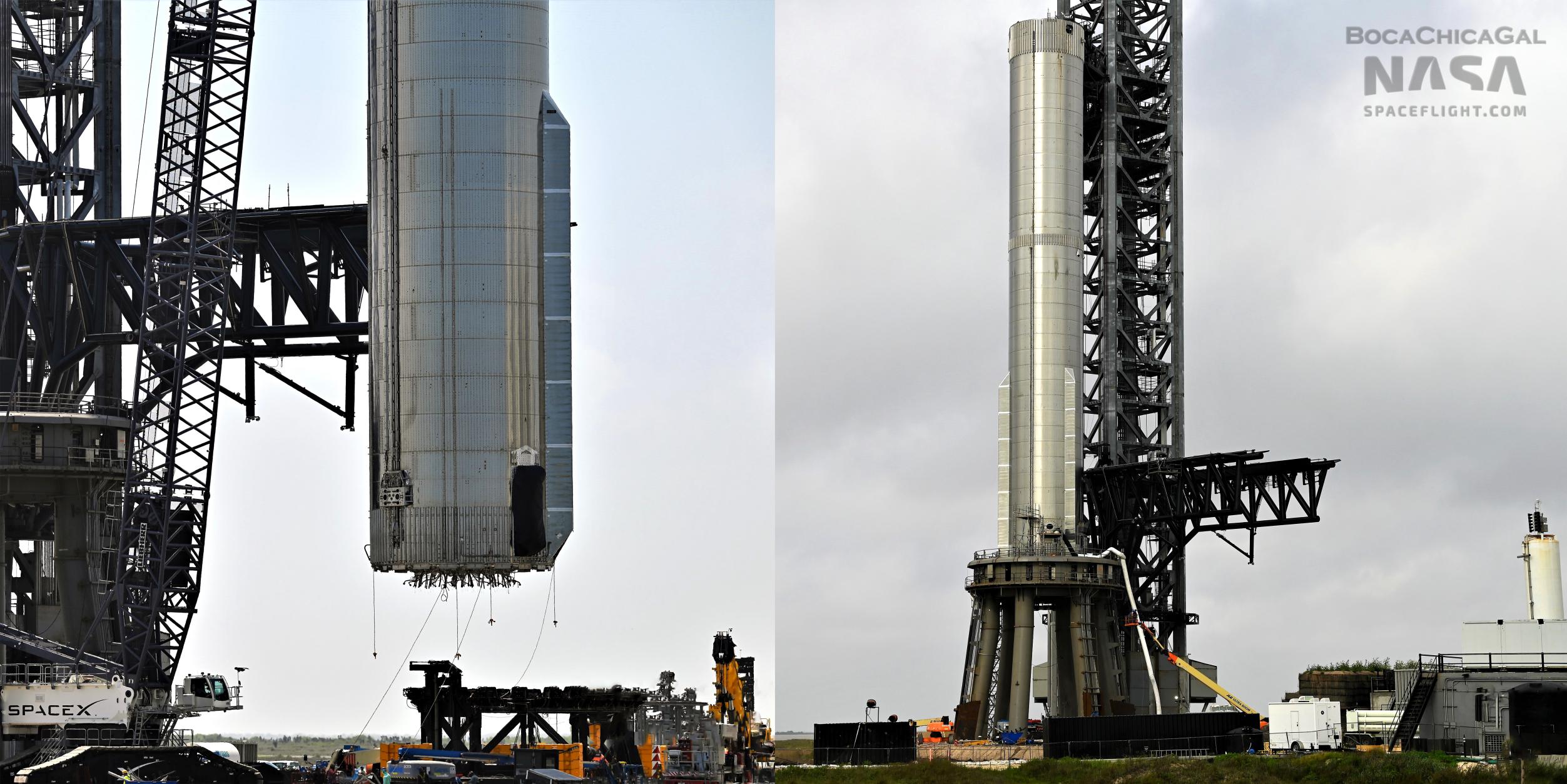
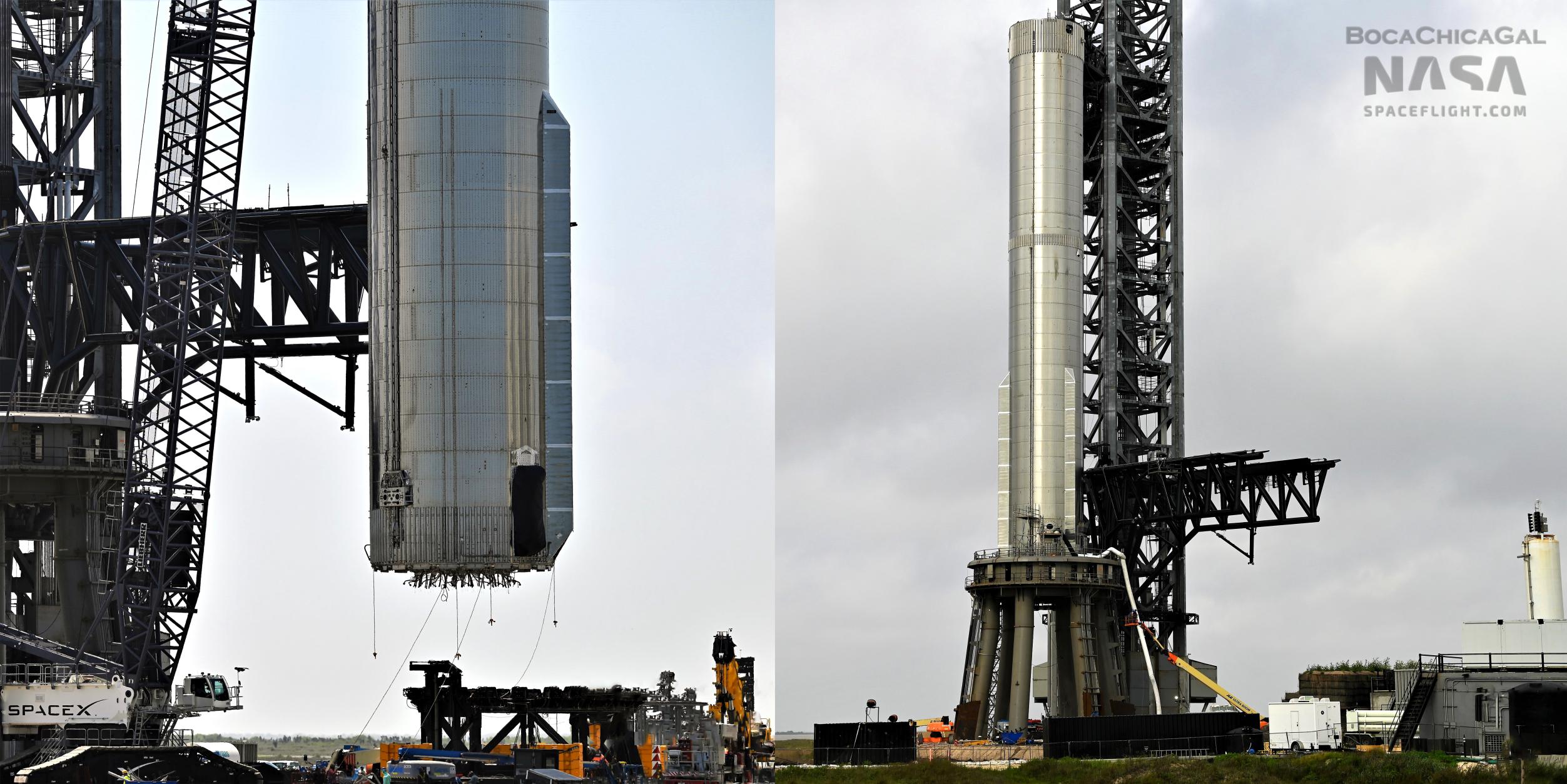
News
SpaceX Super Heavy booster returns to launch pad after major repairs
SpaceX has returned its newest Super Heavy to Starbase’s orbital launch site (OLS) after rapidly repairing damage the booster suffered during its first round of testing.
Super Heavy Booster 7 (B7) left the High Bay it was assembled in for the first time on March 31st and rolled a few miles down the road to nearby Starship launch and test facilities on a set of self-propelled mobile transporters (SPMTs). On April 2nd, the roughly 67-meter-tall (~220 ft; 69m w/ Raptors) rocket was installed on top of Starbase’s lone orbital launch mount (OLM), setting the stage for crucial qualification testing.
The start of that process was exceptionally successful. On April 4th, after a smooth launch mount installation, SpaceX quickly filled Booster 7’s propellant tanks with a relatively benign cryogenic fluid (liquid nitrogen, liquid oxygen, or both) to simulate the thermal and mechanical characteristics of real flammable propellant. Despite the fact that the test marked the first time SpaceX had fully filled a Super Heavy prototype’s tanks, Booster 7 sailed through the ‘cryoproof’ without any obvious issue.
On April 8th, SpaceX moved Super Heavy B7 from the orbital launch mount to a structural test stand that had been installed and modified just a few hundred feet away in the weeks prior. This is where Booster 7’s near-perfect start to qualification testing took a bit of a turn. Booster 7 is only the third full-size Super Heavy prototype SpaceX has tested since July 2021. Like Booster 3 and Booster 4 before it, Booster 7 features some major design changes that ultimately make the prototype a pathfinder, necessitating extensive qualification testing.
To name just a few of the changes, Super Heavy B7 is the first booster fitted with a 33-engine puck and the first finished Starship prototype of any kind designed to use new Raptor V2 engines. With all 33 engines installed and operating a full thrust, Booster 7’s entire structure – and its aft thrust section especially – would be subjected to around 40% more thrust and stress than Booster 4, which indirectly completed structural testing with the help of a sacrificial test tank. Beyond differences in thrust and mechanical stress, Booster 7 is also the first Super Heavy to reach the test stand with secondary ‘header’ tanks meant to store landing propellant.
It’s unclear if those header tanks were fully filled and drained during Booster 7’s cryoproof, but they would not be quite as cooperative during a different kind of cryogenic testing on the structural test stand. The stand SpaceX modified specifically for Super Heavy B7 was outfitted with 13 hydraulic rams to simulate the full thrust of the booster’s central Raptor V2 engines – up to almost 3000 tons (~6.6M lbf) compared to Booster 4’s ~1700 tons (~3.7M lbf) with a smaller cluster of nine engines.
Implosion at the Structural Test Stand
After a few false starts and minor tests on the stand, Booster 7 finally managed some significant testing on April 14th. Judging by the rhythmic shattering of ice that built up on Super Heavy’s tanks, the test stand was able to simulate the thrust of Raptors to some degree and subject the booster to major mechanical stress that was felt from tip to tail. Within a few days, Booster 7 was removed from the test stand and returned to the high bay on April 18th. Around April 21st or 22nd, an image was leaked showing extensive damage inside Booster 7, confirming that the Super Heavy’s test campaign had been forced to end prematurely.
Right away, the damage shown in the photo hinted at an operational failure, meaning that mistakes made by the rocket’s operators may have been more to blame than a possible design flaw. The photo shows a short portion of B7’s liquid methane (LCH4) transfer tube that runs through the booster’s new liquid oxygen (LOx) header tank, which itself sits inside Super Heavy’s main LOx tank at the aft end of the rocket – a tube inside a small tank inside a large tank, in other words. Super Heavy’s LCH4 transfer tube generally does what it says, allowing methane to safely fly down through the main LOx tank and fuel up to 33 Raptor engines. At full thrust, that tube would need to supply around 20 tons (~45,000 lb) of methane per second.
However, on top of merely transferring methane through the oxygen tank, Booster 7 introduced a design change that allows some or all of that tube to change functions and become a header tank mid-flight. That would require a system of valves that could seal off the main LCH4 tank once it was emptied, turning the transfer tube into a sort of giant steel straw filled with enough LCH4 to fuel Super Heavy’s boost-back and landing burns.
The damaged transfer tube in the leaked photo of Booster 7 doesn’t look that unlike what one might expect to see if they sucked through one end of a straw while blocking the other end, collapsing the center. Translated to the scale of Super Heavy, after an otherwise successful day of structural testing, SpaceX operators may have accidentally closed or opened the wrong valves while draining the booster’s transfer tube of liquid oxygen or nitrogen. As the heavy liquid drained from the tube, a lack of pressure equalization could have quickly drawn a vacuum and caused the tube to implode.
On April 29th, a SpaceX fan turned analyst published an analysis that convincingly pinpointed the moment Booster 7’s transfer tube collapsed. Simultaneously, because it showed that the transfer tube likely imploded during detanking, the analysis more or less confirmed the above speculation that the failure had been caused by a degree of operator error or poor test design. Of course, it’s possible that a hardware or software design flaw contributed to or caused the anomaly or that something like a pressure differential in the LOx header tank and LCH4 header tube could also explain the damage, but the accidental formation of a vacuum during detanking is arguably the simplest (obvious) explanation.
After the image of the internal damage leaked, the immediate consensus among fans and close followers was that Booster 7 was beyond repair. Instead, SpaceX appears to have proven those assumptions wrong and somehow managed to repair the upgraded Super Heavy to the point that it was worth testing again less than three weeks after returning to the high bay. On May 6th, B7 was rolled back to the launch site and installed, for the second time, on the orbital launch mount.
Prior to the failure, the general expectation was that SpaceX would begin installing Raptor V2 engines as soon as Booster 7 passed structural testing. It remains to be seen if SpaceX wants to repeat Booster 7’s cryoproof or structural testing to ensure that its quick repairs did the job before proceeding into static fire testing as previously planned. Nonetheless, hope lives on for the Super Heavy prototype and new test windows have been scheduled from 10am to 10pm on May 9th, 10th, and 11th.
News
Tesla begins Robotaxi certification push in Arizona: report
Tesla seems serious about expanding its Robotaxi service to several states in the coming months.
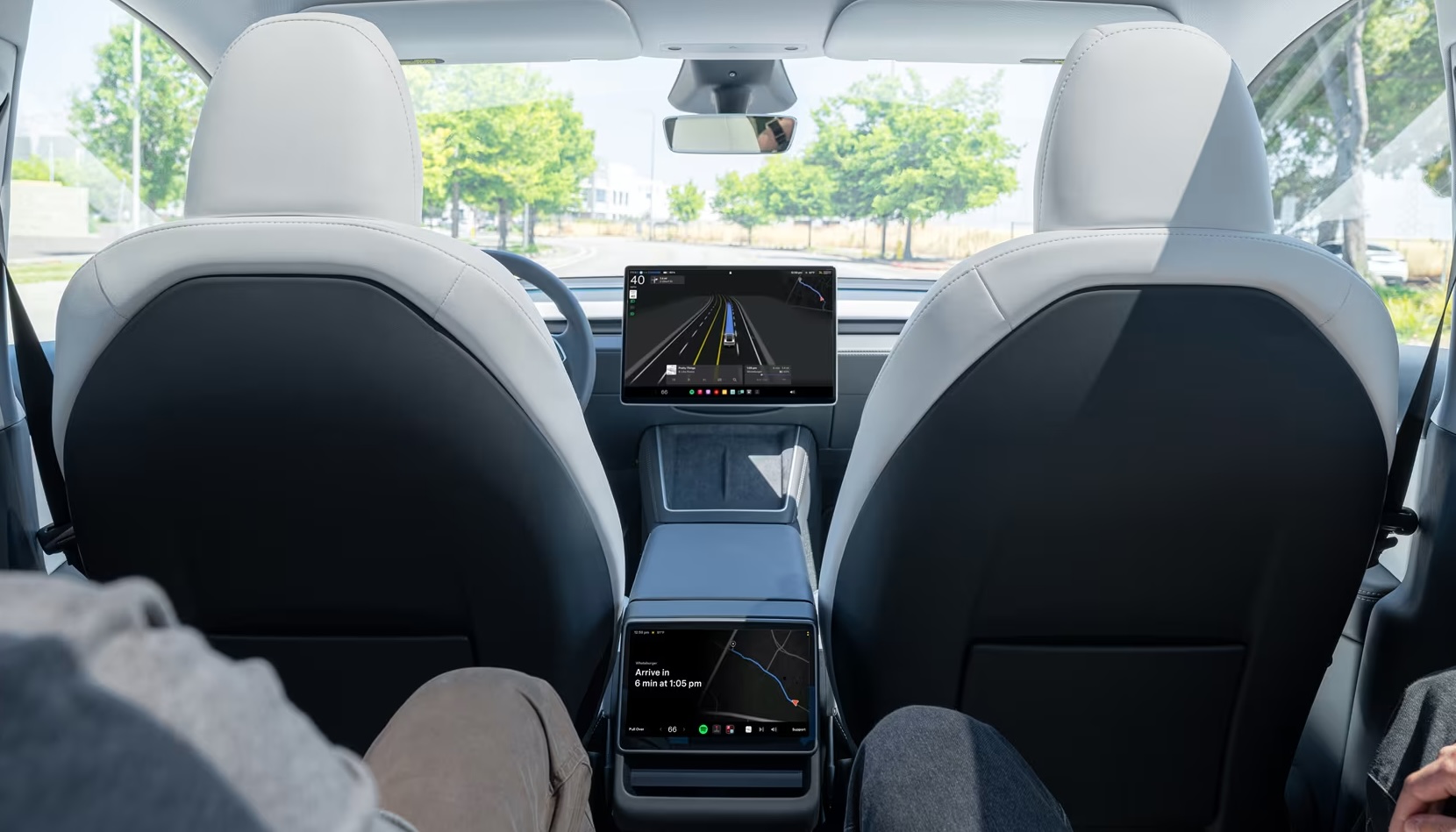
Tesla has initiated discussions with Arizona transportation regulators to certify its driverless Robotaxi service in the state, as per a recent report from Bloomberg News. The move follows Tesla’s launch of its Robotaxi pilot program in Austin, Texas, as well as CEO Elon Musk’s recent comments about the service’s expansion in the Bay Area.
The Arizona Department of Transportation confirmed to Bloomberg that Tesla has reached out to begin the certification process for autonomous ride-sharing operations in the state. While details remain limited, the outreach suggests that Tesla is serious about expanding its driverless Robotaxi service to several territories in the coming months.
The Arizona development comes as Tesla prepares to expand its service area in Austin this weekend, as per CEO Elon Musk in a post on X. Musk also stated that Tesla is targeting the San Francisco Bay Area as its next major market, with a potential launch “in a month or two,” pending regulatory approvals.
Tesla first launched its autonomous ride-hailing program on June 22 in Austin with a small fleet of Model Y vehicles, accompanied by a Tesla employee in the passenger seat to monitor safety. While still classified as a test, Musk has said the program will expand to about 1,000 vehicles in the coming months. Tesla will later upgrade its Robotaxi fleet with the Cyercab, a two-seater that is designed without a steering wheel.
Sightings of Cybercab castings around the Giga Texas complex suggests that Tesla may be ramping the initial trial production of the self-driving two-seater. Tesla, for its part, has noted in the past that volume production of the Cybercab is expected to start sometime next year.
In California, Tesla has already applied for a transportation charter-party carrier permit from the state’s Public Utilities Commission. The company is reportedly taking a phased approach to operating in California, with the Robotaxi service starting with pre-arranged rides for employees in vehicles with safety drivers.
News
Tesla sets November 6 date for 2025 Annual Shareholder Meeting
The automaker announced the date on Thursday in a Form 8-K.
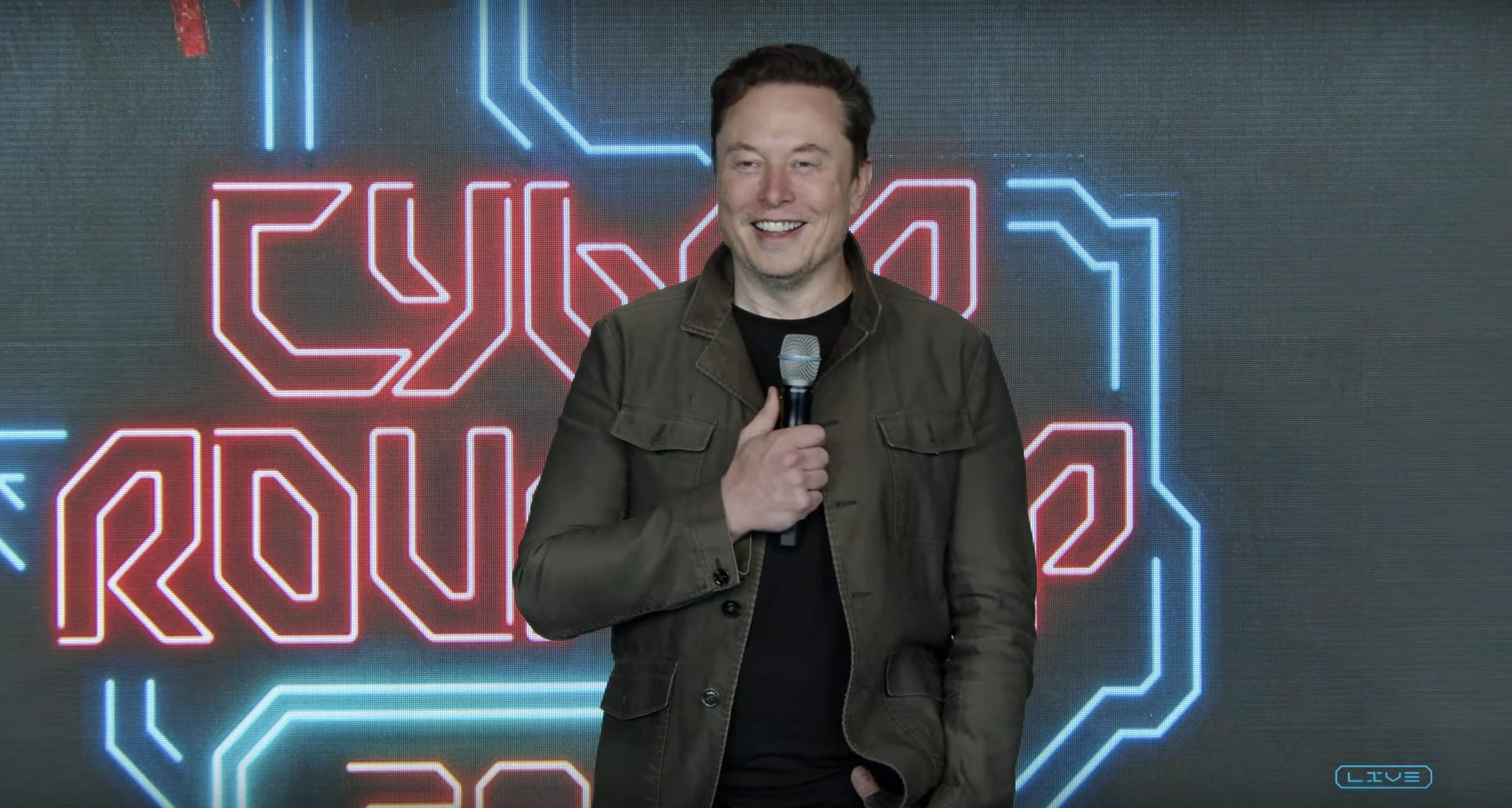
Tesla has scheduled its 2025 annual shareholder meeting for November 6, addressing investor concerns that the company was nearing a legal deadline to hold the event.
The automaker announced the date on Thursday in a Form 8-K submitted to the United States Securities and Exchange Commission (SEC). The company also listed a new proposal submission deadline of July 31 for items to be included in the proxy statement.
Tesla’s announcement followed calls from a group of 27 shareholders, including the leaders of large public pension funds, which urged Tesla’s board to formally set the meeting date, as noted in a report from The Wall Street Journal.
The group noted that under Texas law, where Tesla is now incorporated, companies must hold annual meetings within 13 months of the last one if requested by shareholders. Tesla’s previous annual shareholder meeting was held on June 13, 2024, which placed the July 13 deadline in focus.
Tesla originally stated in its 2024 annual report that it would file its proxy statement by the end of April. However, an amended filing on April 30 indicated that the Board of Directors had not yet finalized a meeting date, at least at the time.
The April filing also confirmed that Tesla’s board had formed a special committee to evaluate certain matters related to CEO Elon Musk’s compensation plan. Musk’s CEO performance award remains at the center of a lengthy legal dispute in Delaware, Tesla’s former state of incorporation.
Due to the aftermath of Musk’s legal dispute about his compensation plan in Delaware, he has not been paid for his work at Tesla for several years. Musk, for his part, has noted that he is more concerned about his voting stake in Tesla than his actual salary.
At last year’s annual meeting, TSLA shareholders voted to reapprove Elon Musk’s compensation plan and ratified Tesla’s decision to relocate its legal domicile from Delaware to Texas.
Elon Musk
Grok coming to Tesla vehicles next week “at the latest:” Elon Musk
Grok’s rollout to Tesla vehicles is expected to begin next week at the latest.
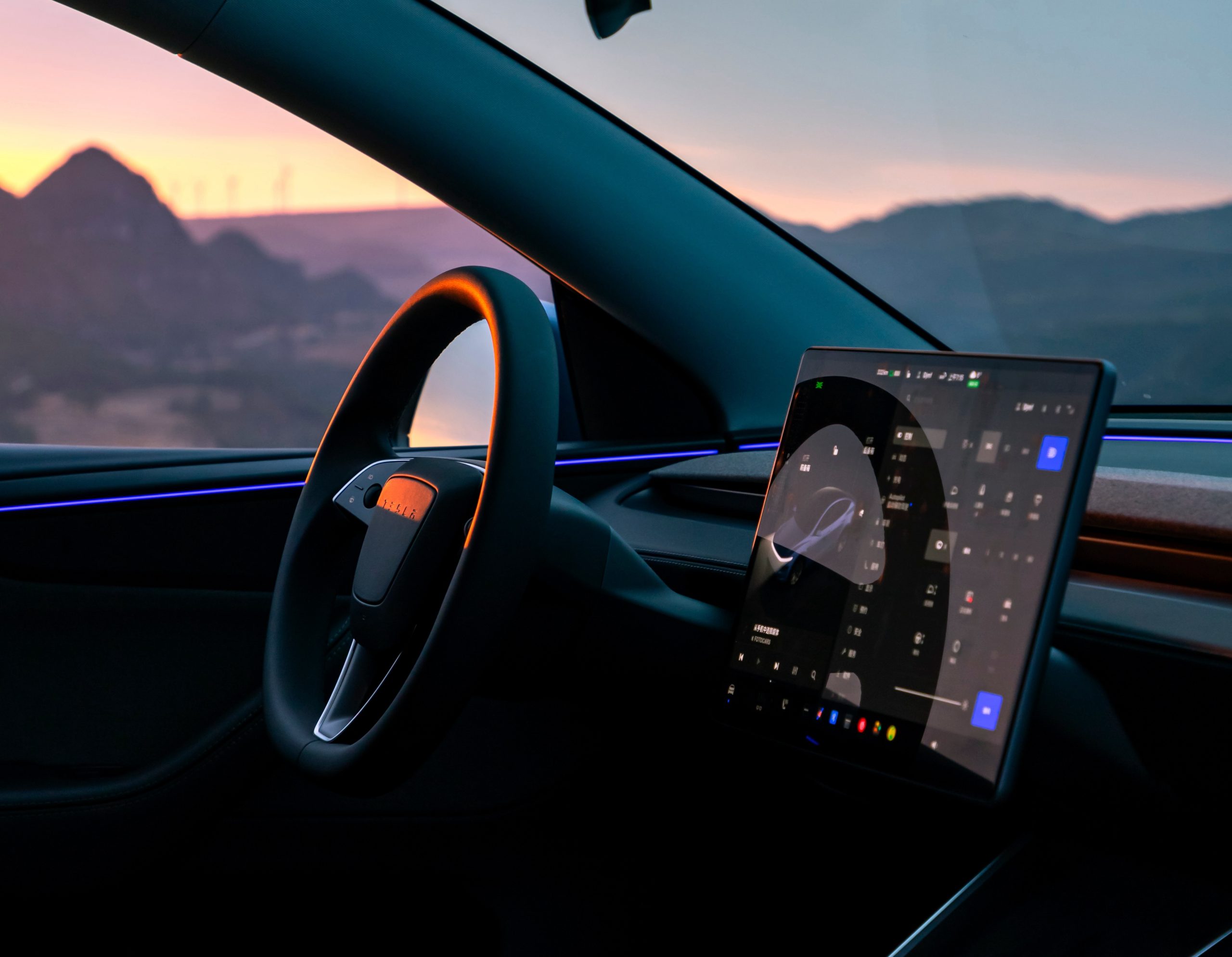
Elon Musk announced on Thursday that Grok, the large language model developed by his startup xAI, will soon be available in Tesla vehicles. Grok’s rollout to Tesla vehicles is expected to begin next week at the latest, further deepening the ties between the two Elon Musk-led companies.
Tesla–xAI synergy
Musk confirmed the news on X shortly after livestreaming the release of Grok 4, xAI’s latest large language model. “Grok is coming to Tesla vehicles very soon. Next week at the latest,” Musk wrote in a post on social media platform X.
During the livestream, Musk and several members of the xAI team highlighted several upgrades to Grok 4’s voice capabilities and performance metrics, positioning the LLM as competitive with top-tier models from OpenAI and Google.
The in-vehicle integration of Grok marks a new chapter in Tesla’s AI development. While Tesla has long relied on in-house systems for autonomous driving and energy optimization, Grok’s integration would introduce conversational AI directly into its vehicles’ user experience. This integration could potentially improve customer interaction inside Tesla vehicles.
xAI and Tesla’s collaborative footprint
Grok’s upcoming rollout to Tesla vehicles adds to a growing business relationship between Tesla and xAI. Earlier this year, Tesla disclosed that it generated $198.3 million in revenue from commercial, consulting, and support agreements with xAI, as noted in a report from Bloomberg News. A large portion of that amount, however, came from the sale of Megapack energy storage systems to the artificial intelligence startup.
In July 2023, Musk polled X users about whether Tesla should invest $5 billion in xAI. While no formal investment has been made so far, 68% of poll participants voted yes, and Musk has since stated that the idea would be discussed with Tesla’s board.
-
Elon Musk1 week ago
Tesla investors will be shocked by Jim Cramer’s latest assessment
-
Elon Musk21 hours ago
xAI launches Grok 4 with new $300/month SuperGrok Heavy subscription
-
Elon Musk3 days ago
Elon Musk confirms Grok 4 launch on July 9 with livestream event
-
News7 days ago
Tesla Model 3 ranks as the safest new car in Europe for 2025, per Euro NCAP tests
-
Elon Musk2 weeks ago
A Tesla just delivered itself to a customer autonomously, Elon Musk confirms
-
Elon Musk1 week ago
xAI’s Memphis data center receives air permit despite community criticism
-
Elon Musk2 weeks ago
Tesla’s Omead Afshar, known as Elon Musk’s right-hand man, leaves company: reports
-
News2 weeks ago
Xiaomi CEO congratulates Tesla on first FSD delivery: “We have to continue learning!”