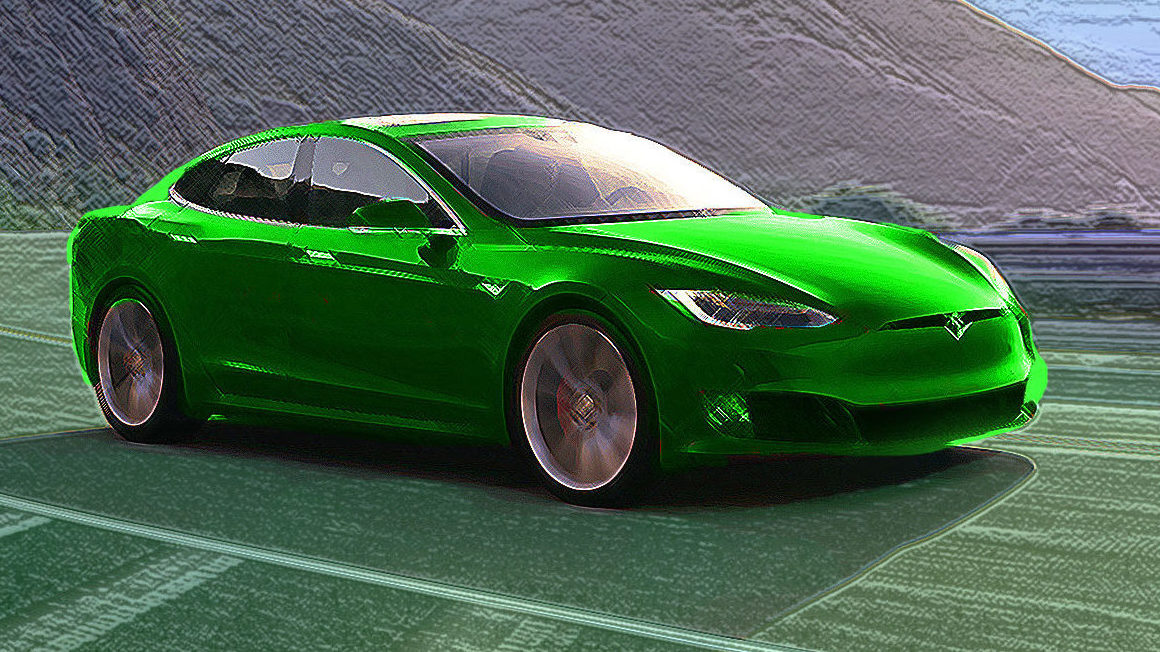
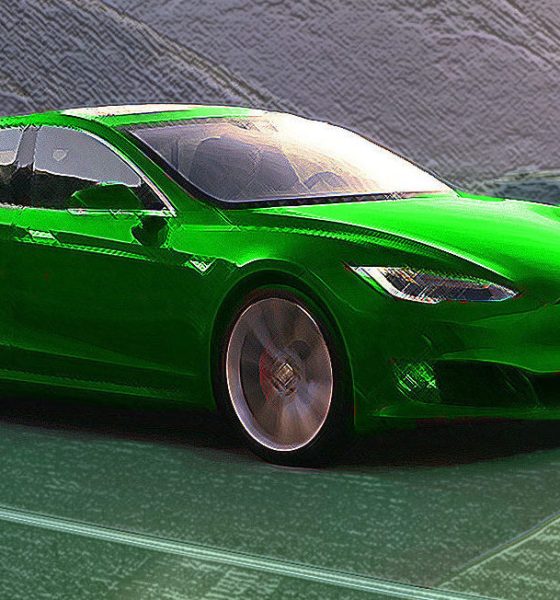
Lifestyle
A Tesla is greener than you think and getting greener – a look at manufacturing
An electric vehicle is more than just a new form of technology. It’s part of a shift in our entire way of life. From a consumables based civilization to a renewable one. My last article focused on the environmental benefits of driving an electric vehicle, but what about manufacturing? Is it also sustainable?
One of the main themes from my previous article is that the data surrounding electric vehicles has been quickly changing. Our electricity grid is getting greener, batteries are increasing in energy density, and costs are falling. This rapid advancement is the reason for many misconceptions about electric vehicles and it holds true of manufacturing as well. This article dives into the manufacturing impact, to give you a better feel for its significance, and show how much better it can get.
First though I want to be clear, an electric vehicle is without a doubt the better environmental choice. To get a good snapshot of this just take a look at the lifecycle greenhouse gas emissions in the graph below. These emissions include everything from raw material extraction, to vehicle manufacturing, through operation, and finally to end of life. It’s clear that the reductions from driving far exceed any emissions from vehicle production. The savings are huge.
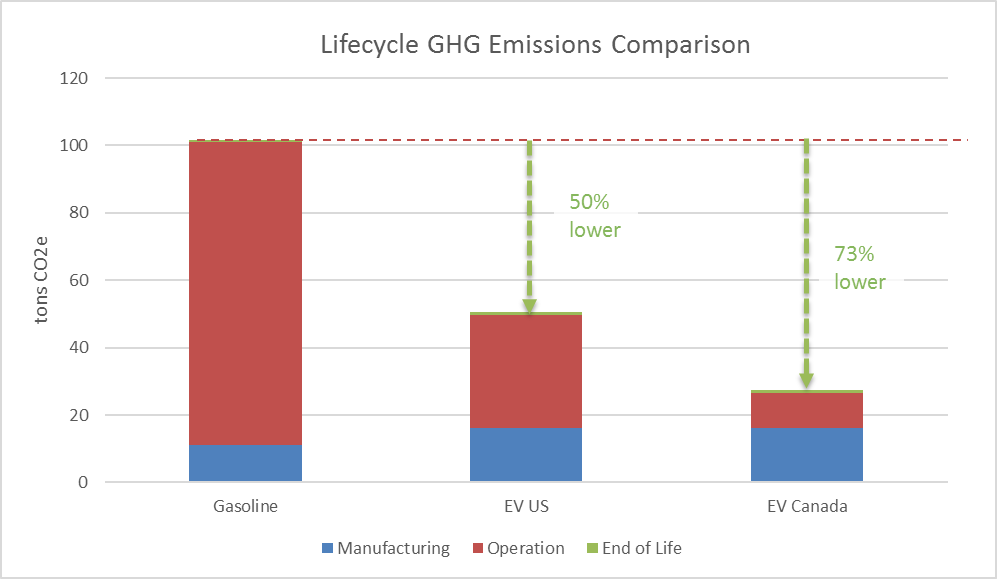
*Based on 180,000 miles of lifetime driving of a large electric sedan (85kWh), batteries manufactured in China, vehicles made in Germany or USA, IPCC median data of lifecycle emissions factors for electricity sources, 2016 electricity source mix from Canada and the USA for EV charging, and EPA data for a 26 mpg vehicle.
But what is the manufacturing based on you say? A fair question. Manufacturing emissions depend on many factors like: which materials are used, the source of those materials, technologies incorporated into the manufacturing processes, material transportation needs, and the type of energy used at each stage of production. The manufacturing data in the graph above is based on batteries produced on a carbon intensive grid (like China) with final vehicle assembly in Germany or the US. For a large 85kWh Tesla battery weighing around 550 kg, the battery would account for 6 tons of greenhouse gas emissions. I’ve seen this as the typical scenario in many research papers but with electricity grids getting cleaner every year the data quickly falls out of date. Still, it serves as a good baseline scenario. You may have seen higher numbers reported elsewhere, but frankly they are based on old data and often use the poor metric of kgCO2e/kWh, which doesn’t hold true as energy density rapidly improves. A better metric is kgCO2e/kg of battery but even that must be continually updated.
What may not be immediately clear from the graph, is that the savings from driving an electric vehicle will very quickly payback the emissions from manufacturing the entire vehicle. In Canada the payback would occur after about 55,000 kms, and the USA at 77,000 kms. So, if you’re already driving, the most environmentally friendly thing you can do is replace your combustion vehicle with an electric vehicle today!
That’s great…..but can we do better?
Remember that the blue bar in the graph assumes batteries are made in China and the vehicles are made in Germany or the USA. Not exactly low carbon electricity grids. It’s also based on studies using electricity data already a few years old and doesn’t account for the specific manufacturing facilities that are already better than the average electricity grids in those countries. Many manufacturers have also incorporated on site renewable energy and better recycling practices.
Manufacturer Highlights
- Tesla currently manufacturers vehicles in California and batteries in Nevada. The Nevada battery Gigafactory will be 100% renewably powered with a 70MW solar array and have on site recycling. The Freemont California grid is actually already very clean with 70% from non-fossil fuels (which partially explains the lack of solar there).
- Chevy’s Bolt is manufactured by GM in Michigan. 54% of the facility’s energy comes from a combination of a 350kW solar array and landfill gas. The batteries are made by LG batteries in Holland Michigan, predominately powered by a natural gas power plant. There is no solar integration in that LG facility but satellite imagery appears to show solar installed on some of their international facilities (oddly this is not mentioned in their sustainability reports). GM also has a plan to use 100% renewable energy by 2050 but that’s almost meaningless because almost everything should be 100% renewably powered by then or we’re going to be in big trouble.
- The Ford Focus EV is also made in Michigan factory which incorporates a 500kW solar array. Their batteries are also made by LG.
- Nissan has a solar array on the Leaf factory in Japan, but they don’t have one on the USA factory. Their batteries are also made by LG.
That’s a good look at today but manufacturers will continue to improve. In fact that’s a recurring theme in all my research, that what was true 5 years ago for electric vehicles is not the reality today and that in turn won’t be representative of the future. Electricity is getting cleaner, cars are getting lighter, recycling is improving, and batteries are becoming more energy dense. All of this makes manufacturing an EV more sustainable. The big question is how quickly and how much can they improve?
There are a variety of papers published on how individual factors can benefit the sustainability of electric vehicle manufacturing. What I’ve done is combine the impacts, as graphed below. The key takeaway from the graph is that Tesla, and possible others, are making EVs with low embodied manufacturing emissions and that this will only improve as time goes on.
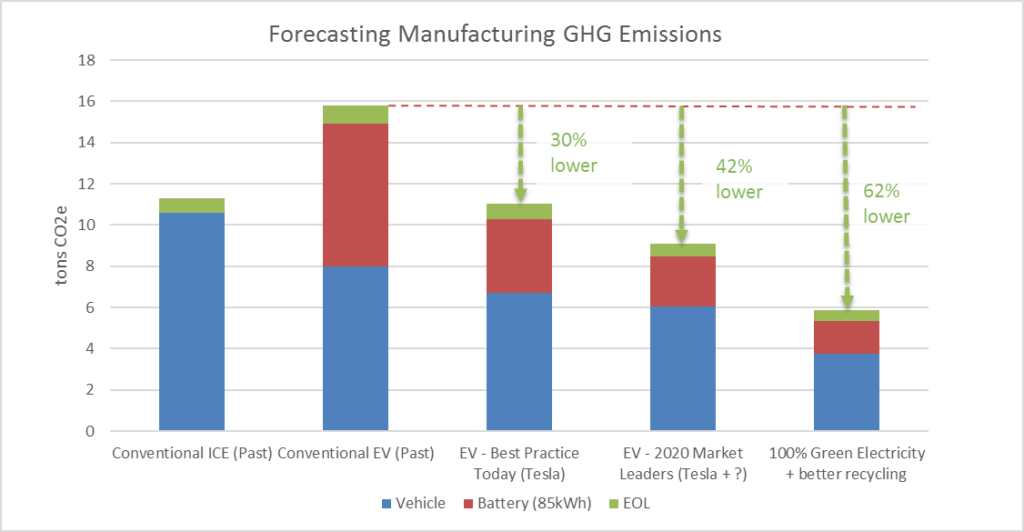
The graph compares the emissions from conventional manufacturing practices for a large combustion sedan and a large EV sedan, and then compares that to sustainability leaders like Tesla today, in 2020, and then into the future. Please remember this is representative data based on many research reports, manufacturing practices, battery density forecasts, some estimations of future conditions, and some interpolation of data.
How are these results achieved?
1: Selecting Clean Electricity Sources
Electricity is used extensively to produce both the materials used in vehicles and the assembled vehicles themselves, but there’s a huge variation in how ‘clean’ electricity grids are. China, Germany, and Michigan, are all locations big on vehicle manufacturing. China also has a huge chunk of the world’s battery production and will continue to do so. By 2020, worldwide production capacity is expected to expand five-fold, with China and South Korea producing 75% of world’s batteries.
In China coal use is down but still accounts for over 60% of electricity production, while in the USA it’s been dropping even faster, now at 30%. Germany, South Korea, and Michigan still get about 40% of their electricity from coal. Coal is a dirty fuel and manufacturers should avoid it to improve their sustainability. Then there’s the issue of climate change, driven by greenhouse gas emissions. Even though natural gas is cleaner to burn than coal, it still creates a lot of greenhouse gas and is responsible for significant methane leaks. For comparison purposes I’ve graphed the greenhouse gas emissions factors for relevant electricity grids and highlighted some specific manufacturer information to account for on-site renewable energy. It makes for an interesting comparison, showing that both the Chevy Bolt and Tesla facilities use electricity sources far greener than even their state grids.
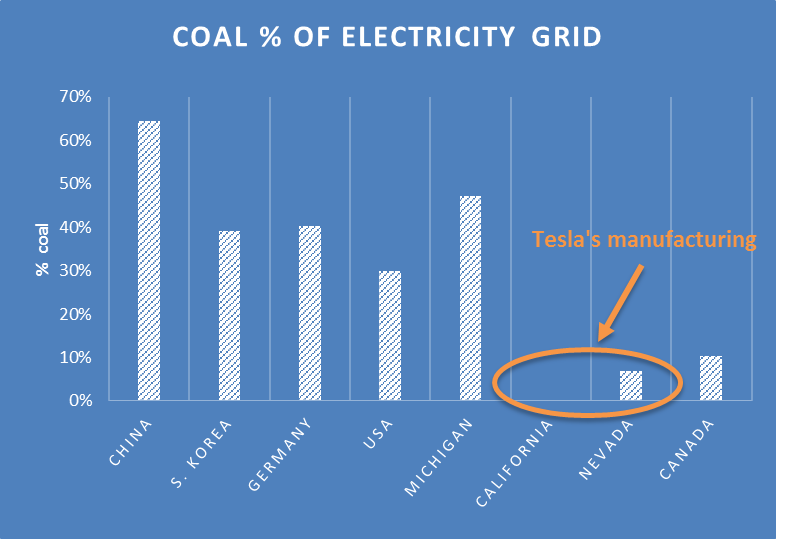
Why is coal considered dirty? Consider that natural gas produces approximately 50% less GHG emissions than coal, 99% less SOx, 90% less NOx, and 99% less particulates.
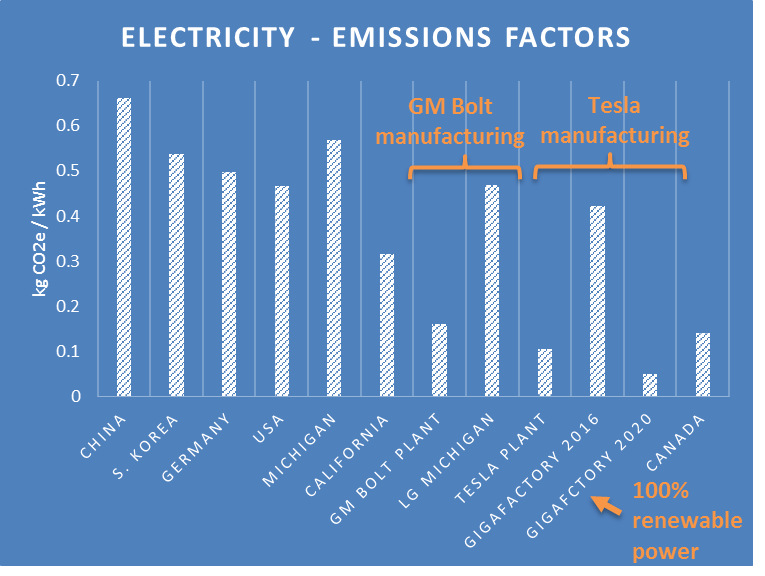
Data uses IPCC median emissions factors for electricity sources, not emission data from the individual plants or regions. It’s important to recognize that many of the components are not made by GM or Tesla at the facilities noted (i.e. airbags, engine blocks, etc). Electricity contributes 29% of the greenhouse gas emissions in the USA and industry is responsible for 21%. That means there’s a lot of room for manufacturing to go green with low-carbon electricity.
Look at the Gigafactory in 2020, what a difference a green electron makes! A recent study from the Norwegian University of Science and Technology found that using renewable electricity could drop production emissions by more than half. That’s for an entire Tesla Model S sized vehicle. With Tesla on the verge of expanding their manufacturing into China, it would be both surprising and disappointing if they didn’t make all new factories 100% renewably powered. It is the new benchmark that they themselves have set for sustainable manufacturing.
2: Light-weighting
You may have noticed a lot of manufacturers using more aluminum in their vehicles. There’s good reason for this. An aluminum body can be 40% lighter than a steel body, according to Audi, and Tesla’s Model S and X use aluminum exclusively in their construction. The push for longer range EVs is resulting in a push for lighter weight vehicles that use less materials. That’s great for the environment.
3: Longer Lasting Cars and Materials
Electric vehicles will last longer than conventional combustion cars today. Aluminum doesn’t rust, electric cars have far fewer moving parts to wear out and few disposable fluids to maintain, and the vehicles get over-the-air updates. But eventually they will wear-out, and this is where recycling comes in.
4: Recycling
Today material recovery rates for steel and aluminum in vehicles are very high, at about 90%. For aluminum this is a big deal because recycled aluminum uses only 5% of the electricity for processing, compared to processing from raw materials. I reached out to Tesla to get information on how much recycled content they use and where their aluminum comes from but they’ve yet to get back to me.
Batteries also benefit from recycling as they are composed mostly of valuable metals like aluminum, copper, nickel, cobalt, and lithium (there’s also the graphite anode to consider). Studies indicate a possible 50% reduction in total battery emissions from recycling. Tesla’s current battery recycler in Europe, Umicore, states that through their recycling they can already recover 70% of the GHG emissions that were produced during the original material extraction and refining stages. Large scale lithium-ion battery recycling won’t be needed for several years. Batteries today are expected to last a decade or more and that is continually improving. Just recently Tesla’s battery research division achieved a doubling of battery lifespans for NMC batteries used in their energy storage (their cars use the NCA chemistry). That was just one year into their work.
Imagine a vehicle that was produced entirely from recycled materials using 100% renewable energy, powered by renewable energy, driving quietly down the road with zero pollution. That’s the future. A truly closed loop, because once the materials are extracted, they can be used again and again. It’s not like gasoline which is used only once.
5: Ethical and local sourcing
The results discussed so far have included the emissions from extracting and processing materials, but what about the ethical and moral considerations? Ensuring that vehicles are produced ethically should be required of every manufacturer. Most of the manufacturers have ethical material sourcing reports, to varying degrees of diligence, and some is mandated of publicly traded companies. Tesla has also reaffirmed their commitment to ethically and locally sourced materials, on a number of occasions.
“Imagine a vehicle that was produced entirely from recycled materials using 100% renewable energy, powered by renewable energy, driving quietly down the road with zero pollution. That’s the future.”
Cobalt and graphite are potentially two of the biggest issues right now. Today 65% of the world’s cobalt comes from the Democratic Republic of Congo and most of the flake natural graphite is coming from China. Using less of these contentious materials is a good place to start. The NCA battery chemistry used by Tesla/Panasonic requires far less cobalt than the NMC chemistry commonly used by other manufacturers. They have also committed to sourcing cobalt from non-conflict zones. Canada seems to have a role to play here. Canada sits third in world production of cobalt and third in nickel production. It’s not a coincidence as cobalt is often the byproduct of nickel production. For graphite Tesla has previously stated that artificially produced graphite from Europe may be used and there are other anode materials in development.
Lithium is probably the most discussed material but accounts for ~10% of the battery by weight. It is overwhelmingly extracted from salt brines, pumped from under dried up salt flats in politically stable countries. It’s a pretty clean process but I do have issue with the evaporation process, as it depletes groundwater aquifers. Thankfully there are companies working to create new processes that don’t rely on evaporation to concentrate the minerals. But even with current methods, extracting a recyclable material like lithium has to be better than fracking for a consumable product like oil.
Conclusion:
Manufacturing electric vehicles today is comparable to or better than a combustion vehicle. This will only get better, especially if it’s something customers care about. It’s time to look beyond operational benefits and pay attention to which manufacturers are sustainability leaders. Vote with your dollars and call on manufacturers to make positive changes.
Tesla is undoubtedly one of the leaders. They are using clean electricity in their production today and their massive battery Gigafactory will be 100% renewably powered once complete. Their batteries have a low environmental impact relative to their peers due to the material composition, high energy densities, and clean electricity used in production. They are also have good recycling practices and will improve that with on-site battery recycling in the future. Their cars are long lasting, made of lightweight materials, and they have a good material sourcing strategy. If they can continue to be leaders in this way and push the industry forward, it may just transform all of manufacturing. That’s not to say Tesla is the only one. There are other manufacturers doing some of these good things, but no one seems to be as thorough or have the complete vision of the best possible future like Tesla does. But hey, if those other manufacturers can prove me wrong, all the better.
Lifestyle
Tesla brings perhaps the coolest interior feature to cars in latest update
Tesla adds on to the “fun” aspect of its vehicles.
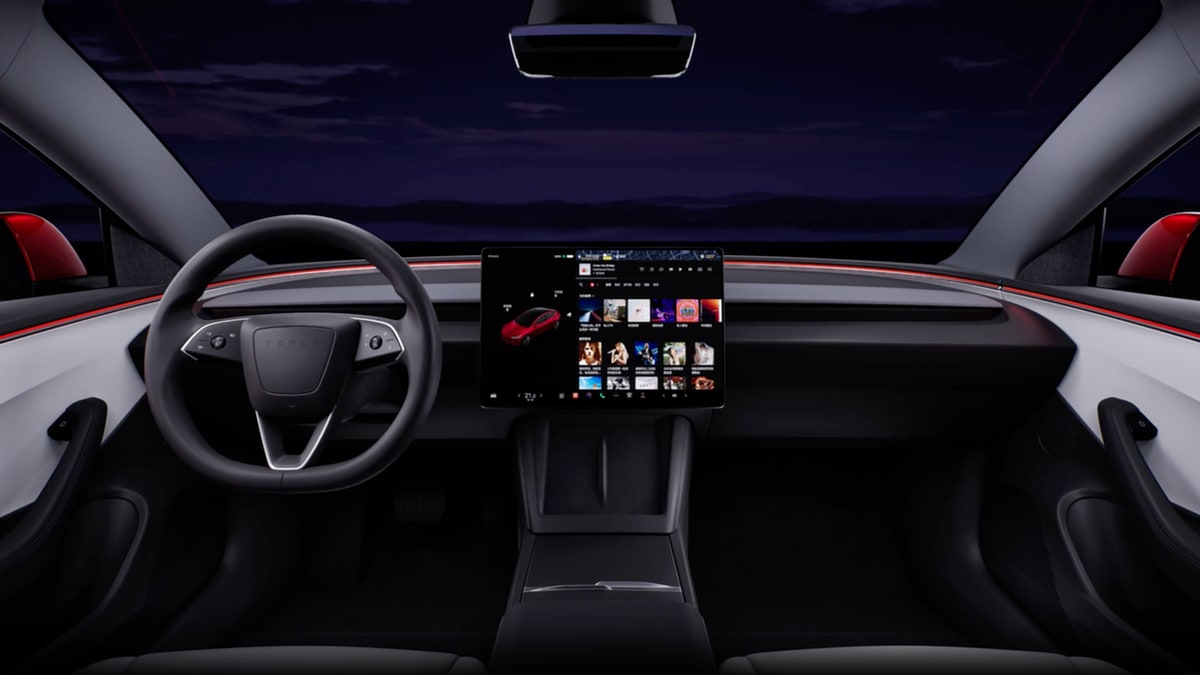
Tesla has brought perhaps the coolest interior feature to its cars in a new update that is rolling out to vehicles now.
The feature will require a newer vehicle that has interior ambient lighting, which is present on the new Model S, Model X, Model 3 “Highland,” and Model Y “Juniper.” The Cybertruck also has ambient lighting strips throughout.
Tesla Model Y’s ambient lighting design changes revealed in leaked video
With the Version 2025.26+ Software Update, Tesla is rolling out a new “Sync Accent Lights w/ Music” feature, which is available on the Tesla Toybox:
Turn your Tesla into a rave cave with the new Light Sync feature 🎶
Rolling out now in software update 2025.26+ pic.twitter.com/IIsQxZ9jDP
— Tesla (@Tesla) July 29, 2025
To enable the feature, you’ll access the Toybox, choose “Light Sync,” and then choose “Sync Accent Lights w/ Music.”
Although it does not improve the performance of the vehicle, it is yet another example of Tesla making one of the coolest cars out there. This is truly a cool add-on that can be used to impress your friends and family.
Elon Musk
xAI, Musk Foundation helps schools near Memphis supercomputer site
Reports of xAI and the Musk Foundation’s work were recently posted by local news media.
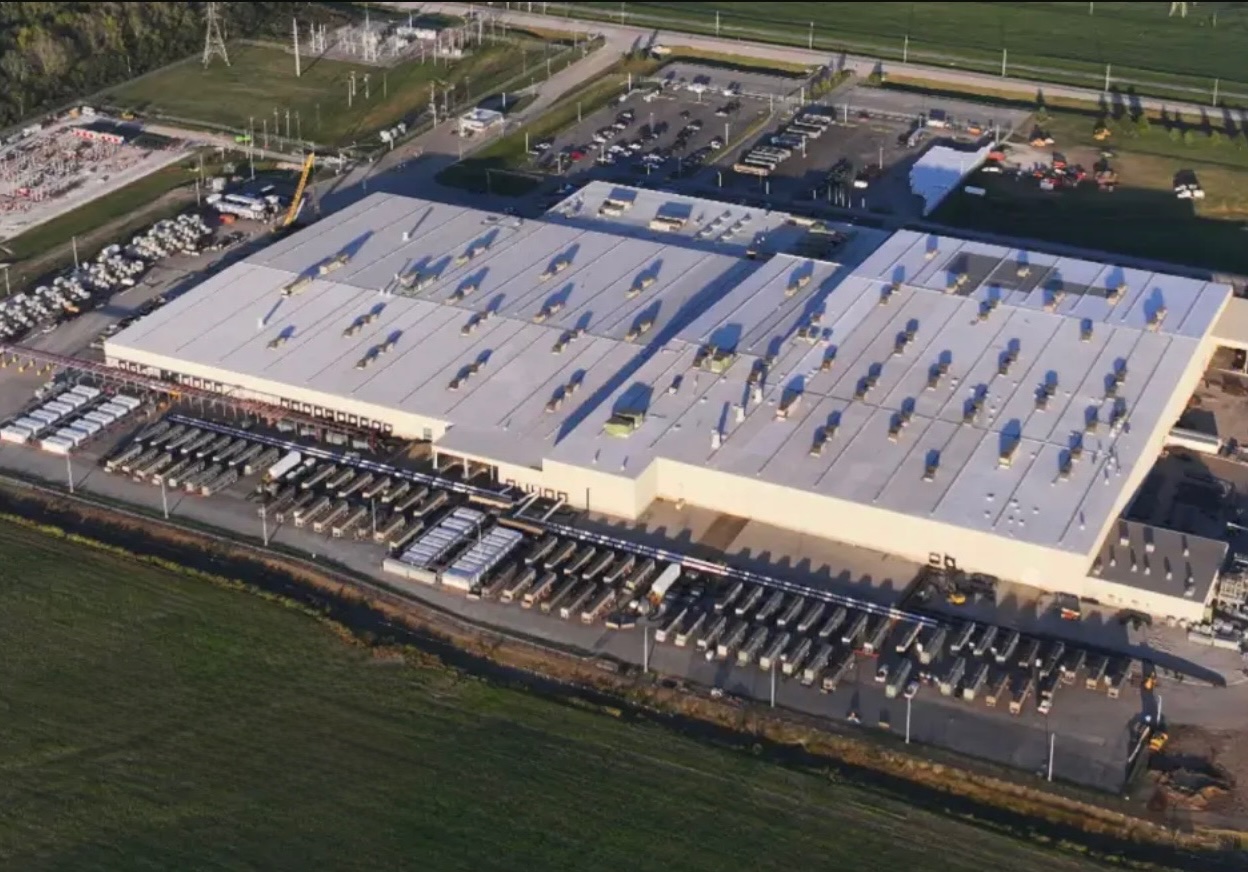
Elon Musk’s artificial intelligence startup xAI and the Musk Foundation have been supporting Memphis-Shelby County Schools with HVAC repairs and facility upgrades, while also funding youth programs for students in the area.
Reports of xAI and the Musk Foundation’s work were recently posted by local news media.
xAI’s school visits lead to facility repairs
Representatives from xAI visited John P. Freeman Optional School, Fairley High School, and Westwood High School, all of which are located near its Colossus supercomputer site, to assess HVAC systems, plumbing, gym facilities, and athletic fields. The visits resulted in a list of priority repairs, some of which were completed in April and May.
In addition to the repairs, xAI also shared a number of initiatives that are planned for students in the area, as stated in a Commercial Appeal report.
“xAI is working on providing STEM workshops for local students, donating equipment to technical training programs, and supporting job fairs to boost employment opportunities. These initiatives reflect xAl’s commitment to fostering education and economic growth in Memphis,” xAI noted in a statement.
Musk Foundation donation
Apart from xAI, the Musk Foundation also donated $350,000 to the Boys & Girls Clubs of Greater Memphis, enabling the reopening of two club sites located at Booker T. Washington High School and Westwood High School. Both locations had closed earlier this year due to lapses in funding. As per xAI, the Musk Foundation’s donation allows clubs to reopen for almost 1,000 students.
The donation will fund staffing, supplies, and transportation, among others. “Kids are the future of humanity,” Elon Musk said in a statement, adding that students need “every chance to shoot for the stars.”
“We’re honored to support the Boys & Girls Clubs of Greater Memphis in reopening these sites, giving kids in underserved communities the tools to build brighter futures,” Musk said.
The gift was praised by local officials, including Boys & Girls Clubs board chair Michael Garriga, who stated that the “commitment will ensure the youth of our community have the opportunities they need to develop their skills and talents to become successful students and future citizens.”
Lifestyle
EV fans urge Tesla to acquire Unplugged Performance for edge in fleet and security industry
Unplugged Performance has built a name for itself by producing performance upgrades for Tesla vehicles.
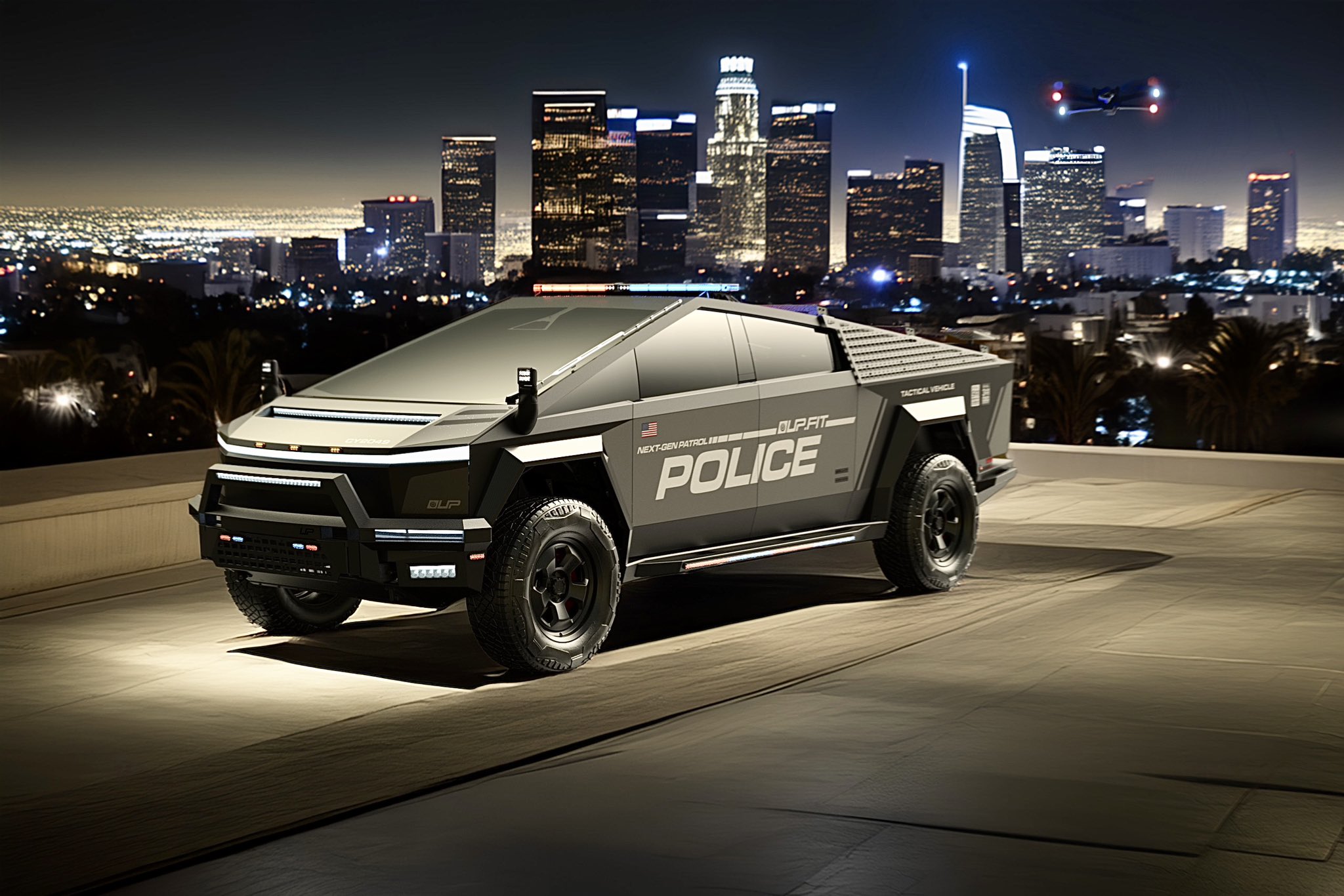
A growing number of Tesla enthusiasts and longtime community voices are calling on the electric vehicle maker to acquire Unplugged Performance, a California-based aftermarket company best known for tuning Tesla vehicles and developing specialized government fleet solutions under its UP.FIT division.
The idea was once considered a niche proposal among EV fans, but it is now gaining serious attention not just as a performance play but as a strategic move to deepen Tesla’s roots in the fleet and security industry.
A strategic fit
Unplugged Performance has built a name for itself by producing performance upgrades for Tesla vehicles, from track-optimized components to visual and aerodynamic upgrades. But in recent years, its UP.FIT division has pivoted toward a more functional future by outfitting Tesla vehicles like Model Ys for police, military, and government use.
That work has sparked growing calls for closer collaboration with Tesla, especially as the EV maker increasingly leans into autonomy, AI, and fleet services as core components of its next chapter.
“I posted this four years ago, but I think it’s more true now than ever,” wrote Whole Mars Catalog, a well-known Tesla investor and FSD Beta tester, on X. “Tesla should buy Unplugged. But not just as a Performance division. What they are doing with UP.FIT unlocks large government and commercial fleet purchases that can improve utilization.”
Tesla fans such as shareholder Sawyer Merritt echoed the sentiment, calling Unplugged a “great fit within Tesla.” adding, “They are literally located directly next to Tesla’s design studio in Hawthorne.”
Enabling the next wave
Supporters of the idea noted that integrating Unplugged into Tesla’s corporate structure could help accelerate the adoption of autonomous technologies in government sectors. With UP.FIT patrol cars already in use across some U.S. police departments, Tesla fans envisioned a future where self-driving Teslas could potentially revolutionize law enforcement, search-and-rescue, and public service logistics.
“Just imagine how autonomous patrol cars could transform policing and bring us into a safer future,” the veteran FSD tester wrote.
The benefits could also extend to Tesla’s existing consumer base. “They also have some incredible products in the works that I think will appeal to many ordinary Tesla drivers — not just those looking for performance or mods. Stuff that’s so good it should have come straight from the design studio next door,” Whole Mars Catalog noted.
Unplugged Performance, founded in 2013, shares not just a product vision with Tesla, but also geography. Its Hawthorne headquarters sits directly adjacent to Tesla’s design studio, and the two companies have maintained a close working relationship over the years. The aftermarket firm has long positioned itself as a “mission-aligned” partner to Tesla.
In response to the recent calls for acquisition, Unplugged Performance acknowledged the support from the community. “Our very existence is to support the Tesla mission with @UpfitTesla and @UnpluggedTesla,” Unplugged CEO Ben Schaffer posted on X. “We love working with Tesla and are grateful for the community’s support since 2013!”
-
Elon Musk15 hours ago
SpaceX Starship Flight 10 was so successful, it’s breaking the anti-Musk narrative
-
News23 hours ago
Tesla China working overtime to deliver Model Y L as quickly as possible
-
Elon Musk3 days ago
Elon Musk argues lidar and radar make self driving cars more dangerous
-
News3 days ago
Tesla Model Y L sold out for September 2025
-
News11 hours ago
Tesla appears to have teased a long-awaited Model Y trim for a Friday launch
-
Elon Musk6 days ago
Elon Musk takes aim at Bill Gates’ Microsoft with new AI venture “Macrohard”
-
Elon Musk21 hours ago
Tesla reveals it has expanded its Robotaxi fleet in Austin
-
News1 day ago
Tesla Semi earns strong reviews from veteran truckers