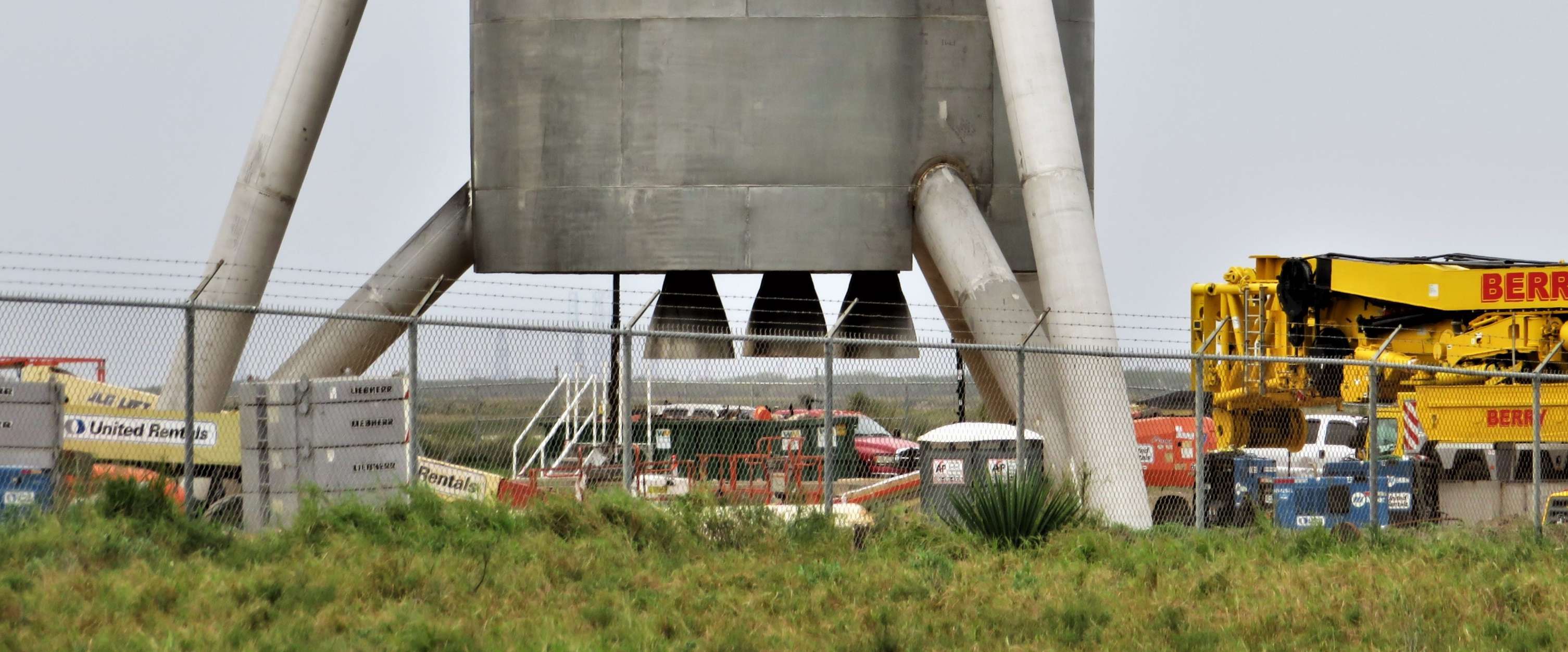
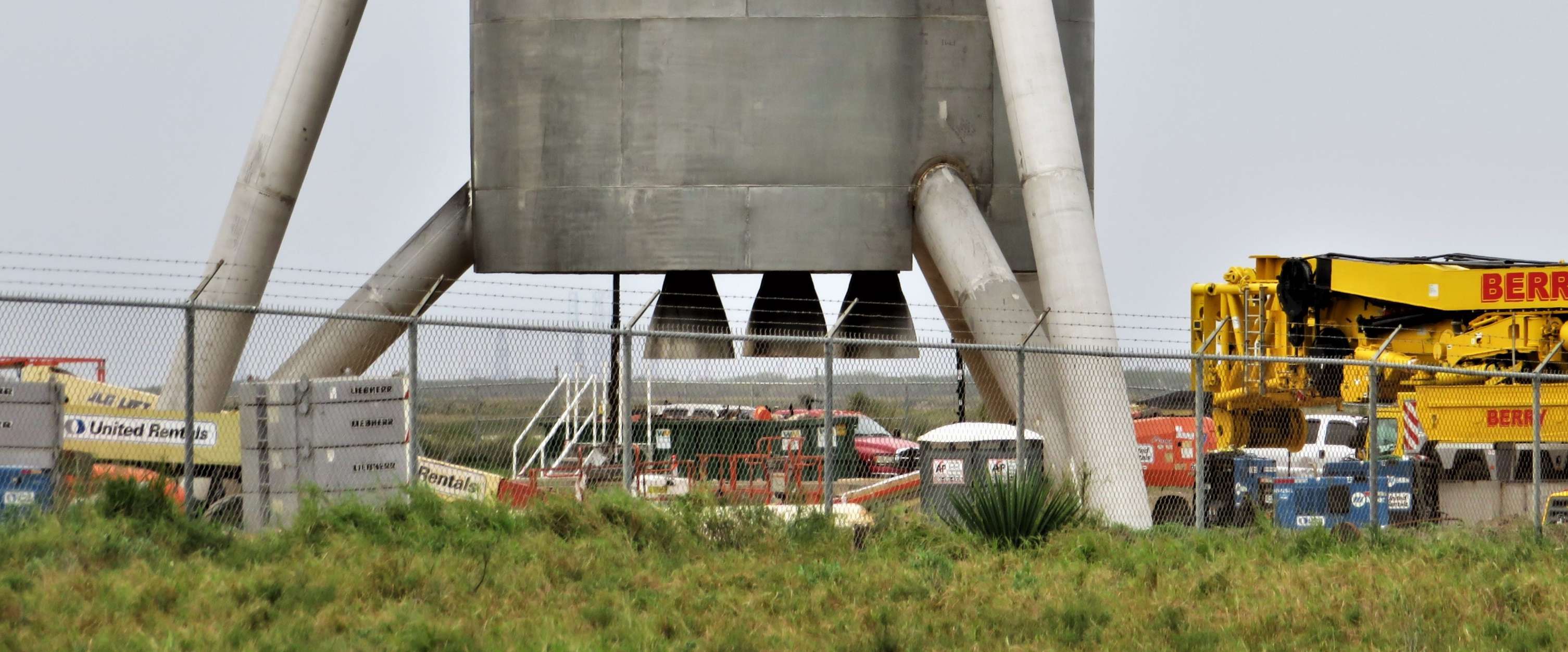
SpaceX
SpaceX’s Starship hopper spotted with trio of dual-bell Raptor engines
Following a brief ‘hop’ (via crane) off of a concrete build stand, the aft section of SpaceX’s first full-scale Starship hopper (Starhopper?) revealed that SpaceX technicians have already installed what appear to be three real Raptor engines, presumably the first time the propulsion system has ever been mounted to something that might eventually fly.
For a number of reasons, there is a strong chance that these Raptors are actually just boilerplate placeholders standing in as structural guides for the real deal some months down the line. On the other hand, there are also a number of reasons to assume that these apparent engines are indeed real Raptors.
Star ship hopper might be a bit bigger than we thought and with the crane placements over the nose end of the vehicle. This could suggest, @SpaceX are planning to move the segment elsewhere perhaps to the welding stand? We will have to wait and see. (Austin Barnard📸) #2019🚀 pic.twitter.com/kn8hhUPWCU
— Austin Barnard🚀 (@austinbarnard45) January 1, 2019
Despite an already shocking series of rapid-fire developments in the South Texas Starhopper saga, the abrupt appearance of what appears to be three Raptor engines – mirroring CEO Elon Musk’s recent statement that the test vehicle would sport three Raptors – is by far the most unexpected moment yet for the prototype Starship. Purportedly a full-scale prototype of BFR’s upper stage/spaceship (now known as Starship), Musk indicated over the last two weeks that the hopper has been designed to perform a number of hop tests in which the craft’s three Raptors would power it to a range of (relatively low) altitudes above Boca Chica, Texas.
According to a recent FCC filing related to this test program, SpaceX is currently seeking a license for Starship hop tests that will not exceed 5 km (3.1 mi) in altitude and/or 6 minutes in duration. There is admittedly nothing mentioned about the maximum allowed velocity during those tests, but – much like Blue Origin performs supersonic tests of New Shepard in Cape Horn, Texas – SpaceX will likely seek and be granted permission to break the sound barrier during those hypothetical tests. Nevertheless, a 5km ceiling is a fairly significant cap on the range of performance Starhopper will be able to test – accelerating vertically at 2Gs, Starhopper could travel from sea level to 5km in less than 30 seconds while reaching speeds no higher than Mach 1-1.5.
- SpaceX technicians and engineers are continuing to work at a breakneck pace on Starhopper. (NASASpaceflight – bocachicagal)
- At this rate, the hopper will likely wind up around 40m (130 feet) tall. (NASASpaceflight – bocachicagal)
- A close examination of these three engine-like protrusions suggests a level of fit and finish far exceeding a boilerplate stand-in. (NASASpaceflight – bocachicagal)
Combined with the apparent fact that this Starhopper’s fins seem unlikely to ever actuate (i.e. no aerodynamic control surfaces), it’s probable that this ad hoc prototype is only meant to perform a very limited range of hop tests, perhaps as basic as ironing out the kinks of operating a trio of gimballed Raptors and ensuring that they can safely and reliably launch, hover, and land a very large Starship-shaped mass simulator. Falcon 9’s Grasshopper and F9R reusability testbeds performed a very similar task some five years ago, offering SpaceX engineers the opportunity to optimize software and hardware needed to reliably recover real orbital-class rockets after launch. Although Falcon 9 has nine gimballed Merlin 1D engines, SpaceX has long sided with the sole center Merlin as the dedicated landing engine and has only briefly experimented with triple-Merlin landing burns.
Dual-expansion whaaaaat?
According to Musk, Raptor – an advanced liquid methane and oxygen engine with a uniquely efficient propulsion cycle – was expected to produce an impressive ~2000 kN (200 ton, 450K lbf) of thrust in its finished form as of September 2018. However, Musk also mentioned in a late-2017 Reddit AMA that SpaceX engineers were modifying the ship’s design to ensure engine-out reliability during all regimes of flight, landing in particular. To accomplish this feat with an engine as powerful as Raptor, two or three Raptors – capable of producing as much as 600 tons of thrust total – would need to reliably throttle as low as 25%, assuming a landing mass of around 150t. To allow a nearly empty ship (~100t) to still reliably land with three Raptors ignited, the engines would need to be able to throttle to 20% or less.
Known as deep throttling in rocketry, ensuring stable combustion and thrust at 20% (let alone 40%) throttle is an extraordinarily challenging feat, often subjecting engines to forces that can literally tear non-optimized hardware apart. To achieve such a deep throttle capability without excessively disrupting the engine’s design, SpaceX appears to have potentially sided with less efficient but extremely simple alternative, known as a dual-bell (or dual-expansion) rocket nozzle. A 1999 Rocketdyne paper concisely explained the primary draws of such a nozzle:
“The [altitude-compensating] dual-bell nozzle offers a unique combination of performance, simplicity, low weight, and ease of cooling” – Horn & Fisher, 1999
Exactly
— Elon Musk (@elonmusk) December 27, 2018
Given that SpaceX has decided to delay the introduction and certification of a vacuum-optimized Raptor engine, choosing to instead use the same Raptor on both BFR stages, something like a dual-bell nozzle would be one of the best possible ways for the company to retain some of the efficiency benefits of a vacuum engine while also drastically improving design simplicity, ease of manufacturing, and cutting development time. Aside from offering efficiency gains by way of altitude compensation, a dual-bell nozzle also happens to enable a given engine to operate a much wider throttle range by mitigating problems with flow separation and instability.
- A gif of Raptor throttling over the course of a 90+ second static-fire test in McGregor, Texas. (SpaceX)
- Note that Merlin 1D and prior Raptor prototypes both feature traditional single nozzles. (Pauline Acalin)
- An overview of dual-bell and deflection nozzles. Raptor appears to have now graduated to the former style. (Johan Steelant, 2011)
- Starhopper’s Raptors feature a very distinct seam and second curve, indicative of a dual-bell nozzle. (NASASpaceflight /u/bocachicagal)
For Starhopper and Starship, both aspects are an undeniable net-gain and it’s entirely possible that these dual-bell nozzles – if successfully demonstrated – could find their way onto Falcon 9 and Falcon Heavy to further boost their booster performance and efficiency.
For prompt updates, on-the-ground perspectives, and unique glimpses of SpaceX’s rocket recovery fleet check out our brand new LaunchPad and LandingZone newsletters!
News
SpaceX launches Ax-4 mission to the ISS with international crew
The SpaceX Falcon 9 launched Axiom’s Ax-4 mission to ISS. Ax-4 crew will conduct 60+ science experiments during a 14-day stay on the ISS.
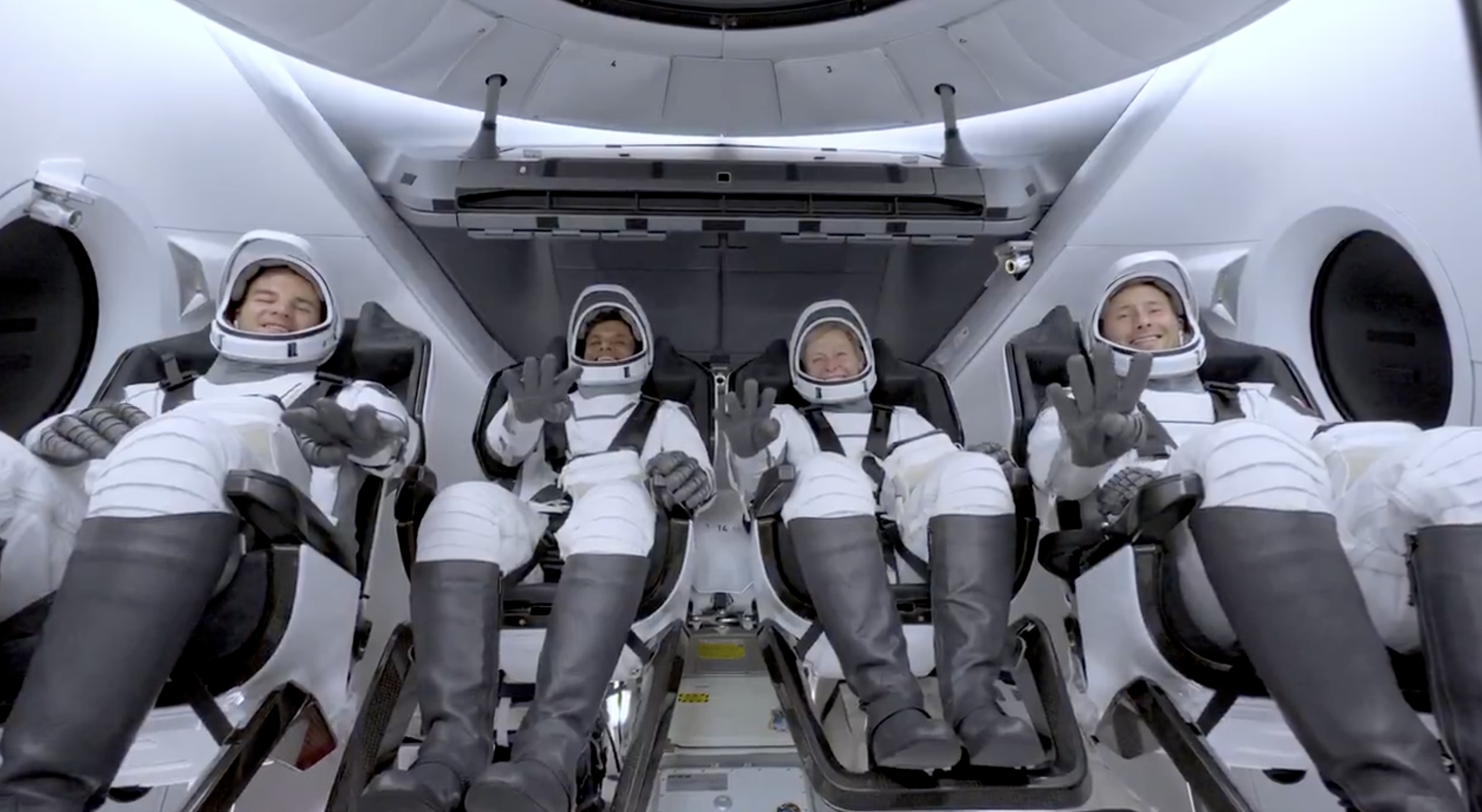
SpaceX launched the Falcon 9 rocket kickstarting Axiom Space’s Ax-4 mission to the International Space Station (ISS). Axiom’s Ax-4 mission is led by a historic international crew and lifted off from Kennedy Space Center’s Launch Complex 39A at 2:31 a.m. ET on June 25, 2025.
The Ax-4 crew is set to dock with the ISS around 7 a.m. ET on Thursday, June 26, 2025. Axiom Space, a Houston-based commercial space company, coordinated the mission with SpaceX for transportation and NASA for ISS access, with support from the European Space Agency and the astronauts’ governments.
The Ax-4 mission marks a milestone in global space collaboration. The Ax-4 crew, commanded by U.S. astronaut Peggy Whitson, includes Shubhanshu Shukla from India as the pilot, alongside mission specialists Sławosz Uznański-Wiśniewski from Poland and Tibor Kapu from Hungary.
“The trip marks the return to human spaceflight for those countries — their first government-sponsored flights in more than 40 years,” Axiom noted.
Shukla’s participation aligns with India’s Gaganyaan program planned for 2027. He is the first Indian astronaut to visit the ISS since Rakesh Sharma in 1984.
Axiom’s Ax-4 mission marks SpaceX’s 18th human spaceflight. The mission employs a Crew Dragon capsule atop a Falcon 9 rocket, designed with a launch escape system and “two-fault tolerant” for enhanced safety. The Axiom mission faced a few delays due to weather, a Falcon 9 leak, and an ISS Zvezda module leak investigation by NASA and Roscosmos before the recent successful launch.
As the crew prepares to execute its scientific objectives, SpaceX’s Ax-4 mission paves the way for a new era of inclusive space research, inspiring future generations and solidifying collaborative ties in the cosmos. During the Ax-4 crew’s 14-day stay in the ISS, the astronauts will conduct nearly 60 experiments.
“We’ll be conducting research that spans biology, material, and physical sciences as well as technology demonstrations,” said Whitson. “We’ll also be engaging with students around the world, sharing our experience and inspiring the next generation of explorers.”
SpaceX’s Ax-4 mission highlights Axiom’s role in advancing commercial spaceflight and fostering international partnerships. The mission strengthens global space exploration efforts by enabling historic spaceflight returns for India, Poland, and Hungary.
News
Starlink Cellular’s T-Mobile service to grow with third-party app data
From Oct 2025, T-Satellite will enable third-party apps in dead zones! WhatsApp, X, AccuWeather + more coming soon.
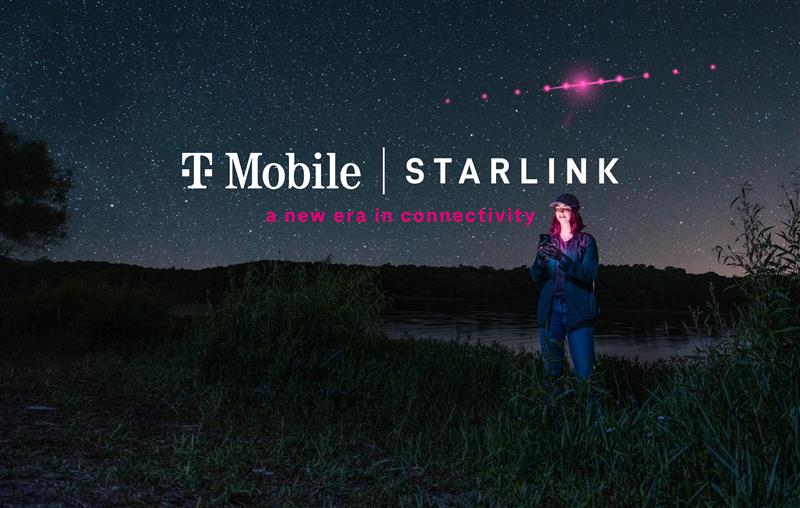
Starlink Cellular’s T-Mobile service will expand with third-party app data support starting in October, enhancing connectivity in cellular dead zones.
T-Mobile’s T-Satellite, supported by Starlink, launches officially on July 23. Following its launch, T-Mobile’s Starlink Cellular service will enable data access for third-party apps like WhatsApp, X, Google, Apple, AccuWeather, and AllTrails on October 1, 2025.
T-Mobile’s Starlink Cellular is currently in free beta. T-Satellite will add MMS support for Android phones on July 23, with iPhone support to follow. MMS support allows users to send images and audio clips alongside texts. By October, T-Mobile will extend emergency texting to all mobile users with compatible phones, beyond just T-Mobile customers, building on its existing 911 texting capability. The carrier also provides developer tools to help app makers integrate their software with T-Satellite’s data service, with plans to grow the supported app list.
T-Mobile announced these updates during an event celebrating an Ookla award naming it the best U.S. phone network, a remarkable turnaround from its last-place ranking a decade ago.
“We not only dream about going from worst to best, we actually do it. We’re a good two years ahead of Verizon and AT&T, and I believe that lead is going to grow,” said T-Mobile’s Chief Operating Officer Srini Gopalan.
T-Mobile unveiled two promotions for its Starlink Cellular services to attract new subscribers. A free DoorDash DashPass membership, valued at $10/month, will be included with popular plans like Experience Beyond and Experience More, offering reduced delivery and service fees. Meanwhile, the Easy Upgrade promotion targets Verizon customers by paying off their phone balances and providing flagship devices like the iPhone 16, Galaxy S25, or Pixel 9.
T-Mobile’s collaboration with SpaceX’s Starlink Cellular leverages orbiting satellites to deliver connectivity where traditional networks fail, particularly in remote areas. Supporting third-party apps underscores T-Mobile’s commitment to enhancing user experiences through innovative partnerships. As T-Satellite’s capabilities grow, including broader app integration and emergency access, T-Mobile is poised to strengthen its lead in the U.S. wireless market.
By combining Starlink’s satellite technology with strategic promotions, T-Mobile is redefining mobile connectivity. The upcoming third-party app data support and official T-Satellite launch mark a significant step toward seamless communication, positioning T-Mobile as a trailblazer in next-generation wireless services.
News
Starlink expansion into Vietnam targets the healthcare sector
Starlink aims to deliver reliable internet to Vietnam’s remote clinics, enabling telehealth and data sharing.

SpaceX’s Starlink expansion into Vietnam targets its healthcare sector. Through Starlink, SpaceX seeks to drive digital transformation in Vietnam.
On June 18, a SpaceX delegation met with Vietnam’s Ministry of Health (MoH) in Hanoi. SpaceX’s delegation was led by Andrew Matlock, Director of Enterprise Sales, and the discussions focused on enhancing connectivity for hospitals and clinics in Vietnam’s remote areas.
Deputy Minister of Health (MoH) Tran Van Thuan emphasized collaboration between SpaceX and Vietnam. Tran stated: “SpaceX should cooperate with the MoH to ensure all hospitals and clinics in remote areas are connected to the StarLink satellite system and share information, plans, and the issues discussed by members of the MoH. The ministry is also ready to provide information and send staff to work with the corporation.”
The MoH assigned its Department of Science, Technology, and Training to work with SpaceX. Starlink Vietnam will also receive support from Vietnam’s Department of International Cooperation. Starlink Vietnam’s agenda includes improving internet connectivity for remote healthcare facilities, developing digital infrastructure for health examinations and remote consultations, and enhancing operational systems.
Vietnam’s health sector is prioritizing IT and digital transformation, focusing on electronic health records, data centers, and remote medical services. However, challenges persist in deploying IT solutions in remote regions, prompting Vietnam to seek partnerships like SpaceX’s.
SpaceX’s Starlink has a proven track record in healthcare. In Rwanda, its services supported 40 health centers, earning praise for improving operations. Similarly, Starlink enabled remote consultations at the UAE’s Emirati field hospital in Gaza, streamlining communication for complex medical cases. These successes highlight Starlink’s potential to transform Vietnam’s healthcare landscape.
On May 20, SpaceX met with Vietnam’s Ministry of Industry and Trade, announcing a $1.5 billion investment to provide broadband internet, particularly in remote, border, and island areas. The first phase includes building 10-15 ground stations across the country. This infrastructure will support Starlink’s healthcare initiatives by ensuring reliable connectivity.
Starlink’s expansion in Vietnam aligns with the country’s push for digital transformation, as outlined by the MoH. By leveraging its satellite internet expertise, SpaceX aims to bridge connectivity gaps, enabling advanced healthcare services in underserved regions. This collaboration could redefine Vietnam’s healthcare infrastructure, positioning Starlink as a key player in the nation’s digital future.
-
Elon Musk2 weeks ago
Tesla investors will be shocked by Jim Cramer’s latest assessment
-
Elon Musk2 days ago
xAI launches Grok 4 with new $300/month SuperGrok Heavy subscription
-
Elon Musk4 days ago
Elon Musk confirms Grok 4 launch on July 9 with livestream event
-
News1 week ago
Tesla Model 3 ranks as the safest new car in Europe for 2025, per Euro NCAP tests
-
Elon Musk2 weeks ago
A Tesla just delivered itself to a customer autonomously, Elon Musk confirms
-
Elon Musk1 week ago
xAI’s Memphis data center receives air permit despite community criticism
-
News2 weeks ago
Xiaomi CEO congratulates Tesla on first FSD delivery: “We have to continue learning!”
-
Investor's Corner2 weeks ago
Tesla gets $475 price target from Benchmark amid initial Robotaxi rollout