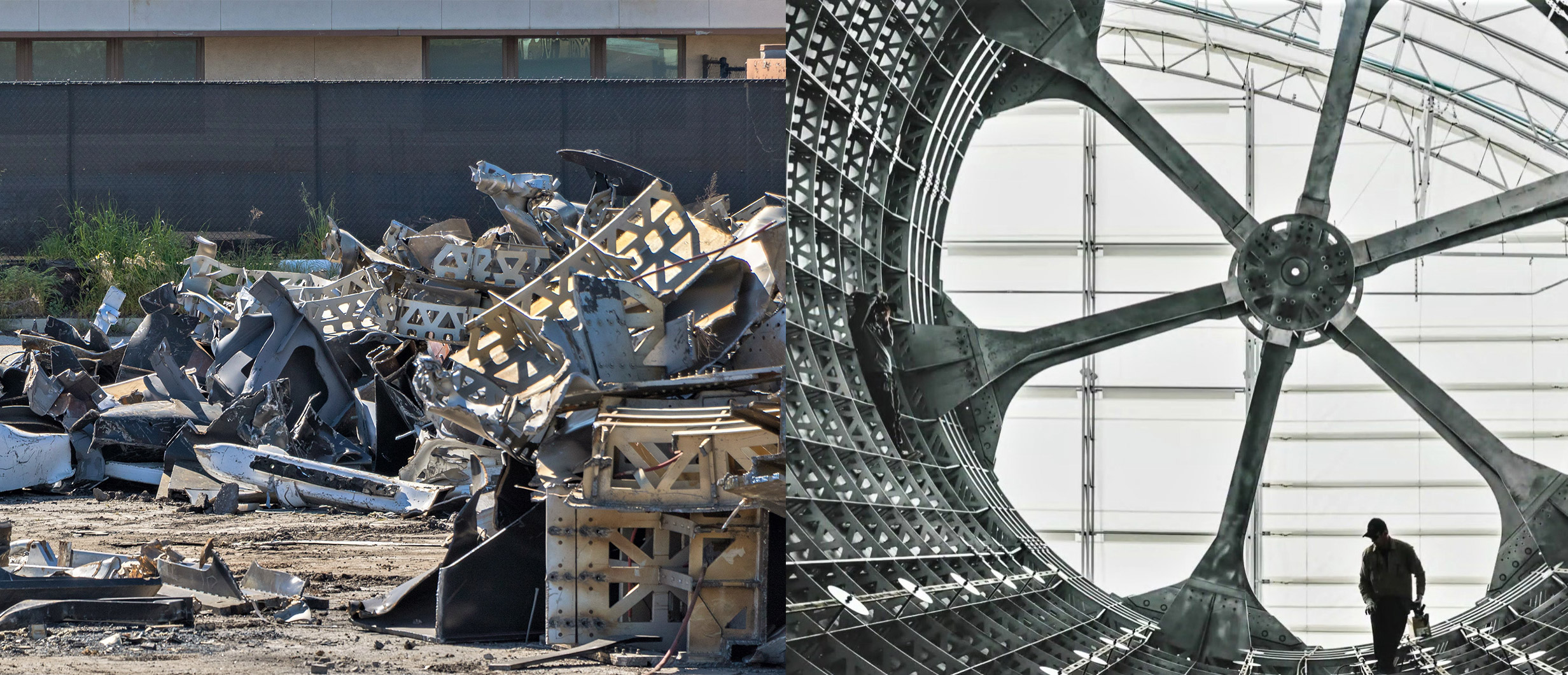
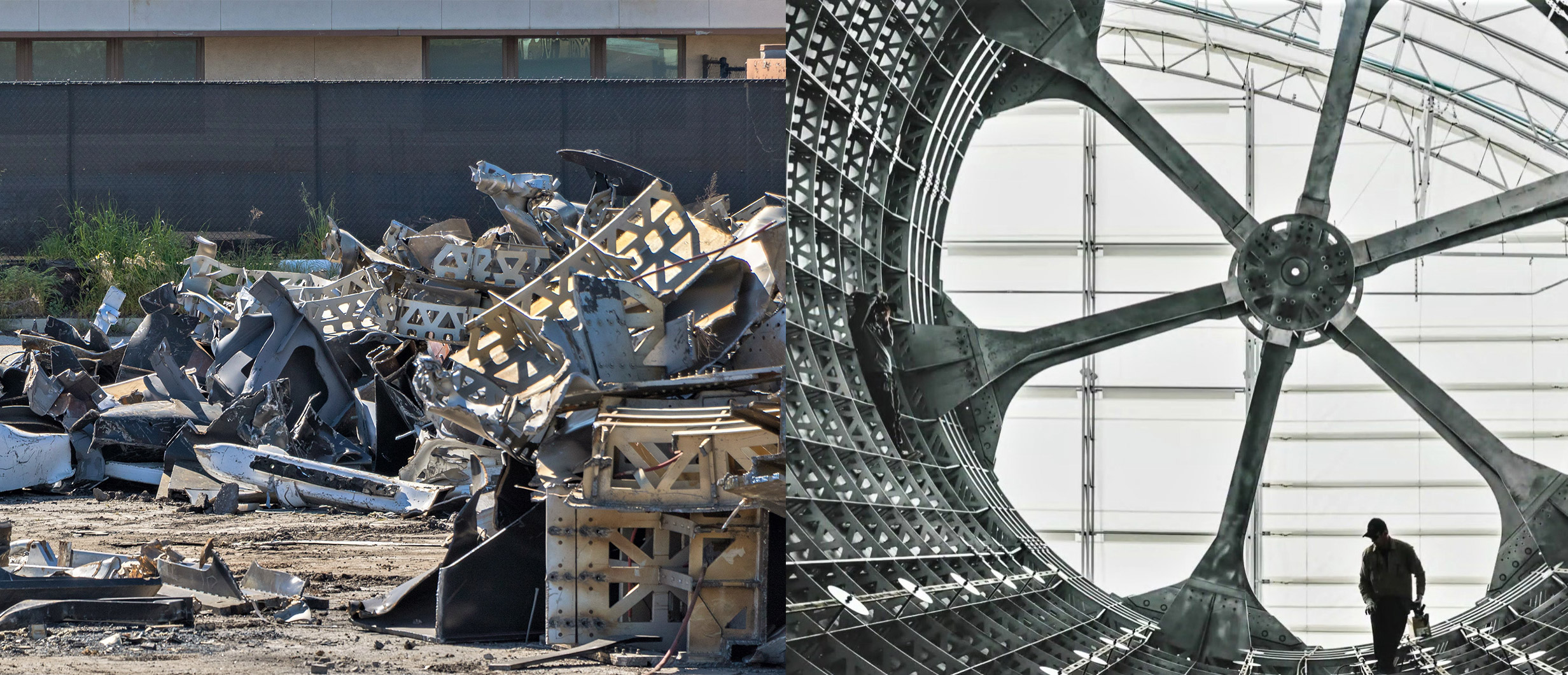
SpaceX
SpaceX goes all-in on steel Starship, scraps expensive carbon fiber BFR tooling
In a wholly unforeseen turn of events, SpaceX has taken the extraordinary step of permanently scrapping both its Port of Los Angeles-based BFR development tent and what seem to be the majority of what it contained, irreparably destroying custom-built tooling meant to support the fabrication of carbon composite BFR spaceships and boosters.
Likely worth anywhere from several to tens of millions of dollars (USD), SpaceX’s advanced BFR production tools were procured from industry-expert Ascent Aerospace sometime in 2017 before being officially delivered to the rocket company’s newly-erected Port of LA tent around April 2018. Situated at the port specifically due to logistical concerns about the high cost of transporting 9m/30ft-diameter objects from SpaceX’s main Hawthorne facilities to a barge for transport east, the company has decided to unequivocally destroy its aerospace-grade composite tooling less than 12 months after accepting delivery. Put simply, this is the best evidence yet that SpaceX – willing or not – has gone all-in on build Starship and Super Heavy out of stainless steel less than six months after CEO Elon Musk began to hint at the program’s utterly radical pivot.
From the very beginning of SpaceX and Elon Musk’s serious pursuit of an entirely reusable launch vehicle capable of transporting dozens of astronauts and passengers to and from Earth and Mars, the plan had been to build the vast majority of the rocket’s booster and spacecraft structures out of advanced carbon fiber composite materials. Above all else, this fundamental architecture was motivated largely by the significant performance gains a rocket could achieve by replacing traditional aluminum tanks and structures with carbon fiber.
For a rocket (and especially an orbital spaceship) meant to somehow make Earth-Mars transport both routine and at least minutely affordable, focusing primarily on the optimization of the mass of cargo delivered relative to the empty weight of the spaceship and booster made (and still does make) a great deal of sense. Assuming that the reusability of a system is roughly constant, the only conceivable way to further lower the cost of price per unit of cargo or passenger ticket would be to increase the usable cargo/passenger capacity for each individual launch, making an extremely light and high-performance rocket the low-hanging fruit target.
The centrality of carbon fiber composites remained with SpaceX’s Sept. 2017 iteration of BFR, downsized by 25% to a diameter of 9m (~30 ft). Around six months later, that commitment to composites was further solidified by the delivery of the first 9m-diameter carbon fiber tooling in March or April 2018. The tooling used to mold and
In the subsequent months of 2018, SpaceX’s BFR and composite R&D team spent tens of thousands of hours building out an ad-hoc advanced composites workshop inside a temporary tent in an industrial area, and ultimately managed to build a number of full-scale carbon fiber segments, including at least one large tank barrel section and the beginnings of a tank dome. In September 2018, that progress was partially revealed alongside the announcement that Japanese billionaire Yasuka Maezawa had purchased the first crewed lunar launch of BFR for several hundred million dollars, set to occur no earlier than 2023.
Two months after indicating that the first BFR “airframe/tank barrel section” would be built out of a “new carbon fiber material”, Musk provided the very first teaser for a “counterintuitive” development that would later be identified as the CEO’s decision to wholly replace BFR’s proposed used of composites with stainless steel and an advanced metallic heat shield. Still more than a little controversial and hard to follow almost half a year later, the feeling at the time was that SpaceX’s eccentric leader had decided to throw away more than 24 months of composite BFR design and development work for an almost entirely unproven alternative approach.
For better or for worse, it appears that SpaceX (or maybe just Musk) has quite literally trashed the most concrete demonstration of a prior commitment to advanced carbon fiber composites, scrapping the vast majority of its composite tooling and perhaps even the prototype BFR segments built in 2018.
It remains to be seen whether the now-permanent decision to pursue a stainless steel design in place of carbon fiber was a very expensive mistake, a stroke of genius, or something in between, However, the undeniably brisk progress made with the BFR’s steel variant in last four or so months bodes well – at a minimum – for Musk’s optimism that this radical change will ultimately result in an operational vehicle far sooner (and presumably cheaper) than the composites route.
Generally speaking, it seems safe to – on the face of it – agree with Musk’s argument that steel should ultimately lend itself far more easily to reusability thanks to its high tolerance for extreme temperatures. Unlike Falcon 9’s aluminum structures (and even the most exotic, advanced carbon fiber composites), certain varieties of stainless steel can weather heating approaching that experienced during orbital reentry with minimal erosion or damage to its mechanical properties. As Musk puts it, the Super Heavy booster’s suborbital trajectory could require almost no heat shielding – and perhaps even paint – at all.
Only time will tell whether the inevitably harsher realities of real-life engineering are so kind. In the meantime, SpaceX is perhaps just hours away from the first attempted static-fire test of a Raptor installed on something approaching flight-hardware, in this case a full-scale Starship hop test prototype.
Check out Teslarati’s Marketplace! We offer Tesla accessories, including for the Tesla Cybertruck and Tesla Model 3.
News
SpaceX launches Ax-4 mission to the ISS with international crew
The SpaceX Falcon 9 launched Axiom’s Ax-4 mission to ISS. Ax-4 crew will conduct 60+ science experiments during a 14-day stay on the ISS.
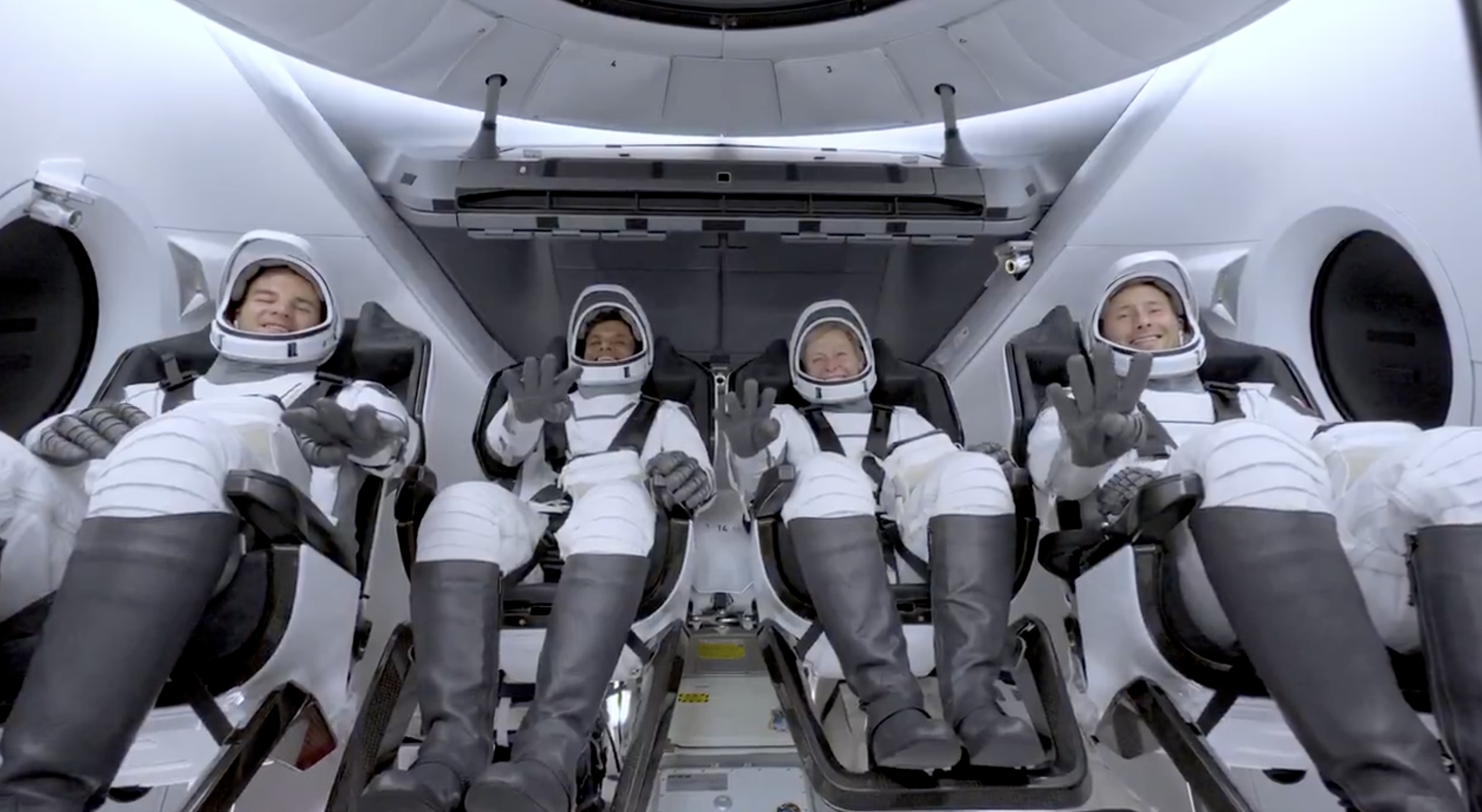
SpaceX launched the Falcon 9 rocket kickstarting Axiom Space’s Ax-4 mission to the International Space Station (ISS). Axiom’s Ax-4 mission is led by a historic international crew and lifted off from Kennedy Space Center’s Launch Complex 39A at 2:31 a.m. ET on June 25, 2025.
The Ax-4 crew is set to dock with the ISS around 7 a.m. ET on Thursday, June 26, 2025. Axiom Space, a Houston-based commercial space company, coordinated the mission with SpaceX for transportation and NASA for ISS access, with support from the European Space Agency and the astronauts’ governments.
The Ax-4 mission marks a milestone in global space collaboration. The Ax-4 crew, commanded by U.S. astronaut Peggy Whitson, includes Shubhanshu Shukla from India as the pilot, alongside mission specialists Sławosz Uznański-Wiśniewski from Poland and Tibor Kapu from Hungary.
“The trip marks the return to human spaceflight for those countries — their first government-sponsored flights in more than 40 years,” Axiom noted.
Shukla’s participation aligns with India’s Gaganyaan program planned for 2027. He is the first Indian astronaut to visit the ISS since Rakesh Sharma in 1984.
Axiom’s Ax-4 mission marks SpaceX’s 18th human spaceflight. The mission employs a Crew Dragon capsule atop a Falcon 9 rocket, designed with a launch escape system and “two-fault tolerant” for enhanced safety. The Axiom mission faced a few delays due to weather, a Falcon 9 leak, and an ISS Zvezda module leak investigation by NASA and Roscosmos before the recent successful launch.
As the crew prepares to execute its scientific objectives, SpaceX’s Ax-4 mission paves the way for a new era of inclusive space research, inspiring future generations and solidifying collaborative ties in the cosmos. During the Ax-4 crew’s 14-day stay in the ISS, the astronauts will conduct nearly 60 experiments.
“We’ll be conducting research that spans biology, material, and physical sciences as well as technology demonstrations,” said Whitson. “We’ll also be engaging with students around the world, sharing our experience and inspiring the next generation of explorers.”
SpaceX’s Ax-4 mission highlights Axiom’s role in advancing commercial spaceflight and fostering international partnerships. The mission strengthens global space exploration efforts by enabling historic spaceflight returns for India, Poland, and Hungary.
News
Starlink Cellular’s T-Mobile service to grow with third-party app data
From Oct 2025, T-Satellite will enable third-party apps in dead zones! WhatsApp, X, AccuWeather + more coming soon.
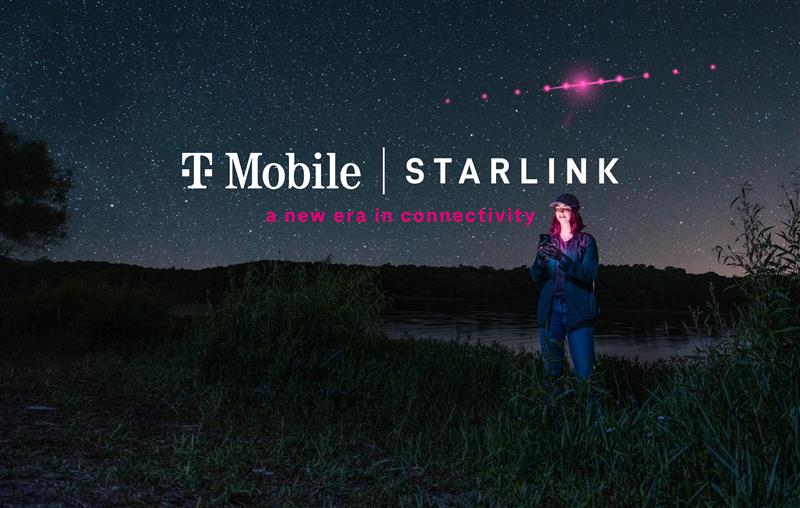
Starlink Cellular’s T-Mobile service will expand with third-party app data support starting in October, enhancing connectivity in cellular dead zones.
T-Mobile’s T-Satellite, supported by Starlink, launches officially on July 23. Following its launch, T-Mobile’s Starlink Cellular service will enable data access for third-party apps like WhatsApp, X, Google, Apple, AccuWeather, and AllTrails on October 1, 2025.
T-Mobile’s Starlink Cellular is currently in free beta. T-Satellite will add MMS support for Android phones on July 23, with iPhone support to follow. MMS support allows users to send images and audio clips alongside texts. By October, T-Mobile will extend emergency texting to all mobile users with compatible phones, beyond just T-Mobile customers, building on its existing 911 texting capability. The carrier also provides developer tools to help app makers integrate their software with T-Satellite’s data service, with plans to grow the supported app list.
T-Mobile announced these updates during an event celebrating an Ookla award naming it the best U.S. phone network, a remarkable turnaround from its last-place ranking a decade ago.
“We not only dream about going from worst to best, we actually do it. We’re a good two years ahead of Verizon and AT&T, and I believe that lead is going to grow,” said T-Mobile’s Chief Operating Officer Srini Gopalan.
T-Mobile unveiled two promotions for its Starlink Cellular services to attract new subscribers. A free DoorDash DashPass membership, valued at $10/month, will be included with popular plans like Experience Beyond and Experience More, offering reduced delivery and service fees. Meanwhile, the Easy Upgrade promotion targets Verizon customers by paying off their phone balances and providing flagship devices like the iPhone 16, Galaxy S25, or Pixel 9.
T-Mobile’s collaboration with SpaceX’s Starlink Cellular leverages orbiting satellites to deliver connectivity where traditional networks fail, particularly in remote areas. Supporting third-party apps underscores T-Mobile’s commitment to enhancing user experiences through innovative partnerships. As T-Satellite’s capabilities grow, including broader app integration and emergency access, T-Mobile is poised to strengthen its lead in the U.S. wireless market.
By combining Starlink’s satellite technology with strategic promotions, T-Mobile is redefining mobile connectivity. The upcoming third-party app data support and official T-Satellite launch mark a significant step toward seamless communication, positioning T-Mobile as a trailblazer in next-generation wireless services.
News
Starlink expansion into Vietnam targets the healthcare sector
Starlink aims to deliver reliable internet to Vietnam’s remote clinics, enabling telehealth and data sharing.

SpaceX’s Starlink expansion into Vietnam targets its healthcare sector. Through Starlink, SpaceX seeks to drive digital transformation in Vietnam.
On June 18, a SpaceX delegation met with Vietnam’s Ministry of Health (MoH) in Hanoi. SpaceX’s delegation was led by Andrew Matlock, Director of Enterprise Sales, and the discussions focused on enhancing connectivity for hospitals and clinics in Vietnam’s remote areas.
Deputy Minister of Health (MoH) Tran Van Thuan emphasized collaboration between SpaceX and Vietnam. Tran stated: “SpaceX should cooperate with the MoH to ensure all hospitals and clinics in remote areas are connected to the StarLink satellite system and share information, plans, and the issues discussed by members of the MoH. The ministry is also ready to provide information and send staff to work with the corporation.”
The MoH assigned its Department of Science, Technology, and Training to work with SpaceX. Starlink Vietnam will also receive support from Vietnam’s Department of International Cooperation. Starlink Vietnam’s agenda includes improving internet connectivity for remote healthcare facilities, developing digital infrastructure for health examinations and remote consultations, and enhancing operational systems.
Vietnam’s health sector is prioritizing IT and digital transformation, focusing on electronic health records, data centers, and remote medical services. However, challenges persist in deploying IT solutions in remote regions, prompting Vietnam to seek partnerships like SpaceX’s.
SpaceX’s Starlink has a proven track record in healthcare. In Rwanda, its services supported 40 health centers, earning praise for improving operations. Similarly, Starlink enabled remote consultations at the UAE’s Emirati field hospital in Gaza, streamlining communication for complex medical cases. These successes highlight Starlink’s potential to transform Vietnam’s healthcare landscape.
On May 20, SpaceX met with Vietnam’s Ministry of Industry and Trade, announcing a $1.5 billion investment to provide broadband internet, particularly in remote, border, and island areas. The first phase includes building 10-15 ground stations across the country. This infrastructure will support Starlink’s healthcare initiatives by ensuring reliable connectivity.
Starlink’s expansion in Vietnam aligns with the country’s push for digital transformation, as outlined by the MoH. By leveraging its satellite internet expertise, SpaceX aims to bridge connectivity gaps, enabling advanced healthcare services in underserved regions. This collaboration could redefine Vietnam’s healthcare infrastructure, positioning Starlink as a key player in the nation’s digital future.
-
Elon Musk2 weeks ago
Tesla investors will be shocked by Jim Cramer’s latest assessment
-
Elon Musk2 days ago
xAI launches Grok 4 with new $300/month SuperGrok Heavy subscription
-
Elon Musk4 days ago
Elon Musk confirms Grok 4 launch on July 9 with livestream event
-
News1 week ago
Tesla Model 3 ranks as the safest new car in Europe for 2025, per Euro NCAP tests
-
Elon Musk2 weeks ago
A Tesla just delivered itself to a customer autonomously, Elon Musk confirms
-
Elon Musk1 week ago
xAI’s Memphis data center receives air permit despite community criticism
-
News2 weeks ago
Xiaomi CEO congratulates Tesla on first FSD delivery: “We have to continue learning!”
-
News2 weeks ago
Tesla sees explosive sales growth in UK, Spain, and Netherlands in June