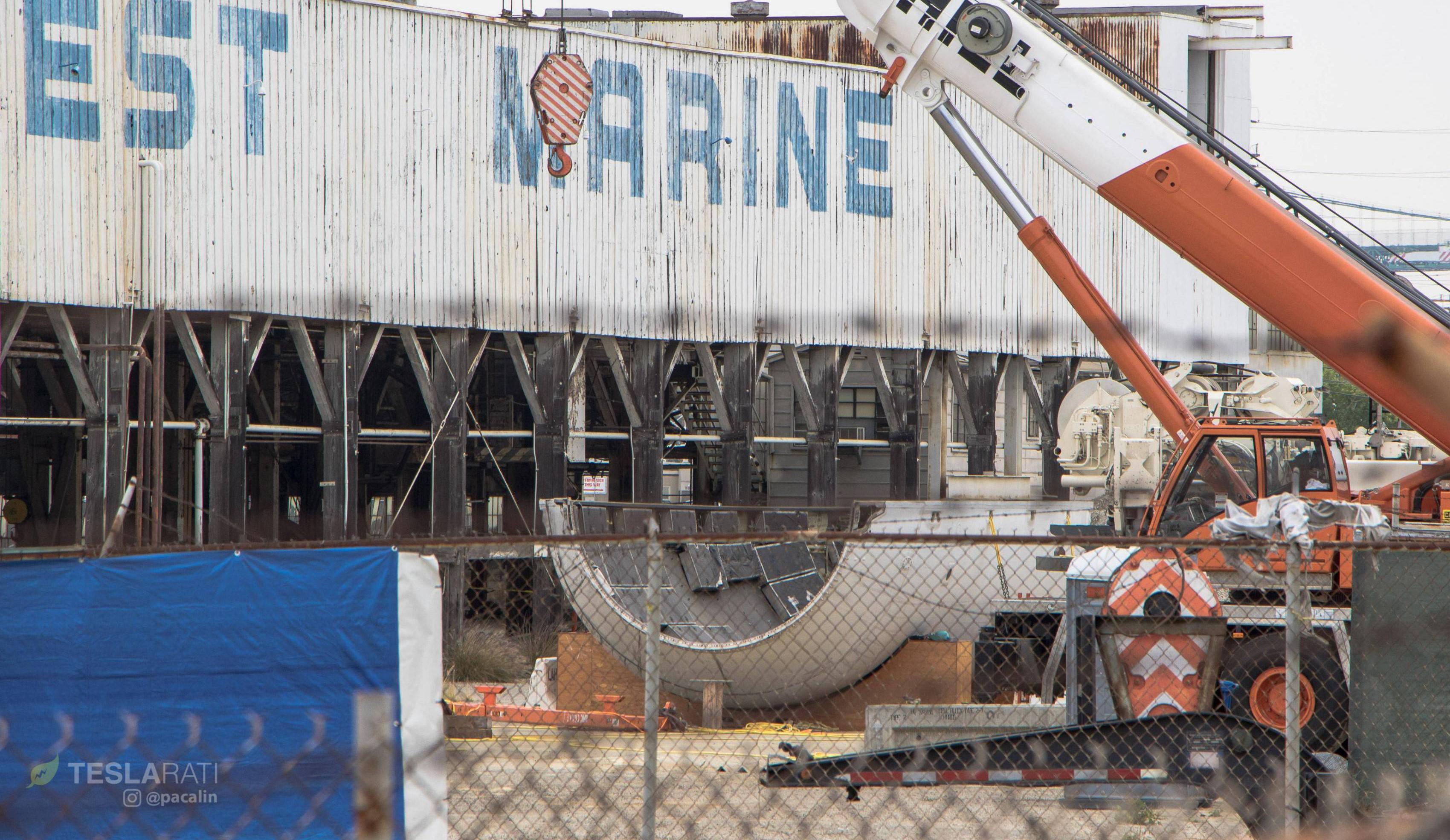
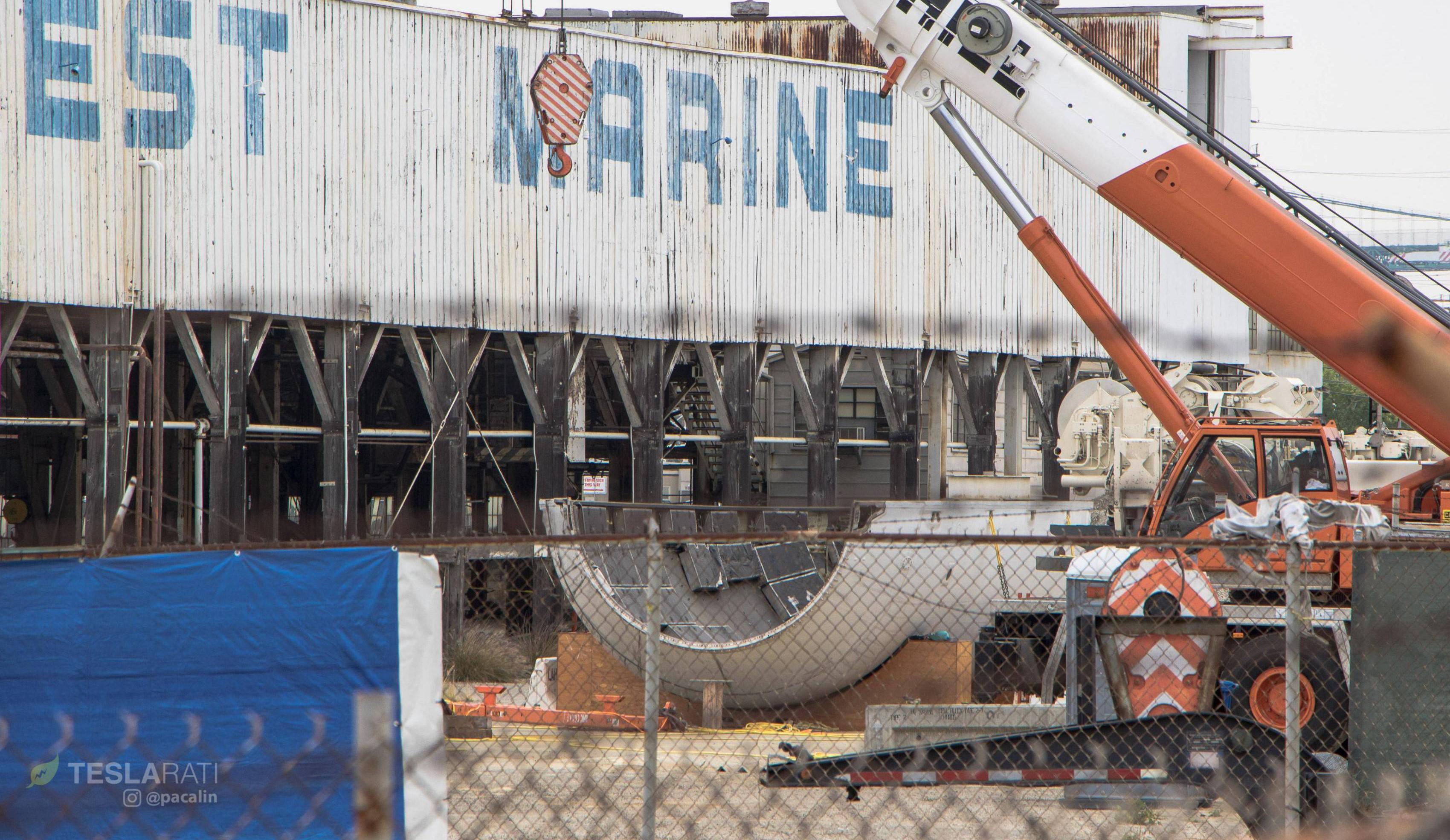
News
SpaceX ramps BFR factory construction as Mr Steven arm surgery continues
Photos taken on July 1st show that land leased by SpaceX to build the first port-located BFR factory and Falcon 9 refurbishment center is continuing to ramp initial construction work, ranging from general clean-up of the long-abandoned berth to serious foundation preparation where SpaceX’s new rocket warehouse will be built.
Previously a shipyard, the Berth 240 facility now leased by SpaceX sat abandoned for the better part of a decade, and features a number of buildings deemed historic landmarks by the city of Los Angeles. As the new tenant, SpaceX is expected to do at least a little refurbishment, with the goal of leaving the site in better shape than they found it in at the end of their 10-year lease. The company does have permission, nonetheless, to demolish one less historic building in order to make space for their planned BFR factory, the construction of which is expected to take 12-18 months for Phase 1 and another 12 or so months for Phase 2, meshing nicely with SpaceX real estate director Bruce McHugh’s estimate of “three to five years” to completion.
On the rocket recovery fleet side of things, SpaceX’s fairing-catcher Mr Steven is still stationed at Berth 240 with all major components of his previous arm assembly now fully removed and stored nearby on the dock. In June 2018, CEO Elon Musk noted on Twitter that the iconic vessel was to have its net grown by a factor of four, meaning that both its length and width would be roughly doubled.

SpaceX’s Berth 240 prospective BFR factory is chock-full of construction equipment. (Pauline Acalin)
Sitting around 400 square meters before arm removal, the new net would be closer to 1500 square meters – roughly 1.5 acres – and could nearly halve the accuracy gap that the company’s engineers need to close in order to reliably catch Falcon payload fairings, cutting 20-30 meters out of the 50 meters most separating the fairing and net at touchdown. Once SpaceX is able to close that gap and start catching fairings before they hit seawater, it should be a fairly simple process to start routinely reusing both halves of the $3 million carbon composite-aluminum honeycomb shells.
Unless they can be rapidly cycled out of the net after landing, recovering both halves may require a second net vessel like Mr Steven, and there could wind up being as many as four Mr Steven copies if the company intends to recovery both fairing halves after every launch from both their California and Florida launch pads. Recent planning on the Florida coast indicates that SpaceX expects their launch cadence to ramp up considerably with the introduction of a fleet of highly-reusable Falcon 9 Block 5 boosters, and the considerable lead-time and sluggishness inherent to manufacturing massive aerospace-grade composite structures with equally vast autoclave ovens means that payload fairings could quite quickly become a bottleneck for SpaceX’s launch business.
- SpaceX’s BFR tent and mandrel, caught on April 14th. (Pauline Acalin)
- Mr Steven out and about with a recovered but unreusable fairing half in May 2018, presumably for some sort of practice. (Pauline Acalin)
While such a bottleneck is far from insurmountable, dramatically expanding Falcon 9 composite component production now would presumably be an inconvenience for SpaceX at a time where they would much rather be focusing internal investments on their next-generation launch vehicle, known as BFR. That rocket is understood to be in the late stages of design and is quickly entering into a more advanced stage of concerted full-scale prototype testing and refinement as SpaceX accumulates invaluable data from hands-on R&D.
Follow us for live updates, peeks behind the scenes, and photos from Teslarati’s East and West Coast photographers.
Teslarati – Instagram – Twitter
Tom Cross – Twitter
Pauline Acalin – Twitter
Eric Ralph – Twitter
News
Tesla begins Robotaxi certification push in Arizona: report
Tesla seems serious about expanding its Robotaxi service to several states in the coming months.
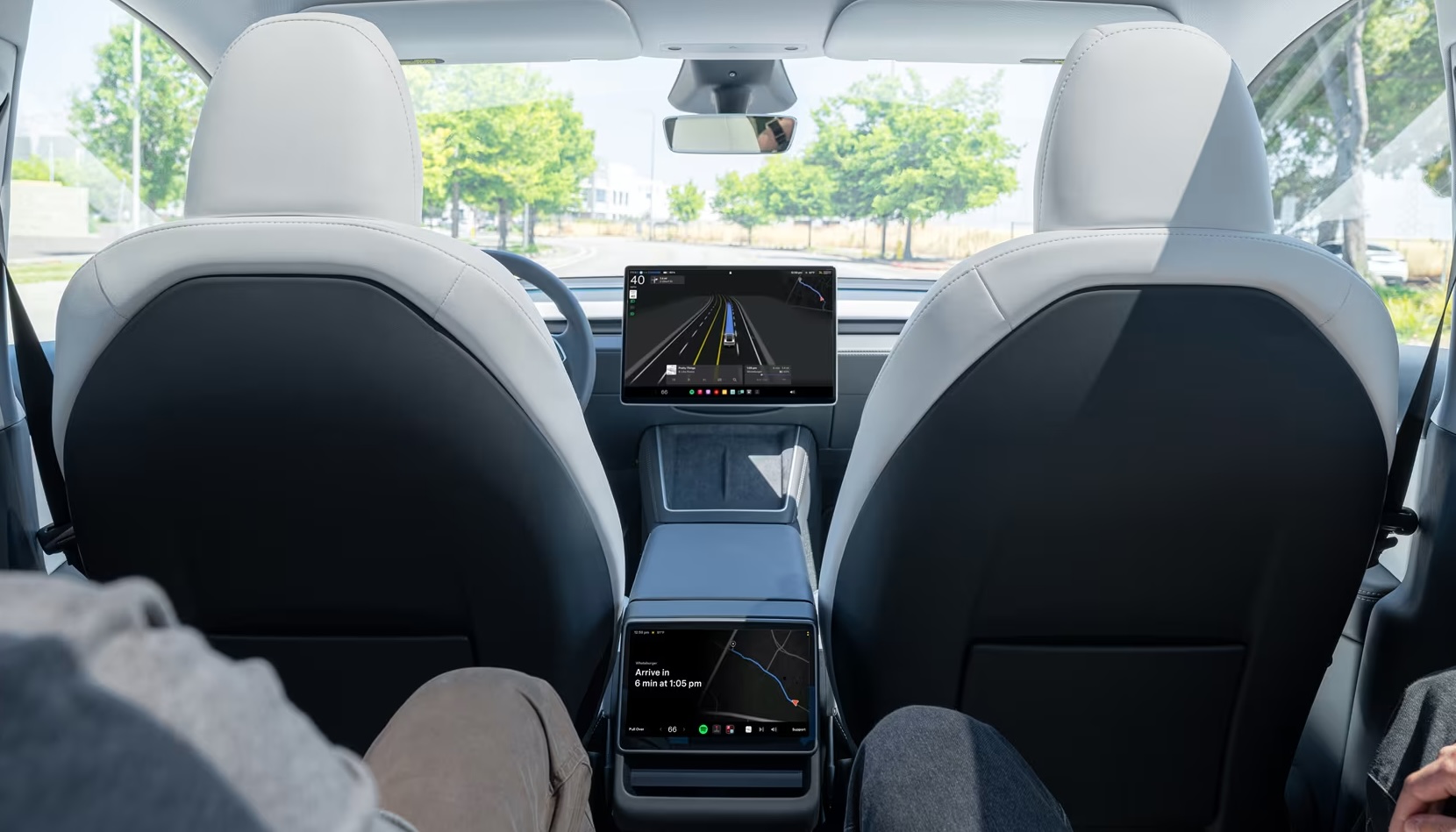
Tesla has initiated discussions with Arizona transportation regulators to certify its driverless Robotaxi service in the state, as per a recent report from Bloomberg News. The move follows Tesla’s launch of its Robotaxi pilot program in Austin, Texas, as well as CEO Elon Musk’s recent comments about the service’s expansion in the Bay Area.
The Arizona Department of Transportation confirmed to Bloomberg that Tesla has reached out to begin the certification process for autonomous ride-sharing operations in the state. While details remain limited, the outreach suggests that Tesla is serious about expanding its driverless Robotaxi service to several territories in the coming months.
The Arizona development comes as Tesla prepares to expand its service area in Austin this weekend, as per CEO Elon Musk in a post on X. Musk also stated that Tesla is targeting the San Francisco Bay Area as its next major market, with a potential launch “in a month or two,” pending regulatory approvals.
Tesla first launched its autonomous ride-hailing program on June 22 in Austin with a small fleet of Model Y vehicles, accompanied by a Tesla employee in the passenger seat to monitor safety. While still classified as a test, Musk has said the program will expand to about 1,000 vehicles in the coming months. Tesla will later upgrade its Robotaxi fleet with the Cyercab, a two-seater that is designed without a steering wheel.
Sightings of Cybercab castings around the Giga Texas complex suggests that Tesla may be ramping the initial trial production of the self-driving two-seater. Tesla, for its part, has noted in the past that volume production of the Cybercab is expected to start sometime next year.
In California, Tesla has already applied for a transportation charter-party carrier permit from the state’s Public Utilities Commission. The company is reportedly taking a phased approach to operating in California, with the Robotaxi service starting with pre-arranged rides for employees in vehicles with safety drivers.
News
Tesla sets November 6 date for 2025 Annual Shareholder Meeting
The automaker announced the date on Thursday in a Form 8-K.
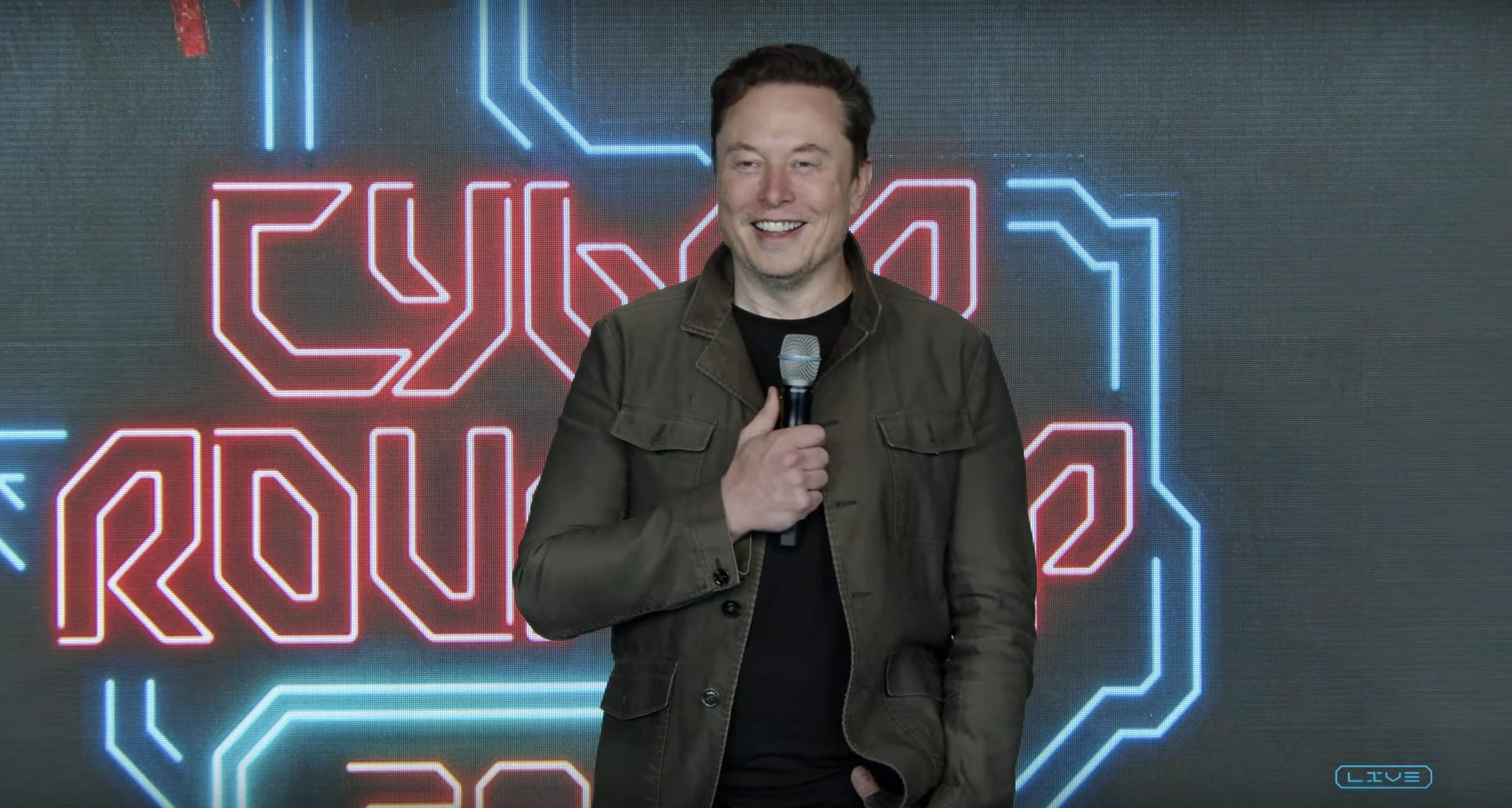
Tesla has scheduled its 2025 annual shareholder meeting for November 6, addressing investor concerns that the company was nearing a legal deadline to hold the event.
The automaker announced the date on Thursday in a Form 8-K submitted to the United States Securities and Exchange Commission (SEC). The company also listed a new proposal submission deadline of July 31 for items to be included in the proxy statement.
Tesla’s announcement followed calls from a group of 27 shareholders, including the leaders of large public pension funds, which urged Tesla’s board to formally set the meeting date, as noted in a report from The Wall Street Journal.
The group noted that under Texas law, where Tesla is now incorporated, companies must hold annual meetings within 13 months of the last one if requested by shareholders. Tesla’s previous annual shareholder meeting was held on June 13, 2024, which placed the July 13 deadline in focus.
Tesla originally stated in its 2024 annual report that it would file its proxy statement by the end of April. However, an amended filing on April 30 indicated that the Board of Directors had not yet finalized a meeting date, at least at the time.
The April filing also confirmed that Tesla’s board had formed a special committee to evaluate certain matters related to CEO Elon Musk’s compensation plan. Musk’s CEO performance award remains at the center of a lengthy legal dispute in Delaware, Tesla’s former state of incorporation.
Due to the aftermath of Musk’s legal dispute about his compensation plan in Delaware, he has not been paid for his work at Tesla for several years. Musk, for his part, has noted that he is more concerned about his voting stake in Tesla than his actual salary.
At last year’s annual meeting, TSLA shareholders voted to reapprove Elon Musk’s compensation plan and ratified Tesla’s decision to relocate its legal domicile from Delaware to Texas.
Elon Musk
Grok coming to Tesla vehicles next week “at the latest:” Elon Musk
Grok’s rollout to Tesla vehicles is expected to begin next week at the latest.
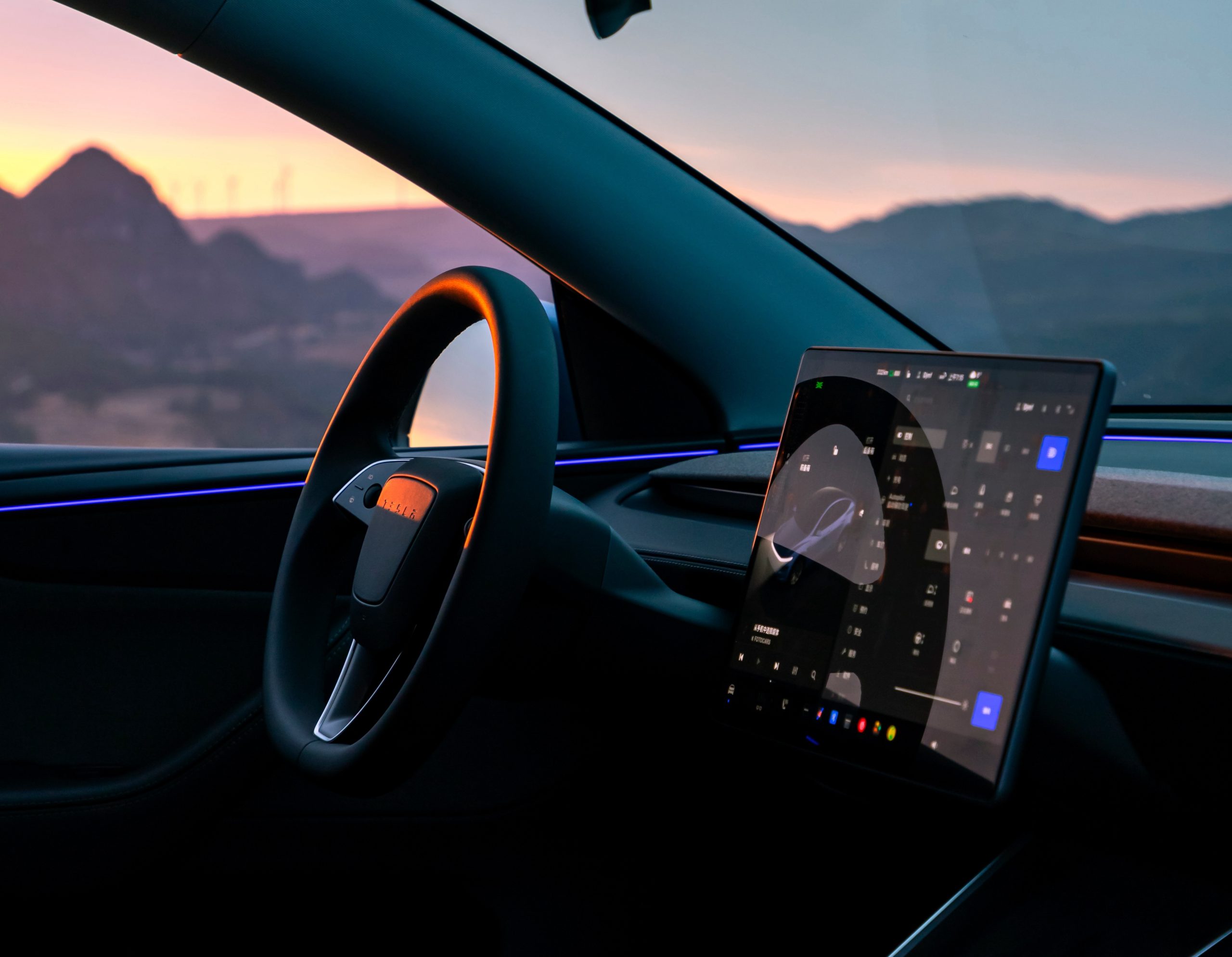
Elon Musk announced on Thursday that Grok, the large language model developed by his startup xAI, will soon be available in Tesla vehicles. Grok’s rollout to Tesla vehicles is expected to begin next week at the latest, further deepening the ties between the two Elon Musk-led companies.
Tesla–xAI synergy
Musk confirmed the news on X shortly after livestreaming the release of Grok 4, xAI’s latest large language model. “Grok is coming to Tesla vehicles very soon. Next week at the latest,” Musk wrote in a post on social media platform X.
During the livestream, Musk and several members of the xAI team highlighted several upgrades to Grok 4’s voice capabilities and performance metrics, positioning the LLM as competitive with top-tier models from OpenAI and Google.
The in-vehicle integration of Grok marks a new chapter in Tesla’s AI development. While Tesla has long relied on in-house systems for autonomous driving and energy optimization, Grok’s integration would introduce conversational AI directly into its vehicles’ user experience. This integration could potentially improve customer interaction inside Tesla vehicles.
xAI and Tesla’s collaborative footprint
Grok’s upcoming rollout to Tesla vehicles adds to a growing business relationship between Tesla and xAI. Earlier this year, Tesla disclosed that it generated $198.3 million in revenue from commercial, consulting, and support agreements with xAI, as noted in a report from Bloomberg News. A large portion of that amount, however, came from the sale of Megapack energy storage systems to the artificial intelligence startup.
In July 2023, Musk polled X users about whether Tesla should invest $5 billion in xAI. While no formal investment has been made so far, 68% of poll participants voted yes, and Musk has since stated that the idea would be discussed with Tesla’s board.
-
Elon Musk1 week ago
Tesla investors will be shocked by Jim Cramer’s latest assessment
-
Elon Musk20 hours ago
xAI launches Grok 4 with new $300/month SuperGrok Heavy subscription
-
Elon Musk3 days ago
Elon Musk confirms Grok 4 launch on July 9 with livestream event
-
News7 days ago
Tesla Model 3 ranks as the safest new car in Europe for 2025, per Euro NCAP tests
-
Elon Musk2 weeks ago
A Tesla just delivered itself to a customer autonomously, Elon Musk confirms
-
Elon Musk1 week ago
xAI’s Memphis data center receives air permit despite community criticism
-
Elon Musk2 weeks ago
Tesla’s Omead Afshar, known as Elon Musk’s right-hand man, leaves company: reports
-
News2 weeks ago
Xiaomi CEO congratulates Tesla on first FSD delivery: “We have to continue learning!”