Rumors have recently emerged from China suggesting that Tesla is looking to tap Switzerland’s Bühler as another Giga Press supplier. Similar to IDRA, Bühler is also a manufacturer of large-scale die-casting machines.
The rumor was initially shared by Tesla and EV industry watcher Chris Zheng on Twitter. Citing information from employees of a Chinese car startup, Zheng noted that China would have a number of vehicles in mass production next year that will be using integrated die castings like the Tesla Model Y. These companies reportedly benchmark and analyze Tesla and its vehicles.
“Tesla’s Giga press supplier will be replaced from Italy’s IDRA to Switzerland’s Bühler next year. The latter is also one of the world’s 6 largest die-casting giants. It rejected Tesla’s demand for a 6000t-level Giga press in 2019, but now their products offer better performance,” Zheng wrote on Twitter.
This is undoubtedly a rumor for now, though it is one that is extremely interesting. Teslarati has reached out to Tesla for a comment on the rumor and will update this story if or when we receive a response.
While the idea of IDRA being replaced by Bühler may sound too extreme, it is possible that Tesla would tap the resources of another die casting machine maker for its upcoming vehicle production ramp. Bühler is an interesting choice nonetheless, especially since the company was one of the firms that rejected Tesla’s proposal for a 6,000-ton Giga Press a few years ago.
Elon Musk himself mentioned this during the Cyber Rodeo event. According to Musk, Tesla had approach the world’s six top die-casting machine makers, and all but IDRA considered the construction of a Giga Press. Tesla has since proven that Giga Presses work, however, so it’s not surprising to see other companies also trying their hand at creating Giga Press-level machines.
“It’s a revolution in car manufacturing to basically make a car out of three major parts — a cast rear, a structural pack, and a cast front. So what you’re looking at are the biggest casting machines ever made. It’s kind of crazy thing to make a car this way. It’s never been done before.
“When we were trying to figure this out, there were six major casting manufacturers in the world. We called six. Five said’ no,’ one said ‘maybe.’ I was like ‘that sounds like a yes.’ So with a lot of effort and great ideas from the team, we’ve made the world’s biggest casting machine work very efficiently to create and radically simplify the manufacturing of the car,” Musk said.
A look at Bühler’s official website shows that the company is also developing giant die-casting machines that offer the highest productivity.
“Automotive manufacturers are currently rethinking production in many ways. Our Carat series enables them to put their ideas of even larger parts into reality, and we support our customers in developing the processes to do so. We see a huge increase in the demand for ever larger machines. With our Carat 840 and Carat 920 we can offer our customers solutions for large structural parts with complex geometries and new body-in-white parts,” Cornel Mendler, Managing Director of Bühler Die Casting, said.
Bühler’s Carat 840 and Carat 920 machines feature locking forces of up to 92,000 kilonewtons (kN). They are also designed to produce as little scrap as possible. “Bühler’s vision for the future of the die casting industry is: 0% scrap, 40% less cycle time, and 24/7 uptime. Advancing further towards this vision is even more important: The larger the castings, the bigger the lever to minimize production costs by reducing scrap, cycle time and increasing uptime of the die-casting system. The design of the Carat 840 and Carat 920 positively impact the quality of these complex, thin-walled parts which require an extremely powerful and accurate injection unit and a homogenous locking force application,” the company wrote in a press release.
Don’t hesitate to contact us with news tips. Just send a message to simon@teslarati.com to give us a heads up.
News
Tesla begins Robotaxi certification push in Arizona: report
Tesla seems serious about expanding its Robotaxi service to several states in the coming months.
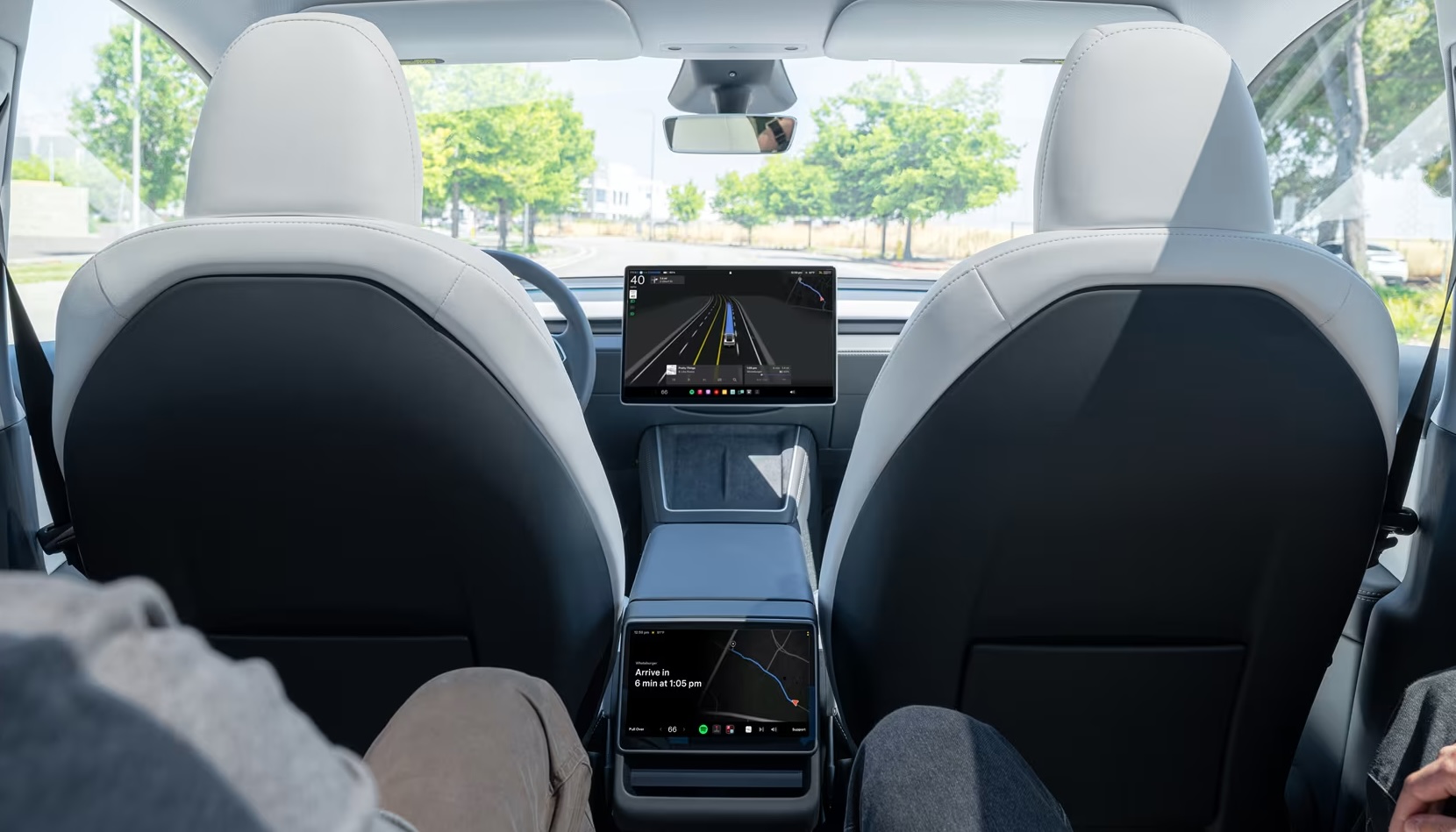
Tesla has initiated discussions with Arizona transportation regulators to certify its driverless Robotaxi service in the state, as per a recent report from Bloomberg News. The move follows Tesla’s launch of its Robotaxi pilot program in Austin, Texas, as well as CEO Elon Musk’s recent comments about the service’s expansion in the Bay Area.
The Arizona Department of Transportation confirmed to Bloomberg that Tesla has reached out to begin the certification process for autonomous ride-sharing operations in the state. While details remain limited, the outreach suggests that Tesla is serious about expanding its driverless Robotaxi service to several territories in the coming months.
The Arizona development comes as Tesla prepares to expand its service area in Austin this weekend, as per CEO Elon Musk in a post on X. Musk also stated that Tesla is targeting the San Francisco Bay Area as its next major market, with a potential launch “in a month or two,” pending regulatory approvals.
Tesla first launched its autonomous ride-hailing program on June 22 in Austin with a small fleet of Model Y vehicles, accompanied by a Tesla employee in the passenger seat to monitor safety. While still classified as a test, Musk has said the program will expand to about 1,000 vehicles in the coming months. Tesla will later upgrade its Robotaxi fleet with the Cyercab, a two-seater that is designed without a steering wheel.
Sightings of Cybercab castings around the Giga Texas complex suggests that Tesla may be ramping the initial trial production of the self-driving two-seater. Tesla, for its part, has noted in the past that volume production of the Cybercab is expected to start sometime next year.
In California, Tesla has already applied for a transportation charter-party carrier permit from the state’s Public Utilities Commission. The company is reportedly taking a phased approach to operating in California, with the Robotaxi service starting with pre-arranged rides for employees in vehicles with safety drivers.
News
Tesla sets November 6 date for 2025 Annual Shareholder Meeting
The automaker announced the date on Thursday in a Form 8-K.
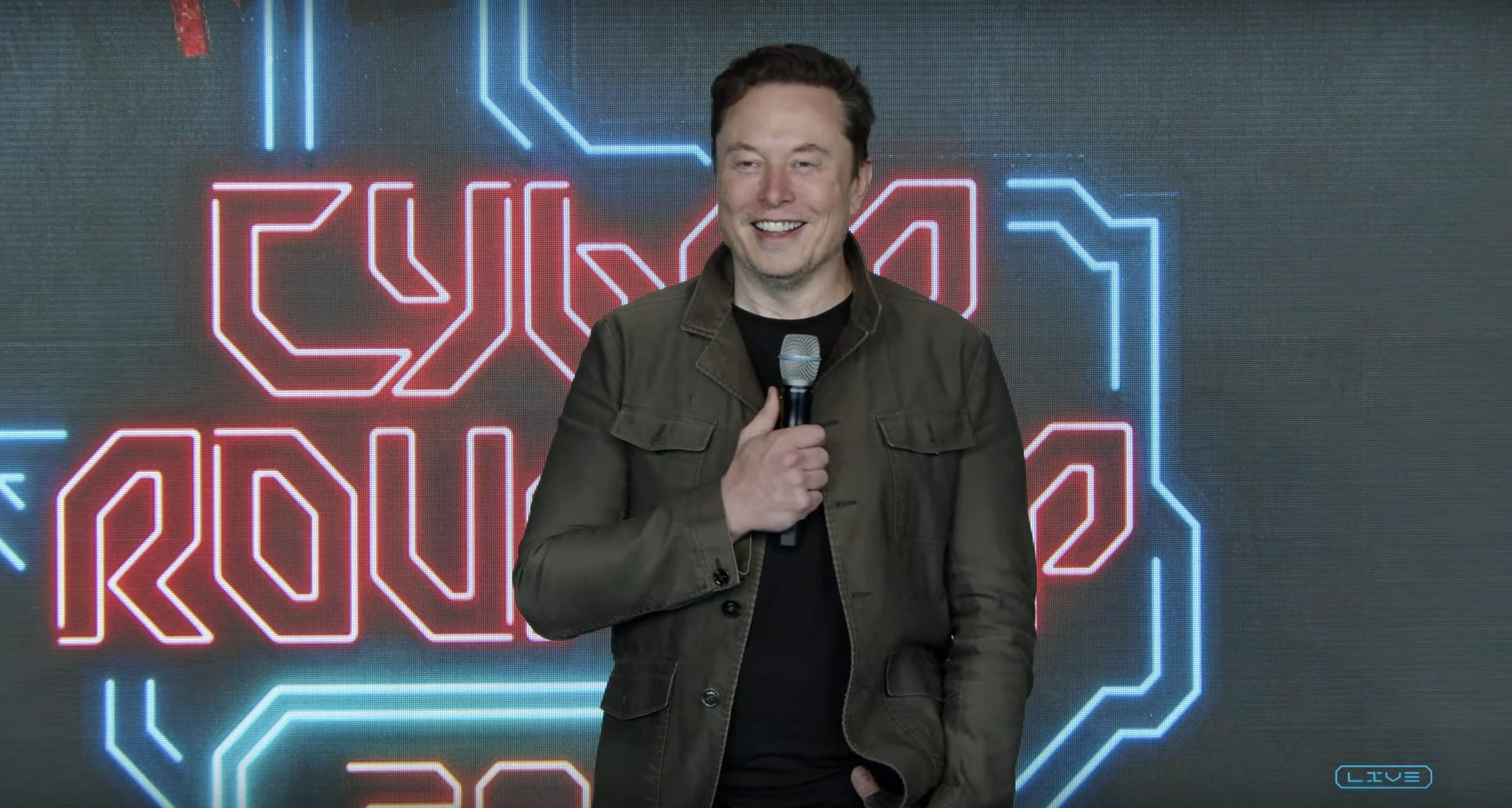
Tesla has scheduled its 2025 annual shareholder meeting for November 6, addressing investor concerns that the company was nearing a legal deadline to hold the event.
The automaker announced the date on Thursday in a Form 8-K submitted to the United States Securities and Exchange Commission (SEC). The company also listed a new proposal submission deadline of July 31 for items to be included in the proxy statement.
Tesla’s announcement followed calls from a group of 27 shareholders, including the leaders of large public pension funds, which urged Tesla’s board to formally set the meeting date, as noted in a report from The Wall Street Journal.
The group noted that under Texas law, where Tesla is now incorporated, companies must hold annual meetings within 13 months of the last one if requested by shareholders. Tesla’s previous annual shareholder meeting was held on June 13, 2024, which placed the July 13 deadline in focus.
Tesla originally stated in its 2024 annual report that it would file its proxy statement by the end of April. However, an amended filing on April 30 indicated that the Board of Directors had not yet finalized a meeting date, at least at the time.
The April filing also confirmed that Tesla’s board had formed a special committee to evaluate certain matters related to CEO Elon Musk’s compensation plan. Musk’s CEO performance award remains at the center of a lengthy legal dispute in Delaware, Tesla’s former state of incorporation.
Due to the aftermath of Musk’s legal dispute about his compensation plan in Delaware, he has not been paid for his work at Tesla for several years. Musk, for his part, has noted that he is more concerned about his voting stake in Tesla than his actual salary.
At last year’s annual meeting, TSLA shareholders voted to reapprove Elon Musk’s compensation plan and ratified Tesla’s decision to relocate its legal domicile from Delaware to Texas.
Elon Musk
Grok coming to Tesla vehicles next week “at the latest:” Elon Musk
Grok’s rollout to Tesla vehicles is expected to begin next week at the latest.
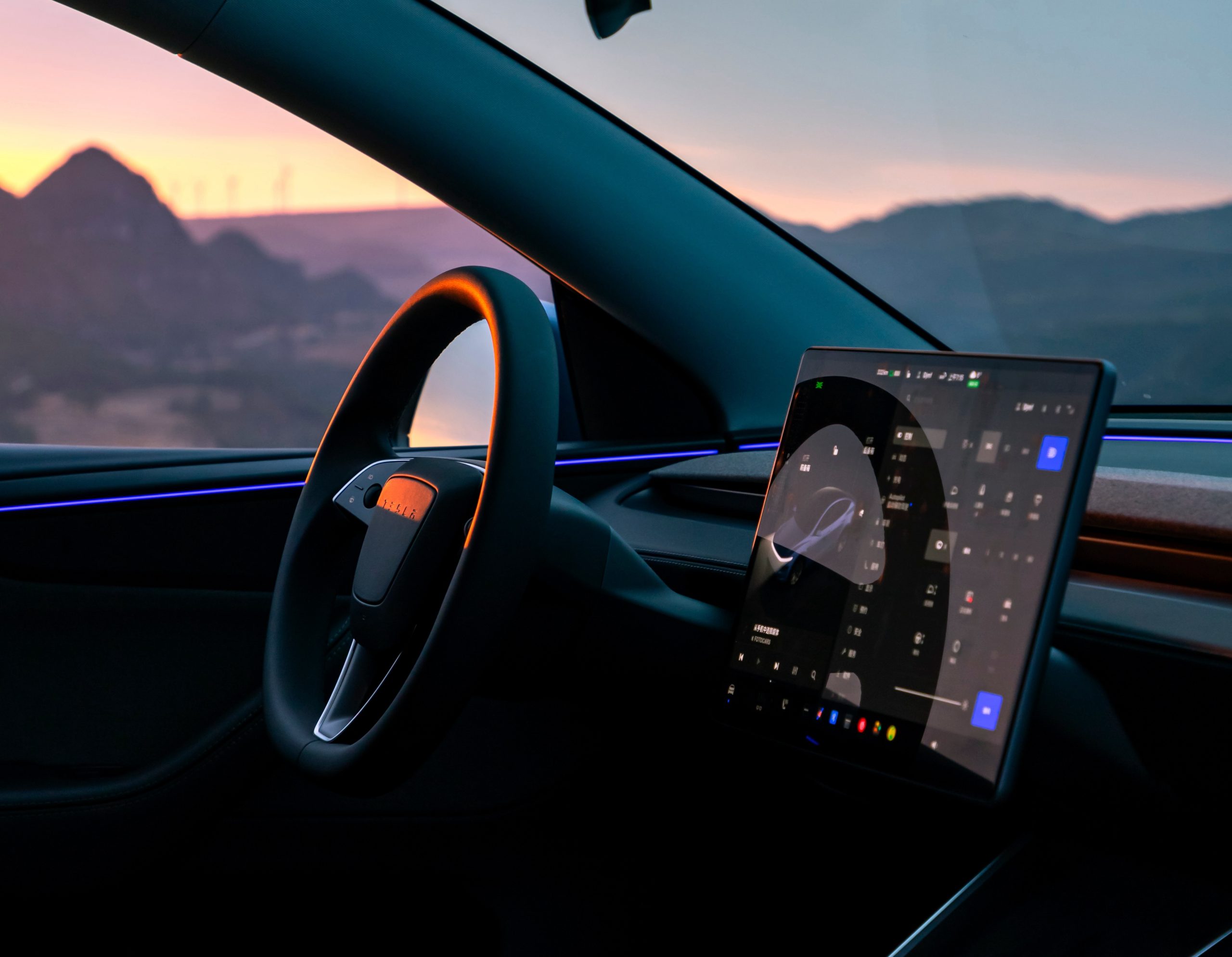
Elon Musk announced on Thursday that Grok, the large language model developed by his startup xAI, will soon be available in Tesla vehicles. Grok’s rollout to Tesla vehicles is expected to begin next week at the latest, further deepening the ties between the two Elon Musk-led companies.
Tesla–xAI synergy
Musk confirmed the news on X shortly after livestreaming the release of Grok 4, xAI’s latest large language model. “Grok is coming to Tesla vehicles very soon. Next week at the latest,” Musk wrote in a post on social media platform X.
During the livestream, Musk and several members of the xAI team highlighted several upgrades to Grok 4’s voice capabilities and performance metrics, positioning the LLM as competitive with top-tier models from OpenAI and Google.
The in-vehicle integration of Grok marks a new chapter in Tesla’s AI development. While Tesla has long relied on in-house systems for autonomous driving and energy optimization, Grok’s integration would introduce conversational AI directly into its vehicles’ user experience. This integration could potentially improve customer interaction inside Tesla vehicles.
xAI and Tesla’s collaborative footprint
Grok’s upcoming rollout to Tesla vehicles adds to a growing business relationship between Tesla and xAI. Earlier this year, Tesla disclosed that it generated $198.3 million in revenue from commercial, consulting, and support agreements with xAI, as noted in a report from Bloomberg News. A large portion of that amount, however, came from the sale of Megapack energy storage systems to the artificial intelligence startup.
In July 2023, Musk polled X users about whether Tesla should invest $5 billion in xAI. While no formal investment has been made so far, 68% of poll participants voted yes, and Musk has since stated that the idea would be discussed with Tesla’s board.
-
Elon Musk1 week ago
Tesla investors will be shocked by Jim Cramer’s latest assessment
-
Elon Musk3 days ago
Elon Musk confirms Grok 4 launch on July 9 with livestream event
-
Elon Musk16 hours ago
xAI launches Grok 4 with new $300/month SuperGrok Heavy subscription
-
News7 days ago
Tesla Model 3 ranks as the safest new car in Europe for 2025, per Euro NCAP tests
-
Elon Musk2 weeks ago
A Tesla just delivered itself to a customer autonomously, Elon Musk confirms
-
Elon Musk1 week ago
xAI’s Memphis data center receives air permit despite community criticism
-
Elon Musk2 weeks ago
Tesla’s Omead Afshar, known as Elon Musk’s right-hand man, leaves company: reports
-
News2 weeks ago
Xiaomi CEO congratulates Tesla on first FSD delivery: “We have to continue learning!”