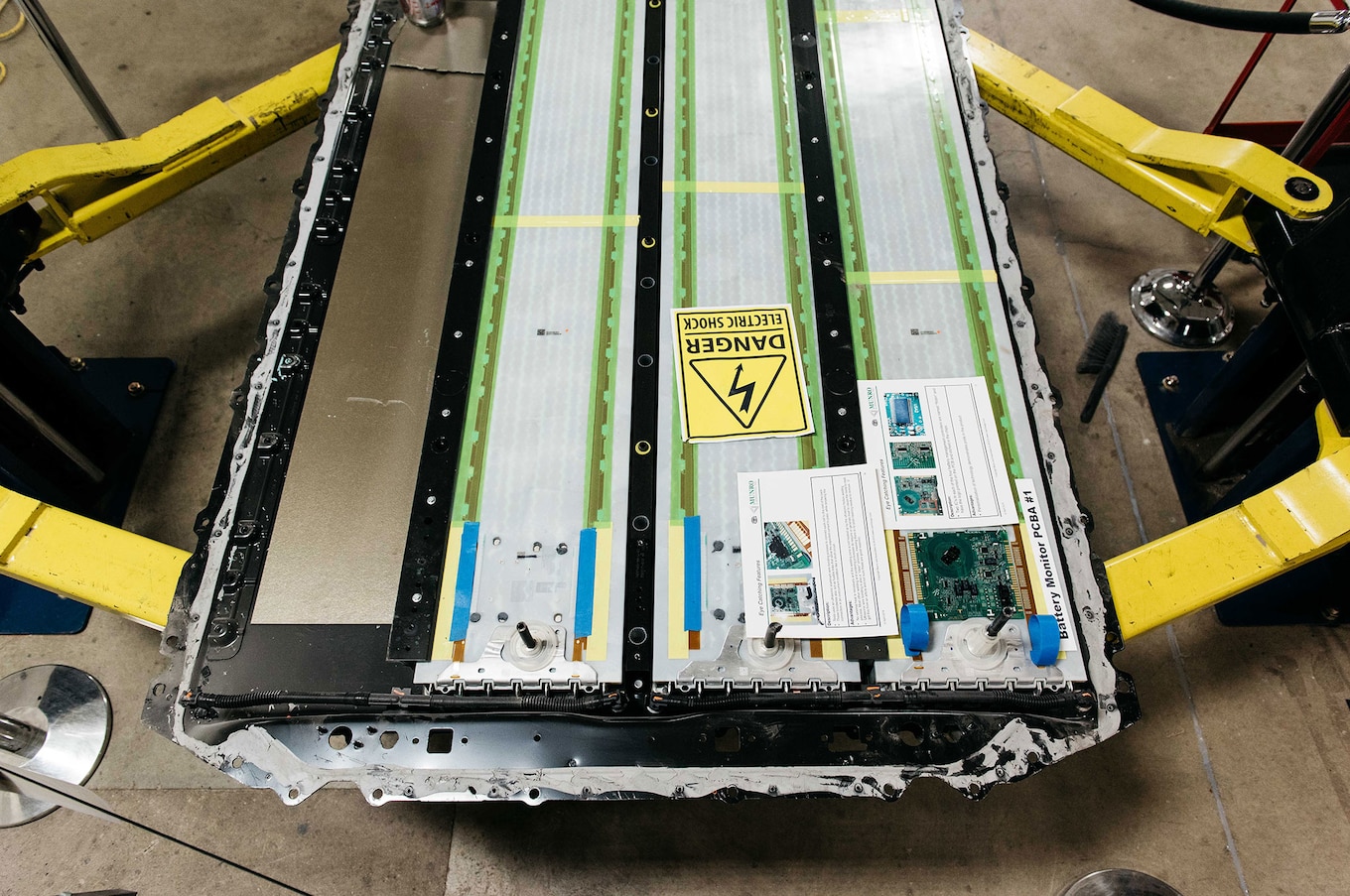
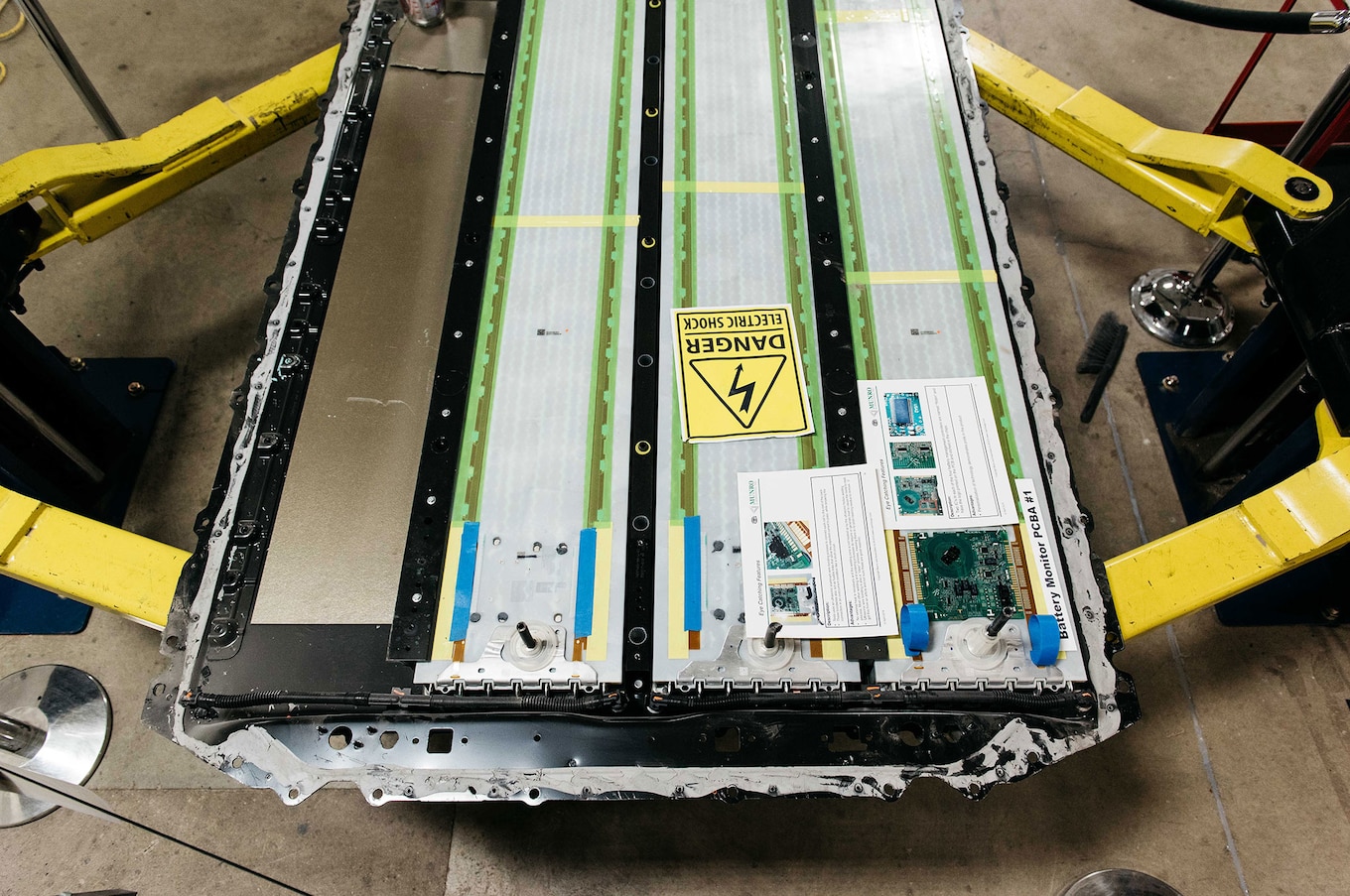
Investor's Corner
Tesla explores safer battery production with novel DCM recovery system patent
In what appears to be yet another step towards its goal of operating the safest car factory in the industry, Tesla has been granted a patent that could pave the way for a safer process in battery production. Published today, the electric car maker’s recent patent describes a system to treat and recycle Dichloromethane (DCM), which is among the materials used in the production of electric car batteries.
DCM is utilized in a variety of industrial processes, particularly in chemical plastic welding, wherein softened plastic pieces or surfaces are welded together. The material is also used to soften plastic sheets for stretching or shaping, and as a solvent to remove unwanted compounds. In Tesla’s case, DCM is among the materials used in the forming of a separator base film for an electric car’s battery system. While DCM is invaluable in manufacturing, though, the material carries some health risks.
Dichloromethane is the least toxic among the simple chlorohydrocarbons, but its high volatility makes it an inhalation hazard nonetheless. Prolonged skin contact with DCM could also result in the material dissolving some of the skin’s fatty tissues, causing irritation or chemical burns. With these risks in mind, the manufacturing industry employs ways to recover DCM. Tesla notes that current systems for DCM treatment and recovery are capital intensive, particularly since the process involves expensive components such as activated carbon beds, condensers, steam boilers and distribution systems, density separation vessels, and waste water treatment systems.
- Tesla’s DCM treatment system. [Credit: US Patent Office]
- A flow chart illustrating operation of an exhaust treatment system for treating a waste exhaust stream containing dichlorom ethane. [Credit: US Patent Office]
Tesla’s diagrams outlining its Dichloromethane recovery system. [Credit: US Patent Office]
Tesla describes conventional DCM treatment systems as follows:
“The DCM itself may then be removed through a heating and/or evaporation process with the exhaust collected. This exhaust containing DCM is then combined with the exhaust from other tools and systems used in the manufacturing process. The combined exhaust may then be fed to a recovery plant to recover DCM. In the recovery plant, the waste exhaust stream is typically treated with activated carbon. This scrubbing process requires high capital expenditure (many expensive components), high operating cost (extensive steam and cooling water consumption which accounts for >20% of total process cost), large footprint requirements, and large amounts of waste water that need to be processed. In order to address these cost and environmental-remediation issues, an improved process for the removal of DCM from exhaust streams is needed.”
Tesla’s take on DCM treatment and recovery utilizes a wet scrubber and a density separator vessel as key components of the system. The wet scrubber in Tesla’s patent has a scrubbing chamber, where water is utilized to scrub the waste exhaust stream containing the DCM. Tesla notes that the wet scrubber could adopt a variety of designs to remove DCM from the waste exhaust stream, including a venturi scrubber design, a condensation scrubber design, an impingement-plate scrubber design, or a packed bed tower design, among others.
Tesla’s use of a density separator vessel is described in the following section from the patent.
“The density separator vessel has an inlet to receive the liquid water and DCM mixture, an outlet to expel DCM, and an outlet to expel waste water. The DCM may be routed back to the industrial process for reuse and/or collected for later use. The waste water may be routed back to the wet scrubber, as shown along (the) waste water return loop. Waste water may also or alternately be routed to waste water treatment system for processing for subsequent treatment by (the) waste water treatment system.
“Typically, a large portion of the waste water is returned to the wet scrubber via (the) waste water return loop and a small portion of the waste water is treated by the waste water treatment system. Even though the waste water may contain small amounts of DCM, the waste water will still retain its ability to scrub the exhaust containing DCM. An advantage of the wet scrubber over the activated carbon beds is that all or most of the water used by the wet scrubber is the waste water from the density separator vessel, resulting in substantial savings of water and energy, and resultantly, substantial cost savings.”
Tesla states that compared to more traditional exhaust treatment systems, the DCM treatment and recovery model outlined in its patent effectively eliminates the use of steam and cooling, while also reducing the amount of throughput needed by a waste water system. With these efficiencies in mind, Tesla notes that it could reduce capital expenditures and operating costs “for the same amount of DCM processed processing.” The increased simplicity of the system and reduced airflow rates are expected to help the company get more savings in both capital expenditures and operating costs as well.
More than a way to optimize its operations, Tesla’s recent patent is also a notable way for the company to keep its battery production lines safer for its employees. Such a system would definitely be invaluable for the company, particularly as Tesla is now preparing the Model 3 for a global rollout. With the Model 3 ramp ever-expanding, and with high-volume vehicles like the Model Y and possibly the Tesla pickup truck in the pipeline, optimizations such as a better DCM treatment and recovery system are all but necessary.
Tesla’s recently published patent on its DCM treatment system could be accessed here.
Investor's Corner
Tesla could save $2.5B by replacing 10% of staff with Optimus: Morgan Stanley
Jonas assigned each robot a net present value (NPV) of $200,000.
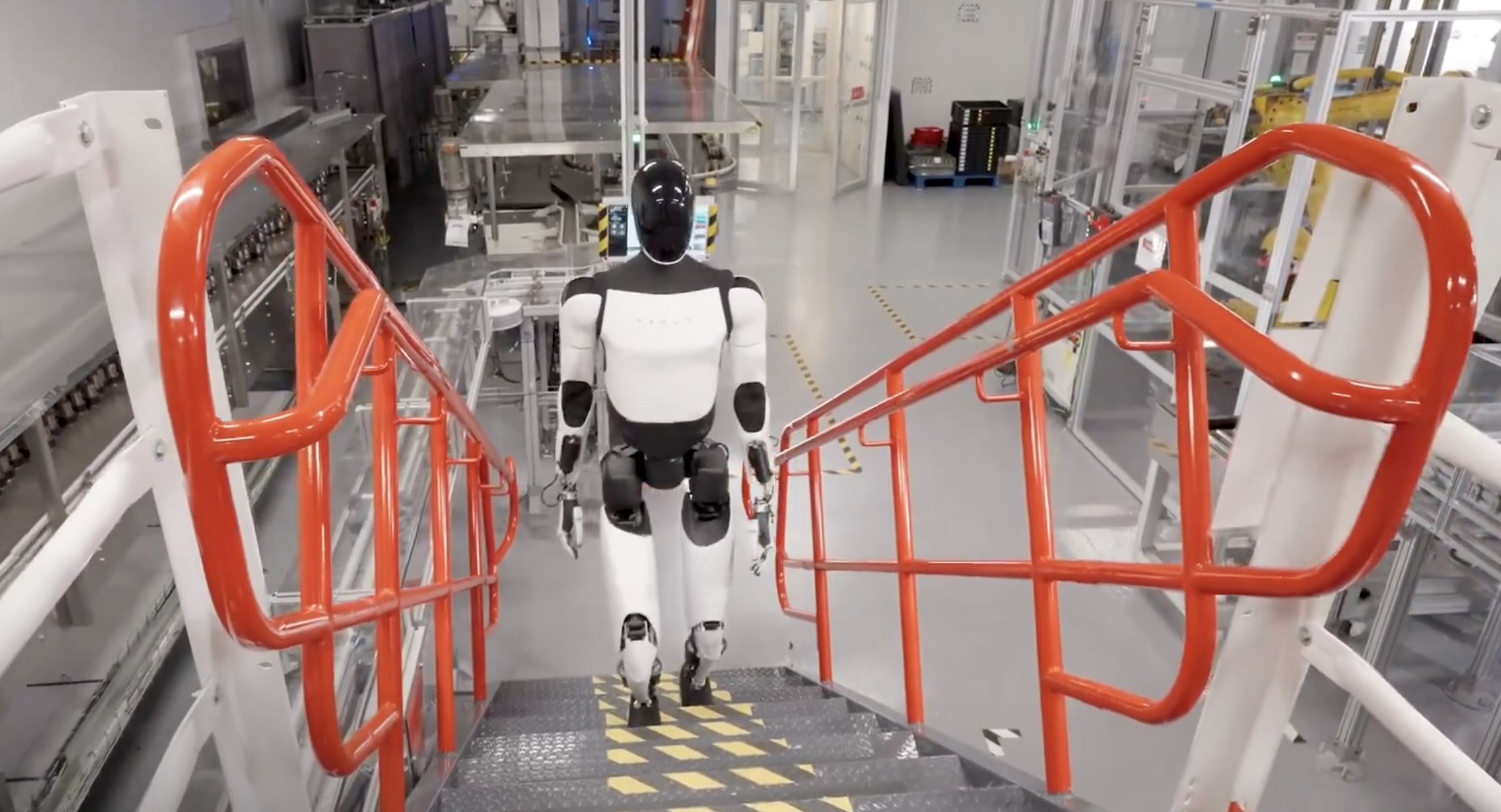
Tesla’s (NASDAQ:TSLA) near-term outlook may be clouded by political controversies and regulatory headwinds, but Morgan Stanley analyst Adam Jonas sees a glimmer of opportunity for the electric vehicle maker.
In a new note, the Morgan Stanley analyst estimated that Tesla could save $2.5 billion by replacing just 10% of its workforce with its Optimus robots, assigning each robot a net present value (NPV) of $200,000.
Morgan Stanley highlights Optimus’ savings potential
Jonas highlighted the potential savings on Tesla’s workforce of 125,665 employees in his note, suggesting that the utilization of Optimus robots could significantly reduce labor costs. The analyst’s note arrived shortly after Tesla reported Q2 2025 deliveries of 384,122 vehicles, which came close to Morgan Stanley’s estimate and slightly under the consensus of 385,086.
“Tesla has 125,665 employees worldwide (year-end 2024). On our calculations, a 10% substitution to humanoid at approximately ($200k NPV/humanoid) could be worth approximately $2.5bn,” Jonas wrote, as noted by Street Insider.
Jonas also issued some caution on Tesla Energy, whose battery storage deployments were flat year over year at 9.6 GWh. Morgan Stanley had expected Tesla Energy to post battery storage deployments of 14 GWh in the second quarter.
Musk’s political ambitions
The backdrop to Jonas’ note included Elon Musk’s involvement in U.S. politics. The Tesla CEO recently floated the idea of launching a new political party, following a poll on X that showed support for the idea. Though a widely circulated FEC filing was labeled false by Musk, the CEO does seem intent on establishing a third political party in the United States.
Jonas cautioned that Musk’s political efforts could divert attention and resources from Tesla’s core operations, adding near-term pressure on TSLA stock. “We believe investors should be prepared for further devotion of resources (financial, time/attention) in the direction of Mr. Musk’s political priorities which may add further near-term pressure to TSLA shares,” Jonas stated.
Investor's Corner
Two Tesla bulls share differing insights on Elon Musk, the Board, and politics
Two noted Tesla bulls have shared differing views on the recent activities of CEO Elon Musk and the company’s leadership.
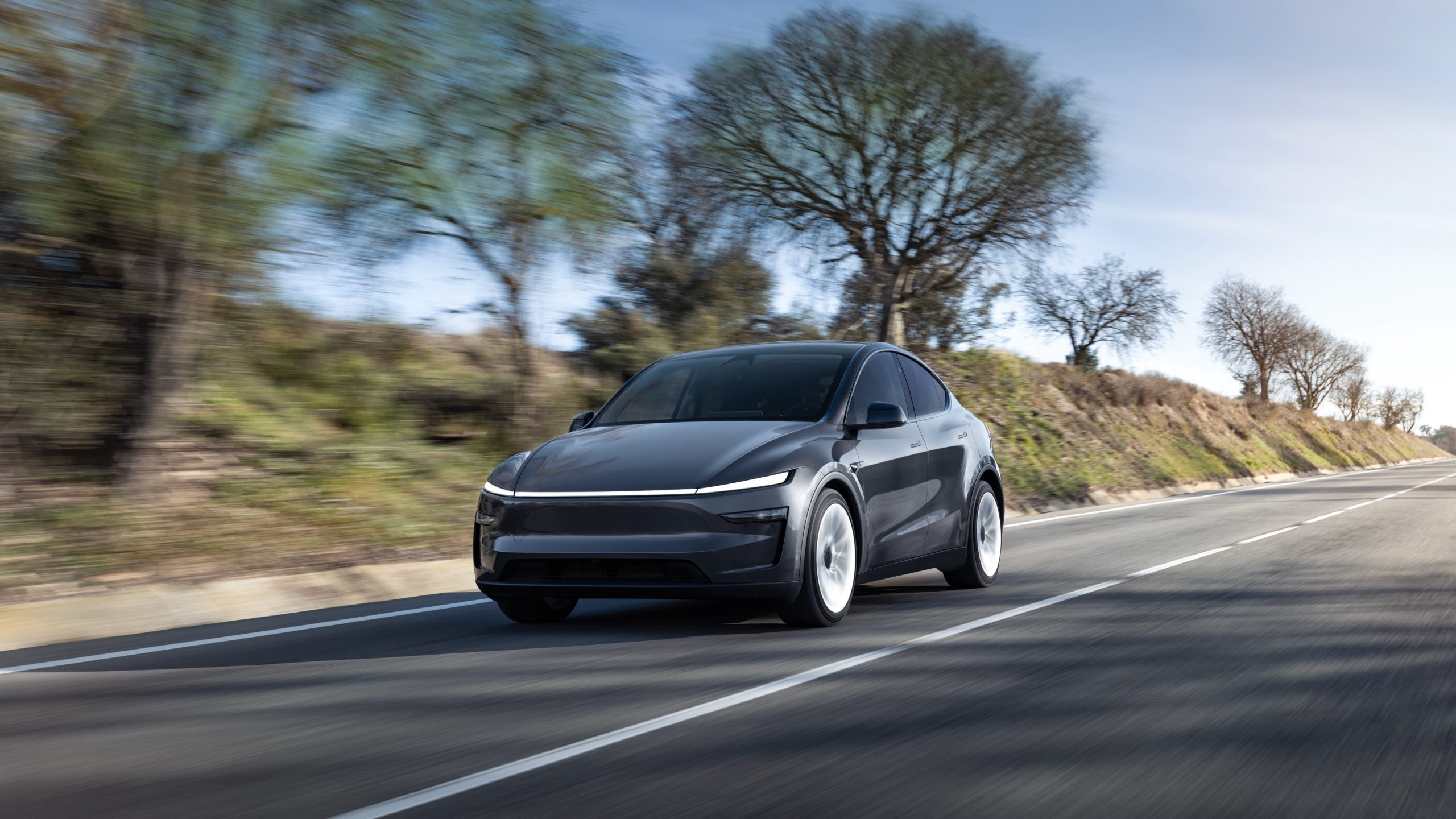
Two noted Tesla (NASDAQ:TSLA) bulls have shared differing views on the recent activities of CEO Elon Musk and the company’s leadership.
While Wedbush analyst Dan Ives called on Tesla’s board to take concrete steps to ensure Musk remains focused on the EV maker, longtime Tesla supporter Cathie Wood of Ark Invest reaffirmed her confidence in the CEO and the company’s leadership.
Ives warns of distraction risk amid crucial growth phase
In a recent note, Ives stated that Tesla is at a critical point in its history, as the company is transitioning from an EV maker towards an entity that is more focused on autonomous driving and robotics. He then noted that the Board of Directors should “act now” and establish formal boundaries around Musk’s political activities, which could be a headwind on TSLA stock.
Ives laid out a three-point plan that he believes could ensure that the electric vehicle maker is led with proper leadership until the end of the decade. First off, the analyst noted that a new “incentive-driven pay package for Musk as CEO that increases his ownership of Tesla up to ~25% voting power” is necessary. He also stated that the Board should establish clear guidelines for how much time Musk must devote to Tesla operations in order to receive his compensation, and a dedicated oversight committee must be formed to monitor the CEO’s political activities.
Ives, however, highlighted that Tesla should move forward with Musk at its helm. “We urge the Board to act now and move the Tesla story forward with Musk as CEO,” he wrote, reiterating its Outperform rating on Tesla stock and $500 per share price target.
Tesla CEO Elon Musk has responded to Ives’ suggestions with a brief comment on X. “Shut up, Dan,” Musk wrote.
Cathie Wood reiterates trust in Musk and Tesla board
Meanwhile, Ark Investment Management founder Cathie Wood expressed little concern over Musk’s latest controversies. In an interview with Bloomberg Television, Wood said, “We do trust the board and the board’s instincts here and we stay out of politics.” She also noted that Ark has navigated Musk-related headlines since it first invested in Tesla.
Wood also pointed to Musk’s recent move to oversee Tesla’s sales operations in the U.S. and Europe as evidence of his renewed focus in the electric vehicle maker. “When he puts his mind on something, he usually gets the job done,” she said. “So I think he’s much less distracted now than he was, let’s say, in the White House 24/7,” she said.
TSLA stock is down roughly 25% year-to-date but has gained about 19% over the past 12 months, as noted in a StocksTwits report.
Investor's Corner
Cantor Fitzgerald maintains Tesla (TSLA) ‘Overweight’ rating amid Q2 2025 deliveries
Cantor Fitzgerald is holding firm on its bullish stance for the electric vehicle maker.
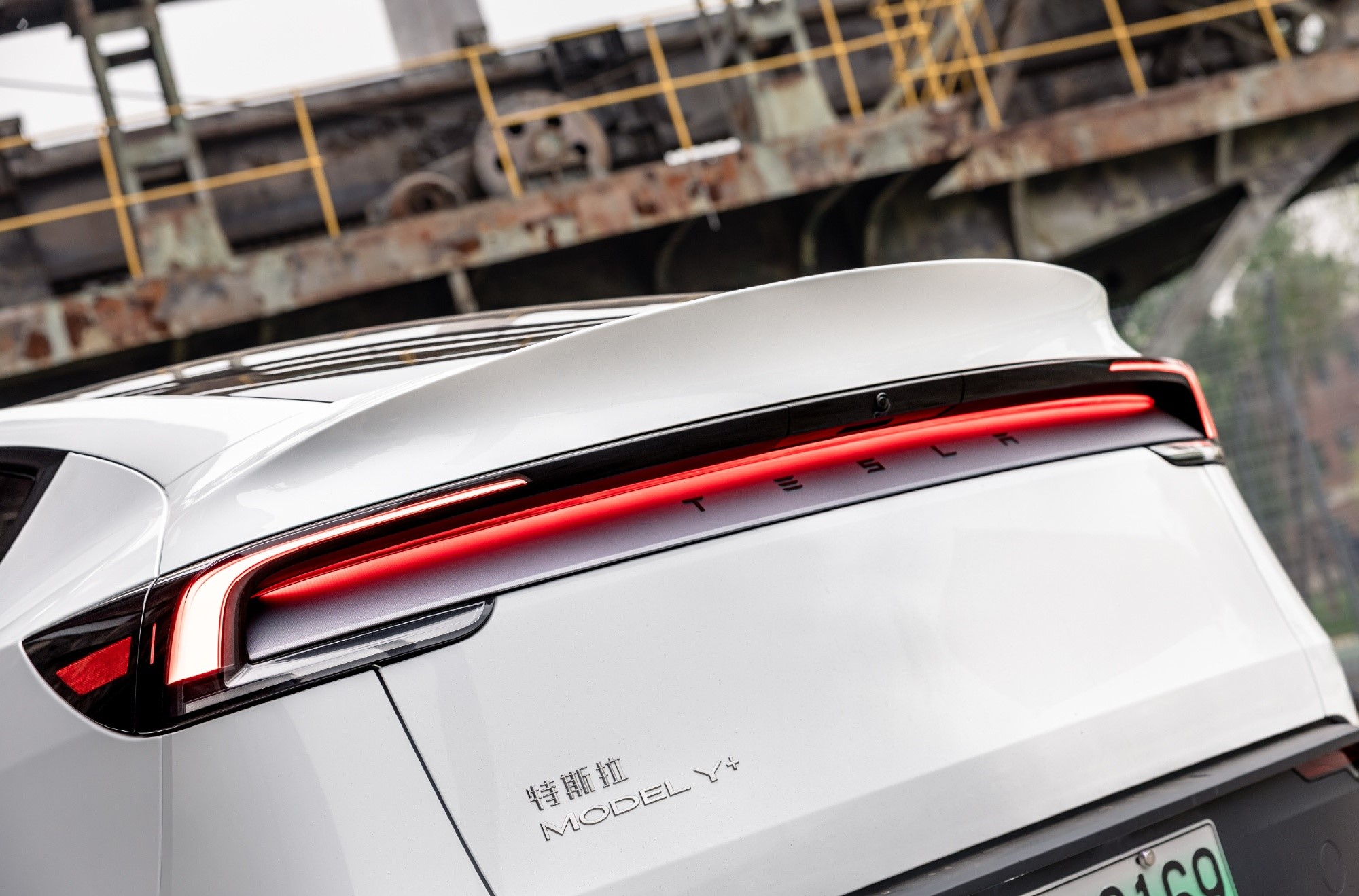
Cantor Fitzgerald is holding firm on its bullish stance for Tesla (NASDAQ: TSLA), reiterating its “Overweight” rating and $355 price target amidst the company’s release of its Q2 2025 vehicle delivery and production report.
Tesla delivered 384,122 vehicles in Q2 2025, falling below last year’s Q2 figure of 443,956 units. Despite softer demand in some countries in Europe and ongoing controversies surrounding CEO Elon Musk, the firm maintained its view that Tesla is a long-term growth story in the EV sector.
Tesla’s Q2 results
Among the 384,122 vehicles that Tesla delivered in the second quarter, 373,728 were Model 3 and Model Y. The remaining 10,394 units were attributed to the Model S, Model X, and Cybertruck. Production was largely flat year-over-year at 410,244 units.
In the energy division, Tesla deployed 9.6 GWh of energy storage in Q2, which was above last year’s 9.4 GWh. Overall, Tesla continues to hold a strong position with $95.7 billion in trailing twelve-month revenue and a 17.7% gross margin, as noted in a report from Investing.com.
Tesla’s stock is still volatile
Tesla’s market cap fell to $941 billion on Monday amid volatility that was likely caused in no small part by CEO Elon Musk’s political posts on X over the weekend. Musk has announced that he is forming the America Party to serve as a third option for voters in the United States, a decision that has earned the ire of U.S. President Donald Trump.
Despite Musk’s controversial nature, some analysts remain bullish on TSLA stock. Apart from Cantor Fitzgerald, Canaccord Genuity also reiterated its “Buy” rating on Tesla shares, with the firm highlighting the company’s positive Q2 vehicle deliveries, which exceeded its expectations by 24,000 units. Cannacord also noted that Tesla remains strong in several markets despite its year-over-year decline in deliveries.
-
Elon Musk2 weeks ago
Tesla investors will be shocked by Jim Cramer’s latest assessment
-
News2 days ago
Tesla debuts hands-free Grok AI with update 2025.26: What you need to know
-
Elon Musk4 days ago
xAI launches Grok 4 with new $300/month SuperGrok Heavy subscription
-
Elon Musk7 days ago
Elon Musk confirms Grok 4 launch on July 9 with livestream event
-
News1 week ago
Tesla Model 3 ranks as the safest new car in Europe for 2025, per Euro NCAP tests
-
Elon Musk2 weeks ago
xAI’s Memphis data center receives air permit despite community criticism
-
News4 days ago
Tesla begins Robotaxi certification push in Arizona: report
-
News2 weeks ago
Tesla sees explosive sales growth in UK, Spain, and Netherlands in June