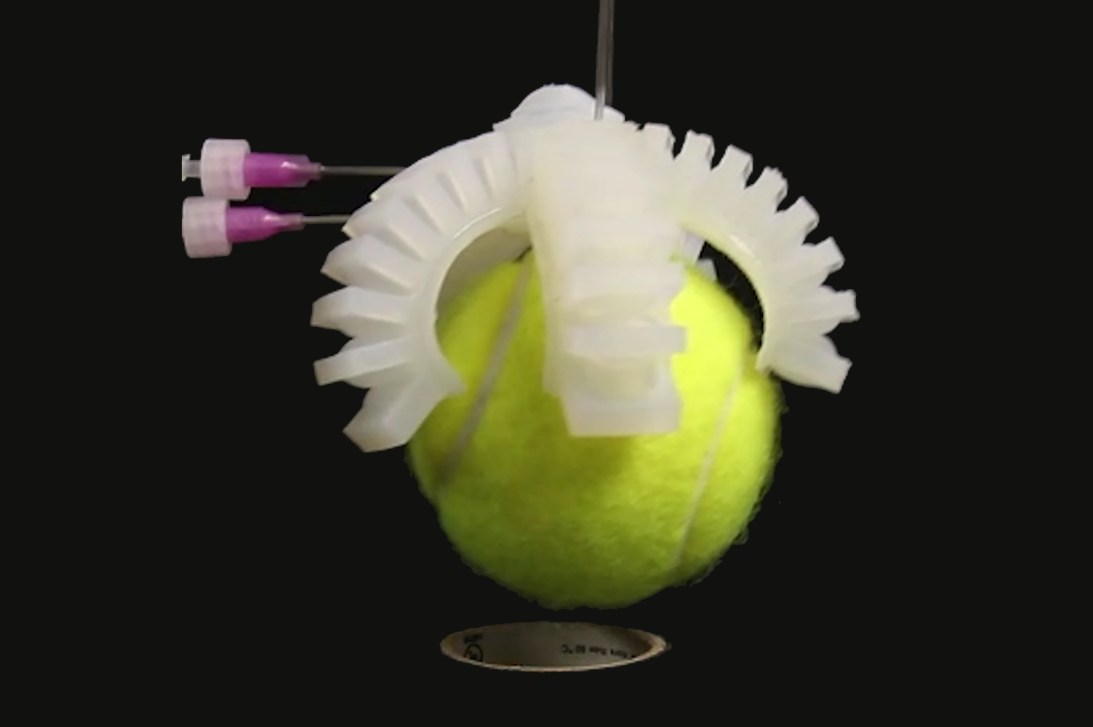
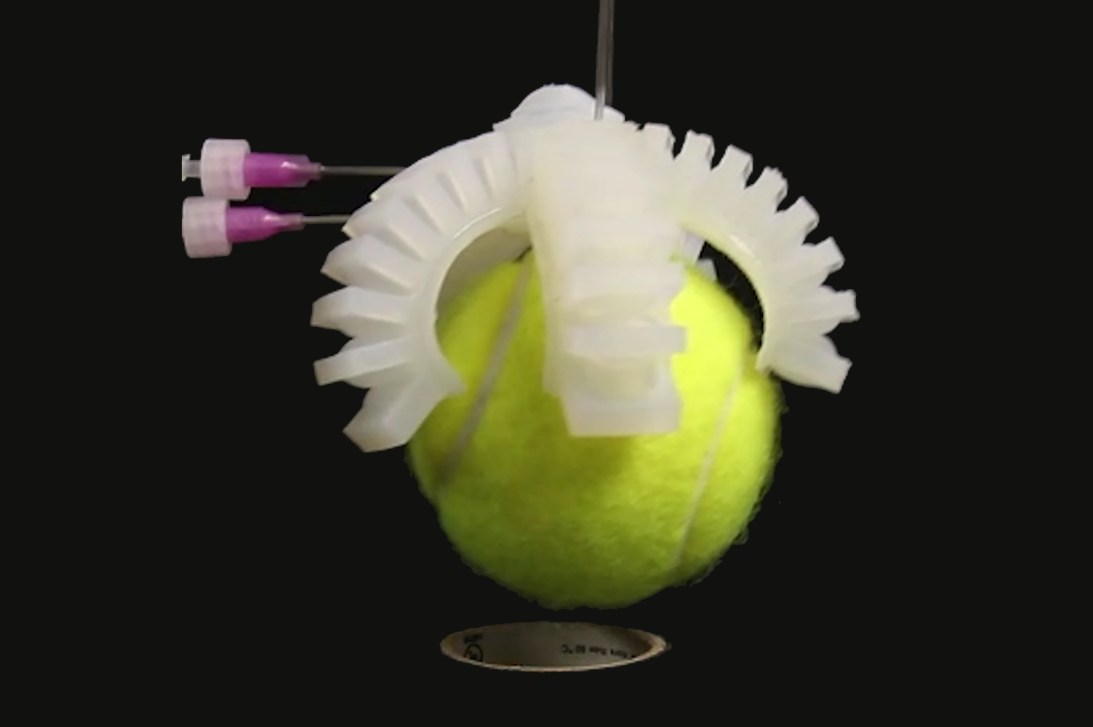
News
Scientists develop “soft valve” to enable human flesh-like robots
The field of soft robotics has achieved some impressive feats in recent years, meaning we are well on our way to life-like robots that possess the very flesh that distinguishes us from our mechanical brethren. Squishy worms, claws, and octopus arms are a few of the machines in development, but they all still have “hard” parts comprising their inner mechanics. Currently, the valves controlling air pressures to manipulate the bots’ movements are rigid, off-the-shelf components. Now, thanks to a new technology created by scientists at the Professor George Whitesides lab at Woodford L. and Ann A. Flowers University, a squishy valve enabling soft robots is available.
Standard hard pneumatic valves help control the movement of soft robots by pushing air (in most cases) into chambers as directed by the device’s operator or programming. A network of tubes or air bladders are built throughout the robot’s appendages, filling or emptying as needed to effect the desired motion. To provide a soft alternative to the rigid components, there are two concepts the new soft valves were driven by: 1) a fleshy membrane that stretches in two directions, similar to a ‘popper’ vending machine toy; and 2) a soft hose that controls air flow by kinking, similar to how bending a garden hose restricts its water flow.
Soft robots are typically made from silicone. With that in mind, doctoral student Philipp Rothemund and postdoctoral fellow Daniel Preston built their valve into a silicone cylinder, separating it into upper and lower chambers. Each chamber contained soft tubes that would kink depending on whether the membrane was stretched in their direction. As air filled one chamber, the membrane would stretch and kink the air hose in the opposite chamber, shutting off the air flow and thus fulfilling the valve functionality needed for soft robots to work as already designed.
- The soft valve developed for soft robots. | Credit: Harvard University
- The soft valve developed for soft robots. | Credit: Harvard University
Soft robots are generally designed to imitate functionality found in living organisms. The ability for hands to grip, for example, seems simple, but without specific data to work with, robots cannot easily repeat that same functionality, nor with the same amount of agility. Adding the ‘soft’ factor provides flexibility and adaptability. Fleshy materials can conform to objects better than rigid ones, enhancing grip, and their shapes can be pushed or pulled, capabilities that are useful for maneuvering in small spaces or preventing major damage from, say, being run over by a vehicle.
As the soft robotics field expands in its development, we can look forward to new solutions in medicine, operational safety, and tasks otherwise difficult for humans to do without high cost, time, or damage considerations. For example, tubing styled after octopus tentacles could maneuver throughout the body during a surgery, minimizing its invasiveness. One could also imagine a search and rescue soft bot pushing through crevices in rubble to find victims of natural disasters.
Combined with advancements in sensor technologies, we could also see fleshy robots that look, feel, and have a sense of touch like ours. On the plus side, robot hugs might actually feel genuine, and robotic workers could operate in outside environments that lack the precision their rigid counterparts need to function properly. Unfortunately, the down sides are plentiful, and movie studios worldwide have entertained us with numerous cyborg dystopias already.
Watch the below video to see the soft valve in action:
News
Tesla UK sales see 14% year-over-year rebound in June: SMMT data
The SMMT stated that Tesla sales grew 14% year-over-year to 7,719 units in June 2025.
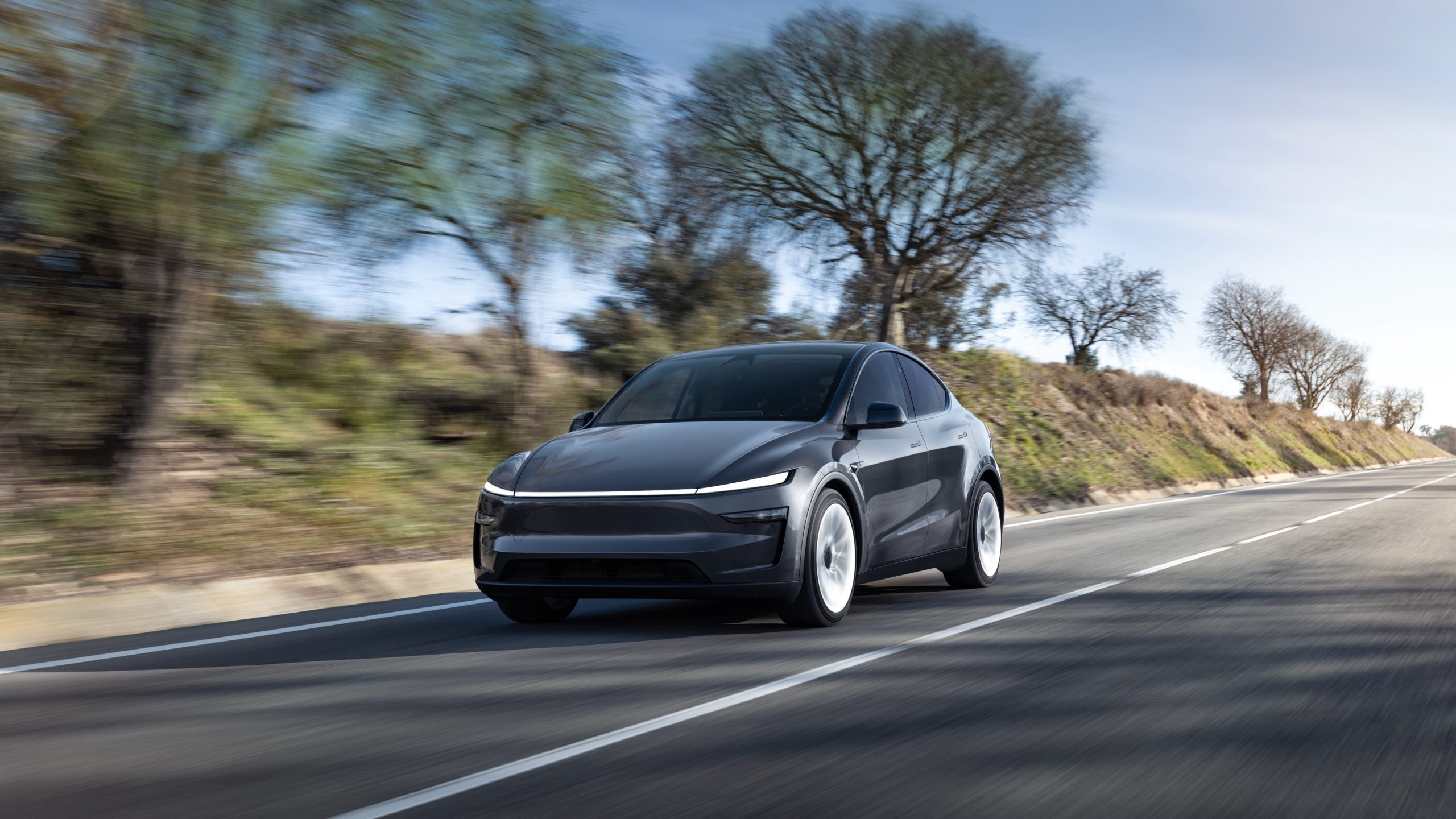
Tesla’s sales in the United Kingdom rose in June, climbing 14% year-over-year to 7,719 units, as per data from the Society of Motor Manufacturers and Traders (SMMT). The spike in the company’s sales coincided with the first deliveries of the updated Model Y last month.
Model Y deliveries support Tesla’s UK recovery
Tesla’s June performance marked one of its strongest months in the UK so far this year, with new Model Y deliveries contributing significantly to the company’s momentum.
While the SMMT listed Tesla with 7,719 deliveries in June, independent data from New AutoMotive suggested that the electric vehicle maker registered 7,891 units during the month instead. However, year-to-date figures for Tesla remain 2% down compared to 2024, as per a report from Reuters.
While Tesla made a strong showing in June, rivals are also growing. Chinese automaker BYD saw UK sales rise nearly fourfold to 2,498 units, while Ford posted the highest EV growth among major automakers, with a more than fourfold increase in the first half of 2025.
Overall, the UK’s battery electric vehicle (BEV) demand surged 39% to to 47,354 units last month, helping push total new car sales in the UK to 191,316 units, up 6.7% from the same period in 2024.
EV adoption accelerates, but concerns linger
June marked the best month for UK car sales since 2019, though the SMMT cautioned that growth in the electric vehicle sector remains heavily dependent on discounting and support programs. Still, one in four new vehicle buyers in June chose a battery electric vehicle.
SMMT Chief Executive Mike Hawes noted that despite strong BEV demand, sales levels are still below regulatory targets. “Further growth in sales, and the sector will rely on increased and improved charging facilities to boost mainstream electric vehicle adoption,” Hawes stated.
Also taking effect this week was a new US-UK trade deal, which lowers tariffs on UK car exports to the United States from 27.5% to 10%. The agreement could benefit UK-based EV producers aiming to expand across the country.
News
Tesla Model 3 ranks as the safest new car in Europe for 2025, per Euro NCAP tests
Despite being on the market longer than many of its rivals, the Tesla Model 3 continues to set the bar for vehicle safety.
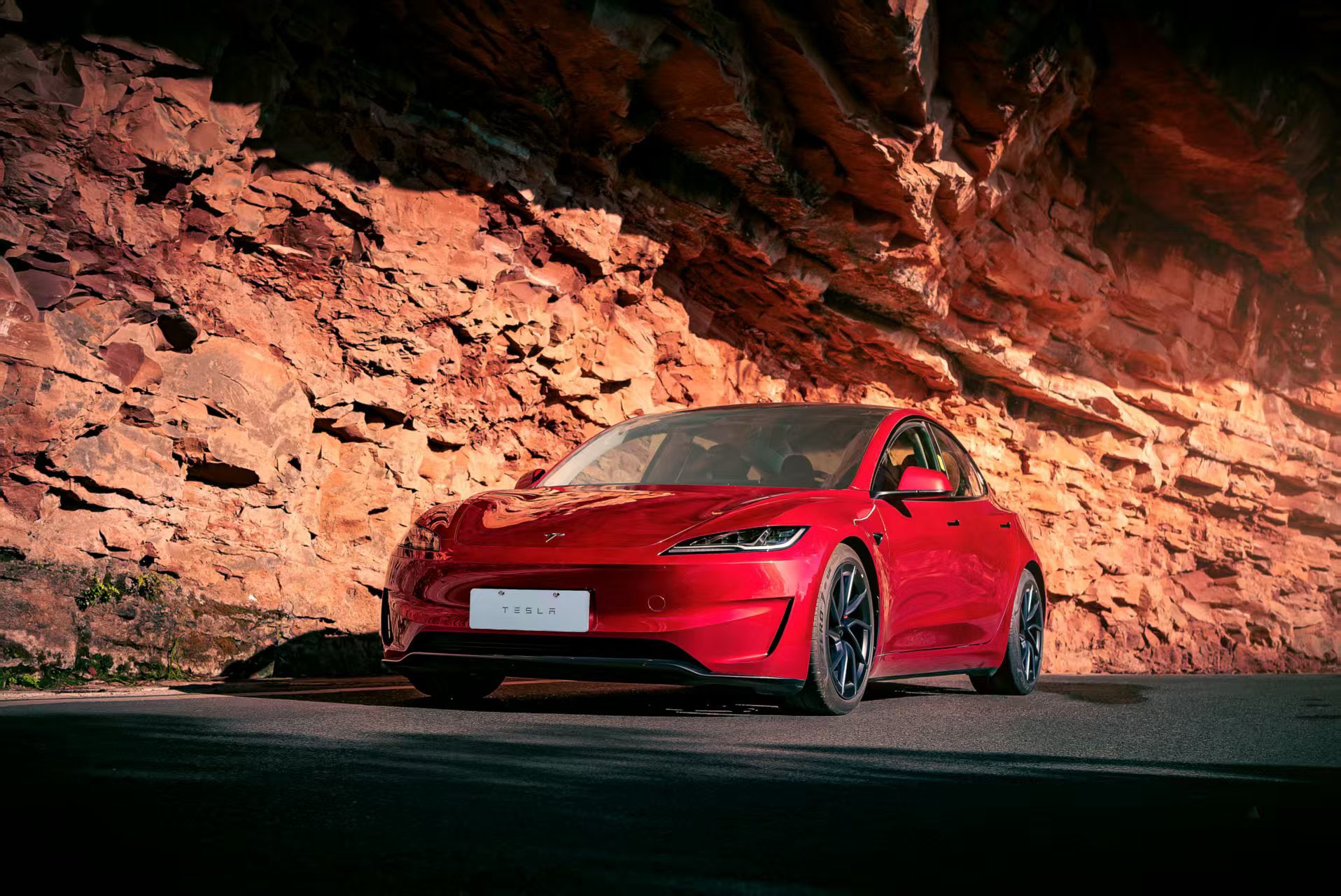
The Tesla Model 3 has been named the safest new car on sale in 2025, according to the latest results from the Euro NCAP. Among 20 newly tested vehicles, the Model 3 emerged at the top of the list, scoring an impressive 359 out of 400 possible points across all major safety categories.
Tesla Model 3’s safety systems
Despite being on the market longer than many of its rivals, the Tesla Model 3 continues to set the bar for vehicle safety. Under Euro NCAP’s stricter 2025 testing protocols, the electric sedan earned 90% for adult occupant protection, 93% for child occupant protection, 89% for pedestrian protection, and 87% for its Safety Assist systems.
The updated Model 3 received particular praise for its advanced driver assistance features, including Tesla’s autonomous emergency braking (AEB) system, which performed well across various test scenarios. Its Intelligent Speed Assistance and child presence detection system were cited as noteworthy features as well, as per a WhatCar report.
Other notable safety features include the Model 3’s pedestrian-friendly pop-up hood and robust crash protection for both front and side collisions. Euro NCAP also highlighted the Model 3’s ability to detect vulnerable road users during complex maneuvers, such as turning across oncoming traffic.
Euro NCAP’s Autopilot caution
While the Model 3’s safety scores were impressive across the board, Euro NCAP did raise concerns about driver expectations of Tesla’s Autopilot system. The organization warned that some owners may overestimate the system’s capabilities, potentially leading to misuse or inattention behind the wheel. Even so, the Model 3 remained the highest-scoring vehicle tested under Euro NCAP’s updated criteria this year.
The Euro NCAP’s concerns are also quite interesting because Tesla’s Full Self-Driving (FSD) Supervised, which is arguably the company’s most robust safety suite, is not allowed for public rollout in Europe yet. FSD Supervised would allow the Model 3 to navigate inner city streets with only minimal human supervision.
Other top scorers included the Volkswagen ID.7, Polestar 3, and Geely EX5, but none matched the Model 3’s total score or consistency across categories. A total of 14 out of 20 newly tested cars earned five stars, while several models, including the Kia EV3, MG ZS, and Renault 5, fell short of the top rating.
Elon Musk
Why Tesla’s Q3 could be one of its biggest quarters in history
Tesla could stand to benefit from the removal of the $7,500 EV tax credit at the end of Q3.
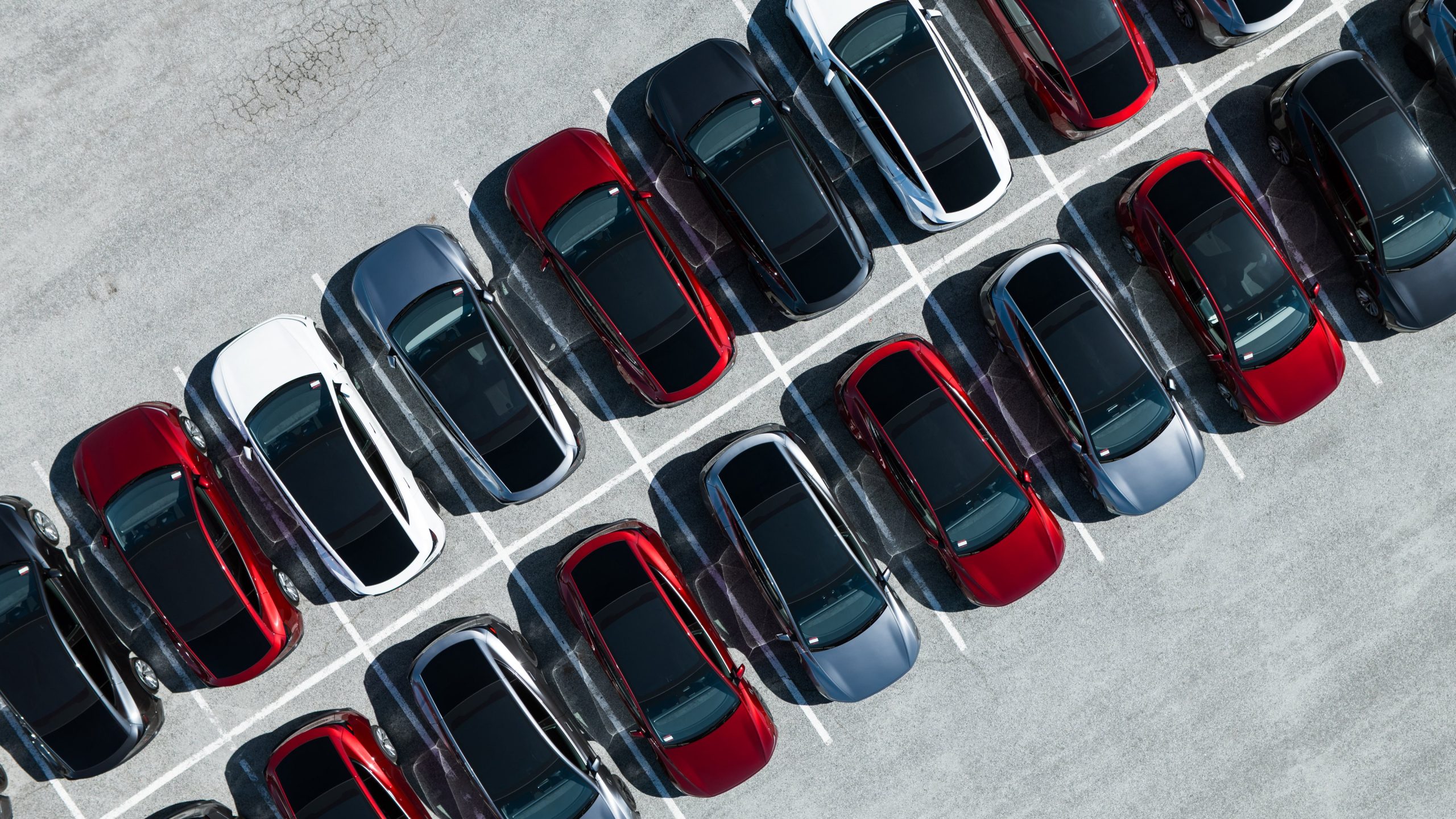
Tesla has gotten off to a slow start in 2025, as the first half of the year has not been one to remember from a delivery perspective.
However, Q3 could end up being one of the best the company has had in history, with the United States potentially being a major contributor to what might reverse a slow start to the year.
Earlier today, the United States’ House of Representatives officially passed President Trump’s “Big Beautiful Bill,” after it made its way through the Senate earlier this week. The bill will head to President Trump, as he looks to sign it before his July 4 deadline.
The Bill will effectively bring closure to the $7,500 EV tax credit, which will end on September 30, 2025. This means, over the next three months in the United States, those who are looking to buy an EV will have their last chance to take advantage of the credit. EVs will then be, for most people, $7,500 more expensive, in essence.
The tax credit is available to any single filer who makes under $150,000 per year, $225,000 a year to a head of household, and $300,000 to couples filing jointly.
Ending the tax credit was expected with the Trump administration, as his policies have leaned significantly toward reliance on fossil fuels, ending what he calls an “EV mandate.” He has used this phrase several times in disagreements with Tesla CEO Elon Musk.
Nevertheless, those who have been on the fence about buying a Tesla, or any EV, for that matter, will have some decisions to make in the next three months. While all companies will stand to benefit from this time crunch, Tesla could be the true winner because of its sheer volume.
If things are done correctly, meaning if Tesla can also offer incentives like 0% APR, special pricing on leasing or financing, or other advantages (like free Red, White, and Blue for a short period of time in celebration of Independence Day), it could see some real volume in sales this quarter.
You can now buy a Tesla in Red, White, and Blue for free until July 14 https://t.co/iAwhaRFOH0
— TESLARATI (@Teslarati) July 3, 2025
Tesla is just a shade under 721,000 deliveries for the year, so it’s on pace for roughly 1.4 million for 2025. This would be a decrease from the 1.8 million cars it delivered in each of the last two years. Traditionally, the second half of the year has produced Tesla’s strongest quarters. Its top three quarters in terms of deliveries are Q4 2024 with 495,570 vehicles, Q4 2023 with 484,507 vehicles, and Q3 2024 with 462,890 vehicles.
-
Elon Musk5 days ago
Tesla investors will be shocked by Jim Cramer’s latest assessment
-
News1 week ago
Tesla Robotaxi’s biggest challenge seems to be this one thing
-
Elon Musk2 weeks ago
First Look at Tesla’s Robotaxi App: features, design, and more
-
News2 weeks ago
Watch Tesla’s first driverless public Robotaxi rides in Texas
-
News2 weeks ago
Watch the first true Tesla Robotaxi intervention by safety monitor
-
Elon Musk2 weeks ago
Tesla officially launches Robotaxi service with no driver
-
Elon Musk1 week ago
A Tesla just delivered itself to a customer autonomously, Elon Musk confirms
-
News2 weeks ago
Tesla Robotaxi rollout proves that Elon Musk still delivers, even if it’s late