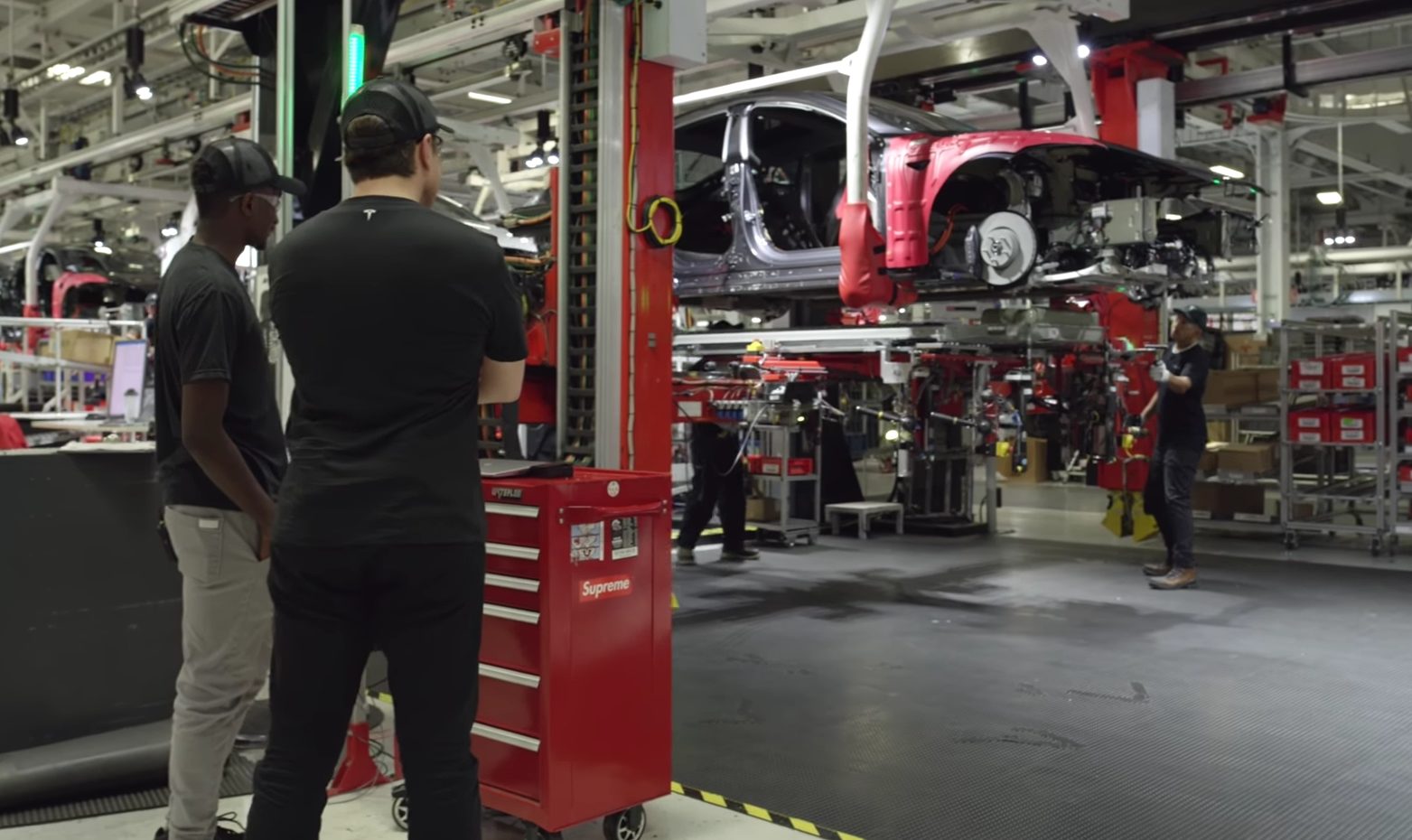
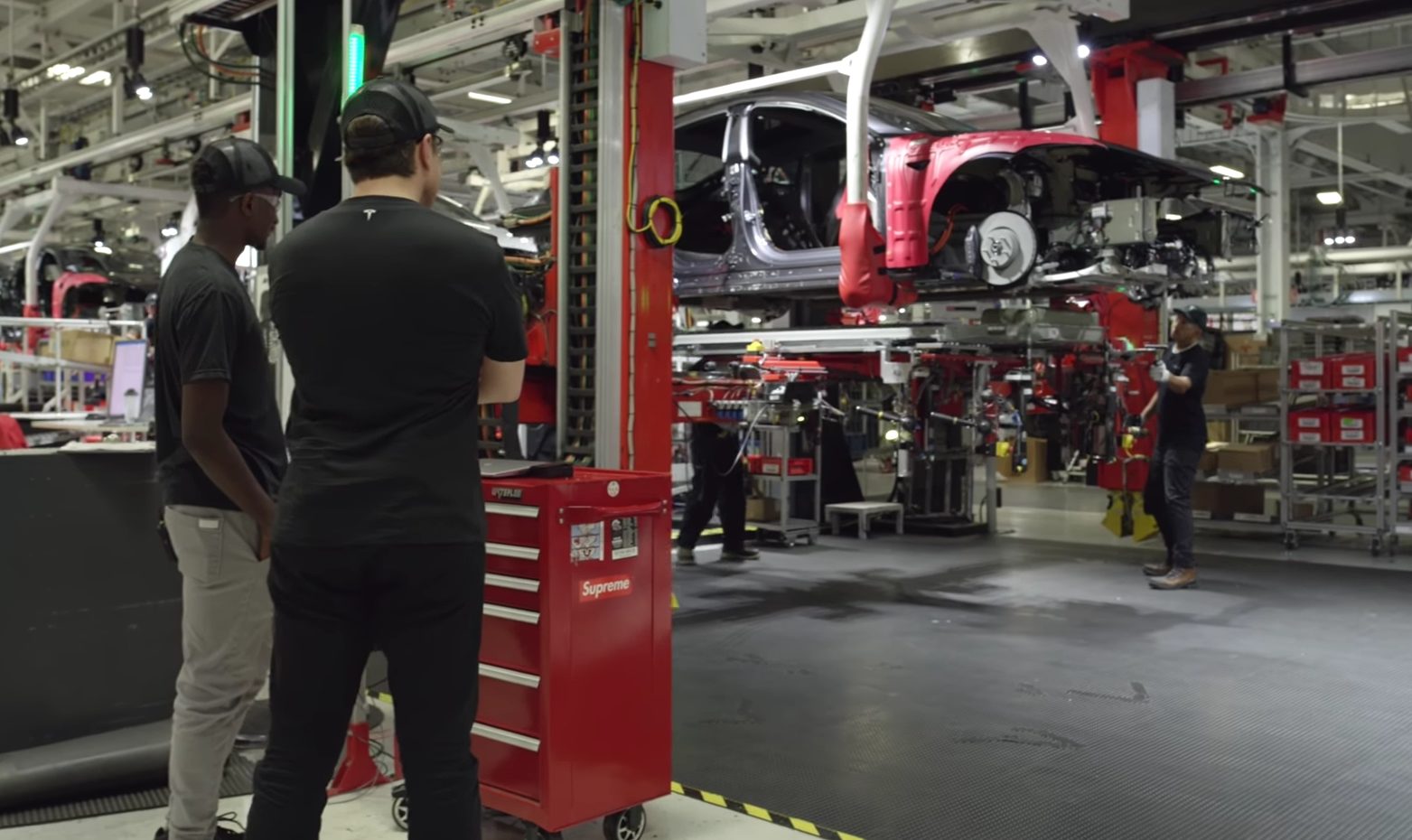
Investor's Corner
Tesla patents AR-based system for faster, more accurate vehicle production
Being a company led by an unorthodox CEO with roots in Silicon Valley, Tesla is on the bleeding edge of the automotive market. Tech is evident in Tesla’s DNA, from the automation in its factories to the deep integration of software on its electric vehicles. If a recently published patent is any indication, even more tech-driven solutions are coming to Tesla’s production lines.
A recent patent, dubbed as “Augmented Reality Application for Manufacturing,” was published last Thursday. In the description of the patent, Tesla noted that existing automotive manufacturing techniques are time-consuming and still require a notable amount of manual calibration and inspection. An example of this is the practice of marking joints and/or inspecting dimensional accuracy of car components by having workers manually overlay plastic molds over a sheet metal object to mark certain parts. These processes take a lot of time and effort, resulting in extra operational costs.
Tesla’s solution is rather simple. Instead of using manual processes to perform tasks that include setup, configuration, calibration, and quality inspection, it would be better to utilize available technologies to make operations faster and more precise. One of these technologies is computer vision and augmented reality tools.
Tesla’s patent uses AR applications and computer vision to “identify an object of interest and the relationship between a user and the object.” The AR device captures a live view of an object, determines the location of the device, as well as the type of the object of interest. By using this system, workers will be able to view instant data about the components they are working on.
“(For example), the AR device identifies that the object of interest is a right-hand front shock tower of a vehicle. The AR device then overlays data corresponding to features of the object of interest, such as mechanical joints, interfaces with other parts, thickness of e-coating, etc. on top of the view of the object of interest. Examples of the joint features include spot welds, self-pierced rivets, laser welds, structural adhesive, and sealers, among others.
“As the user moves around the object, the view of the object from the perspective of the AR device and the overlaid data of the detected features adjust accordingly. The user can also interact with the AR device. For example, a user can display information on each of the identified features. In some embodiments, for example, the AR device displays the tolerances associated with each detected feature, such as the location of a spot weld or hole.”
Apart from allowing production to move faster, the AR-based system could also be used for quality inspections. Tesla even noted that such a system could be tapped to determine if panels in vehicles are within tolerances, and if holes in the electric cars’ frames are drilled or punched at the correct location.
- An illustration of Tesla’s AR-augmented production system. [Credit: US Patent Office]
- An illustration of Tesla’s AR-augmented production system. [Credit: US Patent Office]
An illustration of Tesla’s AR-augmented production system. [Credit: US Patent Office]
“There are many practical applications for the augmented reality (AR) manufacturing techniques discussed herein. In some embodiments, the AR device is used to program a robot to assemble one or more parts including identifying and marking the precise location and order of welds, self-pierced rivets, laser welds, adhesives, sealers, holes, fasteners, or other mechanical joints, etc. As another example, the AR device can be used to inspect the quality of the assembly for a vehicle such as whether the locations of welds are correct, whether the interfaces between parts such as body panels are within tolerances, whether holes are drilled or punched at the correct location, whether the fit and finish of assembly is correct, etc.
“In some embodiments, vision recognition is utilized. Individual sheet metal components and/or assemblies that are or will be part of the body-in-white (also known as the structural frame or body) are recognized. Once the component/system has been identified, computer-aided design (CAD) information (e.g., information and/or symbols associated with the mechanical joints) is aligned/scaled and rendered on corresponding identified physical model components. The application of the disclosed techniques applies to many different contexts of manufacturing.
“For example, the AR device can be used to map the quality of a coating on an automotive part such as determining the thickness of an e-coating on a vehicle body and identifying problem areas that are difficult to coat. In some embodiments, the AR device is used to map out a factory floor and to identify the precise location and orientation robots should be installed at to build out an assembly line. The robots are positioned based on the AR device such that the installed robots will not interfere with each other or other obstructions in the environment.”
An AR-based system that augments production fits very well with Tesla’s reputation as a car maker that never stays stagnant. During an interview at Gigafactory 1, Tesla President of Automotive Jerome Guillen mentioned that the company’s battery cells — while already industry-leading — are always evolving. Elon Musk echoed this idea as well, when he noted that improvements to Tesla’s electric cars are being rolled out as soon as they are ready. Optimizations such as the use of AR and computer vision in the production line is yet another example.
Investor's Corner
Tesla could save $2.5B by replacing 10% of staff with Optimus: Morgan Stanley
Jonas assigned each robot a net present value (NPV) of $200,000.
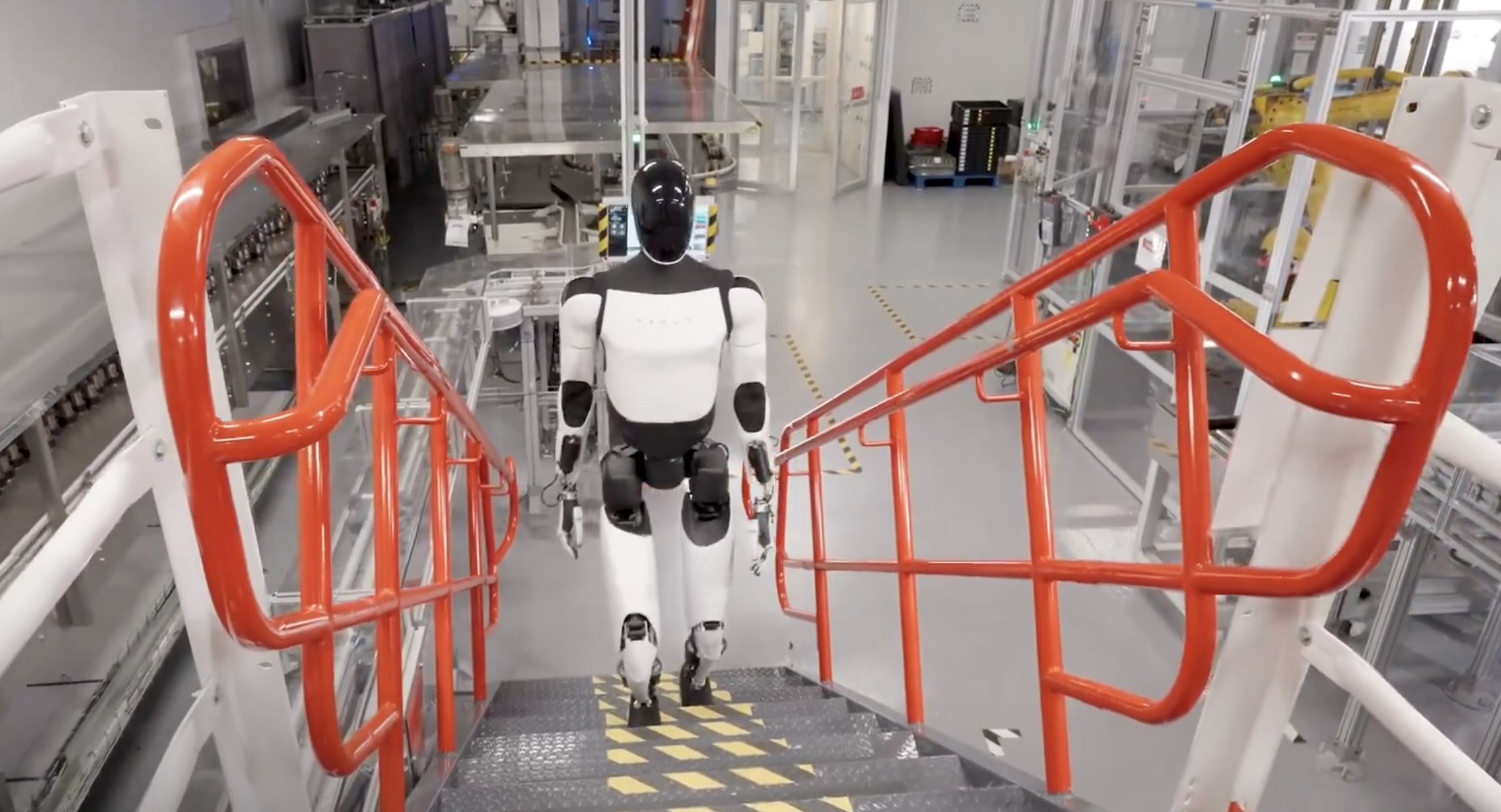
Tesla’s (NASDAQ:TSLA) near-term outlook may be clouded by political controversies and regulatory headwinds, but Morgan Stanley analyst Adam Jonas sees a glimmer of opportunity for the electric vehicle maker.
In a new note, the Morgan Stanley analyst estimated that Tesla could save $2.5 billion by replacing just 10% of its workforce with its Optimus robots, assigning each robot a net present value (NPV) of $200,000.
Morgan Stanley highlights Optimus’ savings potential
Jonas highlighted the potential savings on Tesla’s workforce of 125,665 employees in his note, suggesting that the utilization of Optimus robots could significantly reduce labor costs. The analyst’s note arrived shortly after Tesla reported Q2 2025 deliveries of 384,122 vehicles, which came close to Morgan Stanley’s estimate and slightly under the consensus of 385,086.
“Tesla has 125,665 employees worldwide (year-end 2024). On our calculations, a 10% substitution to humanoid at approximately ($200k NPV/humanoid) could be worth approximately $2.5bn,” Jonas wrote, as noted by Street Insider.
Jonas also issued some caution on Tesla Energy, whose battery storage deployments were flat year over year at 9.6 GWh. Morgan Stanley had expected Tesla Energy to post battery storage deployments of 14 GWh in the second quarter.
Musk’s political ambitions
The backdrop to Jonas’ note included Elon Musk’s involvement in U.S. politics. The Tesla CEO recently floated the idea of launching a new political party, following a poll on X that showed support for the idea. Though a widely circulated FEC filing was labeled false by Musk, the CEO does seem intent on establishing a third political party in the United States.
Jonas cautioned that Musk’s political efforts could divert attention and resources from Tesla’s core operations, adding near-term pressure on TSLA stock. “We believe investors should be prepared for further devotion of resources (financial, time/attention) in the direction of Mr. Musk’s political priorities which may add further near-term pressure to TSLA shares,” Jonas stated.
Investor's Corner
Two Tesla bulls share differing insights on Elon Musk, the Board, and politics
Two noted Tesla bulls have shared differing views on the recent activities of CEO Elon Musk and the company’s leadership.
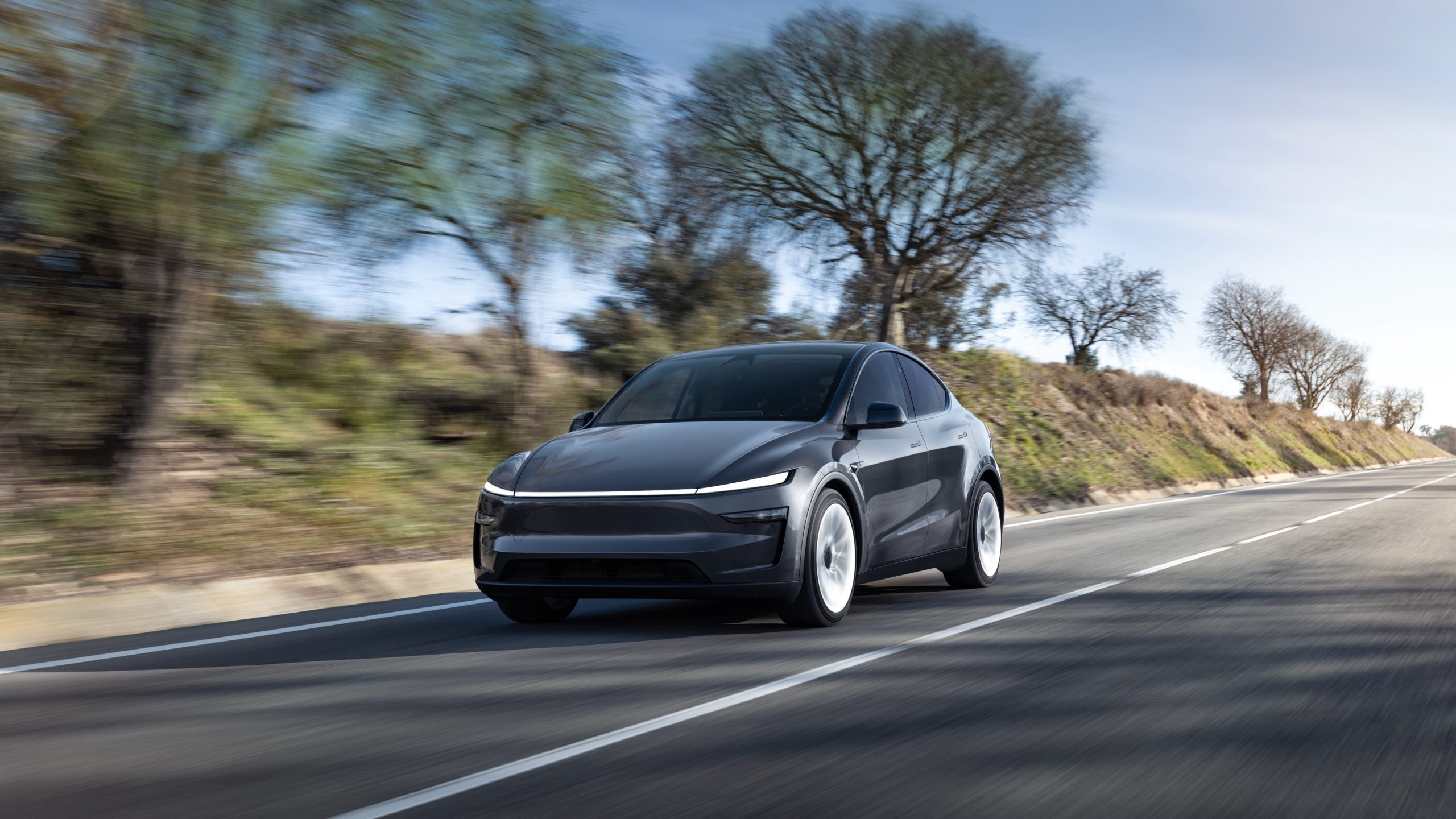
Two noted Tesla (NASDAQ:TSLA) bulls have shared differing views on the recent activities of CEO Elon Musk and the company’s leadership.
While Wedbush analyst Dan Ives called on Tesla’s board to take concrete steps to ensure Musk remains focused on the EV maker, longtime Tesla supporter Cathie Wood of Ark Invest reaffirmed her confidence in the CEO and the company’s leadership.
Ives warns of distraction risk amid crucial growth phase
In a recent note, Ives stated that Tesla is at a critical point in its history, as the company is transitioning from an EV maker towards an entity that is more focused on autonomous driving and robotics. He then noted that the Board of Directors should “act now” and establish formal boundaries around Musk’s political activities, which could be a headwind on TSLA stock.
Ives laid out a three-point plan that he believes could ensure that the electric vehicle maker is led with proper leadership until the end of the decade. First off, the analyst noted that a new “incentive-driven pay package for Musk as CEO that increases his ownership of Tesla up to ~25% voting power” is necessary. He also stated that the Board should establish clear guidelines for how much time Musk must devote to Tesla operations in order to receive his compensation, and a dedicated oversight committee must be formed to monitor the CEO’s political activities.
Ives, however, highlighted that Tesla should move forward with Musk at its helm. “We urge the Board to act now and move the Tesla story forward with Musk as CEO,” he wrote, reiterating its Outperform rating on Tesla stock and $500 per share price target.
Tesla CEO Elon Musk has responded to Ives’ suggestions with a brief comment on X. “Shut up, Dan,” Musk wrote.
Cathie Wood reiterates trust in Musk and Tesla board
Meanwhile, Ark Investment Management founder Cathie Wood expressed little concern over Musk’s latest controversies. In an interview with Bloomberg Television, Wood said, “We do trust the board and the board’s instincts here and we stay out of politics.” She also noted that Ark has navigated Musk-related headlines since it first invested in Tesla.
Wood also pointed to Musk’s recent move to oversee Tesla’s sales operations in the U.S. and Europe as evidence of his renewed focus in the electric vehicle maker. “When he puts his mind on something, he usually gets the job done,” she said. “So I think he’s much less distracted now than he was, let’s say, in the White House 24/7,” she said.
TSLA stock is down roughly 25% year-to-date but has gained about 19% over the past 12 months, as noted in a StocksTwits report.
Investor's Corner
Cantor Fitzgerald maintains Tesla (TSLA) ‘Overweight’ rating amid Q2 2025 deliveries
Cantor Fitzgerald is holding firm on its bullish stance for the electric vehicle maker.
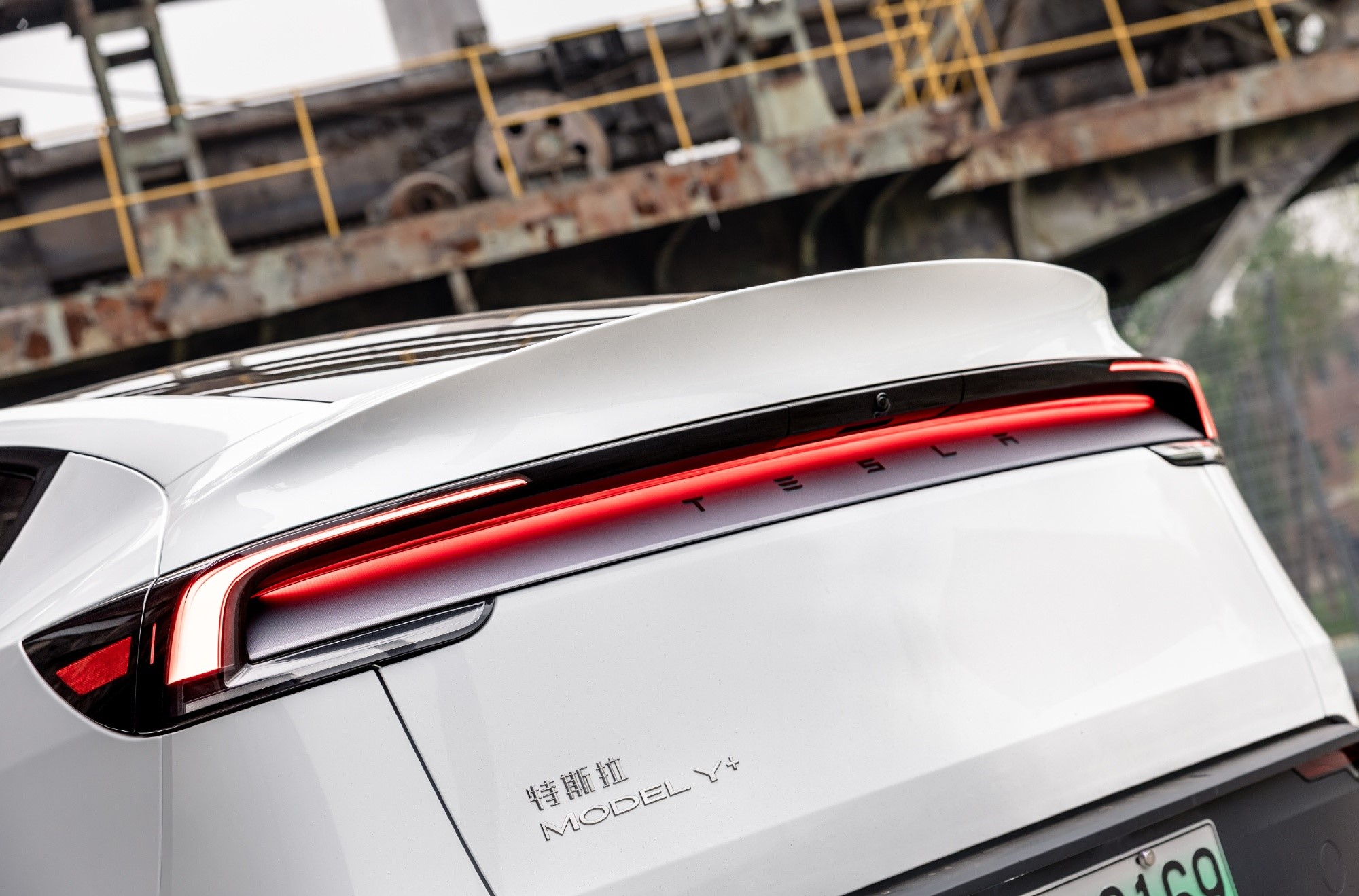
Cantor Fitzgerald is holding firm on its bullish stance for Tesla (NASDAQ: TSLA), reiterating its “Overweight” rating and $355 price target amidst the company’s release of its Q2 2025 vehicle delivery and production report.
Tesla delivered 384,122 vehicles in Q2 2025, falling below last year’s Q2 figure of 443,956 units. Despite softer demand in some countries in Europe and ongoing controversies surrounding CEO Elon Musk, the firm maintained its view that Tesla is a long-term growth story in the EV sector.
Tesla’s Q2 results
Among the 384,122 vehicles that Tesla delivered in the second quarter, 373,728 were Model 3 and Model Y. The remaining 10,394 units were attributed to the Model S, Model X, and Cybertruck. Production was largely flat year-over-year at 410,244 units.
In the energy division, Tesla deployed 9.6 GWh of energy storage in Q2, which was above last year’s 9.4 GWh. Overall, Tesla continues to hold a strong position with $95.7 billion in trailing twelve-month revenue and a 17.7% gross margin, as noted in a report from Investing.com.
Tesla’s stock is still volatile
Tesla’s market cap fell to $941 billion on Monday amid volatility that was likely caused in no small part by CEO Elon Musk’s political posts on X over the weekend. Musk has announced that he is forming the America Party to serve as a third option for voters in the United States, a decision that has earned the ire of U.S. President Donald Trump.
Despite Musk’s controversial nature, some analysts remain bullish on TSLA stock. Apart from Cantor Fitzgerald, Canaccord Genuity also reiterated its “Buy” rating on Tesla shares, with the firm highlighting the company’s positive Q2 vehicle deliveries, which exceeded its expectations by 24,000 units. Cannacord also noted that Tesla remains strong in several markets despite its year-over-year decline in deliveries.
-
Elon Musk2 weeks ago
Tesla investors will be shocked by Jim Cramer’s latest assessment
-
News3 days ago
Tesla debuts hands-free Grok AI with update 2025.26: What you need to know
-
Elon Musk1 week ago
Elon Musk confirms Grok 4 launch on July 9 with livestream event
-
Elon Musk5 days ago
xAI launches Grok 4 with new $300/month SuperGrok Heavy subscription
-
News2 weeks ago
Tesla Model 3 ranks as the safest new car in Europe for 2025, per Euro NCAP tests
-
Elon Musk2 weeks ago
xAI’s Memphis data center receives air permit despite community criticism
-
News5 days ago
Tesla begins Robotaxi certification push in Arizona: report
-
Elon Musk2 weeks ago
Tesla reveals it is using AI to make factories more sustainable: here’s how