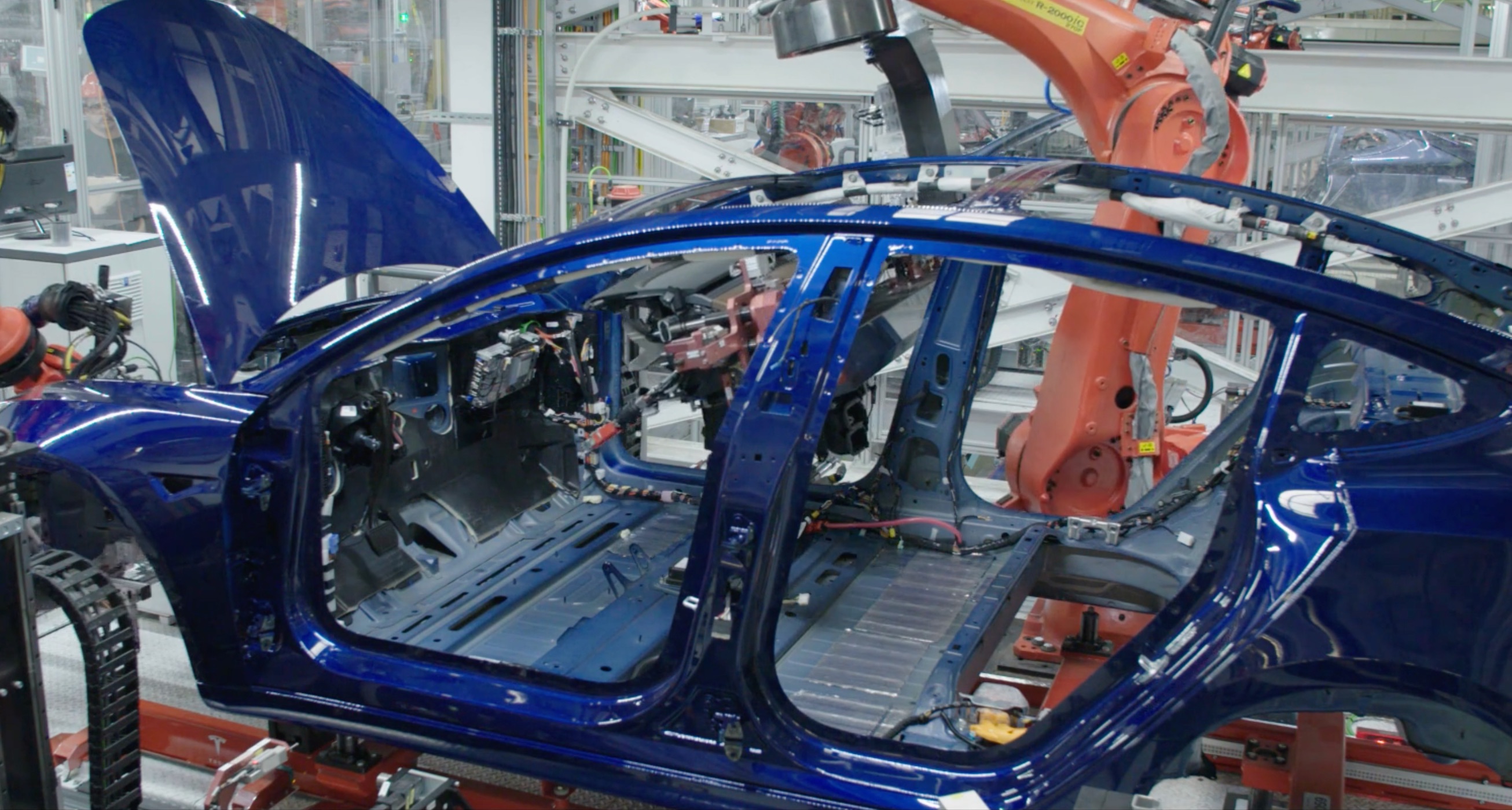
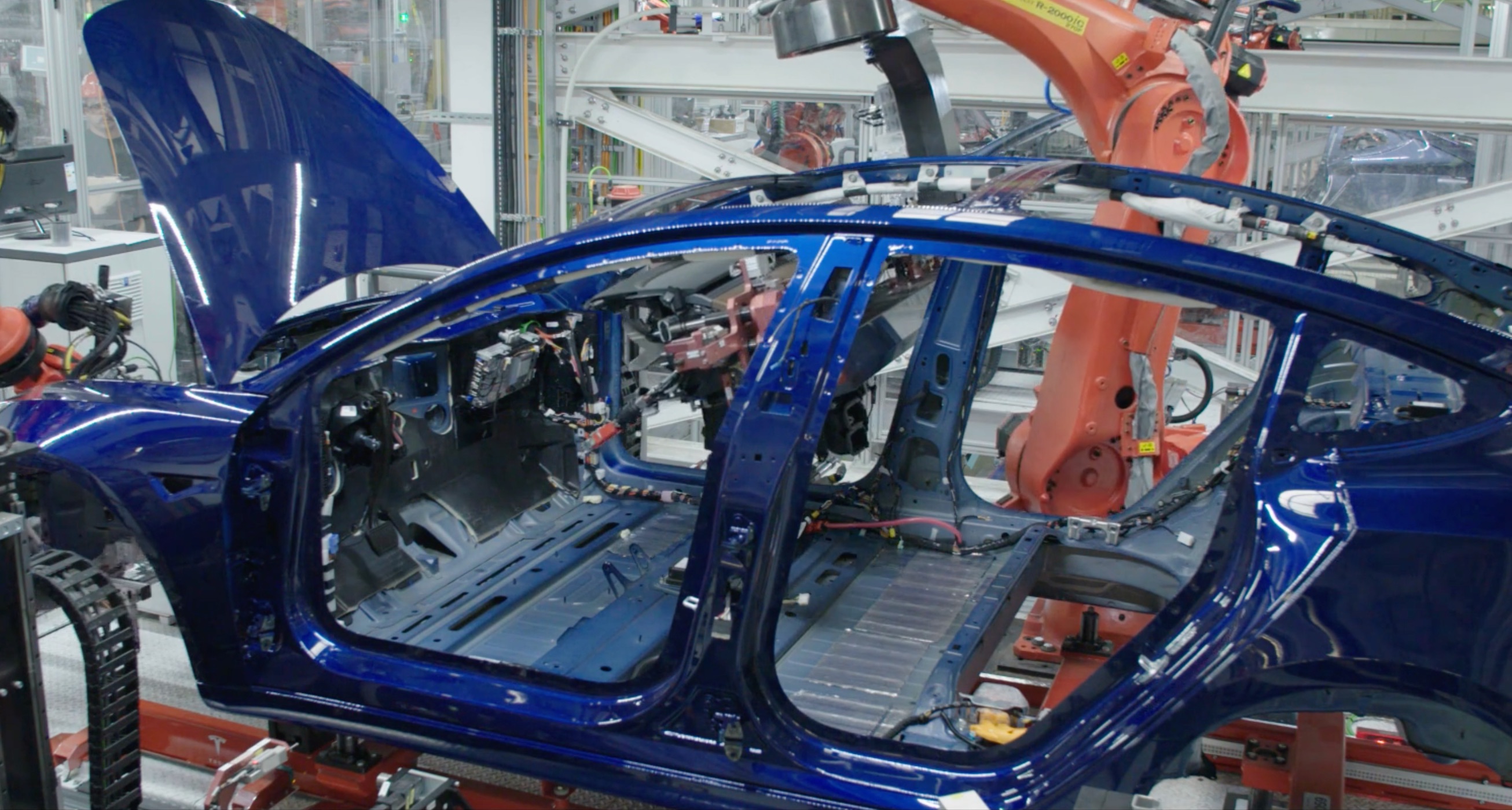
Investor's Corner
Tesla Model 3 delays due to battery module assembly line
Tesla has confirmed that the source of its Model 3 production bottleneck is the battery module assembly line at its $5 billion Gigafactory 1 facility in Sparks, Nevada. The Silicon Valley electric car maker noted in its third quarter 2017 earnings report that the manufacturing process for Model 3’s battery modules – processes that were “done by manufacturing systems suppliers” – were taken over and “significantly redesigned” by Tesla, thus causing the delays.
“To date, our primary production constraint has been in the battery module assembly line at Gigafactory 1, where cells are packaged into modules.” reads the statement from Tesla in its update letter. Furthermore, Tesla says engineering talent at the company have been redirected to fine-tune the automated processes involved with battery module production, noting that these were key elements of which were “done by manufacturing systems suppliers”. This is one of the primary reasons why only 260 Model 3 vehicles have been produced at the end of the third-quarter. Tesla did not provide any guidance on how this will translate into end of year Model 3 production numbers, but did note that throughput is expected to increase substantially in November. The company also noted that Model 3 volume production of 5,000 vehicles per week is expected late in the first quarter of 2018, delayed three months from CEO Elon Musk’s original end of year guidance.
Like the Model S and Model X which uses a low-mount battery pack that’s made up of individual lithium-ion cells that are packed into battery modules, Model 3 utilizes the same design for its skateboard-style battery pack but with fewer modules. Tesla’s mass market-intent vehicle uses a larger 2170 form factor cylindrical cell versus Model S and X that utilize a 18650 lithium-ion cell that resembles a traditional AA battery. Taking a look at a Tesla battery pack teardown video that we shared in the past, we can see that Tesla arranges Model S and X battery cells into 16 modules that are inserted into an aluminum battery case. Model 3 on the other hand utilizes only 4 modules, thereby arranging more battery cells into larger compartments.
Model 3 production constraint is related to the automated processes that’s responsible for manufacturing two of the four Model 3 battery modules. “Four modules are packaged into an aluminum case to form a Model 3 battery pack. The combined complexity of module design and its automated manufacturing process has taken this line longer to ramp than expected. The biggest challenge is that the first two zones of a four zone process, key elements of which were done by manufacturing systems suppliers, had to be taken over and significantly redesigned by Tesla.” said Tesla in its update letter.
Musk added additional color during the Q&A call with analysts following the update letter, citing challenges faced by the programs that operate the robots in Model 3’s battery assembly line. “We had to rewrite all of the software, from scratch. We managed to write 20 to 30 man-years of software in 4 weeks.” said Musk in explaining the level of reprogramming needed on the factory floor.
Both Musk and CTO JB Straubel reasserted that Model 3’s design is vastly less complex than Model S and X, and built with high volume production in mind. “The initial phase of manufacturing in any new vehicle is always challenging, and the Model 3 production ramp is no exception,” said Tesla.
Because the production process for Model 3 is highly automated, any misconfiguration or general issue around a specific machine in the process becomes amplified across all other machines that rely on it. There’s less tolerance for errors in an automated process, explained Musk. Once Tesla fixes many of the mechanical and electrical issues that it’s currently facing, production ramp up will scale exponentially. Conversely, Model S and Model X production was far less automated, which served as a double edged sword: Tesla was able to quickly address issues in the production process by increasing the number of human labor hours involved, but at the expense of reaching a finite production level.
Tesla Model 3 production is expected to reach 5,000 units per week in the first quarter of 2018, but achieving its originally planned 10,000 units produced per week “sometime in 2018” still remains unclear.
Elon Musk
Tesla analyst issues stern warning to investors: forget Trump-Musk feud

A Tesla analyst today said that investors should not lose sight of what is truly important in the grand scheme of being a shareholder, and that any near-term drama between CEO Elon Musk and U.S. President Donald Trump should not outshine the progress made by the company.
Gene Munster of Deepwater Management said that Tesla’s progress in autonomy is a much larger influence and a significantly bigger part of the company’s story than any disagreement between political policies.
Munster appeared on CNBC‘s “Closing Bell” yesterday to reiterate this point:
“One thing that is critical for Tesla investors to remember is that what’s going on with the business, with autonomy, the progress that they’re making, albeit early, is much bigger than any feud that is going to happen week-to-week between the President and Elon. So, I understand the reaction, but ultimately, I think that cooler heads will prevail. If they don’t, autonomy is still coming, one way or the other.”
BREAKING: GENE MUNSTER SAYS — $TSLA AUTONOMY IS “MUCH BIGGER” THAN ANY FEUD 👀
He says robotaxis are coming regardless ! pic.twitter.com/ytpPcwUTFy
— TheSonOfWalkley (@TheSonOfWalkley) July 2, 2025
This is a point that other analysts like Dan Ives of Wedbush and Cathie Wood of ARK Invest also made yesterday.
On two occasions over the past month, Musk and President Trump have gotten involved in a very public disagreement over the “Big Beautiful Bill,” which officially passed through the Senate yesterday and is making its way to the House of Representatives.
Musk is upset with the spending in the bill, while President Trump continues to reiterate that the Tesla CEO is only frustrated with the removal of an “EV mandate,” which does not exist federally, nor is it something Musk has expressed any frustration with.
In fact, Musk has pushed back against keeping federal subsidies for EVs, as long as gas and oil subsidies are also removed.
Nevertheless, Ives and Wood both said yesterday that they believe the political hardship between Musk and President Trump will pass because both realize the world is a better place with them on the same team.
Munster’s perspective is that, even though Musk’s feud with President Trump could apply near-term pressure to the stock, the company’s progress in autonomy is an indication that, in the long term, Tesla is set up to succeed.
Tesla launched its Robotaxi platform in Austin on June 22 and is expanding access to more members of the public. Austin residents are now reporting that they have been invited to join the program.
Elon Musk
Tesla surges following better-than-expected delivery report
Tesla saw some positive momentum during trading hours as it reported its deliveries for Q2.
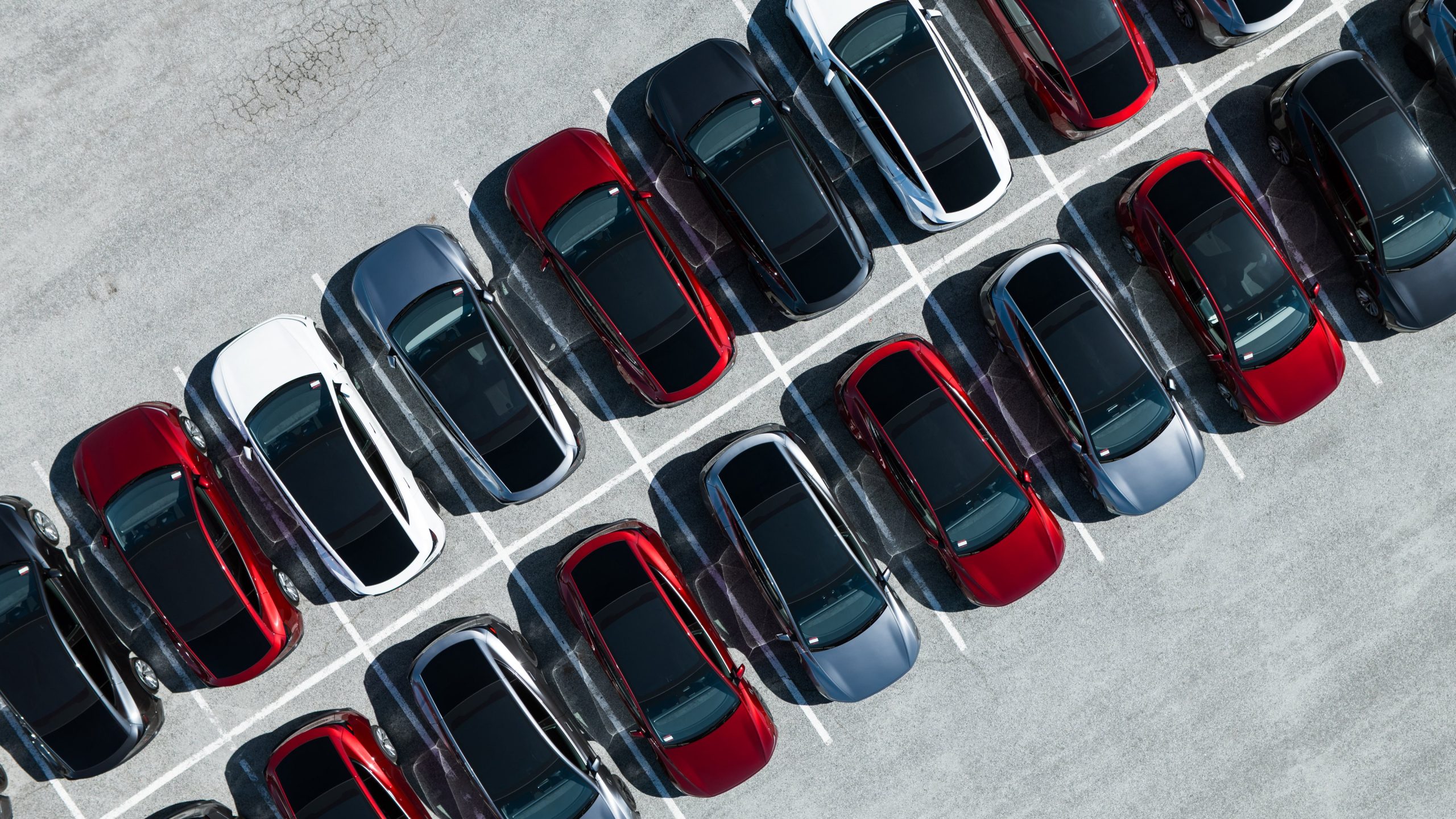
Tesla (NASDAQ: TSLA) surged over four percent on Wednesday morning after the company reported better-than-expected deliveries. It was nearly right on consensus estimations, as Wall Street predicted the company would deliver 385,000 cars in Q2.
Tesla reported that it delivered 384,122 vehicles in Q2. Many, including those inside the Tesla community, were anticipating deliveries in the 340,000 to 360,000 range, while Wall Street seemed to get it just right.
Tesla delivers 384,000 vehicles in Q2 2025, deploys 9.6 GWh in energy storage
Despite Tesla meeting consensus estimations, there were real concerns about what the company would report for Q2.
There were reportedly brief pauses in production at Gigafactory Texas during the quarter and the ramp of the new Model Y configuration across the globe were expected to provide headwinds for the EV maker during the quarter.
At noon on the East Coast, Tesla shares were up about 4.5 percent.
It is expected that Tesla will likely equal the number of deliveries it completed in both of the past two years.
It has hovered at the 1.8 million mark since 2023, and it seems it is right on pace to match that once again. Early last year, Tesla said that annual growth would be “notably lower” than expected due to its development of a new vehicle platform, which will enable more affordable models to be offered to the public.
These cars are expected to be unveiled at some point this year, as Tesla said they were “on track” to be produced in the first half of the year. Tesla has yet to unveil these vehicle designs to the public.
Dan Ives of Wedbush said in a note to investors this morning that the company’s rebound in China in June reflects good things to come, especially given the Model Y and its ramp across the world.
He also said that Musk’s commitment to the company and return from politics played a major role in the company’s performance in Q2:
“If Musk continues to lead and remain in the driver’s seat, we believe Tesla is on a path to an accelerated growth path over the coming years with deliveries expected to ramp in the back-half of 2025 following the Model Y refresh cycle.”
Ives maintained his $500 price target and the ‘Outperform’ rating he held on the stock:
“Tesla’s future is in many ways the brightest it’s ever been in our view given autonomous, FSD, robotics, and many other technology innovations now on the horizon with 90% of the valuation being driven by autonomous and robotics over the coming years but Musk needs to focus on driving Tesla and not putting his political views first. We maintain our OUTPERFORM and $500 PT.”
Moving forward, investors will look to see some gradual growth over the next few quarters. At worst, Tesla should look to match 2023 and 2024 full-year delivery figures, which could be beaten if the automaker can offer those affordable models by the end of the year.
Investor's Corner
Tesla delivers 384,000 vehicles in Q2 2025, deploys 9.6 GWh in energy storage
The quarter’s 9.6 GWh energy storage deployment marks one of Tesla’s highest to date.
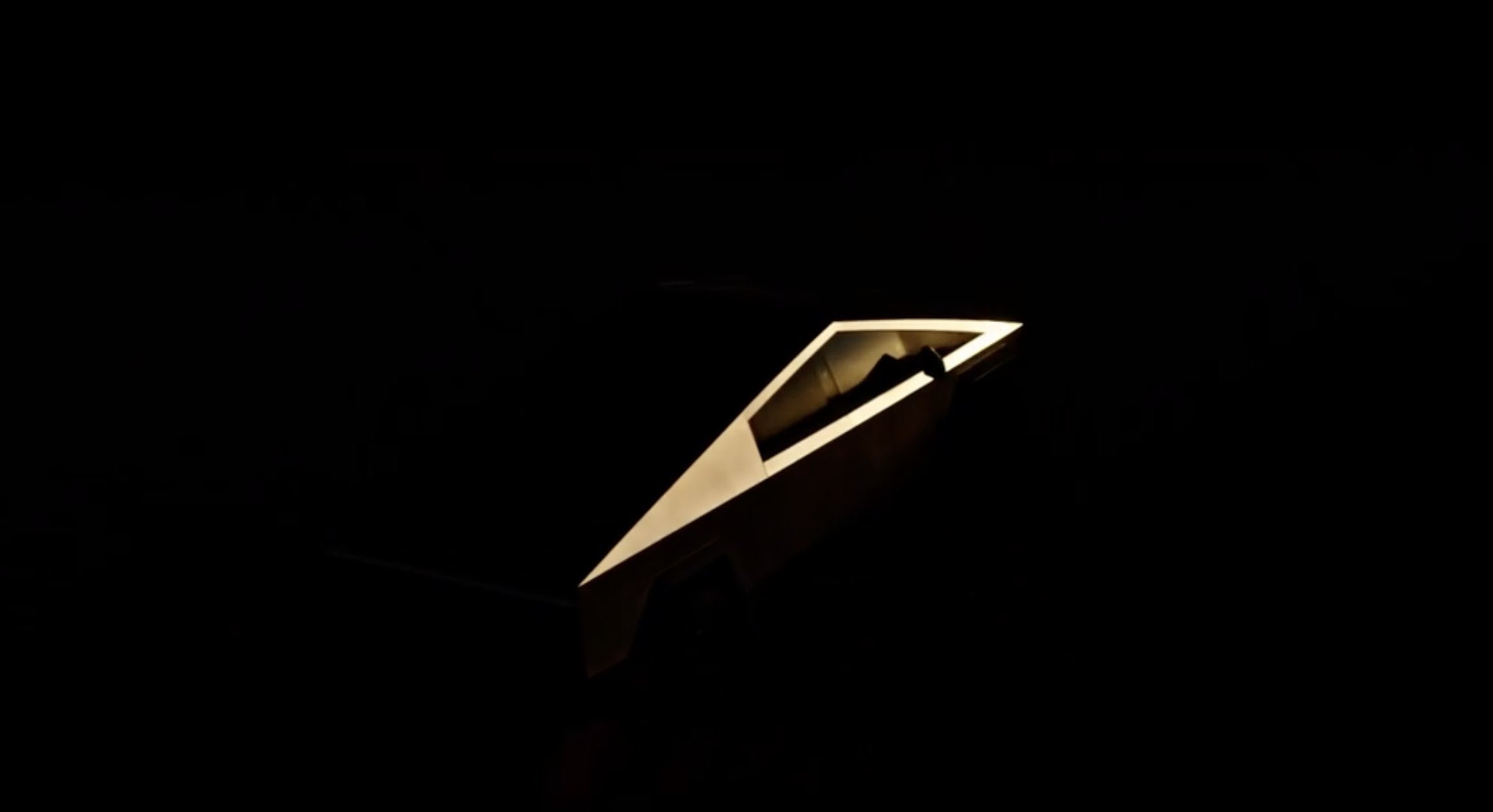
Tesla (NASDAQ: TSLA) has released its Q2 2025 vehicle delivery and production report. As per the report, the company delivered over 384,000 vehicles in the second quarter of 2025, while deploying 9.6 GWh in energy storage. Vehicle production also reached 410,244 units for the quarter.
Model 3/Y dominates output, ahead of earnings call
Of the 410,244 vehicles produced during the quarter, 396,835 were Model 3 and Model Y units, while 13,409 were attributed to Tesla’s other models, which includes the Cybertruck and Model S/X variants. Deliveries followed a similar pattern, with 373,728 Model 3/Ys delivered and 10,394 from other models, totaling 384,122.
The quarter’s 9.6 GWh energy storage deployment marks one of Tesla’s highest to date, signaling continued strength in the Megapack and Powerwall segments.
Year-on-year deliveries edge down, but energy shows resilience
Tesla will share its full Q2 2025 earnings results after the market closes on Wednesday, July 23, 2025, with a live earnings call scheduled for 4:30 p.m. CT / 5:30 p.m. ET. The company will publish its quarterly update at ir.tesla.com, followed by a Q&A webcast featuring company leadership. Executives such as CEO Elon Musk are expected to be in attendance.
Tesla investors are expected to inquire about several of the company’s ongoing projects in the upcoming Q2 2025 earnings call. Expected topics include the new Model Y ramp across the United States, China, and Germany, as well as the ramp of FSD in territories outside the US and China. Questions about the company’s Robotaxi business, as well as the long-referenced but yet to be announced affordable models are also expected.
-
Elon Musk4 days ago
Tesla investors will be shocked by Jim Cramer’s latest assessment
-
News1 week ago
Tesla Robotaxi’s biggest challenge seems to be this one thing
-
Elon Musk2 weeks ago
First Look at Tesla’s Robotaxi App: features, design, and more
-
News2 weeks ago
SpaceX and Elon Musk share insights on Starship Ship 36’s RUD
-
News2 weeks ago
Watch Tesla’s first driverless public Robotaxi rides in Texas
-
News1 week ago
Watch the first true Tesla Robotaxi intervention by safety monitor
-
News2 weeks ago
Tesla has started rolling out initial round of Robotaxi invites
-
Elon Musk2 weeks ago
Tesla to launch in India in July with vehicles already arriving: report