

News
Tesla Model Y rigid wiring is a step towards Elon Musk’s ‘Alien Dreadnought’ factory
The Tesla Model Y’s wiring seems to hint that little by little, the electric car maker is still moving towards a production line that is so automated, it is worthy of being dubbed an “Alien Dreadnought” factory. The most recent hint of this came in a video from auto teardown expert Sandy Munro, who is currently engaged in a thorough analysis and teardown of the Tesla Model Y.
Munro’s Model Y teardown has reached a point where the auto veteran is now looking into the all-electric crossover’s wiring system. Much to his pleasant surprise, Munro found that some of the Model Y’s wiring has become very different from those found in an early-production Model 3 he tore down and studied back in 2018. One of the key differences could be found in the wiring that connects the Model Y’s charge port to its battery pack.
As noted by Sandy Munro in his video, the heavy cables that connect the Model Y’s charge port to its battery pack are fitted inside a metal pipe. The auto veteran noted that this strategy has several advantages. By using a metal pipe, Tesla can ensure that the Model Y’s wiring is always a perfect fit during the vehicle’s assembly. The system also saves up space and weight compared to traditional cables, such as those found in the early-production Model 3.
This novel wiring system echoes a lot of the discussions in a previous Tesla patent published back in late 2018. In that particular patent, Tesla discussed how flexible wires are not optimized for production processes that are heavily reliant on automated machinery. Tesla’s patent then suggested the use of rigid cables, which could be easily picked up and installed by machines with very little margin or error. Interestingly enough, the Model Y’s wiring system that Munro recently discovered seemed to be quite similar to the structural cabling design that Tesla described in its patent.
The fact that the Model Y’s wiring seems to be optimized for automated production lines bodes well for Tesla. Elon Musk has always envisioned that Tesla factories will eventually run with minimal human staff, as robots would dominate the manufacturing line. Prior to the Model 3 ramp, for one, Musk described his vision for a factory that was so automated, Tesla’s internal name for it was the “Alien Dreadnought,” a reference to the hyper-advanced extraterrestrial ships in science fiction.
The pursuit for the Alien Dreadnought factory eventually had to take a step back during the Model 3 ramp, after the vehicle’s hyper-automated lines ended up performing less effectively than a production line that employs both humans and machines. Elon Musk, for his part, later admitted that he overreached with the Model 3’s automation. The CEO even remarked later that ultimately, he learned that “humans are underrated.”
If Munro’s discoveries on the Model Y’s wiring are any indication, it appears that Tesla is still making a lot of headway in optimizing its vehicles for automated production and assembly. The Model Y’s rigid wiring may be a simple change from the Model 3, but it goes a long way in proving that little by little, Tesla is still focused on improving its vehicles, from one iteration to the next.
Watch Sandy Munro’s latest feature on the Tesla Model Y in the video below.
News
Tesla UK sales see 14% year-over-year rebound in June: SMMT data
The SMMT stated that Tesla sales grew 14% year-over-year to 7,719 units in June 2025.
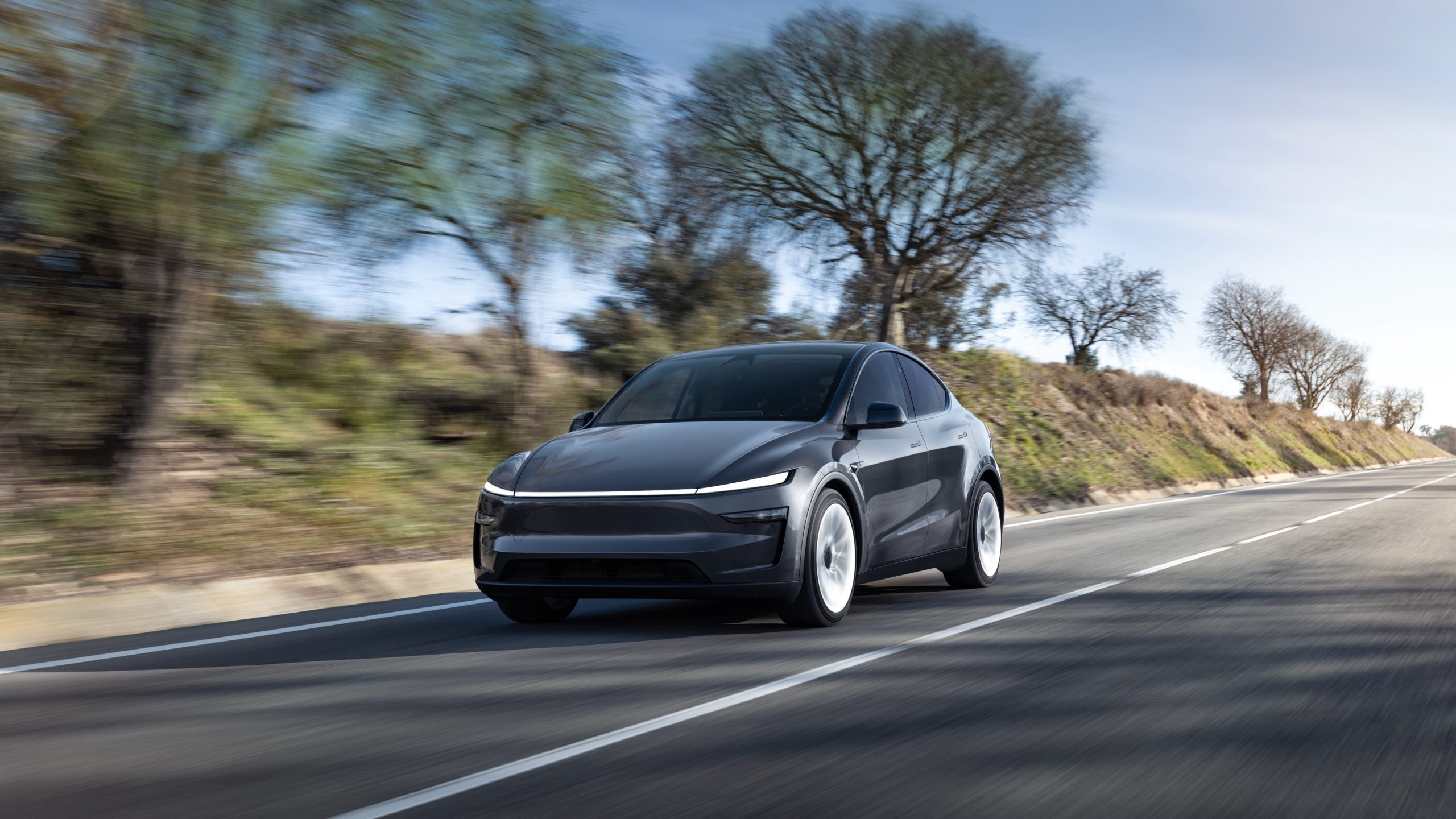
Tesla’s sales in the United Kingdom rose in June, climbing 14% year-over-year to 7,719 units, as per data from the Society of Motor Manufacturers and Traders (SMMT). The spike in the company’s sales coincided with the first deliveries of the updated Model Y last month.
Model Y deliveries support Tesla’s UK recovery
Tesla’s June performance marked one of its strongest months in the UK so far this year, with new Model Y deliveries contributing significantly to the company’s momentum.
While the SMMT listed Tesla with 7,719 deliveries in June, independent data from New AutoMotive suggested that the electric vehicle maker registered 7,891 units during the month instead. However, year-to-date figures for Tesla remain 2% down compared to 2024, as per a report from Reuters.
While Tesla made a strong showing in June, rivals are also growing. Chinese automaker BYD saw UK sales rise nearly fourfold to 2,498 units, while Ford posted the highest EV growth among major automakers, with a more than fourfold increase in the first half of 2025.
Overall, the UK’s battery electric vehicle (BEV) demand surged 39% to to 47,354 units last month, helping push total new car sales in the UK to 191,316 units, up 6.7% from the same period in 2024.
EV adoption accelerates, but concerns linger
June marked the best month for UK car sales since 2019, though the SMMT cautioned that growth in the electric vehicle sector remains heavily dependent on discounting and support programs. Still, one in four new vehicle buyers in June chose a battery electric vehicle.
SMMT Chief Executive Mike Hawes noted that despite strong BEV demand, sales levels are still below regulatory targets. “Further growth in sales, and the sector will rely on increased and improved charging facilities to boost mainstream electric vehicle adoption,” Hawes stated.
Also taking effect this week was a new US-UK trade deal, which lowers tariffs on UK car exports to the United States from 27.5% to 10%. The agreement could benefit UK-based EV producers aiming to expand across the country.
News
Tesla Model 3 ranks as the safest new car in Europe for 2025, per Euro NCAP tests
Despite being on the market longer than many of its rivals, the Tesla Model 3 continues to set the bar for vehicle safety.
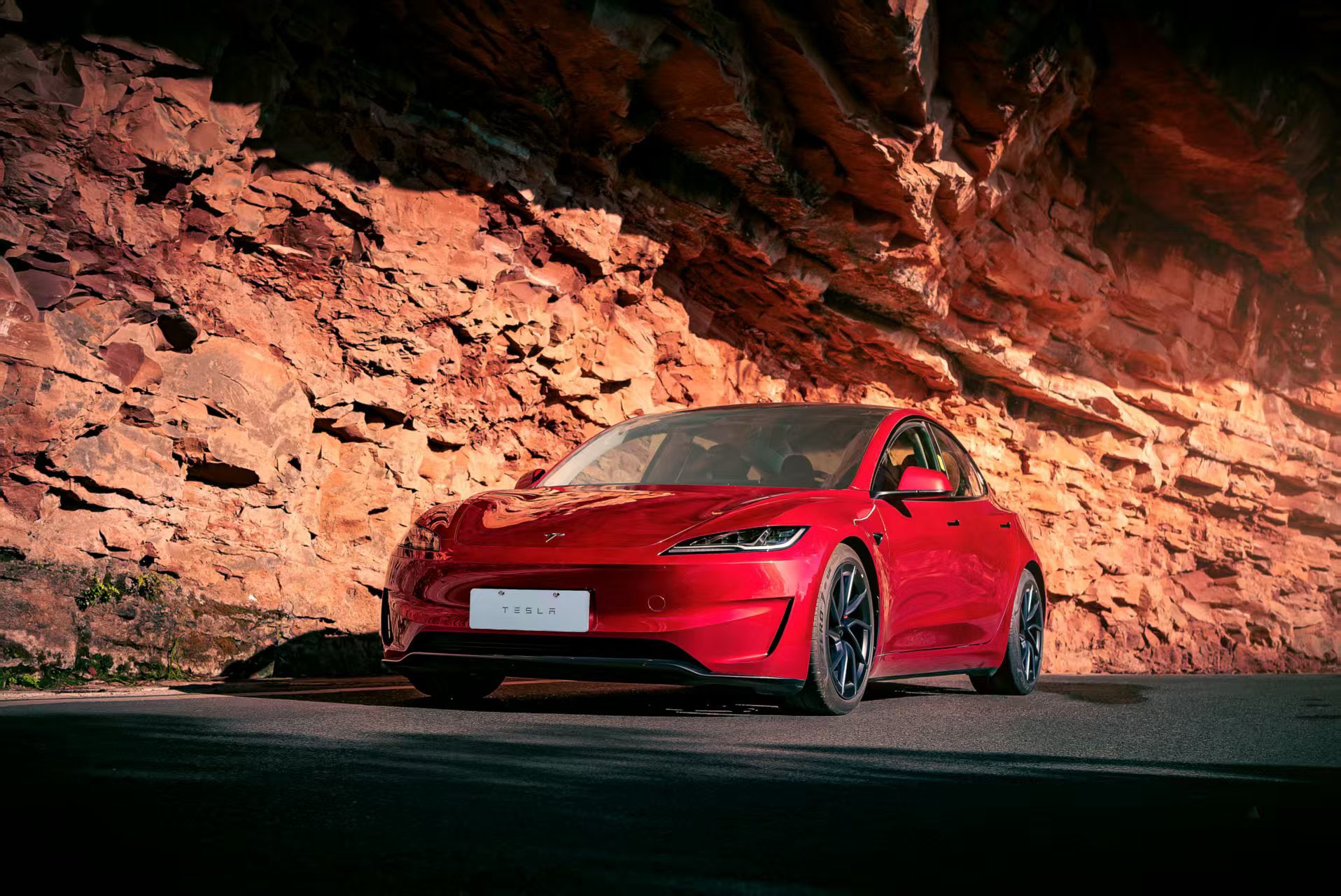
The Tesla Model 3 has been named the safest new car on sale in 2025, according to the latest results from the Euro NCAP. Among 20 newly tested vehicles, the Model 3 emerged at the top of the list, scoring an impressive 359 out of 400 possible points across all major safety categories.
Tesla Model 3’s safety systems
Despite being on the market longer than many of its rivals, the Tesla Model 3 continues to set the bar for vehicle safety. Under Euro NCAP’s stricter 2025 testing protocols, the electric sedan earned 90% for adult occupant protection, 93% for child occupant protection, 89% for pedestrian protection, and 87% for its Safety Assist systems.
The updated Model 3 received particular praise for its advanced driver assistance features, including Tesla’s autonomous emergency braking (AEB) system, which performed well across various test scenarios. Its Intelligent Speed Assistance and child presence detection system were cited as noteworthy features as well, as per a WhatCar report.
Other notable safety features include the Model 3’s pedestrian-friendly pop-up hood and robust crash protection for both front and side collisions. Euro NCAP also highlighted the Model 3’s ability to detect vulnerable road users during complex maneuvers, such as turning across oncoming traffic.
Euro NCAP’s Autopilot caution
While the Model 3’s safety scores were impressive across the board, Euro NCAP did raise concerns about driver expectations of Tesla’s Autopilot system. The organization warned that some owners may overestimate the system’s capabilities, potentially leading to misuse or inattention behind the wheel. Even so, the Model 3 remained the highest-scoring vehicle tested under Euro NCAP’s updated criteria this year.
The Euro NCAP’s concerns are also quite interesting because Tesla’s Full Self-Driving (FSD) Supervised, which is arguably the company’s most robust safety suite, is not allowed for public rollout in Europe yet. FSD Supervised would allow the Model 3 to navigate inner city streets with only minimal human supervision.
Other top scorers included the Volkswagen ID.7, Polestar 3, and Geely EX5, but none matched the Model 3’s total score or consistency across categories. A total of 14 out of 20 newly tested cars earned five stars, while several models, including the Kia EV3, MG ZS, and Renault 5, fell short of the top rating.
Elon Musk
Why Tesla’s Q3 could be one of its biggest quarters in history
Tesla could stand to benefit from the removal of the $7,500 EV tax credit at the end of Q3.
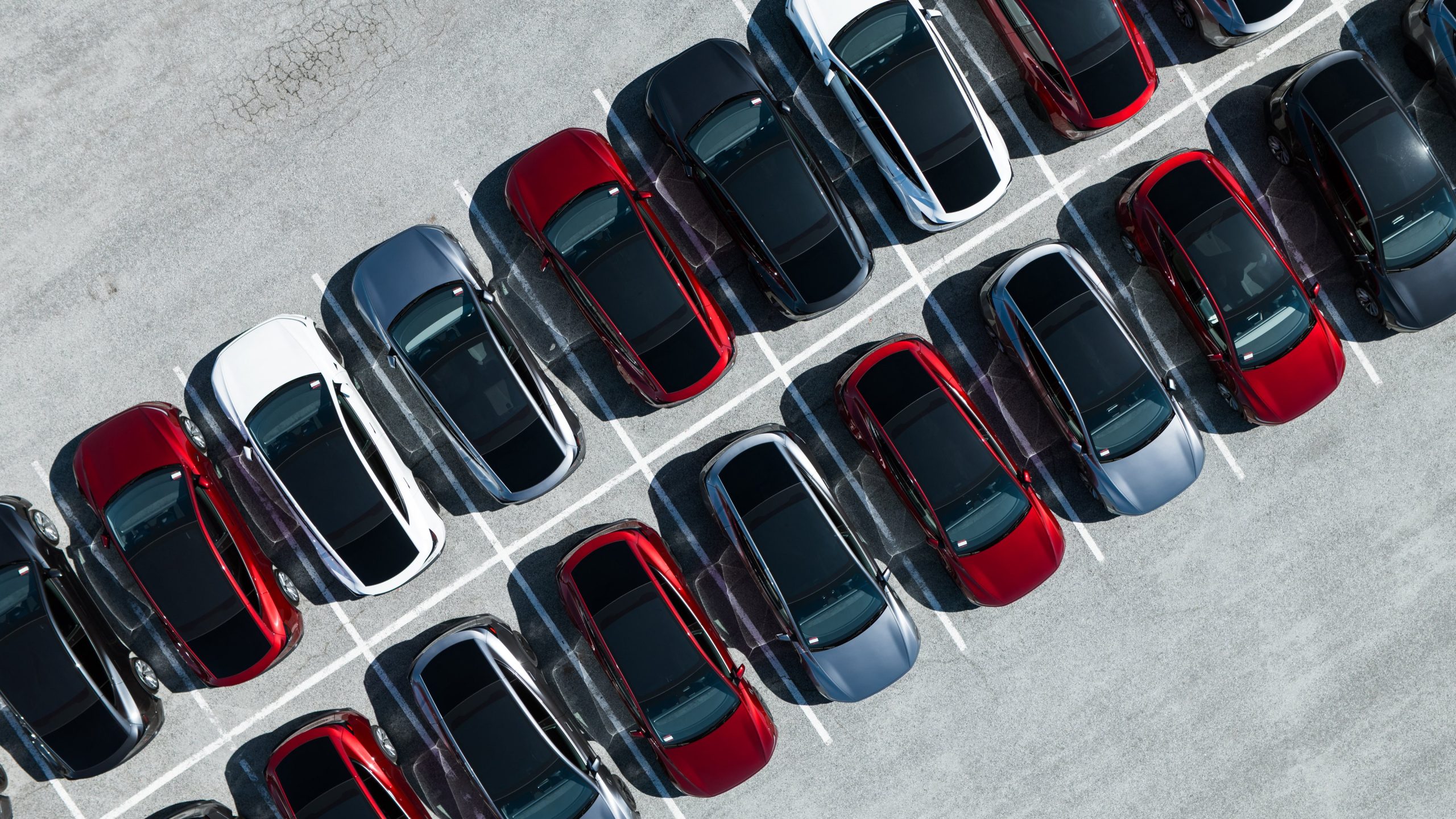
Tesla has gotten off to a slow start in 2025, as the first half of the year has not been one to remember from a delivery perspective.
However, Q3 could end up being one of the best the company has had in history, with the United States potentially being a major contributor to what might reverse a slow start to the year.
Earlier today, the United States’ House of Representatives officially passed President Trump’s “Big Beautiful Bill,” after it made its way through the Senate earlier this week. The bill will head to President Trump, as he looks to sign it before his July 4 deadline.
The Bill will effectively bring closure to the $7,500 EV tax credit, which will end on September 30, 2025. This means, over the next three months in the United States, those who are looking to buy an EV will have their last chance to take advantage of the credit. EVs will then be, for most people, $7,500 more expensive, in essence.
The tax credit is available to any single filer who makes under $150,000 per year, $225,000 a year to a head of household, and $300,000 to couples filing jointly.
Ending the tax credit was expected with the Trump administration, as his policies have leaned significantly toward reliance on fossil fuels, ending what he calls an “EV mandate.” He has used this phrase several times in disagreements with Tesla CEO Elon Musk.
Nevertheless, those who have been on the fence about buying a Tesla, or any EV, for that matter, will have some decisions to make in the next three months. While all companies will stand to benefit from this time crunch, Tesla could be the true winner because of its sheer volume.
If things are done correctly, meaning if Tesla can also offer incentives like 0% APR, special pricing on leasing or financing, or other advantages (like free Red, White, and Blue for a short period of time in celebration of Independence Day), it could see some real volume in sales this quarter.
You can now buy a Tesla in Red, White, and Blue for free until July 14 https://t.co/iAwhaRFOH0
— TESLARATI (@Teslarati) July 3, 2025
Tesla is just a shade under 721,000 deliveries for the year, so it’s on pace for roughly 1.4 million for 2025. This would be a decrease from the 1.8 million cars it delivered in each of the last two years. Traditionally, the second half of the year has produced Tesla’s strongest quarters. Its top three quarters in terms of deliveries are Q4 2024 with 495,570 vehicles, Q4 2023 with 484,507 vehicles, and Q3 2024 with 462,890 vehicles.
-
Elon Musk4 days ago
Tesla investors will be shocked by Jim Cramer’s latest assessment
-
News1 week ago
Tesla Robotaxi’s biggest challenge seems to be this one thing
-
Elon Musk2 weeks ago
First Look at Tesla’s Robotaxi App: features, design, and more
-
News2 weeks ago
SpaceX and Elon Musk share insights on Starship Ship 36’s RUD
-
News2 weeks ago
Watch Tesla’s first driverless public Robotaxi rides in Texas
-
News1 week ago
Watch the first true Tesla Robotaxi intervention by safety monitor
-
News2 weeks ago
Tesla has started rolling out initial round of Robotaxi invites
-
Elon Musk2 weeks ago
Tesla to launch in India in July with vehicles already arriving: report