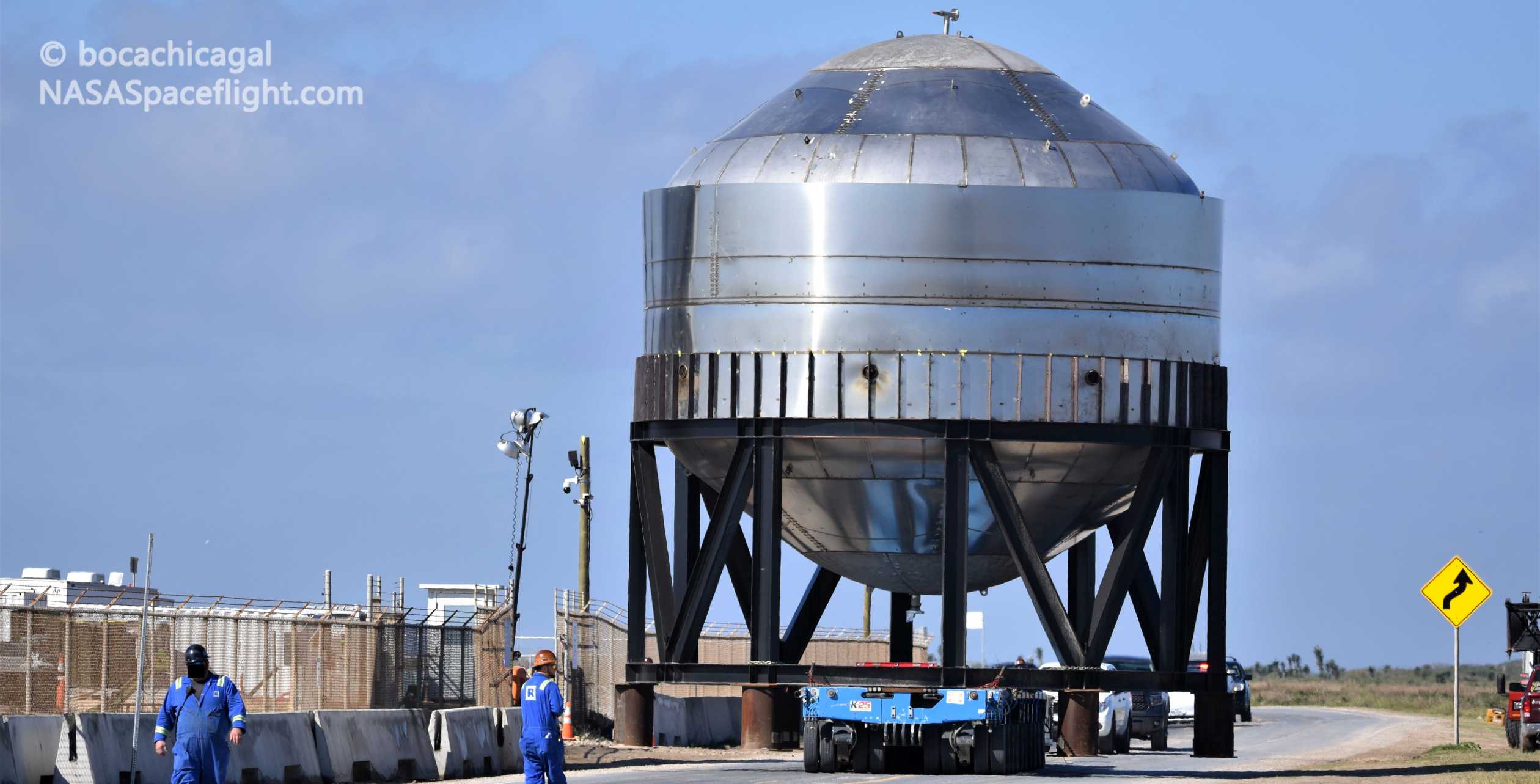
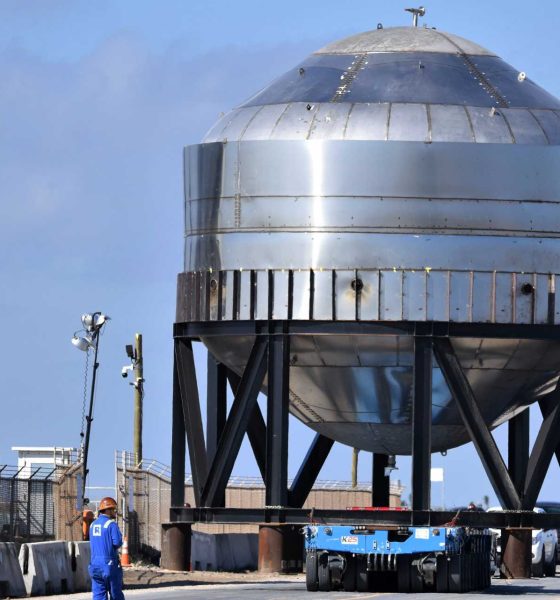
News
SpaceX is ready to build the first Starship destined for space after latest tests
After a busy several days of rocket hardware testing, Elon Musk says that SpaceX may be ready to build the first Starship prototype destined for space.
According to Musk, one test in particular – performed in South Texas just yesterday – is an encouraging sign that SpaceX’s Starship team is becoming increasingly competent at building the massive steel parts that will ultimately make up the generation launch vehicle. For SpaceX, the particular skills and expertise needed to precisely and consistently build a launch vehicle – let alone a rocket as large and complex as Starship – are quite a bit different from those it has mastered with Falcon 9, Falcon Heavy, and Dragon.
A lot of the expertise – particularly engineering talent, countless lessons-learned, and insight into reusability – is directly transferable from Falcon rockets to SpaceX’s Starship/Super Heavy program. Where it really isn’t transferable, however, is in the methods required to actually build the steel subcomponents that must ultimately be assembled together to form the rocket’s upper stage and booster. As a result, SpaceX has spent more than a year focused on building, testing, scrapping, improving, and re-testing any number of critical Starship components. Over the last four weeks (and last few days in particular), that testing has come to a head and Elon Musk believes the results have opened the door for SpaceX to begin building its first space-bound Starship prototypes.
SpaceX’s latest round of full-scale Starship hardware tests began just 10-20 days ago, depending on how one counts. Back around the start of the new calendar year, SpaceX began rapidly integrating two new Starship bulkheads and two cylindrical steel rings (barrel sections), ultimately delivering a finished ‘test tank’ after just 20 days of work. On January 10th, scarcely 24 hours after the two halves of the test tank were welded together, SpaceX sent the Starship test tank to its nearby launch pad and pressurized it with water until it quite literally burst.
Musk tweeted the results of that intentional test-to-destruction just a few hours after it was completed, revealing that SpaceX’s upgraded production and integration techniques enabled the tank to survive pressures almost 20% greater than the minimum Starships will need to perform orbital launches.
“Critically, the tank reached a maximum sustained pressure of 7.1 bar (103 psi), 18% more than the operating pressure (6 bar/87 psi) Musk says Starship prototypes will need to begin orbital test flights. At 7.1 bar, the test tank would have been experiencing an incredible ~20,000 metric tons (45 million lbf) of force spread out over its interior surfaces — equivalent to ~20% of the weight of an entire US Navy aircraft carrier. Perhaps even more impressive, that same Starship test tank was built from almost nothing extremely quickly, going from first weld to said pressurization test in just three weeks (20 days).
With relatively minor improvements to welding conditions and the manufacturing precision of Starship rings and domes, Musk believes that SpaceX can reliably build Starships and Super Heavy boosters to survive pressures greater than 8.5 bar (125 psi), guaranteeing a safety margin of at least 40%. Even a minor improvement of ~6% would give Starship a safety margin of 125%, enough – in the eyes of most engineering standards committees – to reasonably certify Starships for orbital test flights.”
Teslarati.com — January 12th, 2020
Test Tank 2: The Tankening
This brings us to January 27th, a little over two weeks after SpaceX completed and burst the first standalone Starship test tank. Over the last week, SpaceX has quickly assembled a second Starship test tank, using a few clearly new methods and parts, as well as a brand-new tent built by the same company that Tesla used for Fremont’s fourth General Assembly line.
In the last few days, two new bulkheads and steel rings came together to form Starship test tank #2, which was subsequently prepped for transport and moved about a mile down the road to SpaceX’s launch facilities on the morning of January 27th. Scarcely a few hours later, well before anyone was paying close attention for test activities, Elon Musk took to Twitter to reveal that the second tank had already been subjected to a pressure test with water. That second tank reportedly survived up to 7.5 bar, an improvement of about 6% compared to the first tank.
This time, however, the tank wasn’t actually catastrophically destroyed by the pressure test, instead developing a leak around the weld connecting the two halves that lead SpaceX to back off. Musk says that that presumably small leak will now be repaired, after which the same tank will be tested again but with one significant difference. Musk says that Test Tank #2’s second pressure test will be performed with a cryogenic liquid — most likely liquid nitrogen (LN2).
In replies after his reveal, Musk noted that he believed the second test tank could perform significantly better if pressurized with a cryogenic liquid. That’s because certain types of steel – particularly those SpaceX has chosen for Starship – exhibit something known as cryogenic hardening when exposed to extremely cold temperatures, producing steel that can be dramatically stronger by some measures.
Ultimately, as mentioned above, a tank pressure safety margin of 125% is the minimum most engineering standards provide for any given orbital-class launch vehicle. At 7.5 bar, even under the very unlikely assumption that Starship tanks will not see even a marginal strength increase at cryogenic temperatures, SpaceX’s second Starship test tank has officially hit that 125% safety margin. As Musk himself noted on Monday, he is now confident that SpaceX can immediately start building the first Starship destined for spaceflight and further revealed that two of that particular Starship’s three tank domes are already nearing completion.
Known as Starship SN01 (serial number 01), there’s a strong possibility that the massive spacecraft will never reach higher than a 20 km (12.5 mi) flight test SpaceX intends to perform. The company’s rapidly changing strategy may very well mean that SN01 – now ‘go’ for production – could also support suborbital spaceflight testing and maybe even the first orbital Starship launch, although orbital launches will require a Super Heavy booster. Elon Musk, for one, has already christened Starship SN01 an “orbital vehicle”.
Check out Teslarati’s Marketplace! We offer Tesla accessories, including for the Tesla Cybertruck and Tesla Model 3.
News
Tesla receives European Ecolabel (EMAS) seal for Giga Berlin-Brandenburg
The EMAS seal highlights Tesla’s existing environmental measures in the facility.
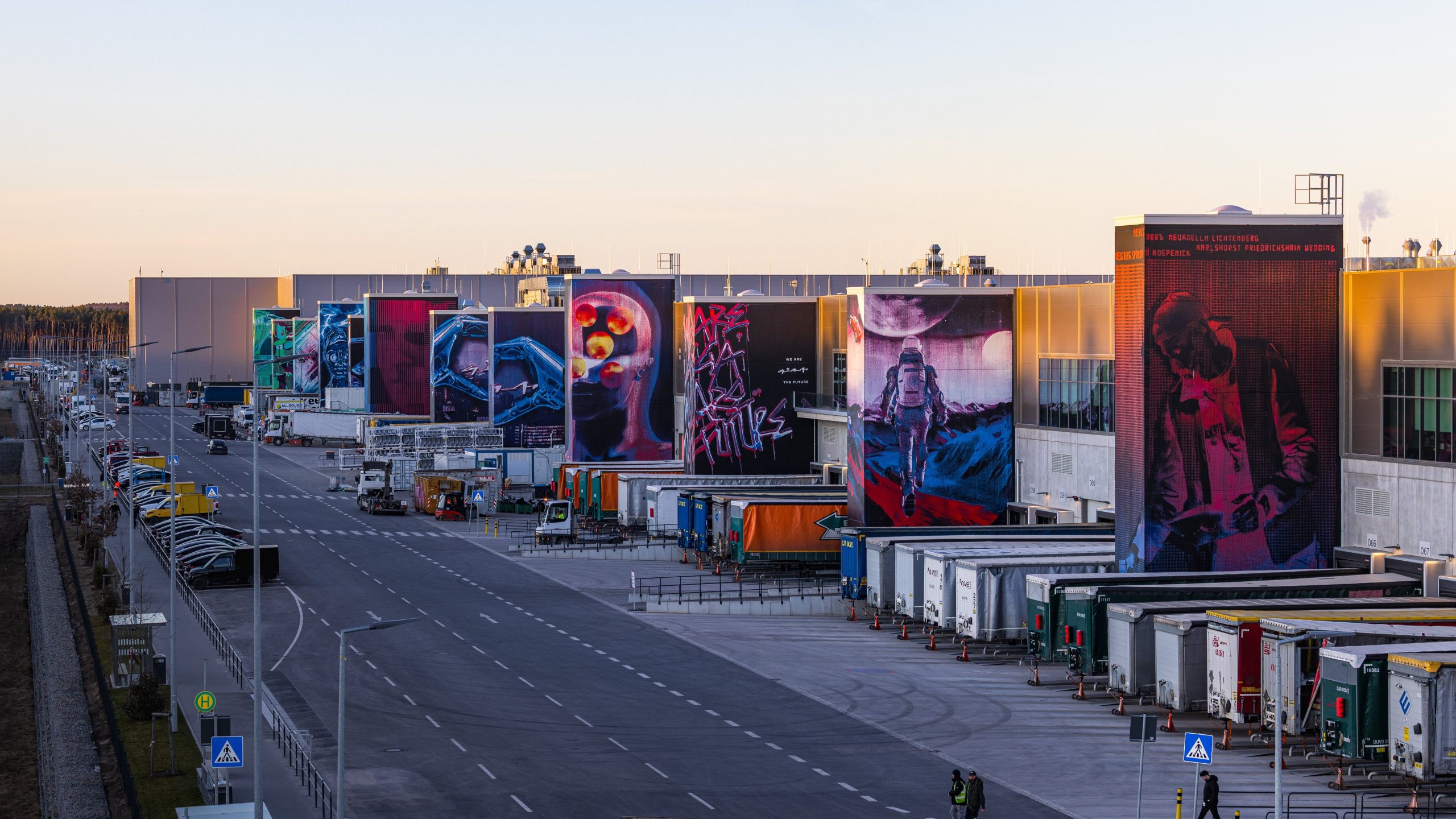
Tesla has been awarded the European Ecolabel (EMAS) seal for Gigafactory Berlin-Brandenburg.
The EMAS seal highlights Tesla’s existing environmental measures in the facility, such as extensive reforestation efforts and reduced water usage. It also emphasizes Tesla’s commitment to improve its environmental initiatives.
Giga Berlin’s environmental initiatives
The EMAS (Eco-Management and Audit Scheme) seal is a long-term environmental management system that focuses on compliance with regulations and improving environmental performance, as noted in a Tagesspiegel report.
Plant manager André Thierig noted that Tesla has already planted over 2 million trees to replace the trees that have been felled to make way for Giga Berlin. Tesla is also targeting an additional 5 to 15 MW peak solar capacity this year to make the plant more sustainable. “We will continue to promote photovoltaics in the future,” he said.
Giga Berlin’s consumption and energy use
In 2024, Giga Berlin consumed about 419,503 MWh of energy, with electricity accounting for more than half, followed by natural gas. The facility is looking to lower natural gas use by redirecting the use of process heating water via waste heat. Water consumption was listed at 2.16 cubic meters per vehicle, significantly below the industry average of 3.5.
This year, Tesla Giga Berlin is looking to recycle 90% of the Model Y plant’s process wastewater. Around 11,000 employees currently work at Giga Berlin, which produces 5,000 vehicles per week or roughly 250,000 units annually.
Certification welcomed but not without criticism
The EMAS program requires companies to disclose resource use, emissions, and improvement plans. Over 40 companies in Brandenburg have EMAS certification.
Brandenburg’s Environment Minister Minister Hanka Mittelstädt (SPD) described Tesla as a role model for the region. “Everything is public, and that also creates a certain amount of trust,” she said, noting that Tesla is a “beacon” in the industry.
Monique Zweig, Managing Director of the East Brandenburg Chamber of Industry and Commerce (IHK), shared her optimism in a comment to rbb24. “At Tesla, you can see that climate goals go hand in hand with industry,” Zweig stated.
Unsurprisingly, local activists expressed skepticism. The Association for Nature and Landscape in Brandenburg, which is against Tesla, questioned whether the certification could be used as “greenwashing.”
The group also alleged that the certificate could pave the way for weaker oversight for the EV maker. “The seal is ‘greenwashing’ to portray the company as more environmentally friendly,” spokesperson Steffen Schorcht noted.
News
I traded my ICE vehicle for a Tesla Model Y: here’s how it went
After working at Teslarati for six years and covering the EV space nearly every single day (I recently published my 5,000th article on here), I figured it was time to make a switch.
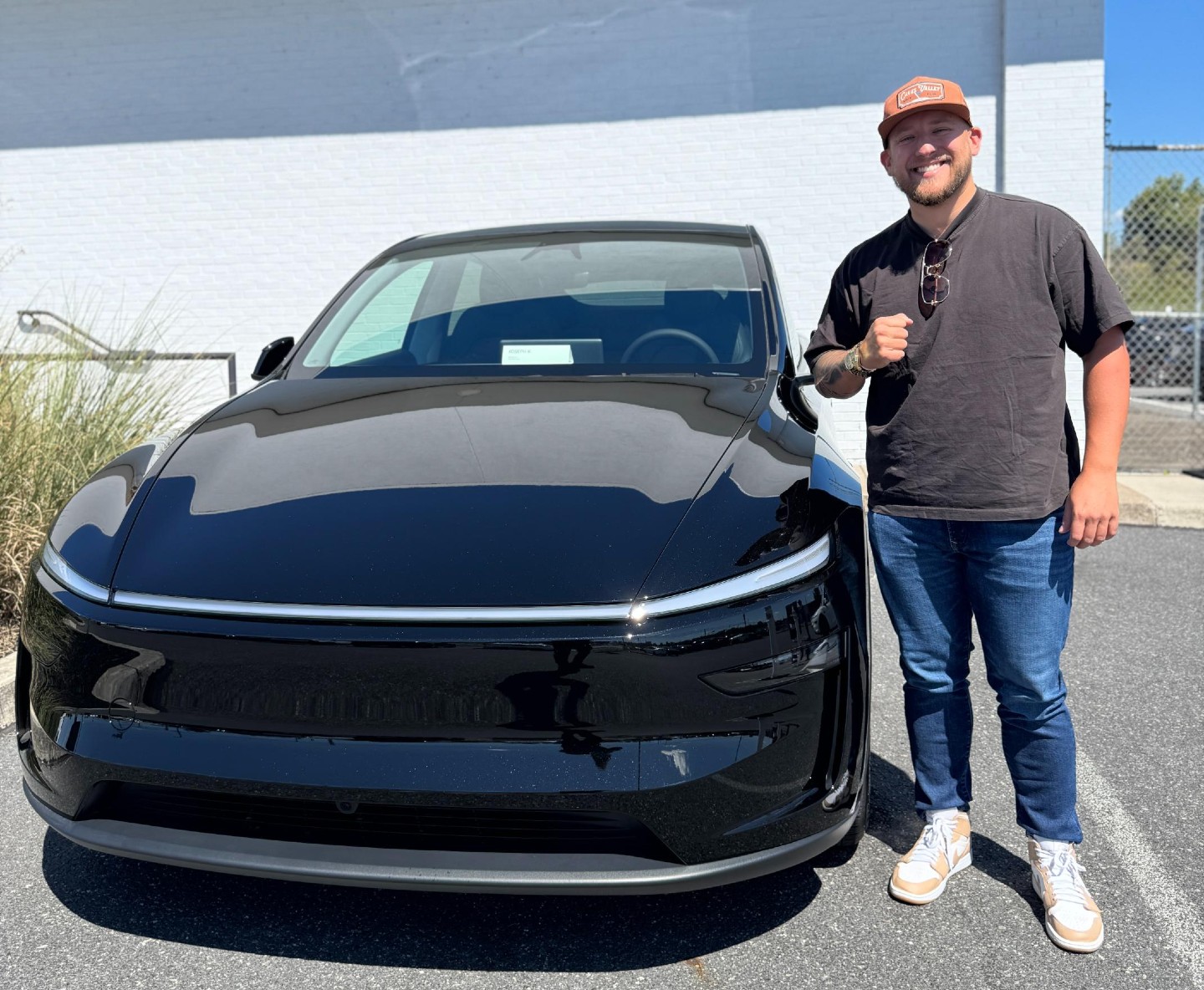
I recently decided, after a variety of things, that I was going to trade in my internal combustion engine (ICE) vehicle for a new Tesla Model Y. It was a long time coming.
After working at Teslarati for six years and covering the EV space nearly every single day (I recently published my 5,000th article on here), I figured it was time to make a switch. Over the past few years, there have been days when I would have been better off with an EV, but my Summer and Winter activities, as well as the price, kept me from making the switch.
Recently, I decided that it was time. My 2021 Ford Bronco Sport had been experiencing a number of issues, none major, but numerous sensor replacements. It was an affordable and fun car, but after fixing the Tire Pressure Monitoring System in the front right tire, an EVAP switch valve in the motor two months ago, and some other things, the Bronco became more of a chore (and a drain on my wallet) than anything.
With the timing of the $7,500 tax credit expiring and a substantial amount of positive equity in my Bronco, I knew it was time. My experience was excellent, but I would like to share some insights with our readers about the entire process, which may also help you make the jump. Others were more of a one-time thing, as they were things customers would only deal with as the tax credit went away.
My Decision
I knew I was going to get a Tesla, and my inability to enjoy a good sedan steered me to a Model Y (no hate toward the Model 3, it’s just not for me). I knew with the weather in Pennsylvania, all-wheel drive was a need, and the price difference between the rear-wheel-drive and AWD configurations of the Y made it a no-brainer.
Plus, I really would like to get this thing out on the beach, something I’ve done every Summer since buying the Bronco with my Fiancè.
🚨 COME WITH ME TO TRADE MY ICE VEHICLE FOR A NEW TESLA MODEL Y 🧵 https://t.co/tqNPOK94rF
— TESLARATI (@Teslarati) August 30, 2025
I actually ordered this car back in June, but ended up canceling the reservation to wait until the end of Summer. I ended up ordering the car I took delivery of on Saturday back on my birthday on August 16.
I was looking for Diamond Black with White Interior, and it was available in Pittsburgh for delivery. However, I really love the team at Tesla Mechanicsburg, so I opted to do a Black on Black Model Y that was a Fremont build, so I could pick it up from the guys up there. The interior color was not a dealbreaker for me. I just wanted to take delivery soon.
I ordered from inventory, which is not something that is possible now. There is no new Model Y inventory within 200 miles of me, a good sign for Tesla but a bad sign if you’re looking to buy something before the quarter ends. Luckily, the IRS is allowing people to enter an agreement for a car, so you could technically build the car of your choice, put a down payment on it, and take delivery after the September 30 cutoff.
Tesla Delivery Day
My appointment was at 12 p.m. and I arrived about ten minutes before. The team greeted me quickly, and I was able to walk right up and see my car with my name on it. It was pretty incredible and a feeling I have not felt in a long time. I’ll be honest, when I bought the Bronco, I never thought I’d own one. When I got one, it felt pretty surreal.
I felt that way yesterday. It was really cool to finally buy a car that I’d only dreamed of owning. It’s not the only car I dream of owning in my lifetime, but it is one I knew I wanted right now. Now that I was showing up to buy it, it really felt surreal.
The process was really fast and efficient, and I could have been in and out in ten minutes if I wanted to. However, I hung around and talked to the guys there; they discussed some good accessories I should consider and suggested some tint.
I was on my way.
My First Drive and What to Expect
I stopped by my Fiancè’s work, showed her the new ride, brought her some lunch, and headed home to my pup. So far, I’ve driven about 60 miles, with most of it being done manually and about 10 miles using Full Self-Driving. I’ve enjoyed driving it myself so much as of right now, but I know FSD will come in handy plenty in the coming months.
My brand new ride! Thank you @tesla @elonmusk for building one badass car
— Joey Klender (@KlenderJoey) August 30, 2025
In the future, I plan to explore a wide range of topics as an owner. I do not currently have home charging, which is something that many people believe is a dealbreaker for owning an EV. I have two Superchargers very close to my place, so I’m not too concerned about it.
I have been in touch with my leasing office about installing a charger or chargers for the past few months, which seems like it could happen early next year.
So far, I’m really happy with how everything has worked out.
News
Tesla Model Y Performance gets positive review from Swedish auto outlet
The refreshed Model Y Performance model receives unique bumpers, red brake calipers, new wheels, and a carbon fiber spoiler.
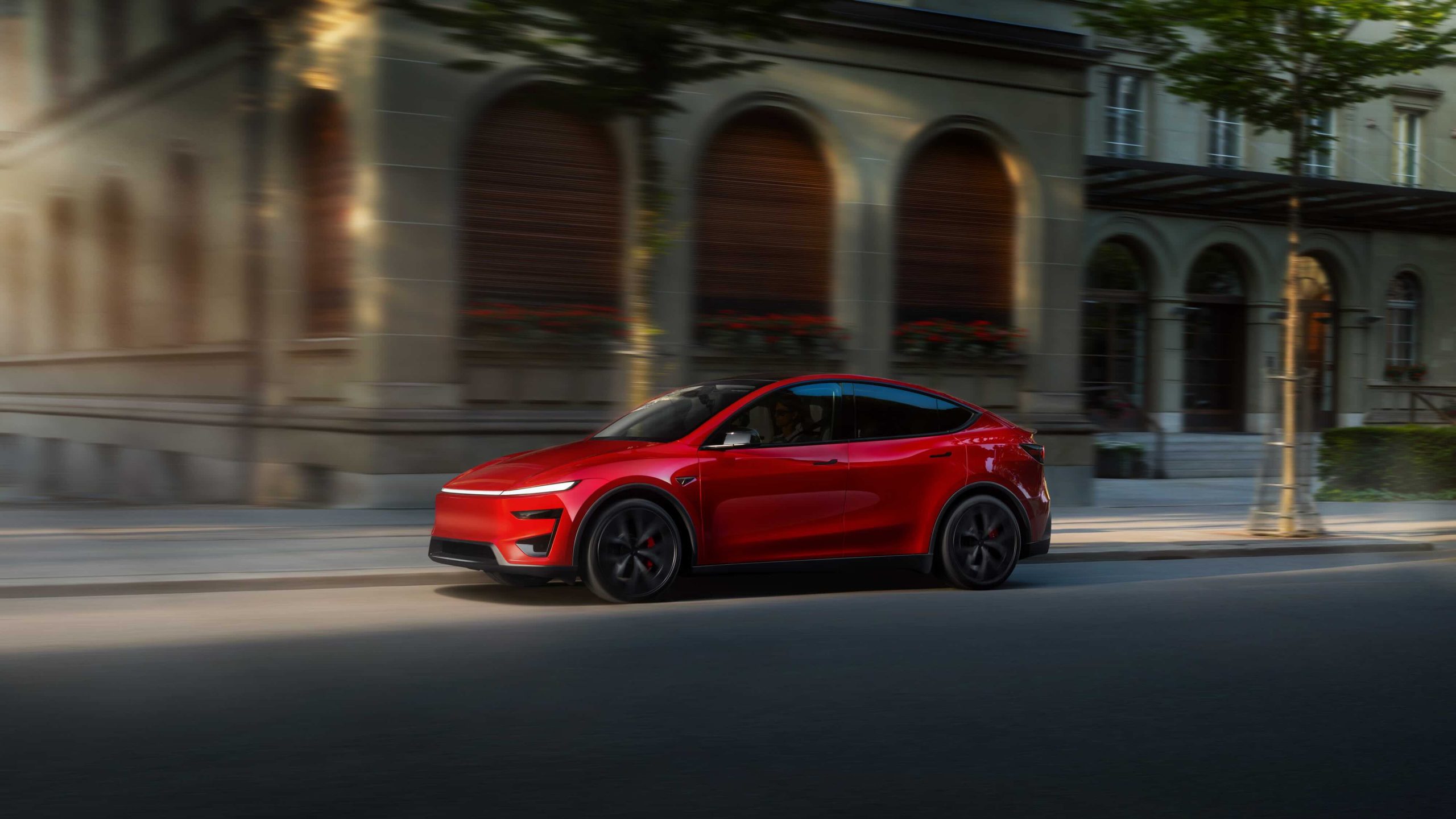
It appears that Tesla has created something special with the new Model Y Performance. The vehicle, which was released earlier late August, has started receiving rave reviews, some of it even from publications that tend to be critical of the EV maker and CEO Elon Musk.
Model Y Performance impressions
Swedish automotive outlet CarUp.se has given the updated Tesla Model Y Performance high marks, highlighting its redesigned sport seats as a standout improvement. Tesla implemented a number of key improvements to the Model Y Performance, such as its redesigned sports seats, which now feature powered thigh extensions like those found in the Model Y L from China.
To summarize, its review, the publication noted that “In addition to making you sit like a king, (the Model Y Performance) is also extremely fast at red lights.” The publication highlighted that “the exterior of the Tesla quickly reveals that it is a Tesla Performance model and there is no doubt that it is a really good-looking electric car.” This is quite impressive considering that the previous-generation Model Y Performance looked quite tame compared to the Model S and X Plaid and the Model 3 Performance.
Tweaks and improvements
The refreshed Model Y Performance model receives unique bumpers, red brake calipers, new wheels, and a carbon fiber spoiler, which together give the crossover a more athletic appearance. Performance badging and projection lighting further distinguish it from other Model Y variants. Inside, the upgraded front sport seats deliver noticeably improved support compared to the standard version, enhancing the vehicle’s balance of comfort and sportiness.
The new Model Y Performance deliver 460 horsepower and a top speed of 250 km/h, while consumption is listed at 16.2 kWh/100 km and range at 580 km WLTP. The crossover also benefits from adaptive suspension with preset damping modes. Manufactured at Gigafactory Berlin-Brandenburg, the Model Y Performance is currently available in Europe and the Middle East, with deliveries expected to start in the next 1-2 months.
-
Elon Musk3 days ago
Elon Musk shares unbelievable Starship Flight 10 landing feat
-
News2 days ago
Tesla is overhauling its Full Self-Driving subscription for easier access
-
Elon Musk5 days ago
SpaceX Starship Flight 10 was so successful, it’s breaking the anti-Musk narrative
-
Elon Musk4 days ago
Elon Musk reveals when SpaceX will perform first-ever Starship catch
-
News3 days ago
Tesla expands crazy new lease deal for insane savings on used inventory
-
News4 days ago
Tesla launches Full Self-Driving in a new region
-
News3 days ago
Tesla talks Semi ramp, Optimus, Robotaxi rollout, FSD with Wall Street firm
-
News4 days ago
Tesla Robotaxi rival Waymo confirms massive fleet expansion in Bay Area