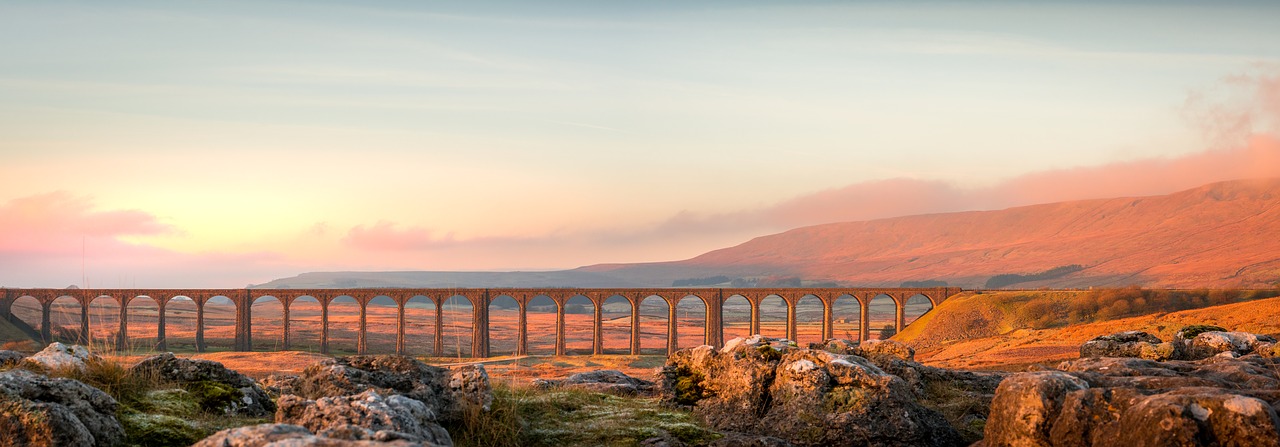
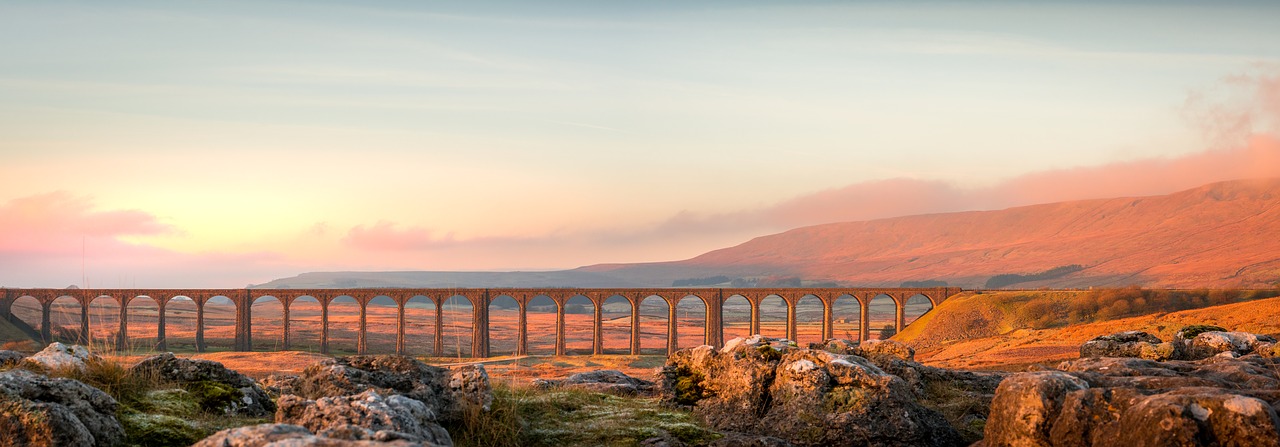
News
“Smart skin” can identify weaknesses in bridges and airplanes using laser scanner
Recent research results have demonstrated that two-dimensional, on-demand mapping of the accumulated strain on metal structures will soon be a reality thanks to an engineered “smart skin” that’s only a fraction of the width of a human hair. By utilizing the unique properties of single-walled carbon nanotubes, a two-layer film airbrushed onto surfaces of bridges, pipelines, and airplanes, among others, can be scanned to reveal weaknesses in near real-time. As a bonus, the technology is barely visible even on a transparent surface, making it that much more flexible as an application.
Stress-inducing events, along with regular wear and tear, can deform structures and machines, affecting their safety and operability. Mechanical strain on structural surfaces provides information on the condition of the materials such as damage location and severity. Existing conventional sensors are only able to measure strain in one point along one axis, but with the smart skin technology, strain detection in any direction or location will be possible.
How “Smart Skin” Technology is Used
In 2002, researchers discovered that single-wall carbon nanotubes fluoresce, i.e., glow brightly when stimulated by a light source. Later, the fluorescence was further found to change color when stretched. This optical property was then considered in the context of metal structures that are subject to strain, specifically to apply the property as a diagnostic tool. To obtain the fluorescent data, researchers applied the smart skin to a testing surface, irradiated the area with a small laser scanner, and captured the resulting nanotube color emissions with an infrared spectrometer. Finally, two-dimensional maps of the accumulated strain were generated with the results.
The primary researchers, Professors Satish Nagarajaiah and Bruce Weisman of Rice University in Texas, have published two scientific papers explaining the methods used for achieving this technology and the results of its proof-of-principle application. As described in the papers, aluminum bars with holes or notches in areas of potential stress were tested with the laser technique to demonstrate the full potential of their invention. The points measured were located 1 millimeter apart, but the researchers stated that the points could be located 20 times closer for even more accurate readings. Standard strain sensors have points located several millimeters apart.
What Are Carbon Nanotubes?
Carbon nanotubes (CNTs) are carbon molecules that have been structurally modified into cylinders, or rather, rolled up sheets of carbon atoms. There has been some evidence suggesting that CNTs can be formed via natural processes such as volcanic events. However, to really capitalize on their unique characteristics, production in a laboratory environment is much more efficient.
Several methods can be used for production, but the most widely used method for synthesizing CNTs is chemical vapor deposition (CVD). This process combines a catalyzing metal with a carbon-containing gas which are heated to approximately 1400 degrees Fahrenheit, triggering the carbon molecules to assemble and grow into nanotubes. The resulting formation resembles a forest or lawn grass, each trunk or blade averaging .43 nanometers in diameter. The length is dependent on variables such as the amount of time spent in the high heat environment.
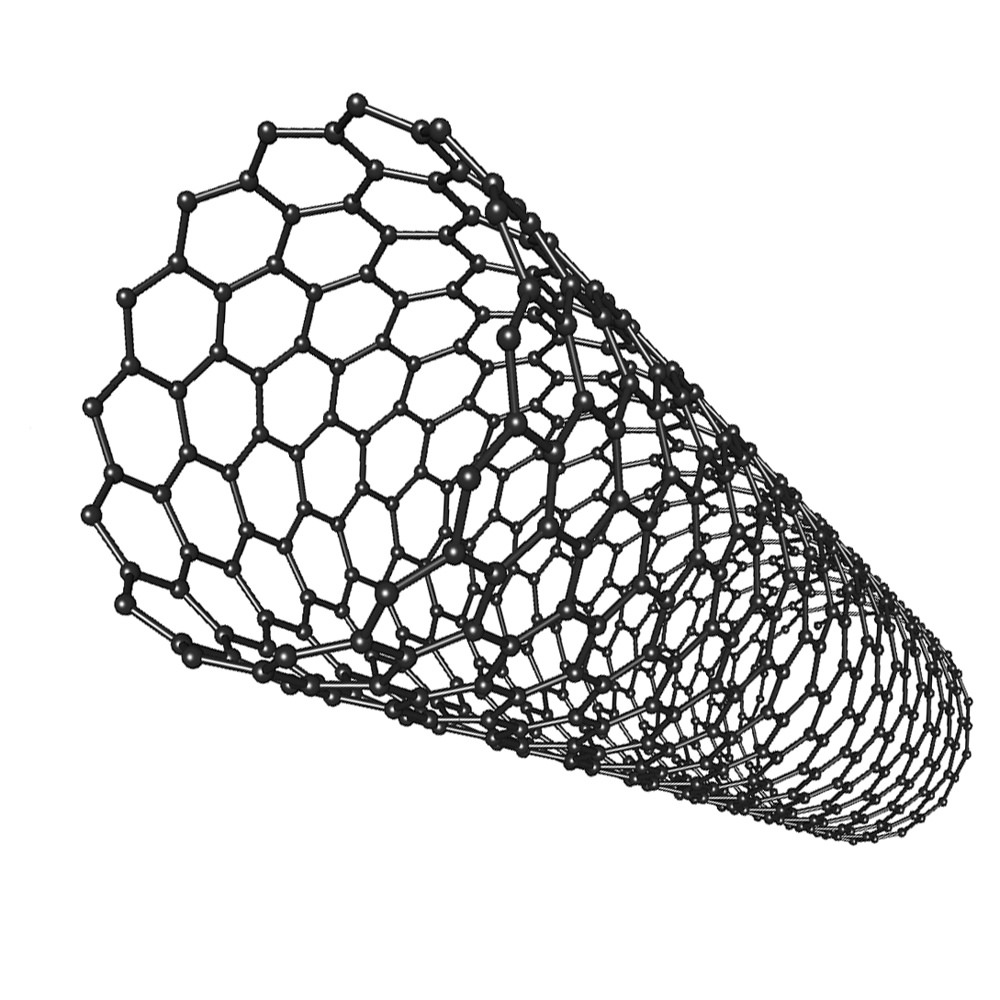
Besides surface analysis, carbon nanotubes have proven invaluable in many research and commercial arenas, their luminescence being only one of many properties that can improve and enable other technologies. Their mechanical tensile strength is 400 times that of steel while only having one sixth the density, making them very lightweight. CNTs also have highly conductive electrical and thermal properties, are extremely resistant to corrosion, and can be filled with other nanomaterials. All of these advantages open up their applications to include solar cells, sensors, drug delivery, electronic devices and shielding, lithium-ion batteries, body armor, and perhaps even a space elevator, assuming significant advances overcome its hurdles.
Next Steps
The nanotube-laced smart skin is ready for scaling up into real-world applications, but its chosen industry may take time to adopt given the general resistance to change in a field with long-standing existing technology. While awaiting embrace in the arena it was primarily designed for, the smart skin has other potential uses in engineering research applications. Bruce Weisman, also the discoverer of CNT fluorescence, anticipates its advantages being used for testing the design of small-scaled structures and engines prior to deployment. Niche applications like these may be the primary entry point into the market for some time to come. In the meantime, the researchers plan to continue developing their strain reader to capture simultaneous readings from large surfaces.
News
Tesla cleared in Canada EV rebate investigation
Tesla has been cleared in an investigation into the company’s staggering number of EV rebate claims in Canada in January.
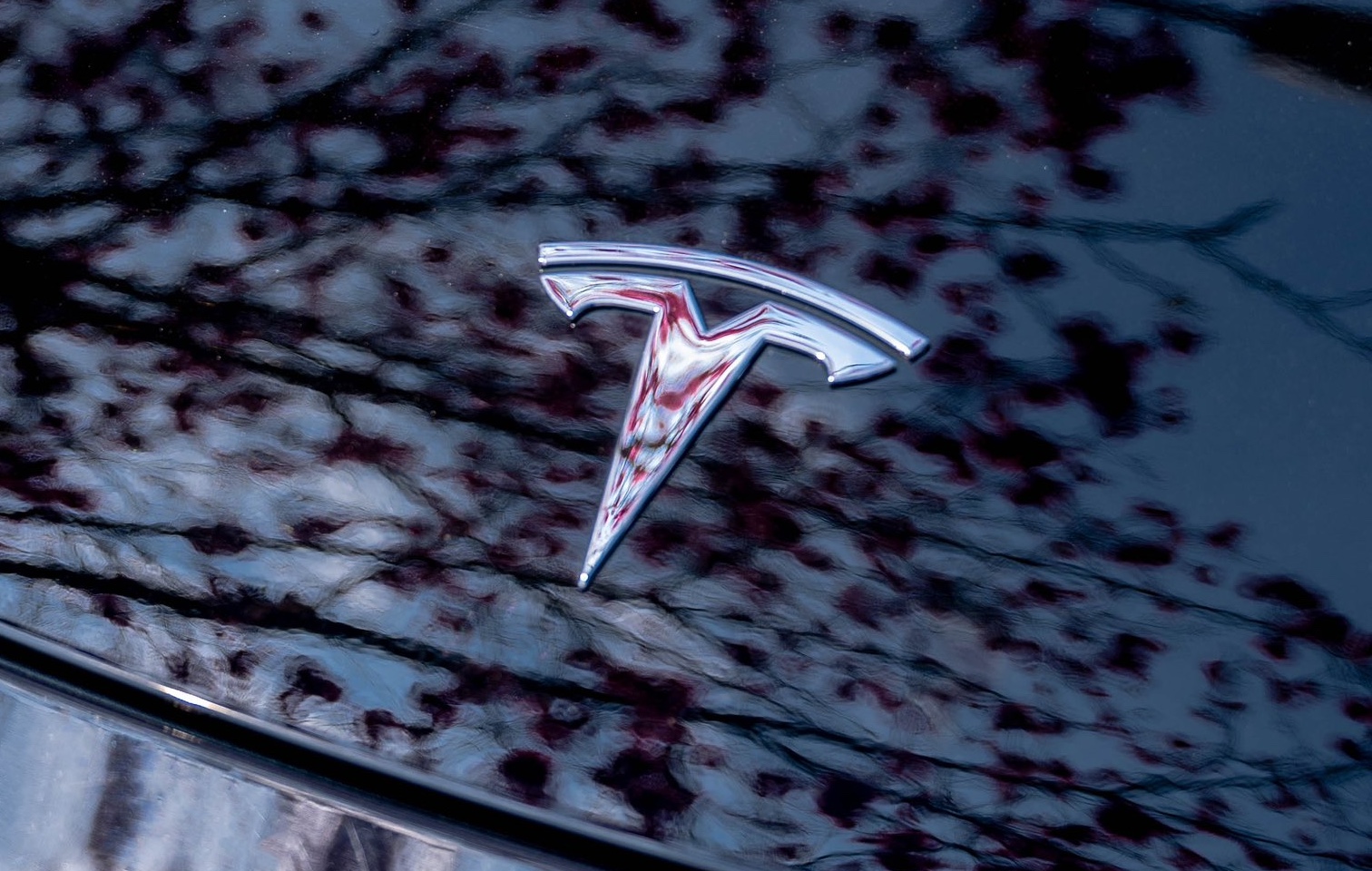
Canadian officials have cleared Tesla following an investigation into a large number of claims submitted to the country’s electric vehicle (EV) rebates earlier this year.
Transport Canada has ruled that there was no evidence of fraud after Tesla submitted 8,653 EV rebate claims for the country’s Incentives for Zero-Emission Vehicles (iZEV) program, as detailed in a report on Friday from The Globe and Mail. Despite the huge number of claims, Canadian authorities have found that the figure represented vehicles that had been delivered prior to the submission deadline for the program.
According to Transport Minister Chrystia Freeland, the claims “were determined to legitimately represent cars sold before January 12,” which was the final day for OEMs to submit these claims before the government suspended the program.
Upon initial reporting of the Tesla claims submitted in January, it was estimated that they were valued at around $43 million. In March, Freeland and Transport Canada opened the investigation into Tesla, noting that they would be freezing the rebate payments until the claims were found to be valid.
READ MORE ON ELECTRIC VEHICLES: EVs getting cleaner more quickly than expected in Europe: study
Huw Williams, Canadian Automobile Dealers Association Public Affairs Director, accepted the results of the investigation, while also questioning how Tesla knew to submit the claims that weekend, just before the program ran out.
“I think there’s a larger question as to how Tesla knew to run those through on that weekend,” Williams said. “It doesn’t appear to me that we have an investigation into any communication between Transport Canada and Tesla, between officials who may have shared information inappropriately.”
Tesla sales have been down in Canada for the first half of this year, amidst turmoil between the country and the Trump administration’s tariffs. Although Elon Musk has since stepped back from his role with the administration, a number of companies and officials in Canada were calling for a boycott of Tesla’s vehicles earlier this year, due in part to his association with Trump.
News
Tesla Semis to get 18 new Megachargers at this PepsiCo plant
PepsiCo is set to add more Tesla Semi Megachargers, this time at a facility in North Carolina.
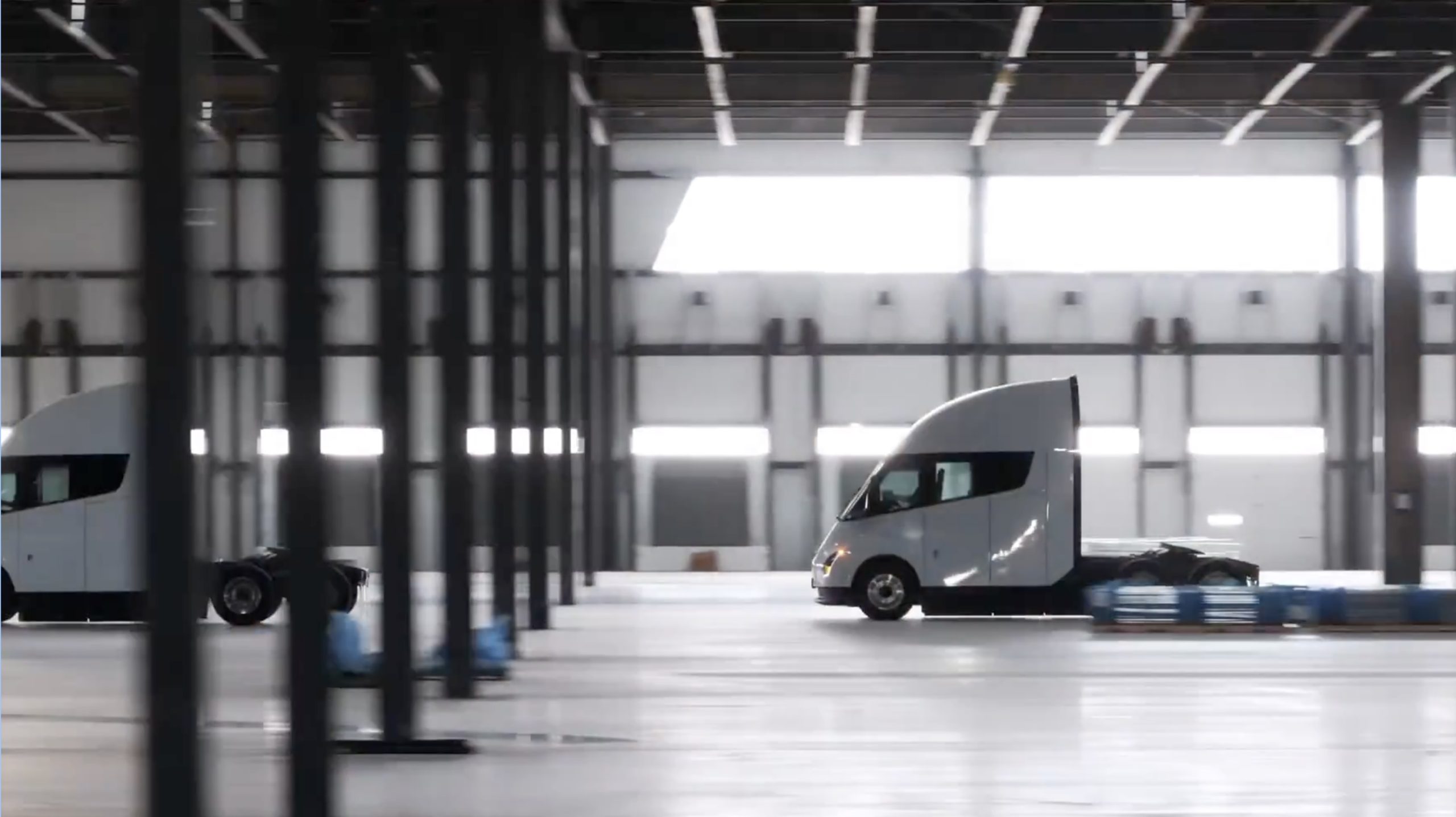
Tesla partner PepsiCo is set to build new Semi charging stations at one of its manufacturing sites, as revealed in new permitting plans shared this week.
On Friday, Tesla charging station scout MarcoRP shared plans on X for 18 Semi Megacharging stalls at PepsiCo’s facility in Charlotte, North Carolina, coming as the latest update plans for the company’s increasingly electrified fleet. The stalls are set to be built side by side, along with three Tesla Megapack grid-scale battery systems.
The plans also note the faster charging speeds for the chargers, which can charge the Class 8 Semi at speeds of up to 1MW. Tesla says that the speed can charge the Semi back to roughly 70 percent in around 30 minutes.
You can see the site plans for the PepsiCo North Carolina Megacharger below.
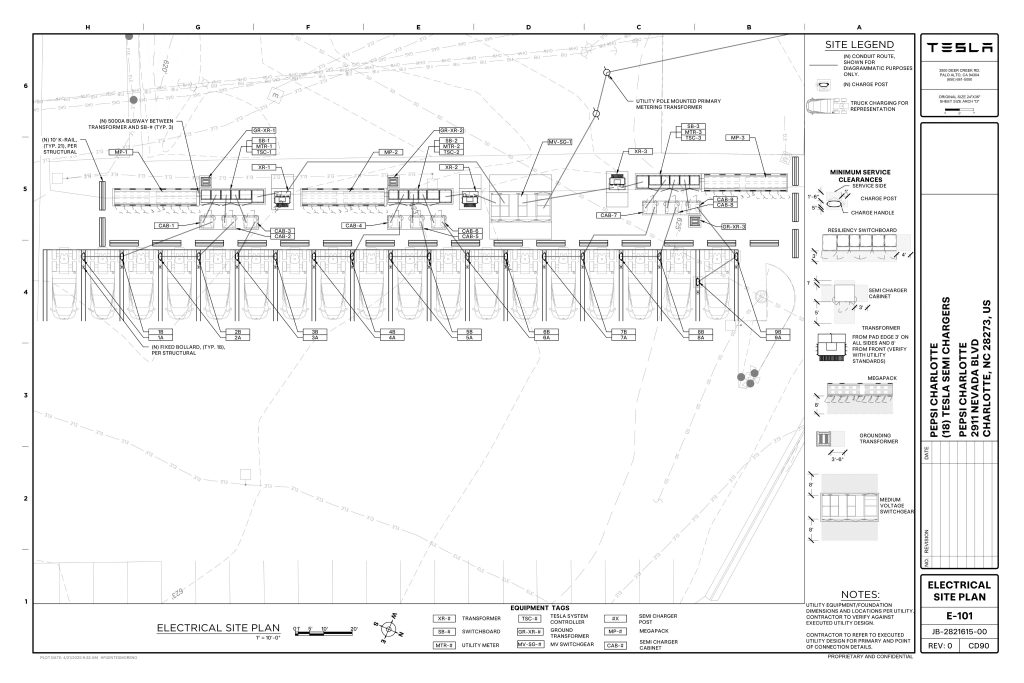
Credit: PepsiCo (via MarcoRPi1 on X)
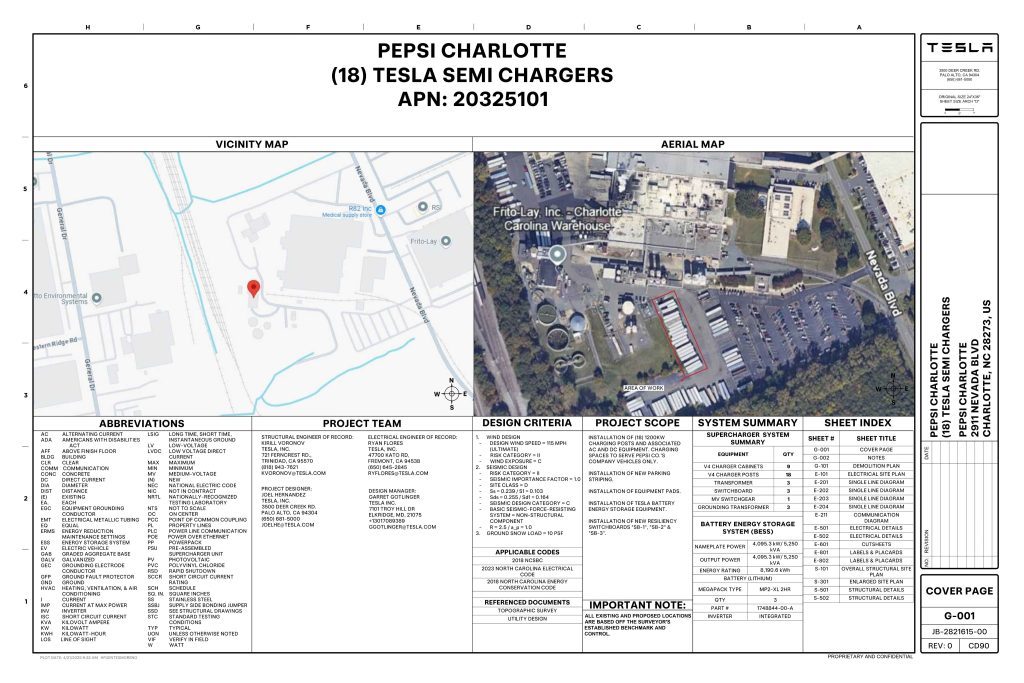
Credit: PepsiCo (via MarcoRPi1 on X)
READ MORE ON THE TESLA SEMI: Tesla to build Semi Megacharger station in Southern California
PepsiCo’s Tesla Semi fleet, other Megachargers, and initial tests and deliveries
PepsiCo was the first external customer to take delivery of Tesla’s Semis back in 2023, starting with just an initial order of 15. Since then, the company has continued to expand the fleet, recently taking delivery of an additional 50 units in California. The PepsiCo fleet was up to around 86 units as of last year, according to statements from Semi Senior Manager Dan Priestley.
Additionally, the company has similar Megachargers at its facilities in Modesto, Sacramento, and Fresno, California, and Tesla also submitted plans for approval to build 12 new Megacharging stalls in Los Angeles County.
Over the past couple of years, Tesla has also been delivering the electric Class 8 units to a number of other companies for pilot programs, and Priestley shared some results from PepsiCo’s initial Semi tests last year. Notably, the executive spoke with a handful of PepsiCo workers who said they really liked the Semi and wouldn’t plan on going back to diesel trucks.
The company is also nearing completion of a higher-volume Semi plant at its Gigafactory in Nevada, which is expected to eventually have an annual production capacity of 50,000 Semi units.
Tesla executive teases plan to further electrify supply chain
News
Tesla sales soar in Norway with new Model Y leading the charge
Tesla recorded a 54% year-over-year jump in new vehicle registrations in June.
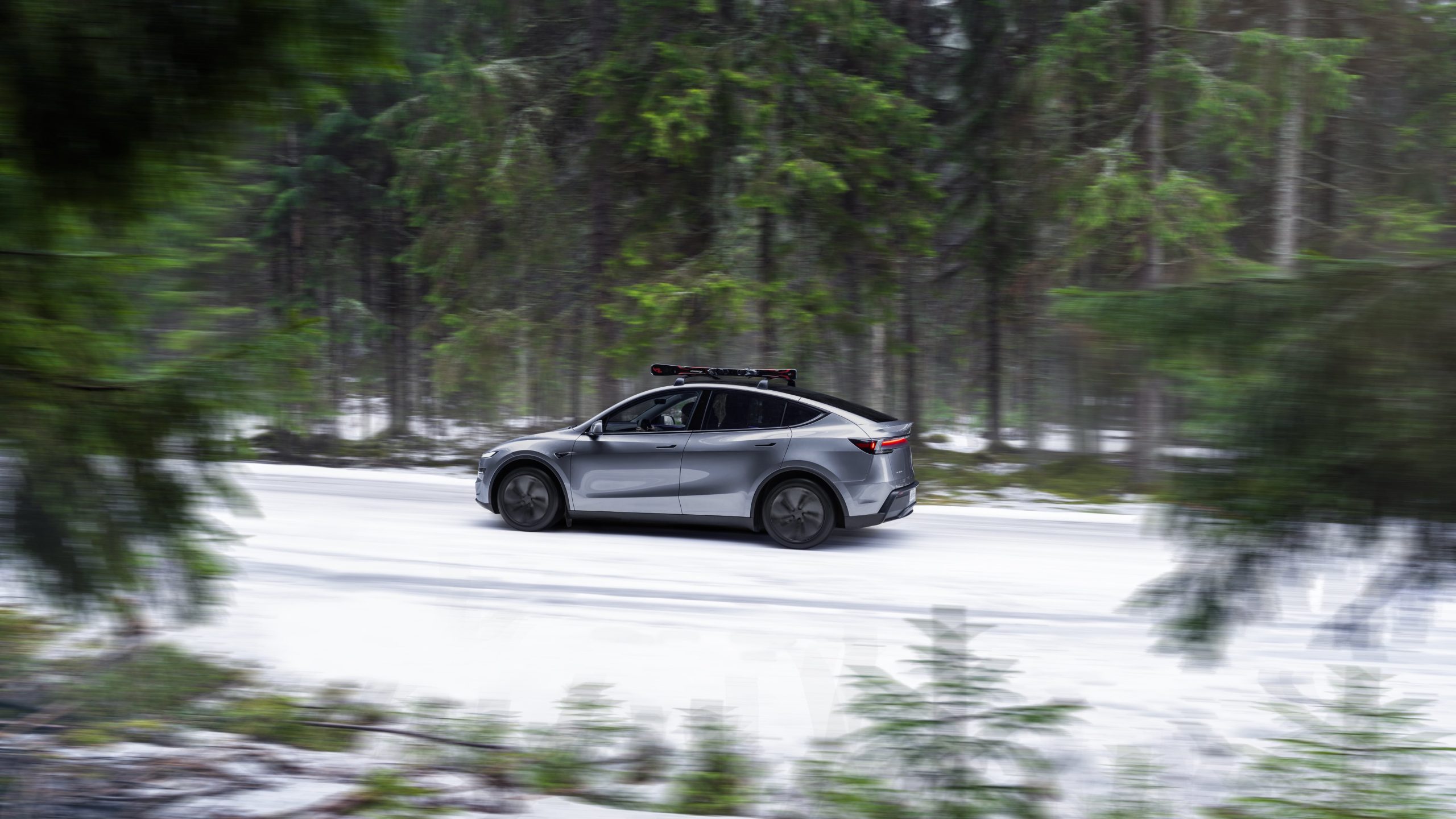
Tesla is seeing strong momentum in Norway, with sales of the new Model Y helping the company maintain dominance in one of the world’s most electric vehicle-friendly markets.
Model Y upgrades and consumer preferences
According to the Norwegian Road Federation (OFV), Tesla recorded a 54% year-over-year jump in new vehicle registrations in June. The Model Y led the charge, posting a 115% increase compared to the same period last year. Tesla Norway’s growth was even more notable in May, with sales surging a whopping 213%, as noted in a CNBC report.
Christina Bu, secretary general of the Norwegian EV Association (NEVA), stated that Tesla’s strong market performance was partly due to the updated Model Y, which is really just a good car, period.
“I think it just has to do with the fact that they deliver a car which has quite a lot of value for money and is what Norwegians need. What Norwegians need, a large luggage space, all wheel drive, and a tow hitch, high ground clearance as well. In addition, quite good digital solutions which people have gotten used to, and also a charging network,” she said.
Tesla in Europe
Tesla’s success in Norway is supported by long-standing government incentives for EV adoption, including exemptions from VAT, road toll discounts, and access to bus lanes. Public and home charging infrastructure is also widely available, making the EV ownership experience in the country very convenient.
Tesla’s performance in Europe is still a mixed bag, with markets like Germany and France still seeing declines in recent months. In areas such as Norway, Spain, and Portugal, however, Tesla’s new car registrations are rising. Spain’s sales rose 61% and Portugal’s sales rose 7% last month. This suggests that regional demand may be stabilizing or rebounding in pockets of Europe.
-
Elon Musk2 weeks ago
Tesla investors will be shocked by Jim Cramer’s latest assessment
-
Elon Musk2 days ago
xAI launches Grok 4 with new $300/month SuperGrok Heavy subscription
-
Elon Musk4 days ago
Elon Musk confirms Grok 4 launch on July 9 with livestream event
-
News1 week ago
Tesla Model 3 ranks as the safest new car in Europe for 2025, per Euro NCAP tests
-
Elon Musk2 weeks ago
A Tesla just delivered itself to a customer autonomously, Elon Musk confirms
-
Elon Musk1 week ago
xAI’s Memphis data center receives air permit despite community criticism
-
News2 weeks ago
Xiaomi CEO congratulates Tesla on first FSD delivery: “We have to continue learning!”
-
Investor's Corner2 weeks ago
Tesla gets $475 price target from Benchmark amid initial Robotaxi rollout