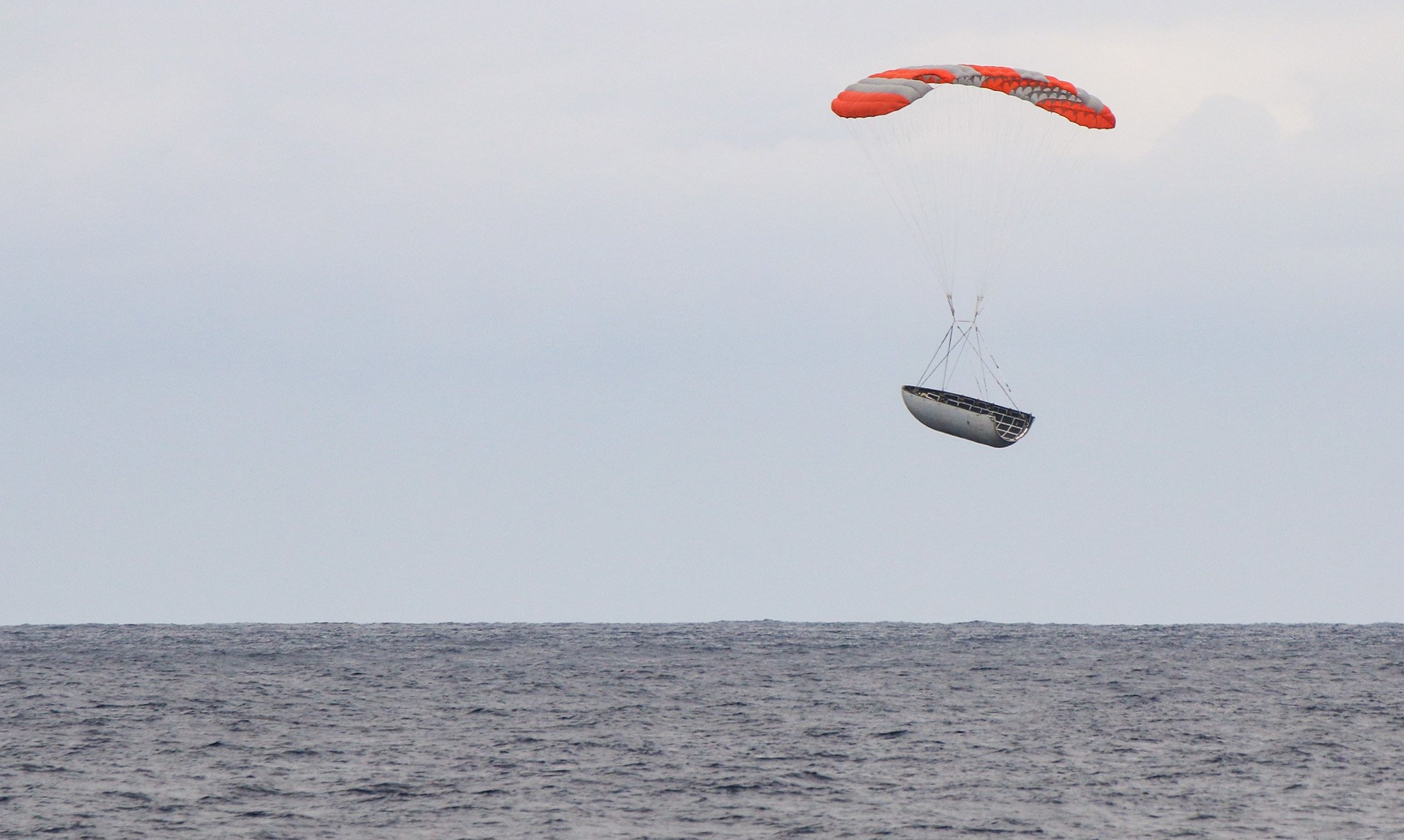
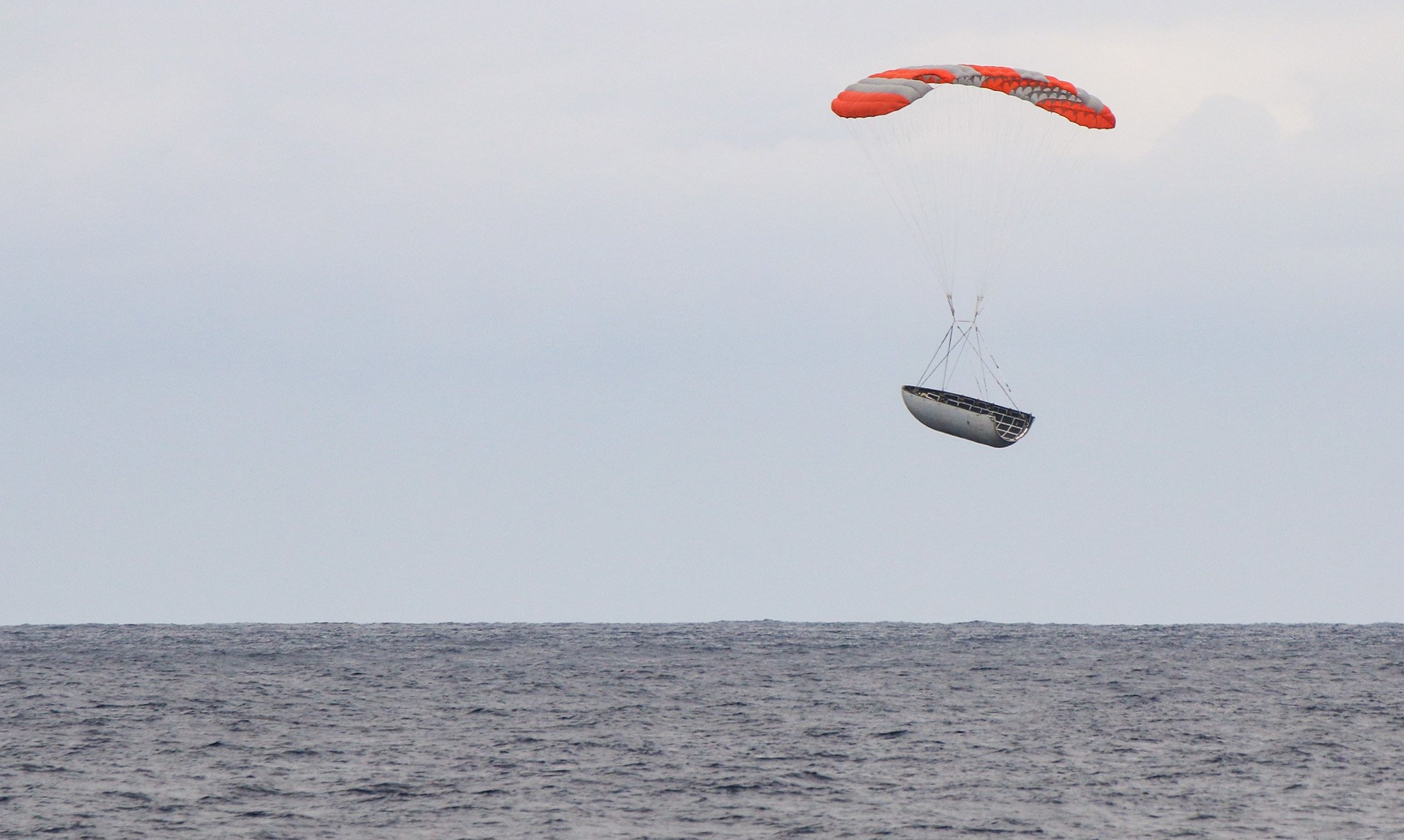
News
SpaceX photos reveal Falcon 9 fairings parasailing to Pacific splashdown
SpaceX has released the first high-quality photos of Falcon 9’s payload fairing recovery hardware in action, showing the massive carbon fiber-aluminum halves gliding by parafoil less than a rocket-length away from recovery vessel Mr. Steven’s massive net.
If anything, these photos demonstrate just how close SpaceX is – both literally and figuratively – to successfully catching payload fairings out of the air, the final keystone of fairing reuse. Per the extraordinarily minimalist appearance of each half’s parafoil recovery hardware and the lack of any clear control mechanism, it’s very likely that SpaceX has sided with an in-canopy system of actuators tasked with subtly warping the parafoil, comparable in functionality to a crude replica of a bird’s wing.
Falcon 9 fairing halves deployed their parafoils and splashed down in the Pacific Ocean last week after the launch of Iridium-6/GRACE-FO. Closest half was ~50m from SpaceX’s recovery ship, Mr. Steven. https://t.co/JS7d5zTdIg pic.twitter.com/LjiTwnB4wd
— SpaceX (@SpaceX) May 31, 2018
In-wing actuation and control is an elegant – if complex – solution to the problem of parafoil guidance. In this case, SpaceX’s contractor (MMIST) likely deserves at least some of the credit for several nearly successful recoveries, delivering each unpowered fairing half from an altitude of 110+ kilometers, speeds of more than 2 kilometers per second, and parabolic trajectories stretching over 800 kilometers to a square roughly 100m by 100m. If each halve’s accuracy can be cut by 75% of that to an area of 50m by 50m, SpaceX and Mr Steven should have no trouble in reliably and routinely catching Falcon 9 payload fairings for rapid reuse, perhaps one day translating into a similar approach for the recovery of Falcon 9’s orbital upper stages.
- The payload fairing for NASA’s Transiting Exoplanet Survey Satellite (TESS) is moved inside the Payload Hazardous Servicing Facility at the agency’s Kennedy Space Center in Florida. (NASA)
- By all appearances, both Iridium-6/GRACE-FO fairing halves were retrieved intact from the ocean surface. Note the tiny technician installing a tarp inside one half. (Chuck Bennett, Instagram @chuckbennett)
- Both fairing halves from SpaceX’s Iridiium-6/GRACE-FO spied aboard Mr Steven after docking. (Pauline Acalin)
It’s unclear if SpaceX has designed and built its fairing recovery parafoils largely on its own or if it has instead sided with established subcontractors like MMIST and consumer-off-the-shelf (COTS) solutions. Regardless, after approximately a year of trying, SpaceX appears to be rounding the very last corner to fairing recovery and reuse, perhaps avoiding the need for a series of drop-and-catch tests hinted at recently by CEO Elon Musk.
Once the massive 800-kilogram components can be captured in flight by Mr. Steven, it should be a fairly prospect for SpaceX to move from recovery to reuse, potentially saving as much as 10% ($6m) of the cost of each Falcon 9 and Falcon Heavy launch. Perhaps even more importantly, fairing reuse would remove some of the pressure placed on SpaceX’s composite production floor, which currently must support the fabrication of dozens of fairing halves, booster interstages, payload adapters, Falcon Heavy nose cones, and much more, including smaller subassemblies required for both Crew and Cargo Dragons.

SpaceX’s composite production floor shown in mid-2016. Note the Falcon Heavy nose cone, two interstages, and two fairing halves. (SpaceX)
As a result of their carbon fiber-aluminum honeycomb construction, each half inherently takes a disproportionate amount of time to manufacture, exaggerated by the need for massive and expensive curing autoclaves (a mix of an oven and a pressure chamber), of which only a handful can fit inside SpaceX’s Hawthorne factory. For a manifest of roughly 30 launches per year, as is the goal for 2018, this would require the production of an entire fairing half every six days, an extraordinary feat of heroics when building massive monolithic composite parts in a space-constrained factory.
With reuse, those heroics could be relaxed or at least focused elsewhere on Falcon 9, Heavy, Crew Dragon, and BFR production. With any luck, SpaceX’s next West coast launch, currently NET early July, may see Mr. Steven’s first-ever successful fairing catch, thanks in part to a brand new net.
Elon Musk
Tesla analysts believe Musk and Trump feud will pass
Tesla CEO Elon Musk and U.S. President Donald Trump’s feud shall pass, several bulls say.
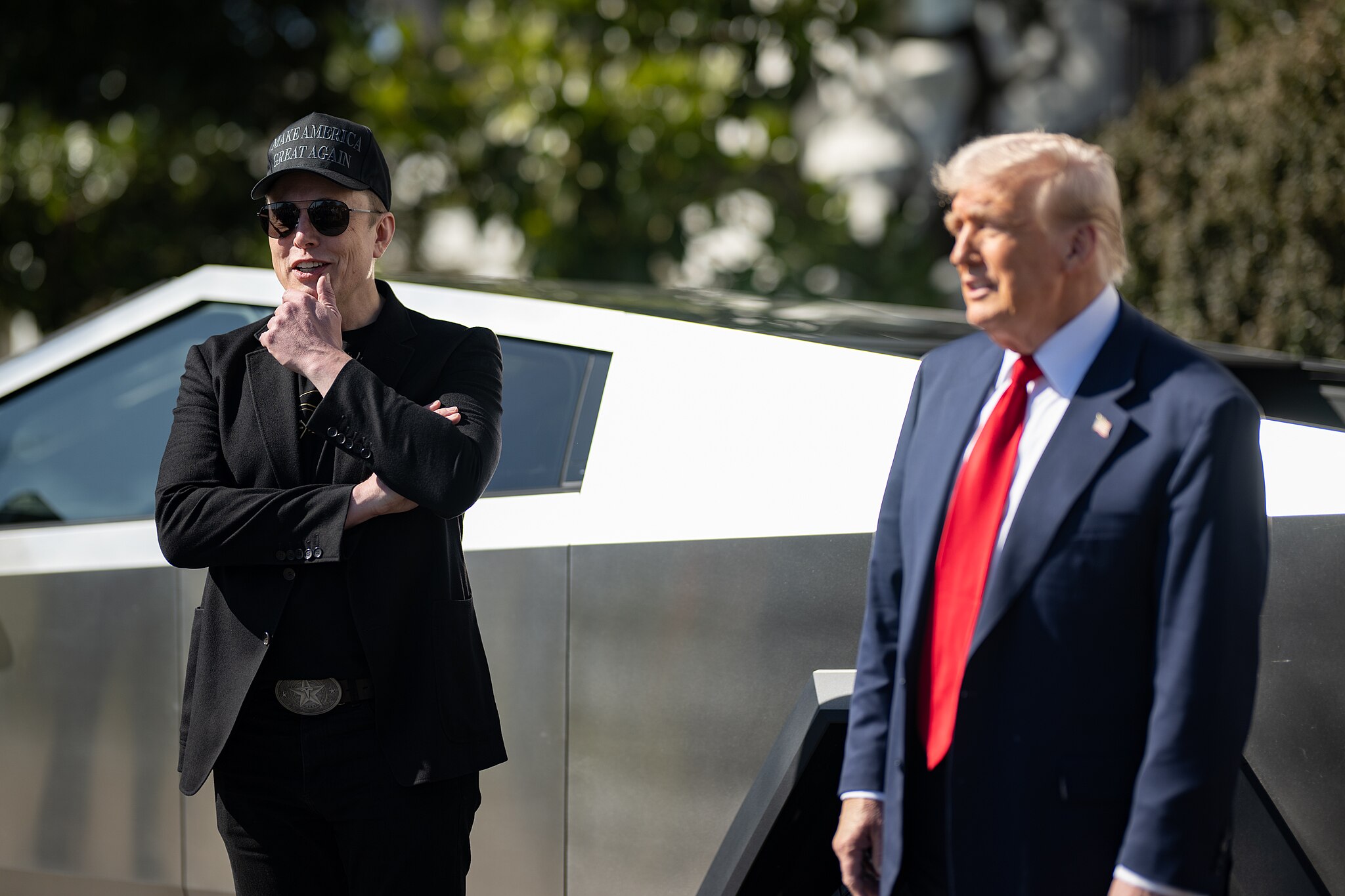
Tesla analysts are breaking down the current feud between CEO Elon Musk and U.S. President Donald Trump, as the two continue to disagree on the “Big Beautiful Bill” and its impact on the country’s national debt.
Musk, who headed the Department of Government Efficiency (DOGE) under the Trump Administration, left his post in May. Soon thereafter, he and President Trump entered a very public and verbal disagreement, where things turned sour. They reconciled to an extent, and things seemed to be in the past.
However, the second disagreement between the two started on Monday, as Musk continued to push back on the “Big Beautiful Bill” that the Trump administration is attempting to sign into law. It would, by Musk’s estimation, increase spending and reverse the work DOGE did to trim the deficit.
Every member of Congress who campaigned on reducing government spending and then immediately voted for the biggest debt increase in history should hang their head in shame!
And they will lose their primary next year if it is the last thing I do on this Earth.
— Elon Musk (@elonmusk) June 30, 2025
President Trump has hinted that DOGE could be “the monster” that “eats Elon,” threatening to end the subsidies that SpaceX and Tesla receive. Musk has not been opposed to ending government subsidies for companies, including his own, as long as they are all abolished.
How Tesla could benefit from the ‘Big Beautiful Bill’ that axes EV subsidies
Despite this contentious back-and-forth between the two, analysts are sharing their opinions now, and a few of the more bullish Tesla observers are convinced that this feud will pass, Trump and Musk will resolve their differences as they have before, and things will return to normal.
ARK Invest’s Cathie Wood said this morning that the feud between Musk and Trump is another example of “this too shall pass:”
BREAKING: CATHIE WOOD SAYS — ELON AND TRUMP FEUD “WILL PASS” 👀 $TSLA
She remains bullish ! pic.twitter.com/w5rW2gfCkx
— TheSonOfWalkley (@TheSonOfWalkley) July 1, 2025
Additionally, Wedbush’s Dan Ives, in a note to investors this morning, said that the situation “will settle:”
“We believe this situation will settle and at the end of the day Musk needs Trump and Trump needs Musk given the AI Arms Race going on between the US and China. The jabs between Musk and Trump will continue as the Budget rolls through Congress but Tesla investors want Musk to focus on driving Tesla and stop this political angle…which has turned into a life of its own in a roller coaster ride since the November elections.”
Tesla shares are down about 5 percent at 3:10 p.m. on the East Coast.
Elon Musk
Tesla scrambles after Musk sidekick exit, CEO takes over sales
Tesla CEO Elon Musk is reportedly overseeing sales in North America and Europe, Bloomberg reports.
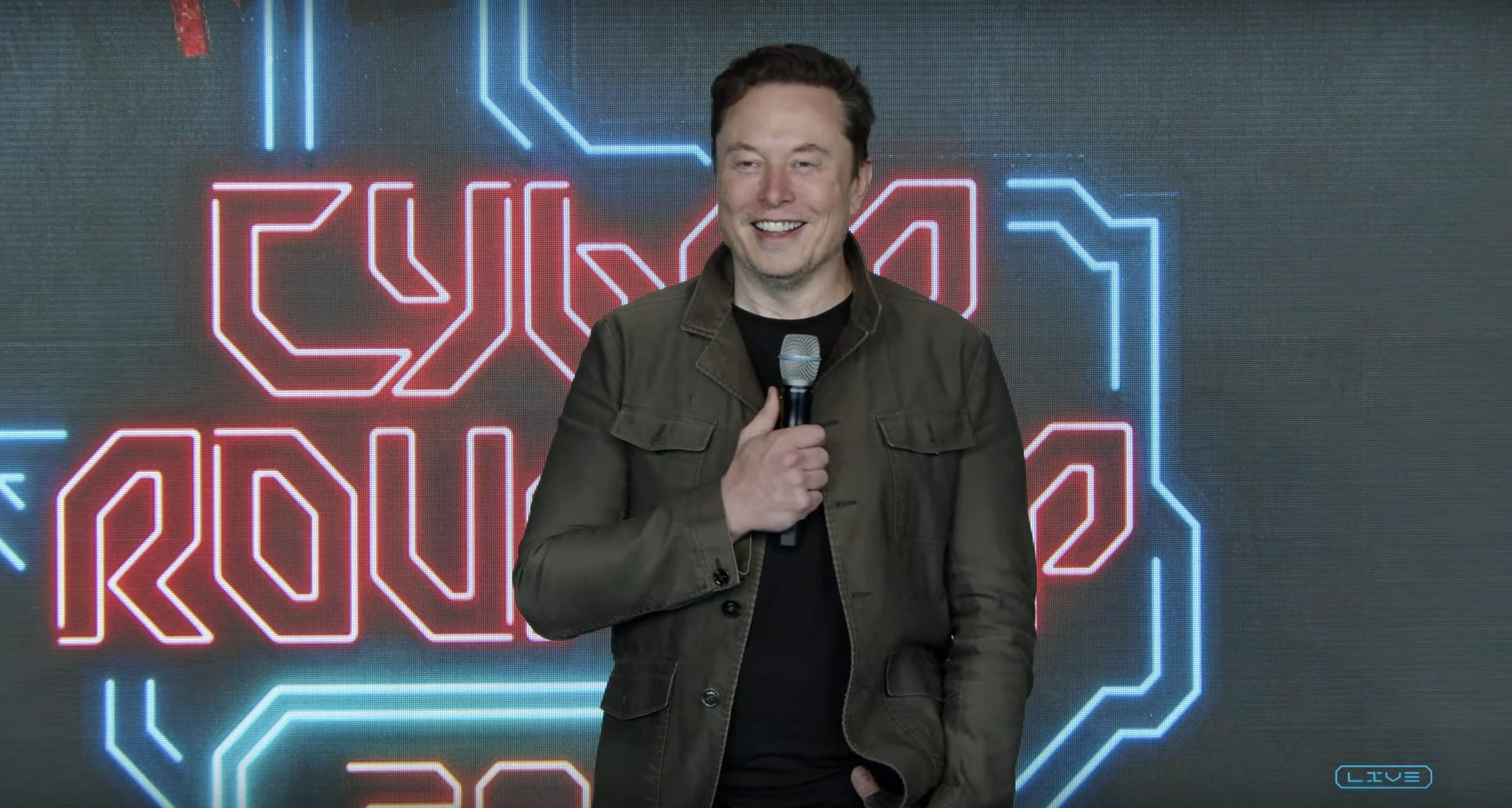
Tesla scrambled its executives around following the exit of CEO Elon Musk’s sidekick last week, Omead Afshar. Afshar was relieved of his duties as Head of Sales for both North America and Europe.
Bloomberg is reporting that Musk is now overseeing both regions for sales, according to sources familiar with the matter. Afshar left the company last week, likely due to slow sales in both markets, ending a seven-year term with the electric automaker.
Tesla’s Omead Afshar, known as Elon Musk’s right-hand man, leaves company: reports
Afshar was promoted to the role late last year as Musk was becoming more involved in the road to the White House with President Donald Trump.
Afshar, whose LinkedIn account stated he was working within the “Office of the CEO,” was known as Musk’s right-hand man for years.
Additionally, Tom Zhu, currently the Senior Vice President of Automotive at Tesla, will oversee sales in Asia, according to the report.
It is a scramble by Tesla to get the company’s proven executives over the pain points the automaker has found halfway through the year. Sales are looking to be close to the 1.8 million vehicles the company delivered in both of the past two years.
Tesla is pivoting to pay more attention to the struggling automotive sales that it has felt over the past six months. Although it is still performing well and is the best-selling EV maker by a long way, it is struggling to find growth despite redesigning its vehicles and launching new tech and improvements within them.
The company is also looking to focus more on its deployment of autonomous tech, especially as it recently launched its Robotaxi platform in Austin just over a week ago.
However, while this is the long-term catalyst for Tesla, sales still need some work, and it appears the company’s strategy is to put its biggest guns on its biggest problems.
News
Tesla upgrades Model 3 and Model Y in China, hikes price for long-range sedan
Tesla’s long-range Model 3 now comes with a higher CLTC-rated range of 753 km (468 miles).
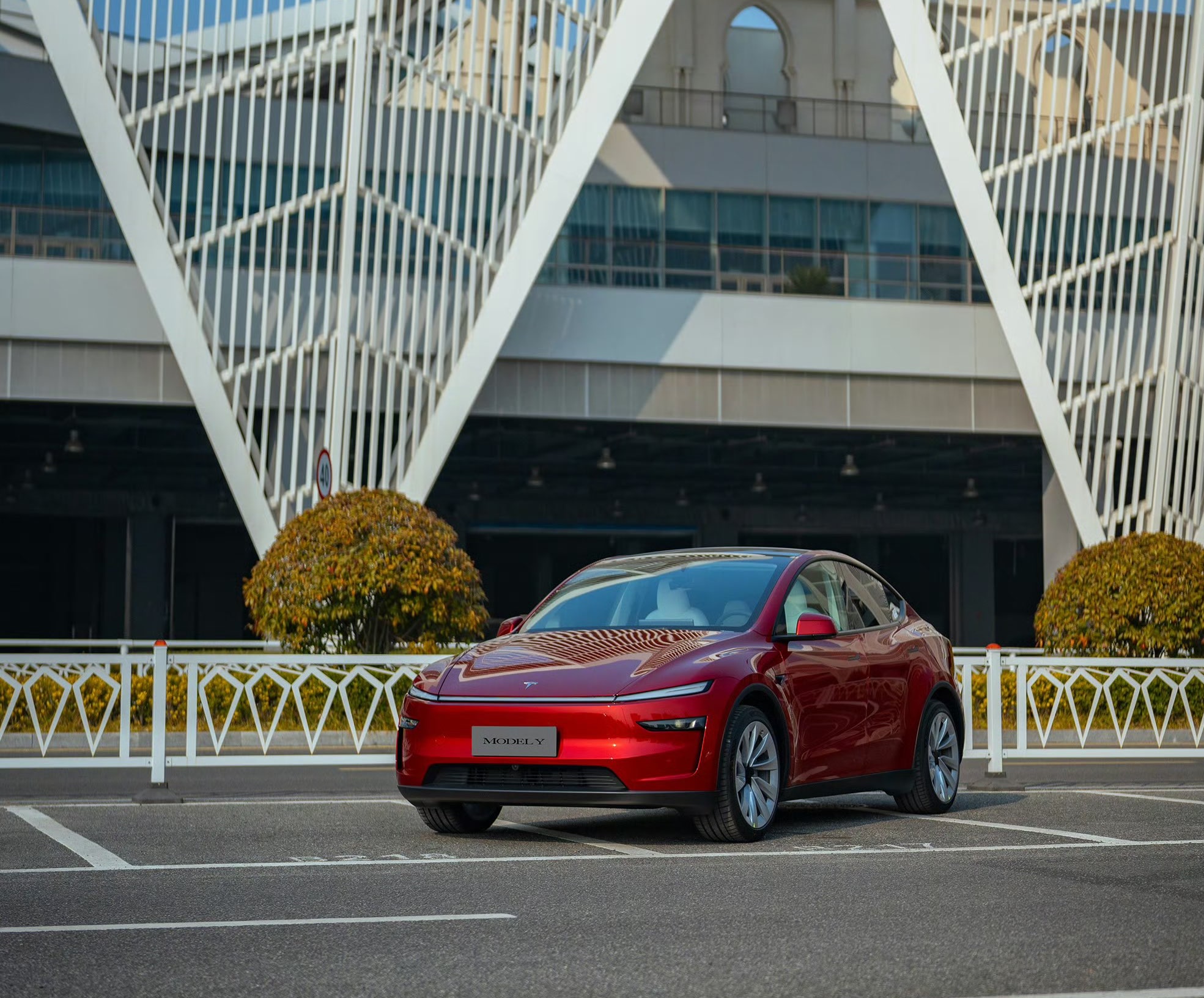
Tesla has rolled out a series of quiet upgrades to its Model 3 and Model Y in China, enhancing range and performance for long-range variants. The updates come with a price hike for the Model 3 Long Range All-Wheel Drive, which now costs RMB 285,500 (about $39,300), up RMB 10,000 ($1,400) from the previous price.
Model 3 gets acceleration boost, extended range
Tesla’s long-range Model 3 now comes with a higher CLTC-rated range of 753 km (468 miles), up from 713 km (443 miles), and a faster 0–100 km/h acceleration time of 3.8 seconds, down from 4.4 seconds. These changes suggest that Tesla has bundled the previously optional Acceleration Boost for the Model 3, once priced at RMB 14,100 ($1,968), as a standard feature.
Delivery wait times for the long-range Model 3 have also been shortened, from 3–5 weeks to just 1–3 weeks, as per CNEV Post. No changes were made to the entry-level RWD or Performance versions, which retain their RMB 235,500 and RMB 339,500 price points, respectively. Wait times for those trims also remain at 1–3 weeks and 8–10 weeks.
Model Y range increases, pricing holds steady
The Model Y Long Range has also seen its CLTC-rated range increase from 719 km (447 miles) to 750 km (466 miles), though its price remains unchanged at RMB 313,500 ($43,759). The model maintains a 0–100 km/h time of 4.3 seconds.
Tesla also updated delivery times for the Model Y lineup. The Long Range variant now shows a wait time of 1–3 weeks, an improvement from the previous 3–5 weeks. The entry-level RWD version maintained its starting price of RMB 263,500, though its delivery window is now shorter at 2–4 weeks.
Tesla continues to offer several purchase incentives in China, including an RMB 8,000 discount for select paint options, an RMB 8,000 insurance subsidy, and five years of interest-free financing for eligible variants.
-
Elon Musk1 day ago
Tesla investors will be shocked by Jim Cramer’s latest assessment
-
News6 days ago
Tesla Robotaxi’s biggest challenge seems to be this one thing
-
News2 weeks ago
Tesla’s Grok integration will be more realistic with this cool feature
-
Elon Musk2 weeks ago
Elon Musk slams Bloomberg’s shocking xAI cash burn claims
-
News2 weeks ago
Tesla China roars back with highest vehicle registrations this Q2 so far
-
News2 weeks ago
Texas lawmakers urge Tesla to delay Austin robotaxi launch to September
-
News2 weeks ago
Tesla dominates Cars.com’s Made in America Index with clean sweep
-
Elon Musk1 week ago
First Look at Tesla’s Robotaxi App: features, design, and more