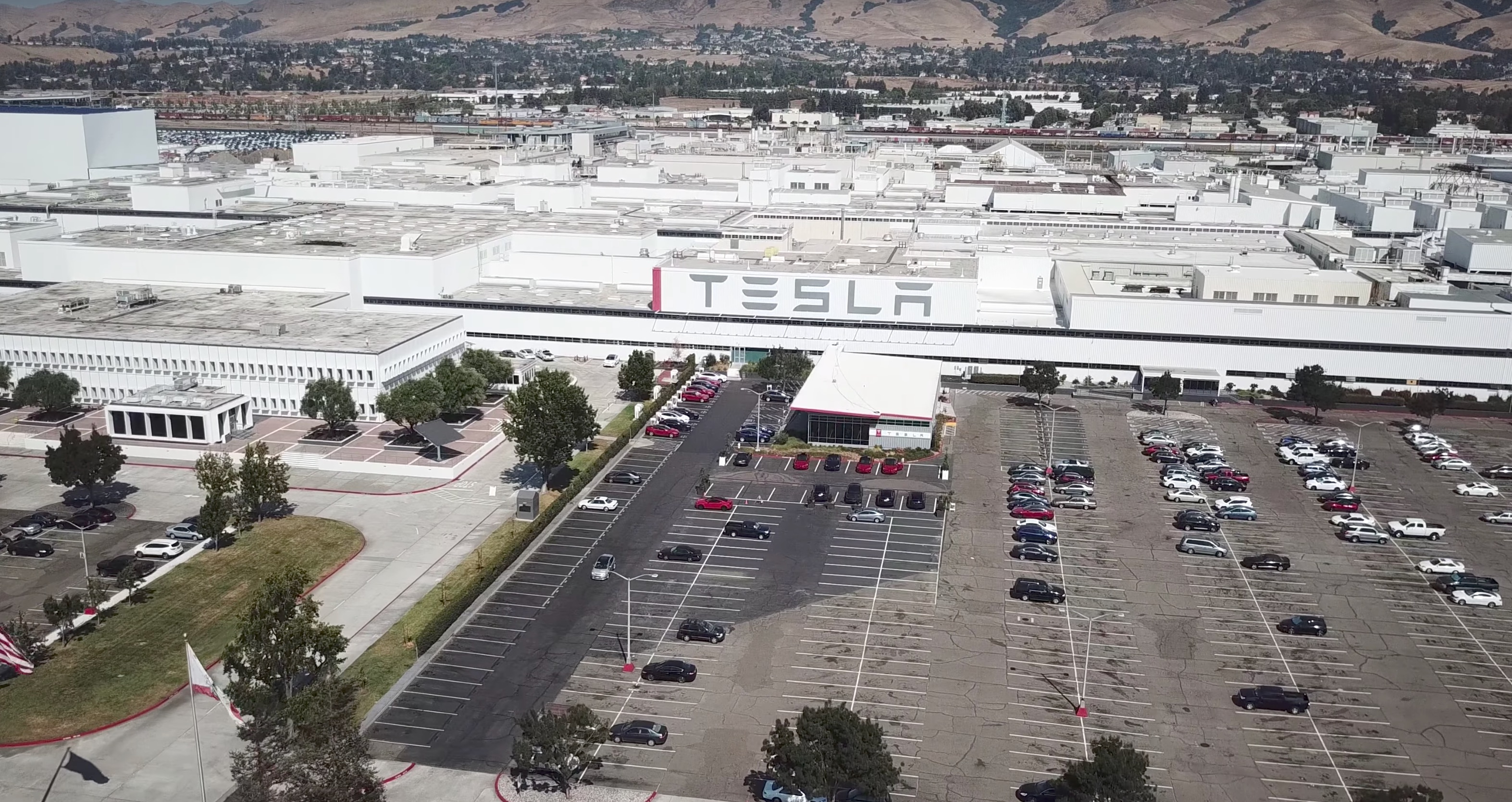
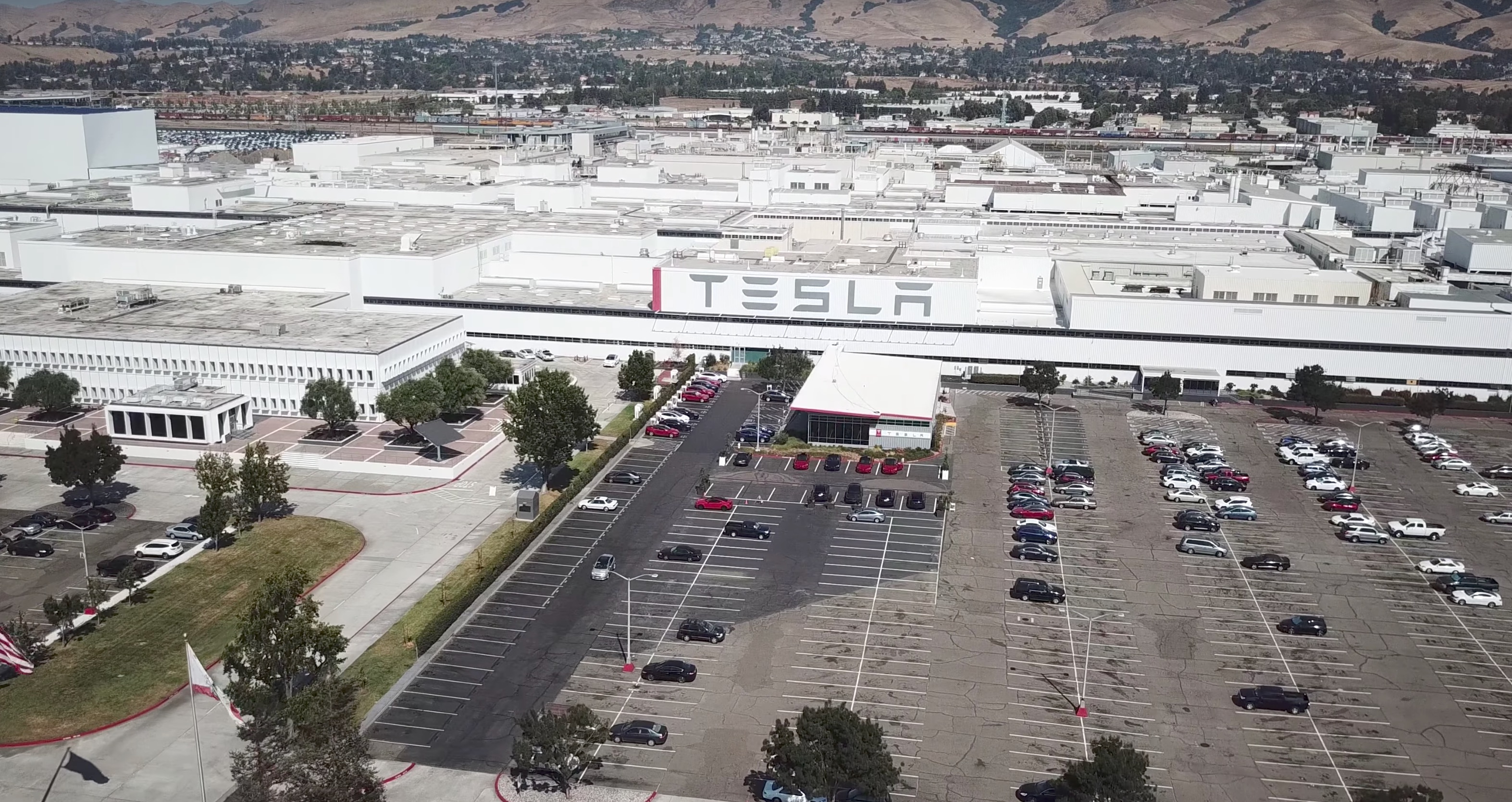
News
Tesla outlines plan to become safest car factory in the world
Tesla VP for Environmental, Health, and Safety (EHS) Laurie Shelby outlined in a blog post how the California-based electric car maker and energy company plans to attain its goal of having the safest car factory in the world. Tesla’s safety plan covers several aspects of its factories’ operations, from the training of new employees to the compensation injured workers receive after incurring work-related injuries.
Shelby, a 25-year veteran in the EHS field, noted that Tesla has been on the right track even before she joined the company back in October 2017. In her blog post, Shelby noted that safety in an automotive production line usually goes down to common sense, a culture that values safety, the rollout of proactive preventive measures, and a management that listens to its employees. The EHD veteran stated that much of these attributes are present in Tesla’s Fremont factory.
One thing that Shelby particularly focused on is Tesla’s proactive stance when it comes to workplace safety. By adopting a proactive stance, the California-based electric car maker and energy firm can address possible safety issues even before an incident happens. In the Model 3 production line alone, a comment from one of the factory’s employees ultimately resulted in the implementation of new safety measures for workers in the assembly line. This, together with Tesla’s habit of observing how employees work even when no issues are occurring, positively impacts the company’s safety.
A key factor in Tesla’s improvement in terms of workplace safety comes from its willingness to change its policies over time as well. According to Shelby, a particularly good example of this is the change in Tesla’s Return to Work program. In the past, Tesla followed the conventional approach in the auto industry, reassigning injured workers to a less demanding post until they are fully recovered. The problem with this system was that employees are paid according to their temporary post, which results in lower pay, despite disability payments or the collection of workers’ compensation.
In Tesla’s new Return to Work program, injured workers still get reassigned to less demanding posts. Unlike the previous system, however, recovering employees will not see any adjustments in their compensation. In the event that Tesla cannot accommodate the recovering worker in the factory, the employee will be temporarily asked to render hours in nonprofits like the YMCA, libraries, or even food pantries, where they will be paid their regular salary.
According to the EHS veteran, the Elon Musk-led firm is implementing an even more intensive training program for new employees, covering the basics of manufacturing, ergonomics, and workplace safety. Tesla is also hiring a new medical director that will oversee a 24/7 in-house medical center. Furthermore, athletic trainers are being hired to work proactively with employees, especially those who are feeling aches and pains from their work in the factory.
Overall, Shelby stated that Tesla had already managed to take significant strides in workplace safety over the years. In 2017 alone, Tesla’s Total Recordable Incident Rate (TRIR), the workplace safety metric, averaged 6.2, which is well within the industry average. In comparison, the Fremont facility, when it was being managed by NUMMI, averaged 12.6 between 2003-2009.
News
Tesla begins Robotaxi certification push in Arizona: report
Tesla seems serious about expanding its Robotaxi service to several states in the coming months.
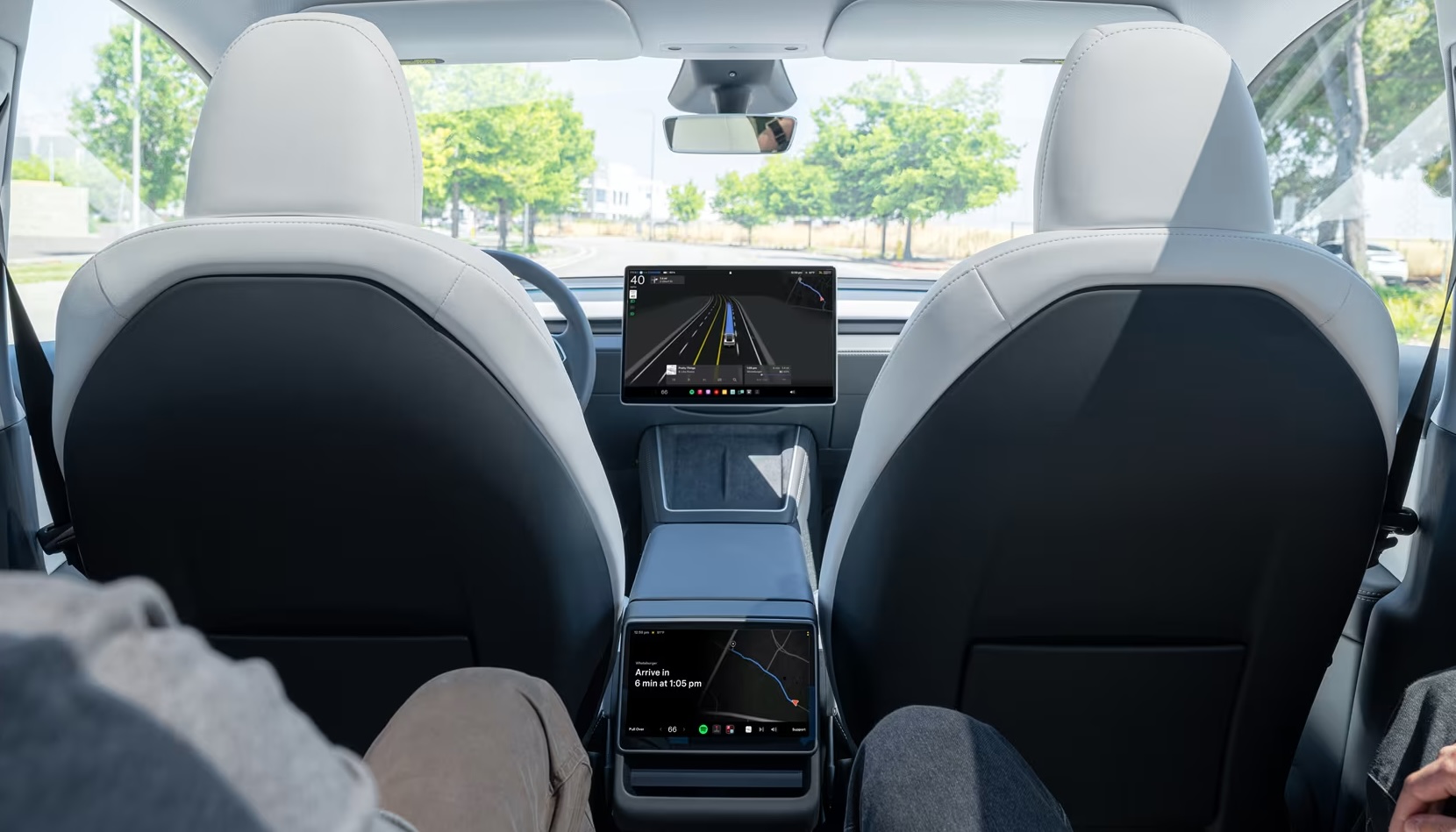
Tesla has initiated discussions with Arizona transportation regulators to certify its driverless Robotaxi service in the state, as per a recent report from Bloomberg News. The move follows Tesla’s launch of its Robotaxi pilot program in Austin, Texas, as well as CEO Elon Musk’s recent comments about the service’s expansion in the Bay Area.
The Arizona Department of Transportation confirmed to Bloomberg that Tesla has reached out to begin the certification process for autonomous ride-sharing operations in the state. While details remain limited, the outreach suggests that Tesla is serious about expanding its driverless Robotaxi service to several territories in the coming months.
The Arizona development comes as Tesla prepares to expand its service area in Austin this weekend, as per CEO Elon Musk in a post on X. Musk also stated that Tesla is targeting the San Francisco Bay Area as its next major market, with a potential launch “in a month or two,” pending regulatory approvals.
Tesla first launched its autonomous ride-hailing program on June 22 in Austin with a small fleet of Model Y vehicles, accompanied by a Tesla employee in the passenger seat to monitor safety. While still classified as a test, Musk has said the program will expand to about 1,000 vehicles in the coming months. Tesla will later upgrade its Robotaxi fleet with the Cyercab, a two-seater that is designed without a steering wheel.
Sightings of Cybercab castings around the Giga Texas complex suggests that Tesla may be ramping the initial trial production of the self-driving two-seater. Tesla, for its part, has noted in the past that volume production of the Cybercab is expected to start sometime next year.
In California, Tesla has already applied for a transportation charter-party carrier permit from the state’s Public Utilities Commission. The company is reportedly taking a phased approach to operating in California, with the Robotaxi service starting with pre-arranged rides for employees in vehicles with safety drivers.
News
Tesla sets November 6 date for 2025 Annual Shareholder Meeting
The automaker announced the date on Thursday in a Form 8-K.
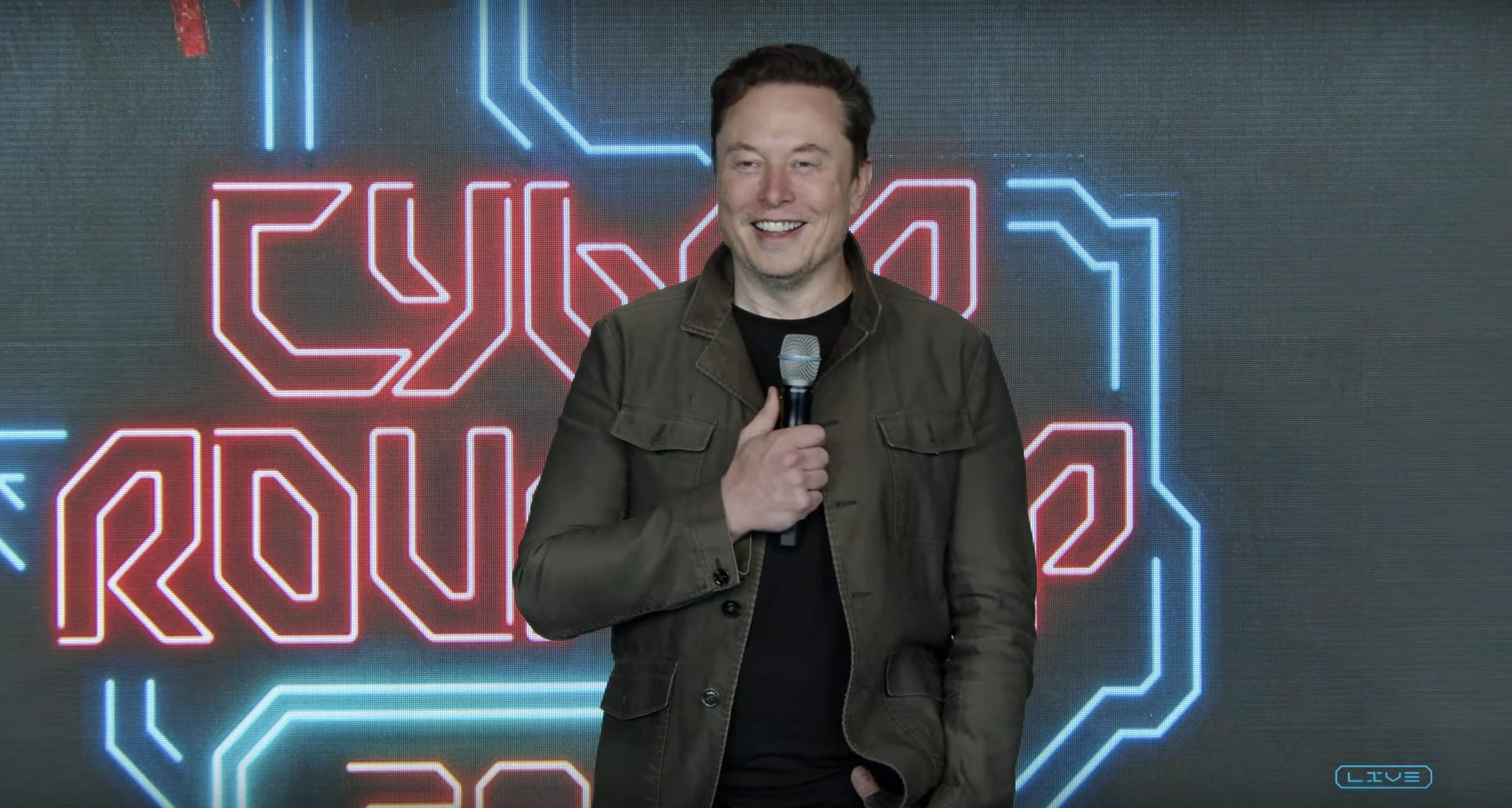
Tesla has scheduled its 2025 annual shareholder meeting for November 6, addressing investor concerns that the company was nearing a legal deadline to hold the event.
The automaker announced the date on Thursday in a Form 8-K submitted to the United States Securities and Exchange Commission (SEC). The company also listed a new proposal submission deadline of July 31 for items to be included in the proxy statement.
Tesla’s announcement followed calls from a group of 27 shareholders, including the leaders of large public pension funds, which urged Tesla’s board to formally set the meeting date, as noted in a report from The Wall Street Journal.
The group noted that under Texas law, where Tesla is now incorporated, companies must hold annual meetings within 13 months of the last one if requested by shareholders. Tesla’s previous annual shareholder meeting was held on June 13, 2024, which placed the July 13 deadline in focus.
Tesla originally stated in its 2024 annual report that it would file its proxy statement by the end of April. However, an amended filing on April 30 indicated that the Board of Directors had not yet finalized a meeting date, at least at the time.
The April filing also confirmed that Tesla’s board had formed a special committee to evaluate certain matters related to CEO Elon Musk’s compensation plan. Musk’s CEO performance award remains at the center of a lengthy legal dispute in Delaware, Tesla’s former state of incorporation.
Due to the aftermath of Musk’s legal dispute about his compensation plan in Delaware, he has not been paid for his work at Tesla for several years. Musk, for his part, has noted that he is more concerned about his voting stake in Tesla than his actual salary.
At last year’s annual meeting, TSLA shareholders voted to reapprove Elon Musk’s compensation plan and ratified Tesla’s decision to relocate its legal domicile from Delaware to Texas.
Elon Musk
Grok coming to Tesla vehicles next week “at the latest:” Elon Musk
Grok’s rollout to Tesla vehicles is expected to begin next week at the latest.
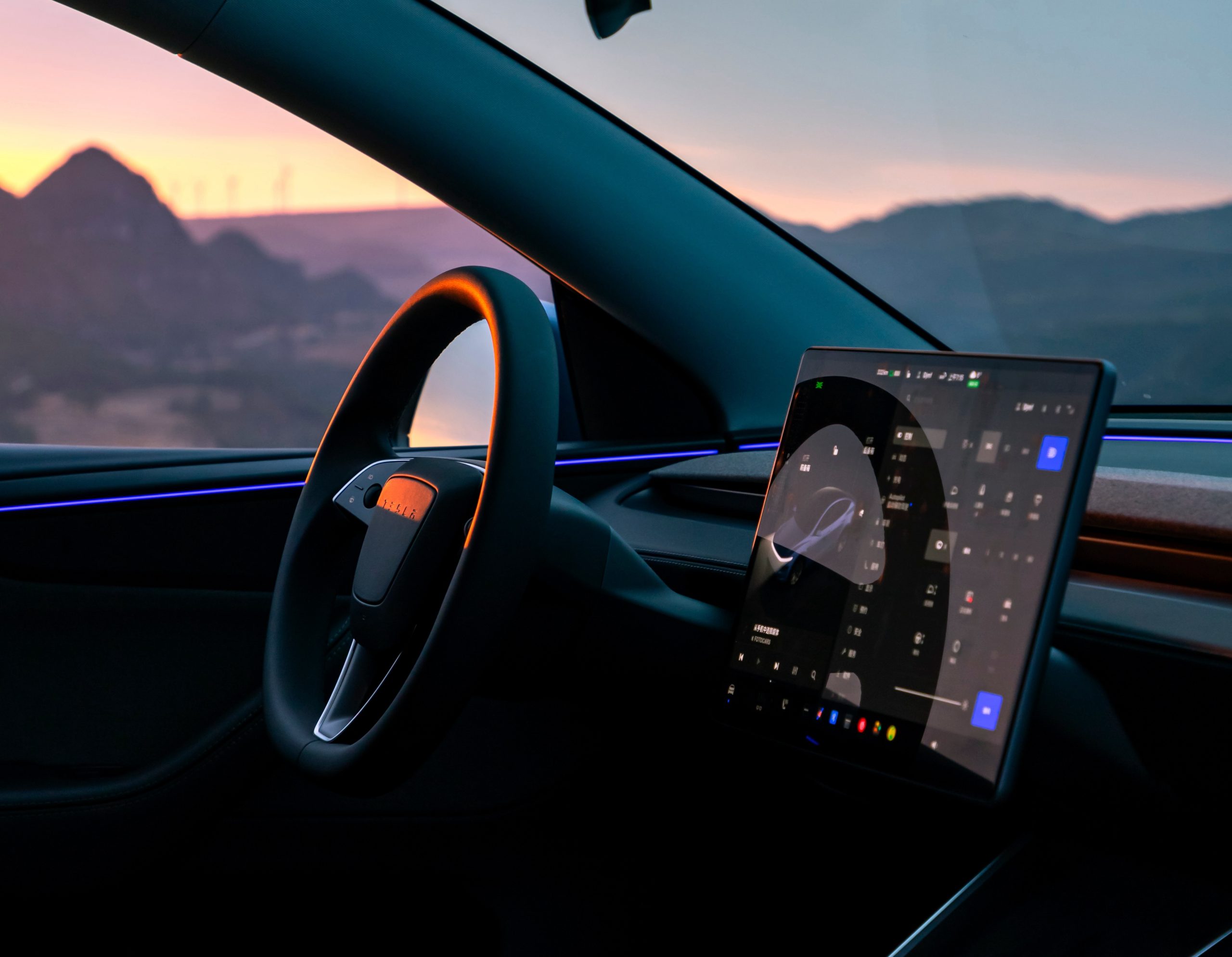
Elon Musk announced on Thursday that Grok, the large language model developed by his startup xAI, will soon be available in Tesla vehicles. Grok’s rollout to Tesla vehicles is expected to begin next week at the latest, further deepening the ties between the two Elon Musk-led companies.
Tesla–xAI synergy
Musk confirmed the news on X shortly after livestreaming the release of Grok 4, xAI’s latest large language model. “Grok is coming to Tesla vehicles very soon. Next week at the latest,” Musk wrote in a post on social media platform X.
During the livestream, Musk and several members of the xAI team highlighted several upgrades to Grok 4’s voice capabilities and performance metrics, positioning the LLM as competitive with top-tier models from OpenAI and Google.
The in-vehicle integration of Grok marks a new chapter in Tesla’s AI development. While Tesla has long relied on in-house systems for autonomous driving and energy optimization, Grok’s integration would introduce conversational AI directly into its vehicles’ user experience. This integration could potentially improve customer interaction inside Tesla vehicles.
xAI and Tesla’s collaborative footprint
Grok’s upcoming rollout to Tesla vehicles adds to a growing business relationship between Tesla and xAI. Earlier this year, Tesla disclosed that it generated $198.3 million in revenue from commercial, consulting, and support agreements with xAI, as noted in a report from Bloomberg News. A large portion of that amount, however, came from the sale of Megapack energy storage systems to the artificial intelligence startup.
In July 2023, Musk polled X users about whether Tesla should invest $5 billion in xAI. While no formal investment has been made so far, 68% of poll participants voted yes, and Musk has since stated that the idea would be discussed with Tesla’s board.
-
Elon Musk1 week ago
Tesla investors will be shocked by Jim Cramer’s latest assessment
-
Elon Musk3 days ago
Elon Musk confirms Grok 4 launch on July 9 with livestream event
-
Elon Musk16 hours ago
xAI launches Grok 4 with new $300/month SuperGrok Heavy subscription
-
News7 days ago
Tesla Model 3 ranks as the safest new car in Europe for 2025, per Euro NCAP tests
-
Elon Musk2 weeks ago
A Tesla just delivered itself to a customer autonomously, Elon Musk confirms
-
Elon Musk1 week ago
xAI’s Memphis data center receives air permit despite community criticism
-
Elon Musk2 weeks ago
Tesla’s Omead Afshar, known as Elon Musk’s right-hand man, leaves company: reports
-
News2 weeks ago
Xiaomi CEO congratulates Tesla on first FSD delivery: “We have to continue learning!”