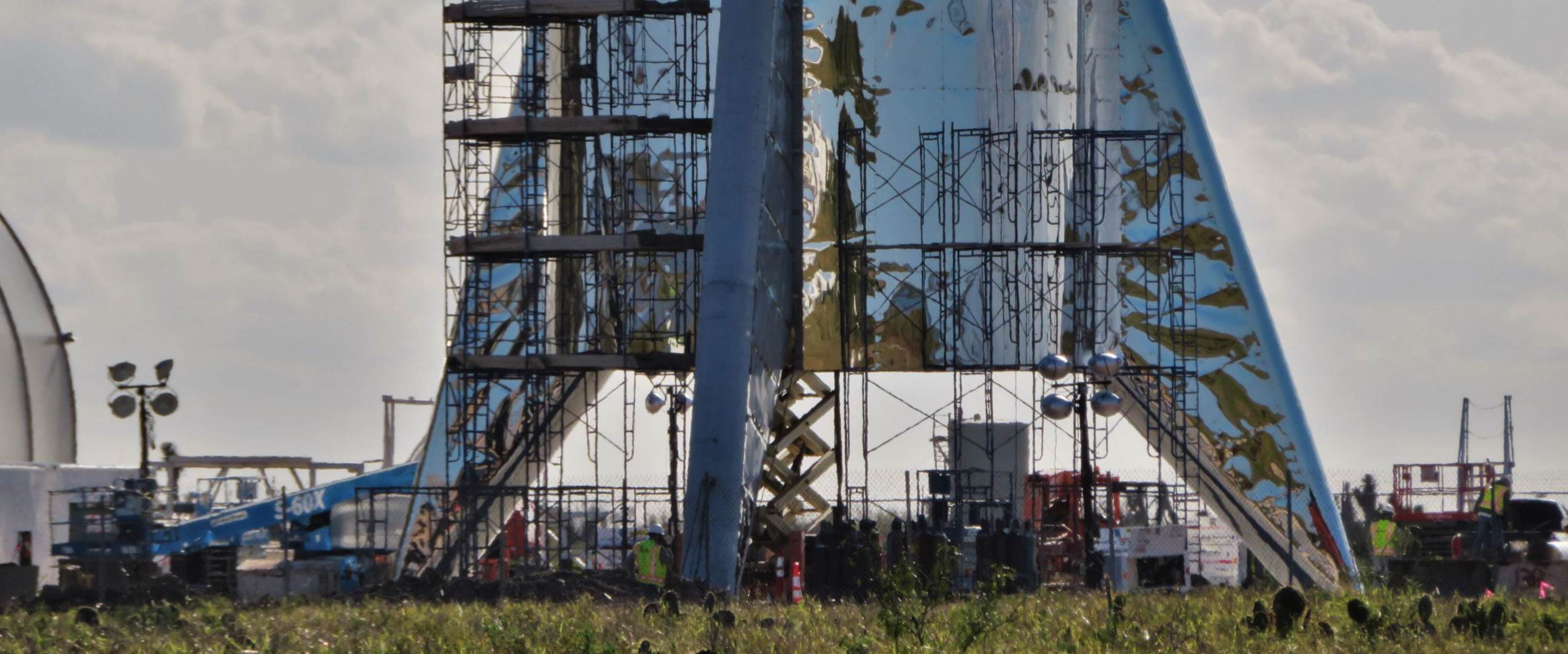
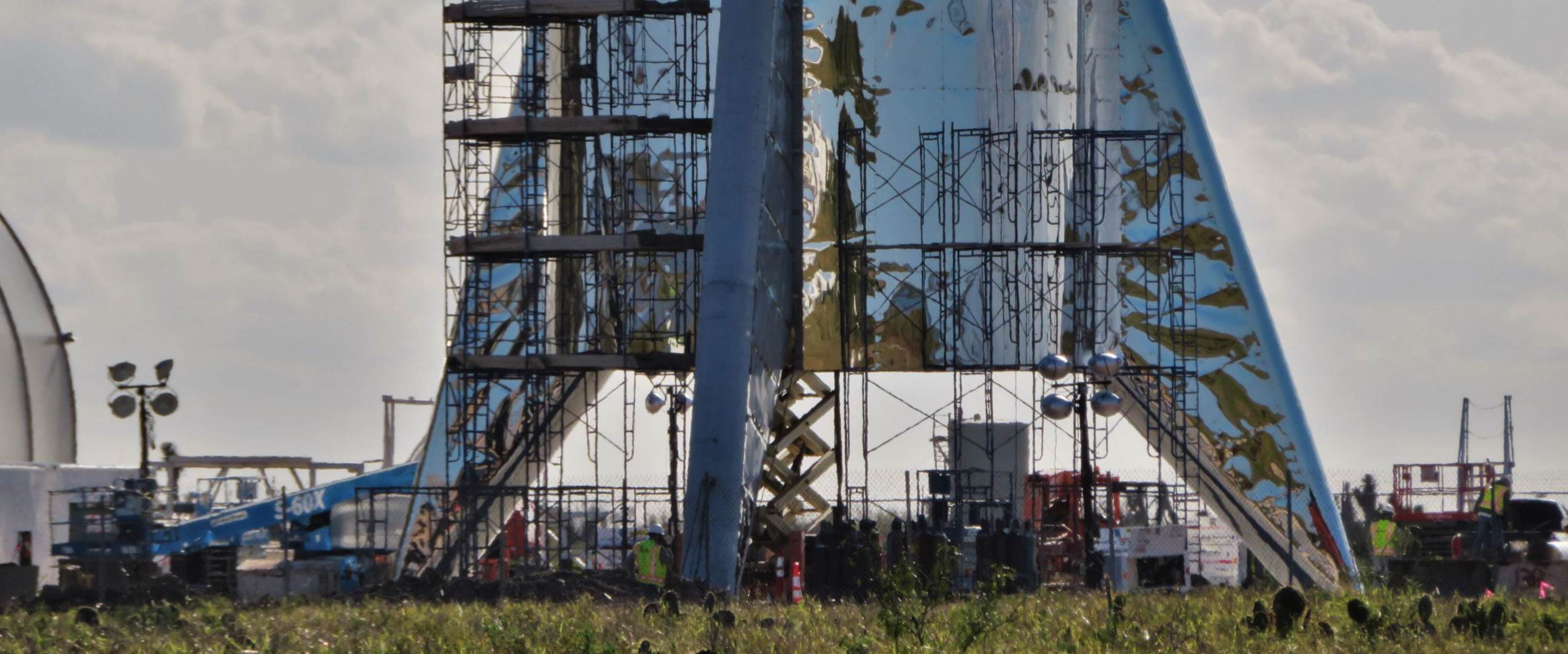
SpaceX
SpaceX CEO Elon Musk says that BFR could cost less to build than Falcon 9
SpaceX CEO Elon Musk believes that there may be a path for the company to ultimately build the massive Starship spacecraft and Super Heavy booster (formerly BFR) for less than Falcon 9/Falcon Heavy, a rocket 3-9 times smaller than BFR.
While it certainly ranks high on the list of wild and wacky things the CEO has said over the years, there may be a few ways – albeit with healthy qualifications – that Starship/Super Heavy production costs could ultimately compare favorably with SpaceX’s Falcon family of launch vehicles. Nevertheless, there are at least as many ways in which the next-gen rocket can (or should) never be able to beat the production cost of what is effectively a far simpler rocket.
This will sound implausible, but I think there’s a path to build Starship / Super Heavy for less than Falcon 9
— Elon Musk (@elonmusk) February 11, 2019
Dirty boosters done dirt cheap
On the one hand, Musk might not necessarily be wrong, especially if one throws the CEO several bones in the interpretation of his brief tweet. BFR at its simplest is going to require a full 38 main rocket engines to achieve its nominal performance goals, 7 on Starship and 31 on Super Heavy. As a dramatically more advanced, larger, and far more complex engine, Raptor will (with very little doubt) cost far more per engine than the relatively simple Merlin 1D. BFR avionics (flight computers, electronics, wiring, harnesses) are likely to be more of a known quantity, meaning that costs will probably be comparable or even lower than Falcon 9’s when measured as a proportion of overall vehicle cost. Assuming that BFR can use the exact same cold gas thruster assemblies currently flying on Falcon 9, that cost should only grow proportionally with vehicle size. Finally, Starship will not require a deployable payload fairing (~10% of Falcon 9’s production cost).
All of those things mean that Starship/Super Heavy will probably be starting off with far better cost efficiency than Falcon 9 was able to, thanks to almost a decade of interim experience both building, flying, and refurbishing the rocket since its 2010 debut. Still, BFR will have to account for entirely new structures like six large tripod fins/wings and their actuators, wholly new thrust structures (akin to Falcon 9’s octaweb) for both stages, and more. Considering Starship on its own, the production of a human-rated spacecraft capable of safely housing dozens of people in space for weeks or months will almost without a doubt rival the cost of airliner production, where a 737 – with almost half a century of production and flight heritage – still holds a price tag of $100-130+ million.
- BFR shown to scale with Falcon 1, 9, and Heavy. (SpaceX)
- A September 2018 render of Starship (then BFS) shows one of the vehicle’s two hinged wings/fins/legs. (SpaceX)
- BFR’s booster, now known as Super Heavy. (SpaceX)
- Sadly, this is a not a sight that will greet Falcon 9 booster B1046’s fourth launch – Crew Dragon’s critical In-Flight Abort test. (SpaceX)
Adding one more assumption, the most lenient interpretation of Musk’s tweet assumes that he is really only subjecting the overall structure (sans engines and any crew-relevant hardware) of BFR relative to Falcon 9. In other words, could a ~300-ton stainless steel rocket structure (BFR) cost the same amount or less to fabricate than a ~30-ton aluminum-lithium alloy rocket structure (Falcon 9/Heavy)? From the very roughest of numerical comparisons, Musk estimated the cost of the stainless steel alloys (300-series) to be used for BFR at around $3 per pound ($6.60/kg), while aluminum-lithium alloys used in aerospace (and on Falcon 9) are sold for around $20/lb ($44/kg)*. As such, simply buying the materials to build the basic structures of BFR and Falcon 9 would cost around and $7.5M and $5M, respectively.
Assuming that the process of assembling, welding, and integrating Starship and Super Heavy structures is somehow 5-10 times cheaper, easier, and less labor-intensive, it’s actually not inconceivable that the cost of building BFR’s structure could ultimately compete with Falcon 9 after production has stabilized after the new rocket’s prototyping phase is over and manufacturing processes are mature.
*Very rough estimate, difficult to find a public cost per unit mass from modern Al-Li suppliers

Costs vs. benefits
On the opposite hand, stainless steel rockets do not have a history of being uniquely cost-effective relative to vehicles using alternative materials. The only orbital-class launch vehicles to use stainless steel (and balloon) tanks are the Atlas booster and the Centaur upper stage, with Atlas dating back to the late 1950s and Centaur beginning launches in the early ’60s. Stainless steel Atlas launches ended in 2005 with the final Atlas III mission, while multiple forms of Centaur continue to fly regularly on ULA’s Atlas V and Delta IV.
Based on a 1966 contract between NASA and General Dynamics placed shortly after Centaur’s tortured development had largely been completed, Centaur upper stages were priced around $25M apiece (2018 USD). In 1980, the hardware for a dedicated Atlas-Centaur launch of a ~1500 kg Comstar I satellite to GTO cost the US the 2018 equivalent of a bit less than $40M ($71M including miscellaneous administrative costs) – $22.4M for Centaur and $17.6M for Atlas. For Atlas, the rocket’s airframe (tanks and general structure) was purchased for around $8.5M. That version of Atlas-Centaur (Atlas-SLV3D Centaur-D1A) was capable of lifting around 5100 kg (11,250 lb) into Low Earth Orbit (LEO) and 1800 kg (~4000 lb) to geostationary transfer orbit (GTO), while it stood around 40m (130 ft) tall, had a tank diameter of 3.05m (10 ft), and weighed ~150t (330,000 lb) fully fueled.
- Atlas shows off its shiny steel balloon tanks. (SDASM)
- The original space-faring Atlas, known as SM-65, seen here with a Mercury space capsule. (NASA)
- A Centaur upper stage is pictured here in 1964. (NASA)
- Atlas SLV3D is pictured here launching a Comstar I satellite.
- A Falcon 9 booster is seen here near the end of its tank welding, just prior to painting. (SpaceX)
- An overview of SpaceX’s Hawthorne factory floor in early 2018. (SpaceX)
In a very loose sense, that particular stainless steel Atlas variant was about half as large and half as capable as the first flight-worthy version of Falcon 9 at roughly the same price at launch ($60-70M). What does this jaunt through the history books tell us about the prospects of a stainless steel Starship and Super Heavy? Well, not much. The problem with trying to understand and pick apart official claims about SpaceX’s next-generation launch architecture is quite simple: only one family of rockets in the history of the industry (Atlas) regularly flew with stainless steel propellant tanks, a half-century lineage that completed its final launch in 2005.
Generally speaking, an industrial sample size of more or less one makes it far from easy to come to any particular conclusions about a given technology or practice, and SpaceX – according to CEO Elon Musk – fully intends to push past the state of the art of stainless steel rocket tankage with BFR. Ultimately, American Marietta/Martin Marietta/Lockheed Martin was never able to produce launch vehicle variants of the stainless steel Atlas family at a cost more than marginally competitive with Falcon 9, despite the latter rocket’s use of a far more expensive metal alloy throughout its primary tanks and structure.
At least 10X cheaper
— Elon Musk (@elonmusk) February 11, 2019
At some point, it’s even worth asking whether the per-unit cost of Starship and Super Heavy should be relevant at all to their design and construction, at least within reason. If the goal of BFR is to drastically lower the cost of launch by radically improving the ease of reuse, it would be truly bizarre (and utterly unintuitive) if those goals could somehow be achieved without dramatically raising the cost of initial hardware procurement. Perhaps the best close comparison to BFR’s goals, modern airliners are eyewateringly expensive ($100-500M apiece) as a consequence of the extraordinary reliability, performance, efficiency, and longevity customers and regulatory agencies demand from them, although those costs are admittedly not the absolute lowest they could be in a perfect manufacturing scenario.
At the end of the day, it appears that Musk is increasingly of the opinion that the pivot to stainless steel could ultimately make BFR simultaneously “better, faster, [&] cheaper”. However improbable that may be, if it does turn out to be the case, Starship and Super Heavy could be an unfathomable leap ahead for reliable and affordable access to space. It could also be another case of Musk’s excitement and optimism getting the better of him and hyping a given product well beyond what it ultimately is able to achieve. Time will tell!
Check out Teslarati’s newsletters for prompt updates, on-the-ground perspectives, and unique glimpses of SpaceX’s rocket launch and recovery processes!
News
SpaceX’s Crew-11 mission targets July 31 launch amid tight ISS schedule
The flight will lift off from Launch Complex 39A at Kennedy Space Center in Florida.
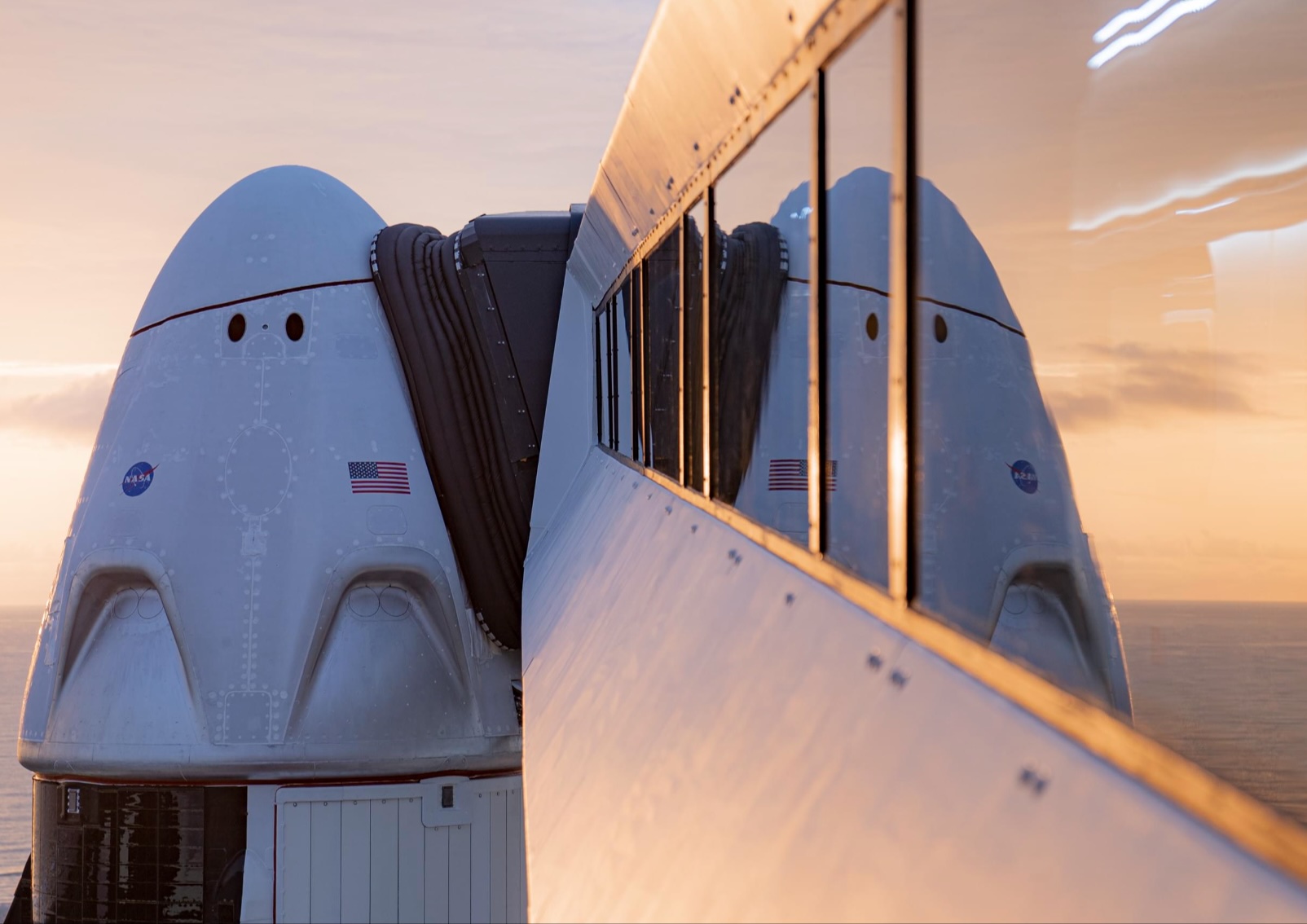
NASA and SpaceX are targeting July 31 for the launch of Crew-11, the next crewed mission to the International Space Station (ISS). The flight will lift off from Launch Complex 39A at Kennedy Space Center in Florida, using the Crew Dragon Endeavour and a Falcon 9 booster.
Crew Dragon Endeavour returns
Crew-11 will be the sixth flight for Endeavour, making it SpaceX’s most experienced crew vehicle to date. According to SpaceX’s director of Dragon mission management, Sarah Walker, Endeavour has already carried 18 astronauts representing eight countries since its first mission with NASA’s Bob Behnken and Doug Hurley in 2020, as noted in an MSN report.
“This Dragon spacecraft has successfully flown 18 crew members representing eight countries to space already, starting with (NASA astronauts) Bob (Behnken) and Doug (Hurley) in 2020, when it returned human spaceflight capabilities to the United States for the first time since the shuttle retired in July of 2011,” Walker said.
For this mission, Endeavour will debut SpaceX’s upgraded drogue 3.1 parachutes, designed to further enhance reentry safety. The parachutes are part of SpaceX’s ongoing improvements to its human-rated spacecraft, and Crew-11 will serve as their first operational test.
The Falcon 9 booster supporting this launch is core B1094, which has launched in two previous Starlink missions, as well as the private Ax-4 mission on June 25, as noted in a Space.com report.
The four-members of Crew-11 are NASA astronauts Zena Cardman and Mike Fincke, as well as Japan’s Kimiya Yui and Russia’s Oleg Platonov.
Tight launch timing
Crew-11 is slated to arrive at the ISS just as NASA coordinates a sequence of missions, including the departure of Crew-10 and the arrival of SpaceX’s CRS-33 mission. NASA’s Bill Spetch emphasized the need for careful planning amid limited launch resources, noting the importance of maintaining station altitude and resupply cadence.
“Providing multiple methods for us to maintain the station altitude is critically important as we continue to operate and get the most use out of our limited launch resources that we do have. We’re really looking forward to demonstrating that capability with (CRS-33) showing up after we get through the Crew-11 and Crew-10 handover,” Spetch stated.
News
SpaceX launches Ax-4 mission to the ISS with international crew
The SpaceX Falcon 9 launched Axiom’s Ax-4 mission to ISS. Ax-4 crew will conduct 60+ science experiments during a 14-day stay on the ISS.
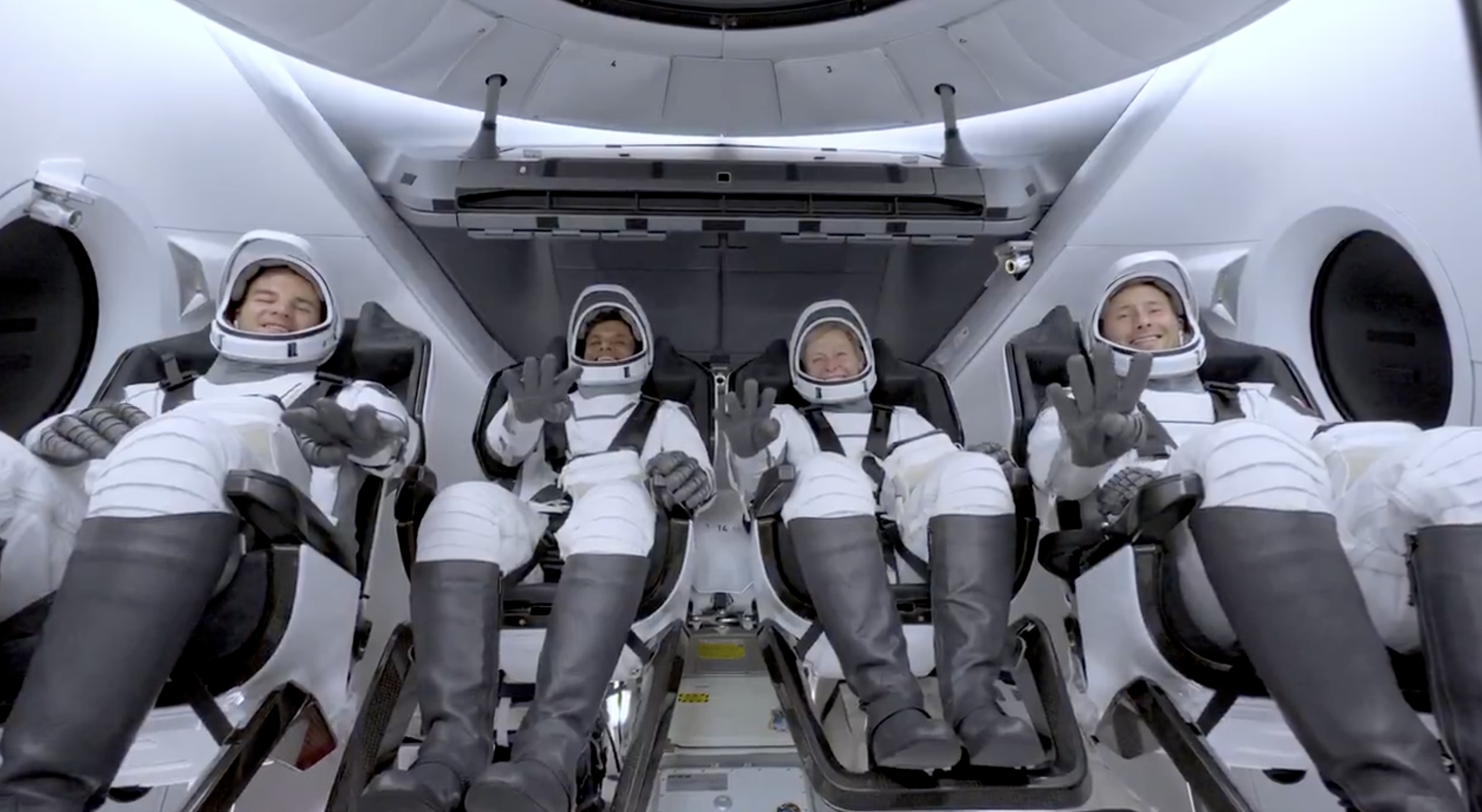
SpaceX launched the Falcon 9 rocket kickstarting Axiom Space’s Ax-4 mission to the International Space Station (ISS). Axiom’s Ax-4 mission is led by a historic international crew and lifted off from Kennedy Space Center’s Launch Complex 39A at 2:31 a.m. ET on June 25, 2025.
The Ax-4 crew is set to dock with the ISS around 7 a.m. ET on Thursday, June 26, 2025. Axiom Space, a Houston-based commercial space company, coordinated the mission with SpaceX for transportation and NASA for ISS access, with support from the European Space Agency and the astronauts’ governments.
The Ax-4 mission marks a milestone in global space collaboration. The Ax-4 crew, commanded by U.S. astronaut Peggy Whitson, includes Shubhanshu Shukla from India as the pilot, alongside mission specialists Sławosz Uznański-Wiśniewski from Poland and Tibor Kapu from Hungary.
“The trip marks the return to human spaceflight for those countries — their first government-sponsored flights in more than 40 years,” Axiom noted.
Shukla’s participation aligns with India’s Gaganyaan program planned for 2027. He is the first Indian astronaut to visit the ISS since Rakesh Sharma in 1984.
Axiom’s Ax-4 mission marks SpaceX’s 18th human spaceflight. The mission employs a Crew Dragon capsule atop a Falcon 9 rocket, designed with a launch escape system and “two-fault tolerant” for enhanced safety. The Axiom mission faced a few delays due to weather, a Falcon 9 leak, and an ISS Zvezda module leak investigation by NASA and Roscosmos before the recent successful launch.
As the crew prepares to execute its scientific objectives, SpaceX’s Ax-4 mission paves the way for a new era of inclusive space research, inspiring future generations and solidifying collaborative ties in the cosmos. During the Ax-4 crew’s 14-day stay in the ISS, the astronauts will conduct nearly 60 experiments.
“We’ll be conducting research that spans biology, material, and physical sciences as well as technology demonstrations,” said Whitson. “We’ll also be engaging with students around the world, sharing our experience and inspiring the next generation of explorers.”
SpaceX’s Ax-4 mission highlights Axiom’s role in advancing commercial spaceflight and fostering international partnerships. The mission strengthens global space exploration efforts by enabling historic spaceflight returns for India, Poland, and Hungary.
News
Starlink Cellular’s T-Mobile service to grow with third-party app data
From Oct 2025, T-Satellite will enable third-party apps in dead zones! WhatsApp, X, AccuWeather + more coming soon.
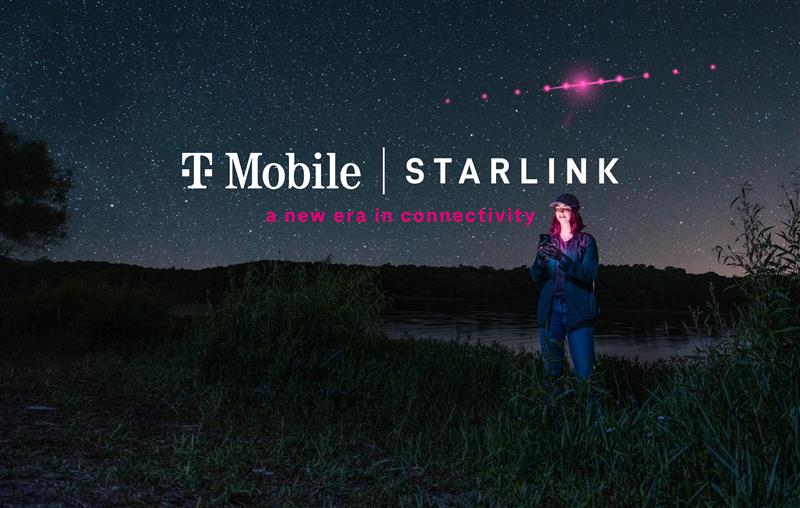
Starlink Cellular’s T-Mobile service will expand with third-party app data support starting in October, enhancing connectivity in cellular dead zones.
T-Mobile’s T-Satellite, supported by Starlink, launches officially on July 23. Following its launch, T-Mobile’s Starlink Cellular service will enable data access for third-party apps like WhatsApp, X, Google, Apple, AccuWeather, and AllTrails on October 1, 2025.
T-Mobile’s Starlink Cellular is currently in free beta. T-Satellite will add MMS support for Android phones on July 23, with iPhone support to follow. MMS support allows users to send images and audio clips alongside texts. By October, T-Mobile will extend emergency texting to all mobile users with compatible phones, beyond just T-Mobile customers, building on its existing 911 texting capability. The carrier also provides developer tools to help app makers integrate their software with T-Satellite’s data service, with plans to grow the supported app list.
T-Mobile announced these updates during an event celebrating an Ookla award naming it the best U.S. phone network, a remarkable turnaround from its last-place ranking a decade ago.
“We not only dream about going from worst to best, we actually do it. We’re a good two years ahead of Verizon and AT&T, and I believe that lead is going to grow,” said T-Mobile’s Chief Operating Officer Srini Gopalan.
T-Mobile unveiled two promotions for its Starlink Cellular services to attract new subscribers. A free DoorDash DashPass membership, valued at $10/month, will be included with popular plans like Experience Beyond and Experience More, offering reduced delivery and service fees. Meanwhile, the Easy Upgrade promotion targets Verizon customers by paying off their phone balances and providing flagship devices like the iPhone 16, Galaxy S25, or Pixel 9.
T-Mobile’s collaboration with SpaceX’s Starlink Cellular leverages orbiting satellites to deliver connectivity where traditional networks fail, particularly in remote areas. Supporting third-party apps underscores T-Mobile’s commitment to enhancing user experiences through innovative partnerships. As T-Satellite’s capabilities grow, including broader app integration and emergency access, T-Mobile is poised to strengthen its lead in the U.S. wireless market.
By combining Starlink’s satellite technology with strategic promotions, T-Mobile is redefining mobile connectivity. The upcoming third-party app data support and official T-Satellite launch mark a significant step toward seamless communication, positioning T-Mobile as a trailblazer in next-generation wireless services.
-
Elon Musk2 weeks ago
Tesla investors will be shocked by Jim Cramer’s latest assessment
-
News2 days ago
Tesla debuts hands-free Grok AI with update 2025.26: What you need to know
-
Elon Musk4 days ago
xAI launches Grok 4 with new $300/month SuperGrok Heavy subscription
-
Elon Musk7 days ago
Elon Musk confirms Grok 4 launch on July 9 with livestream event
-
News1 week ago
Tesla Model 3 ranks as the safest new car in Europe for 2025, per Euro NCAP tests
-
Elon Musk2 weeks ago
xAI’s Memphis data center receives air permit despite community criticism
-
News4 days ago
Tesla begins Robotaxi certification push in Arizona: report
-
Elon Musk2 weeks ago
Tesla scrambles after Musk sidekick exit, CEO takes over sales