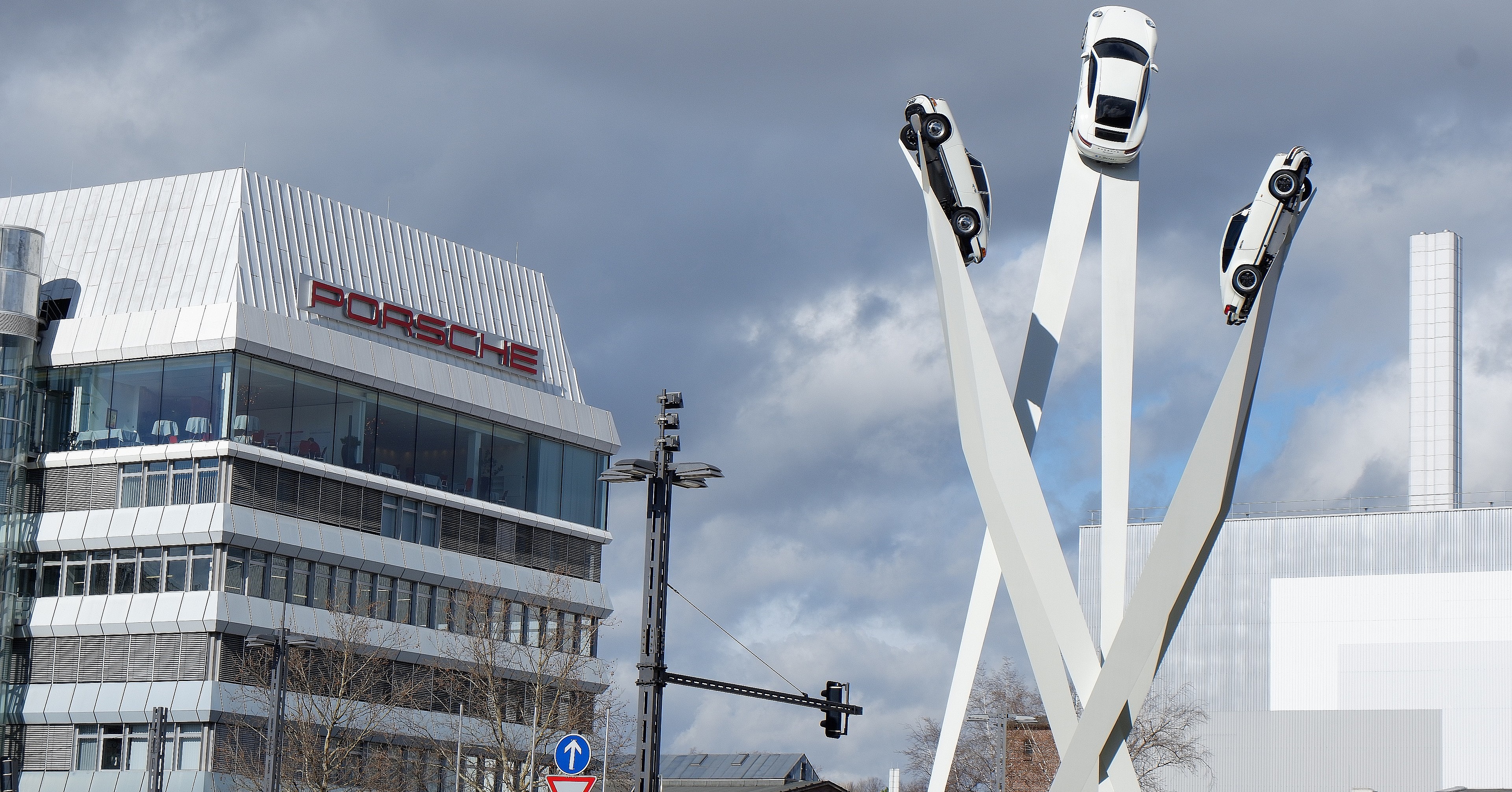
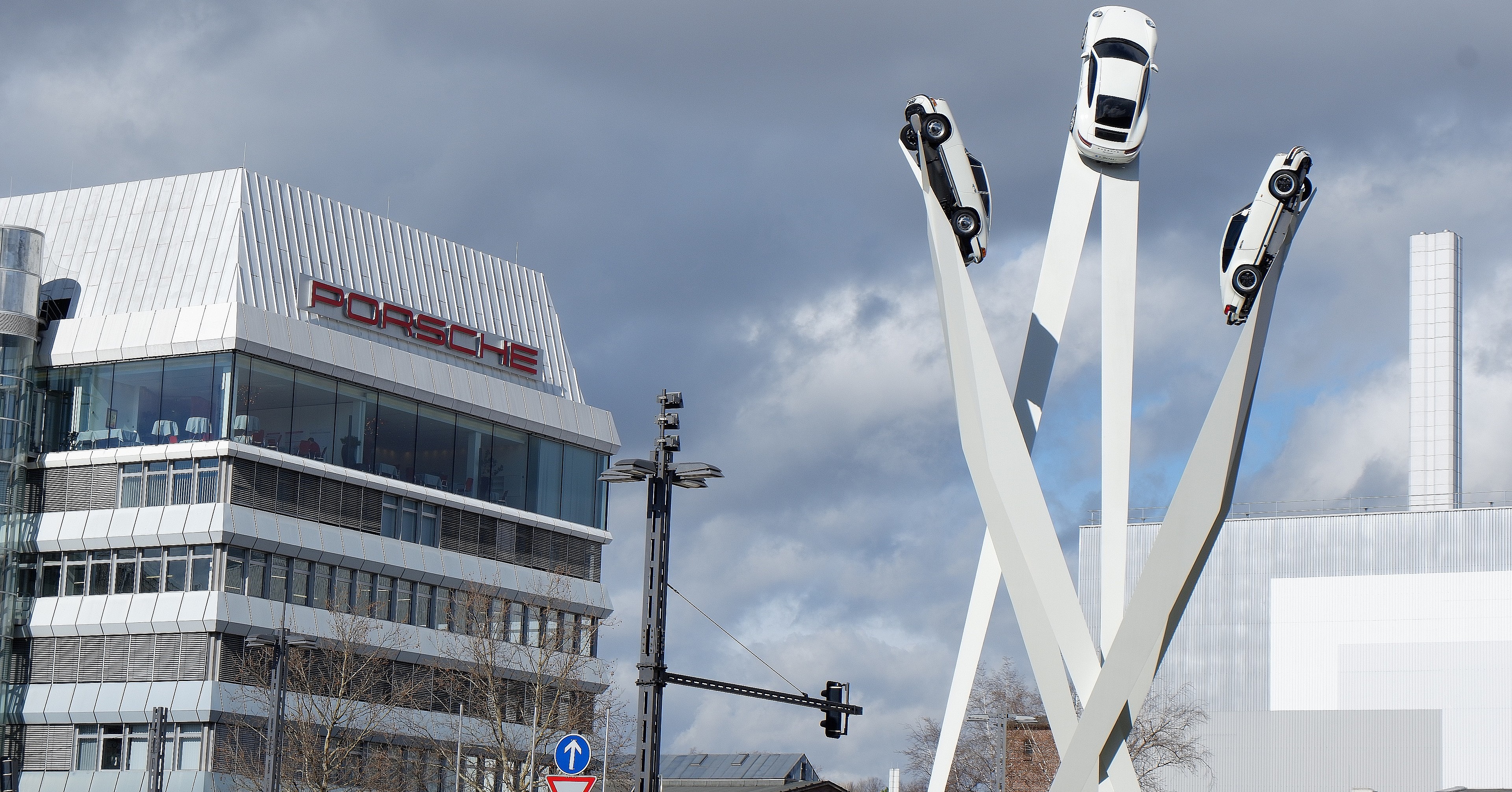
News
Exclusive: Porsche’s electric heart beats in the Taycan’s Zuffenhausen factory
Beside the red-bricked walls of Porsche’s headquarters at Zuffenhausen, an electric transformation is taking place. It is a transformation that echoes back to its earliest days, despite the company’s pedigree with the internal combustion engine. Tall, modern-looking buildings sit side-by-side with older factories and shops that have literally witnessed history. The faint sounds of heavy machinery are audible in the distance, a reminder that work in the historic site is ongoing.
“We’re building a factory within a factory within a city with residences close by, hardly any space, and this in high speed,” says Porsche representative of the project David Tryggvason, lightly pointing out that the timeframe of the project is very Porsche-like: Sporty.
Porsche is actively engaged in a massive construction project in its Stuttgart-Zuffenhausen site, roughly 120 miles from Frankfurt, with the company running full throttle as it prepares for the production of the Taycan. The result of these efforts could only be described as a rebirth of sorts, since the company that started with an electric car is now pushing itself to re-embrace all-electric vehicles, perhaps just as intended by its founder, Ferdinand Porsche, more than a hundred years ago.
An electric transition
A lot is riding on the Porsche Taycan. During the company’s annual press conference, Porsche CEO Oliver Blume and Deputy Chairman of the Executive Board Lutz Meschke emphasized how all-electric vehicles like the Taycan and its lineup of hybrid cars are pertinent for the company’s future. In a statement, Meschke noted that by 2030, vehicles powered by an internal combustion engine would likely be the exception to the rule.
“One thing is clear: from 2030 onwards; there probably won’t be any vehicle model from Porsche without an electric variant. I actually presume that by 2025, we will have electrified significantly more than half of our entire model range. But the combustion engine will still be around in 2030. Our 911 will hopefully still be driving with them for a long time to come. Conventionally powered vehicles will at that point be the niche in our electric fleet,” he said.
Before it can produce a successful electric vehicle, Porsche needs to ensure that it has the facilities necessary to build a completely different type of car. The veteran automaker opted to construct several new facilities to accommodate the Taycan’s production, and it had to overcome numerous challenges to make the buildout possible. The Zuffenhausen site is a stone’s throw away from a residential neighborhood, and the site itself is split by a four-lane road. With space being scarce, Tryggvason notes that the company did the only thing it can do: it built up. Overall, building the Taycan is complex. Setting up the facility even more so. For the project manager, the challenges were worth it. “We believe in the product,” David said.

A high-stakes, collective effort
The company’s bet on the Taycan is evident in its investment for the vehicle and the actions of its own employees. Porsche is spending about 6 billion euros (around $6.81 billion) for the development of its electric mobility initiatives. Porsche Production 4.0, a campaign aimed at ushering in a new era of vehicle production, is also underway. Accelerating these developments is a deal that the carmaker struck with its employees, who agreed to forego a small part of their collective salary increase in exchange for their participation in the Taycan’s production and release.
David Tryggvason and Porsche Press Spokesman Jorg Walz later directed me to the roof of one of the new buildings, and I was able to get a pretty good view of the factory itself. They pointed out how the Taycan starts its life by having its electric motors, batteries, and axles assembled. The electric car’s body then gets put together, painted, and transported across a long conveyor system where it can go through final assembly and married to its electric drive unit.
A key to the successful production run of the Porsche Taycan is the company’s target of manufacturing the vehicle in a “smart, lean and green” manner. Examples of these include a flexi-line that uses automated guided vehicles for simpler assembly despite the expansive customization requests from Taycan buyers, optimizations in the use of resources and space, and an initiative to ensure that the entire production process of the all-electric car at Porsche’s Stuttgart-Zuffenhausen site is CO2-neutral. This is made possible through several programs such as the electrification of logistics vehicles, the use of waste heat in the paint shop, and a pilot trial that involves the adoption of nitrogen-absorbing facade surfaces, to name a few.
Race-bred batteries for a race-bred electric car
Not one to waste a rare opportunity to ask for details about the Taycan, I decided to ask a little about the electric car’s battery performance. Over the past year, several great electric vehicles were released by veteran carmakers such as Jaguar and Mercedes-Benz, but inasmuch as the machines themselves were impressive, their batteries left much to be desired. The I-PACE, for all its stunning interior and excellent design, is pretty much the electric equivalent of a gas guzzler. The Mercedes-Benz EQC seems to be the same.
Porsche uses pouch cells from LG Chem in the Taycan’s battery pack, which is expected to give the vehicle over 300 miles of range per charge under the NEDC standard. The company is aiming for ultra-fast 350 kW charging as well, thanks to its 800-volt technology, which was used first in Porsche’s LMP1 racecar 919 Hybrid. I asked how the Taycan’s battery holds up when charged continually with such a high rate of charge. Walz smiled and candidly stated “We’re very optimistic.”
After the annual press conference, I was able to sit in for an informal discussion of Porsche’s electrification with executive board member Detlev von Platen. The Porsche exec highlighted that the Taycan’s battery cells were closely developed by the company, thanks to its experience from its high-performance hybrid vehicles. Examples include the legendary Porsche 918 Spyder hypercar and the three-time Le Mans-winning Porsche 919 Hybrid racecar, both of which required some work in their batteries.
“So we’re absolutely involved, deeply involved, in the development of the (Taycan’s battery) cells and the technology behind it. We haven’t started last year with the Taycan. We have worked since a long time already on battery technology from motorsport. Our prototypes like the 919 Hybrid was electrified. So I would say, in general terms, that we have started to work on battery technology at least ten years now,” Von Platen candidly said.
I was reminded of David Tryggvason’s overview of the Taycan’s components a couple of days before, when he remarked that some of the Porsche personnel who worked for the 918 Spyder hypercar also worked in the development of the Taycan. Upon hearing Von Platen’s description of Porsche’s work with batteries, I couldn’t help but agree with his point. Porsche has produced several iconic vehicles in the past, and the majority of them are powered by the internal combustion engine. Despite this, it is difficult to argue that the best cars the company has ever produced, such as the 919 Hybrid, are imbued with electric propulsion at their core. Beneath the roaring engines of the vehicles were electric motors and batteries that ultimately unlocked the cars’ real potential.

From the past to the future
An engineer at heart, Ferdinand Porsche started with an electric car at the end of the 19th century. He later dipped his feet in hybrid propulsion, before going ahead and gaining mastery of the internal combustion engine. From this perspective, the development of the Taycan feels like a homage to the company’s roots, and this is a big reason why Porsche is dead serious about the vehicle. In what appears to be a gesture to prove this, the Taycan is being built on the company’s most historic site, and it will be produced alongside the 911, a vehicle that can only be dubbed as the quintessential Porsche.
As I grabbed my travel gear and scurried to the remaining shuttle that was awaiting my presence, I looked back at Porsche’s headquarters one last time. There in the dark sky stood a marvel of orderliness in this ever-changing world. It was a moment that can only to be described as surreal, when the past breathes new life into the future. Seconds later, as I buckled myself down on the shuttle seat and gazed into a disappearing Zuffenhausen site, the sounds of whirring machinery and vehicles rolling off the factory floor can be heard in the distance. Beneath this orchestra of sounds were the rhythmic thumps of heavy equipment that continued to work tirelessly to build Taycan’s upcoming production facilities.
I couldn’t help but imagine that the sounds were representative of the electric heartbeat of a carmaker, coming to life once more.
News
Tesla launches in India with Model Y, showing pricing will be biggest challenge
Tesla finally got its Model Y launched in India, but it will surely come at a price for consumers.
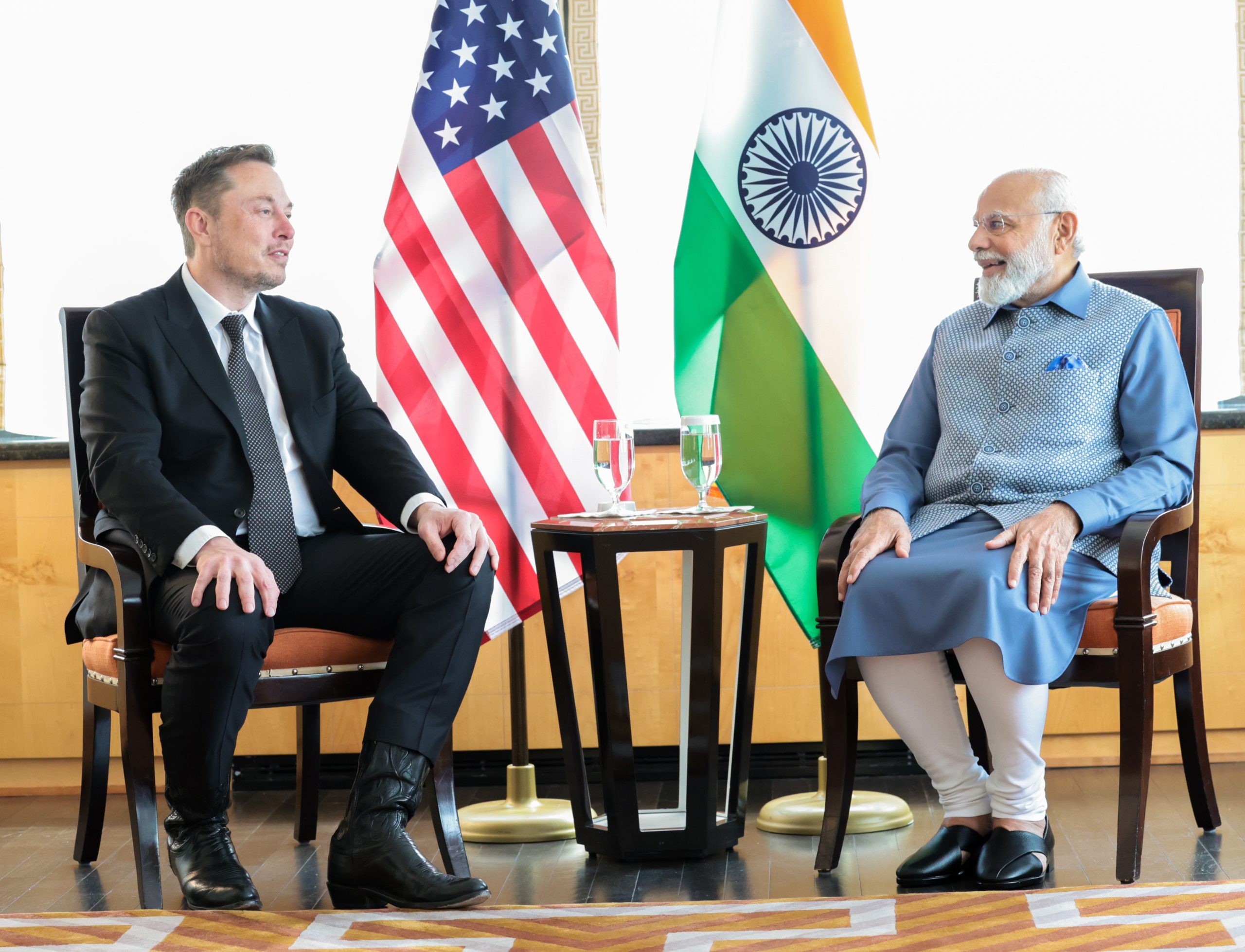
Tesla has officially launched in India following years of delays, as it brought its Model Y to the market for the first time on Tuesday.
However, the launch showed that pricing is going to be its biggest challenge. The all-electric Model Y is priced significantly higher than in other major markets in which Tesla operates.
On Tuesday, Tesla’s Model Y went up for sale for 59,89,000 rupees for the Rear-Wheel Drive configuration, while the Long Range Rear-Wheel Drive was priced at 67,89,000.
This equates to $69,686 for the RWD and $78,994 for the Long Range RWD, a substantial markup compared to what these cars sell for in the United States.
🚨 Here’s the difference in price for the Tesla Model Y in the U.S. compared to India.
🚨 59,89,000 is $69,686
🚨 67,89,000 is $78,994 pic.twitter.com/7EUzyWLcED— TESLARATI (@Teslarati) July 15, 2025
Deliveries are currently scheduled for the third quarter, and it will be interesting to see how many units they can sell in the market at this price point.
The price includes tariffs and additional fees that are applied by the Indian government, which has aimed to work with foreign automakers to come to terms on lower duties that increase vehicle cost.
Tesla Model Y seen testing under wraps in India ahead of launch
There is a chance that these duties will be removed, which would create a more stable and affordable pricing model for Tesla in the future. President Trump and Indian Prime Minister Narendra Modi continue to iron out those details.
Maharashtra Chief Minister Devendra Fadnavis said to reporters outside the company’s new outlet in the region (via Reuters):
“In the future, we wish to see R&D and manufacturing done in India, and I am sure at an appropriate stage, Tesla will think about it.”
It appears to be eerily similar to the same “game of chicken” Tesla played with Indian government officials for the past few years. Tesla has always wanted to enter India, but was unable to do so due to these import duties.
India wanted Tesla to commit to building a Gigafactory in the country, but Tesla wanted to test demand first.
It seems this could be that demand test, and the duties are going to have a significant impact on what demand will actually be.
Elon Musk
Tesla ups Robotaxi fare price to another comical figure with service area expansion
Tesla upped its fare price for a Robotaxi ride from $4.20 to, you guessed it, $6.90.
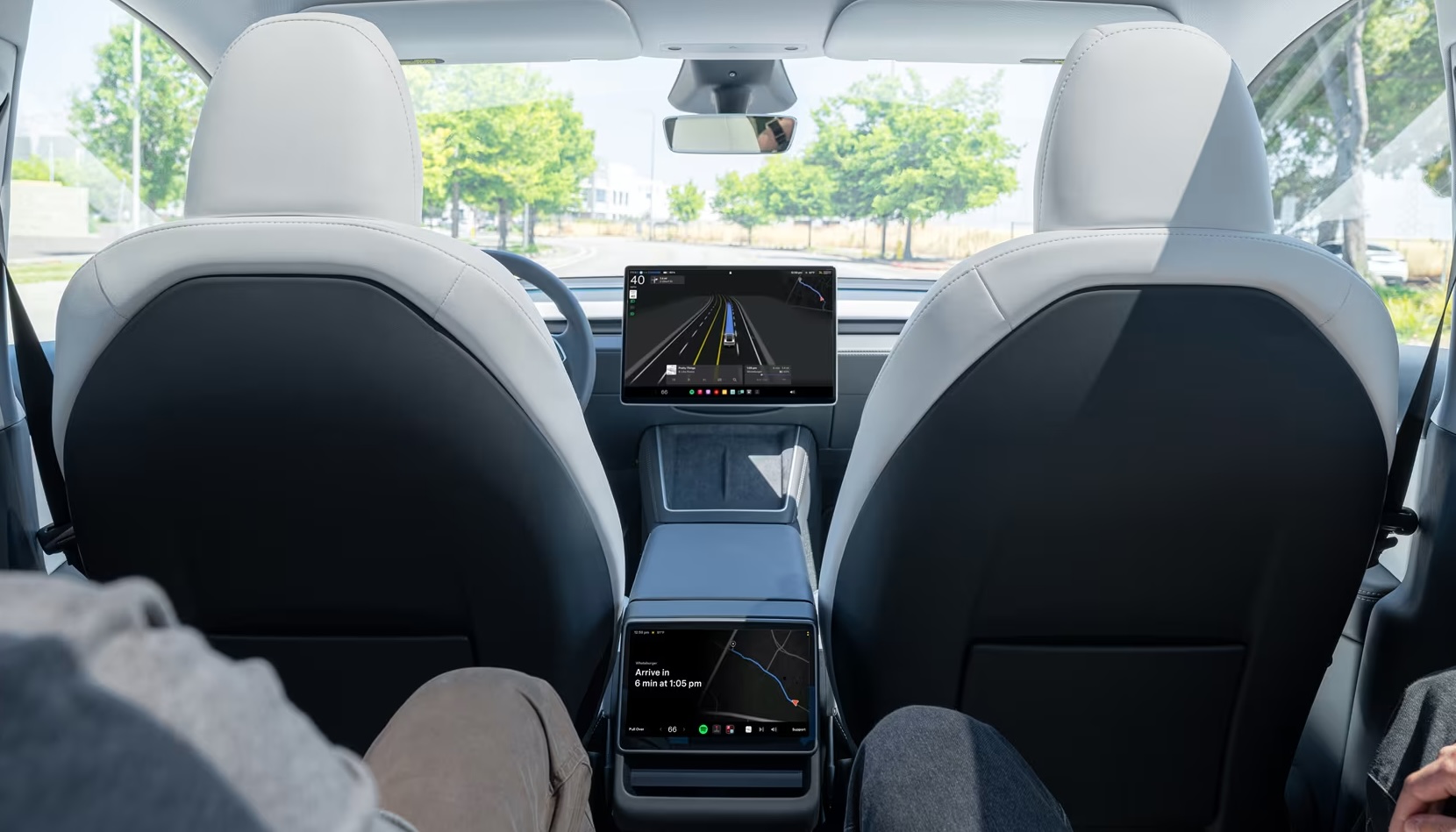
Tesla has upped its fare price for the Robotaxi platform in Austin for the first time since its launch on June 22. The increase came on the same day that Tesla expanded its Service Area for the Robotaxi ride-hailing service, offering rides to a broader portion of the city.
The price is up from $4.20, a figure that many Tesla fans will find amusing, considering CEO Elon Musk has used that number, as well as ’69,’ as a light-hearted attempt at comedy over the past several years.
Musk confirmed yesterday that Tesla would up the price per ride from that $4.20 point to $6.90. Are we really surprised that is what the company decided on, as the expansion of the Service Area also took effect on Monday?
But the price is now a princely $6.90, as foretold in the prophecy 😂
— Elon Musk (@elonmusk) July 14, 2025
The Service Area expansion was also somewhat of a joke too, especially considering the shape of the new region where the driverless service can travel.
I wrote yesterday about how it might be funny, but in reality, it is more of a message to competitors that Tesla can expand in Austin wherever it wants at any time.
Tesla’s Robotaxi expansion wasn’t a joke, it was a warning to competitors
It was only a matter of time before the Robotaxi platform would subject riders to a higher, flat fee for a ride. This is primarily due to two reasons: the size of the access program is increasing, and, more importantly, the service area is expanding in size.
Tesla has already surpassed Waymo in Austin in terms of its service area, which is roughly five square miles larger. Waymo launched driverless rides to the public back in March, while Tesla’s just became available to a small group in June. Tesla has already expanded it, allowing new members to hail a ride from a driverless Model Y nearly every day.
The Robotaxi app is also becoming more robust as Tesla is adding new features with updates. It has already been updated on two occasions, with the most recent improvements being rolled out yesterday.
Tesla updates Robotaxi app with several big changes, including wider service area
News
Tesla Model Y and Model 3 dominate U.S. EV sales despite headwinds
Tesla’s two mainstream vehicles accounted for more than 40% of all EVs sold in the United States in Q2 2025.
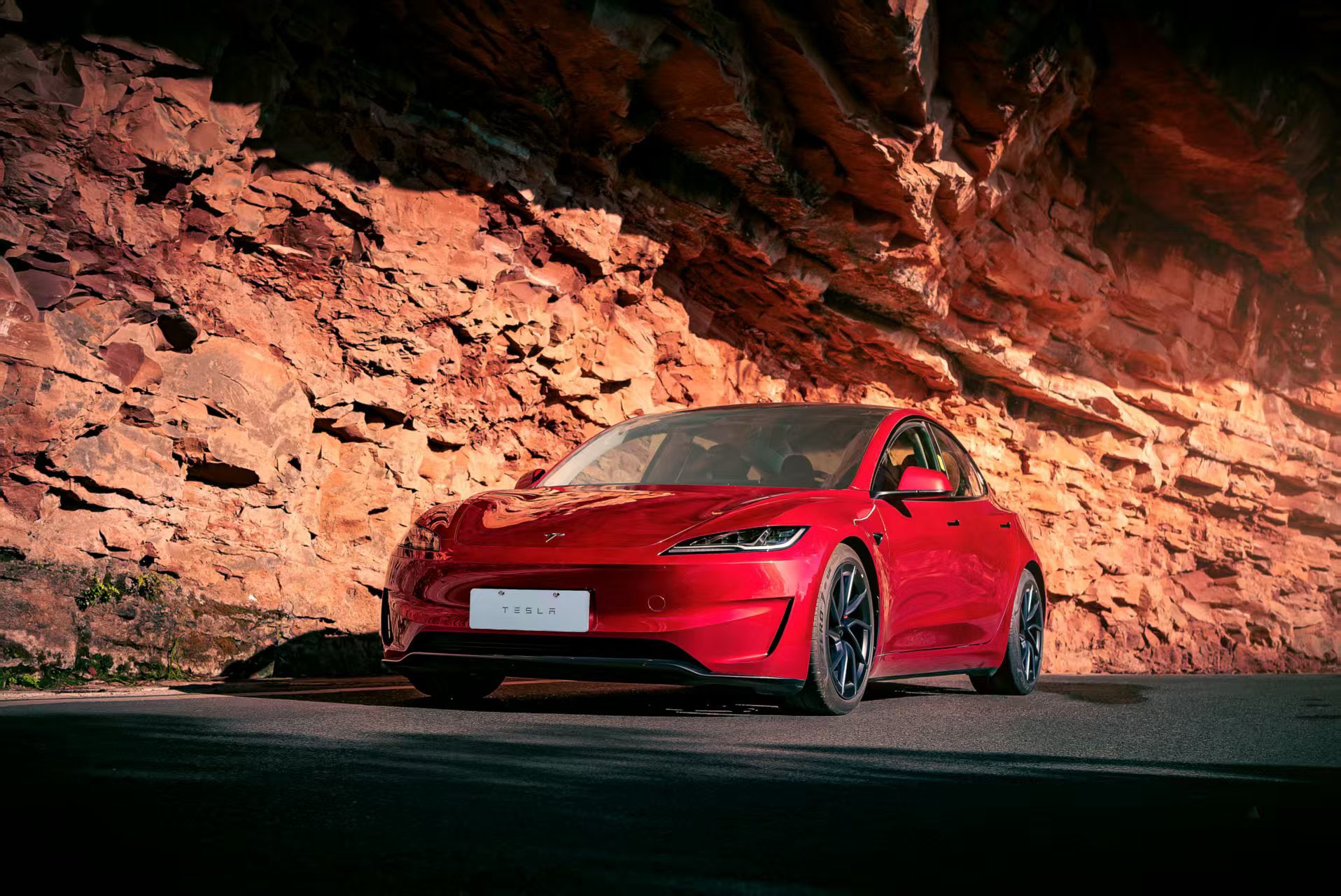
Tesla’s Model Y and Model 3 remained the top-selling electric vehicles in the U.S. during Q2 2025, even as the broader EV market dipped 6.3% year-over-year.
The Model Y logged 86,120 units sold, followed by the Model 3 at 48,803. This means that Tesla’s two mainstream vehicles accounted for 43% of all EVs sold in the United States during the second quarter, as per data from Cox Automotive.
Tesla leads amid tax credit uncertainty and a tough first half
Tesla’s performance in Q2 is notable given a series of hurdles earlier in the year. The company temporarily paused Model Y deliveries in Q1 as it transitioned to the production of the new Model Y, and its retail presence was hit by protests and vandalism tied to political backlash against CEO Elon Musk. The fallout carried into Q2, yet Tesla’s two mass-market vehicles still outsold the next eight EVs combined.
Q2 marked just the third-ever YoY decline in quarterly EV sales, totaling 310,839 units. Electric vehicle sales, however, were still up 4.9% from Q1 and reached a record 607,089 units in the first half of 2025. Analysts also expect a surge in Q3 as buyers rush to qualify for federal EV tax credits before they expire on October 1, Cox Automotive noted in a post.
Legacy rivals gain ground, but Tesla holds its commanding lead
General Motors more than doubled its EV volume in the first half of 2025, selling over 78,000 units and boosting its EV market share to 12.9%. Chevrolet became the second-best-selling EV brand, pushing GM past Ford and Hyundai. Tesla, however, still retained a commanding 44.7% electric vehicle market share despite a 12% drop in in Q2 revenue, following a decline of almost 9% in Q1.
Incentives reached record highs in Q2, averaging 14.8% of transaction prices, roughly $8,500 per vehicle. As government support winds down, the used EV market is also gaining momentum, with over 100,000 used EVs sold in Q2.
Q2 2025 Kelley Blue Book EV Sales Report by Simon Alvarez on Scribd
-
News3 days ago
Tesla debuts hands-free Grok AI with update 2025.26: What you need to know
-
Elon Musk1 week ago
Elon Musk confirms Grok 4 launch on July 9 with livestream event
-
Elon Musk6 days ago
xAI launches Grok 4 with new $300/month SuperGrok Heavy subscription
-
News2 weeks ago
Tesla Model 3 ranks as the safest new car in Europe for 2025, per Euro NCAP tests
-
Elon Musk2 weeks ago
xAI’s Memphis data center receives air permit despite community criticism
-
News5 days ago
Tesla begins Robotaxi certification push in Arizona: report
-
Elon Musk2 weeks ago
Tesla reveals it is using AI to make factories more sustainable: here’s how
-
Elon Musk2 weeks ago
Tesla scrambles after Musk sidekick exit, CEO takes over sales