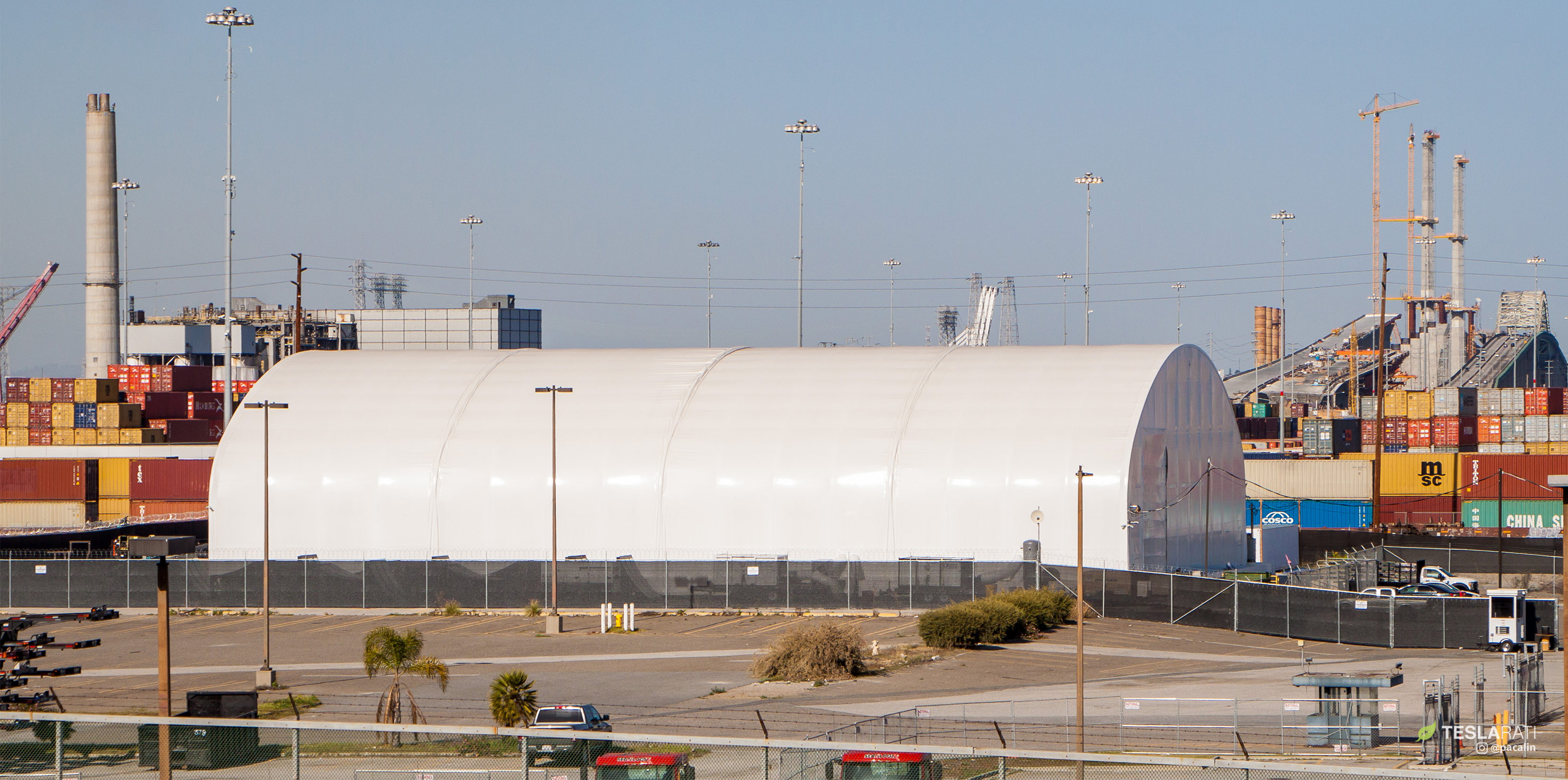
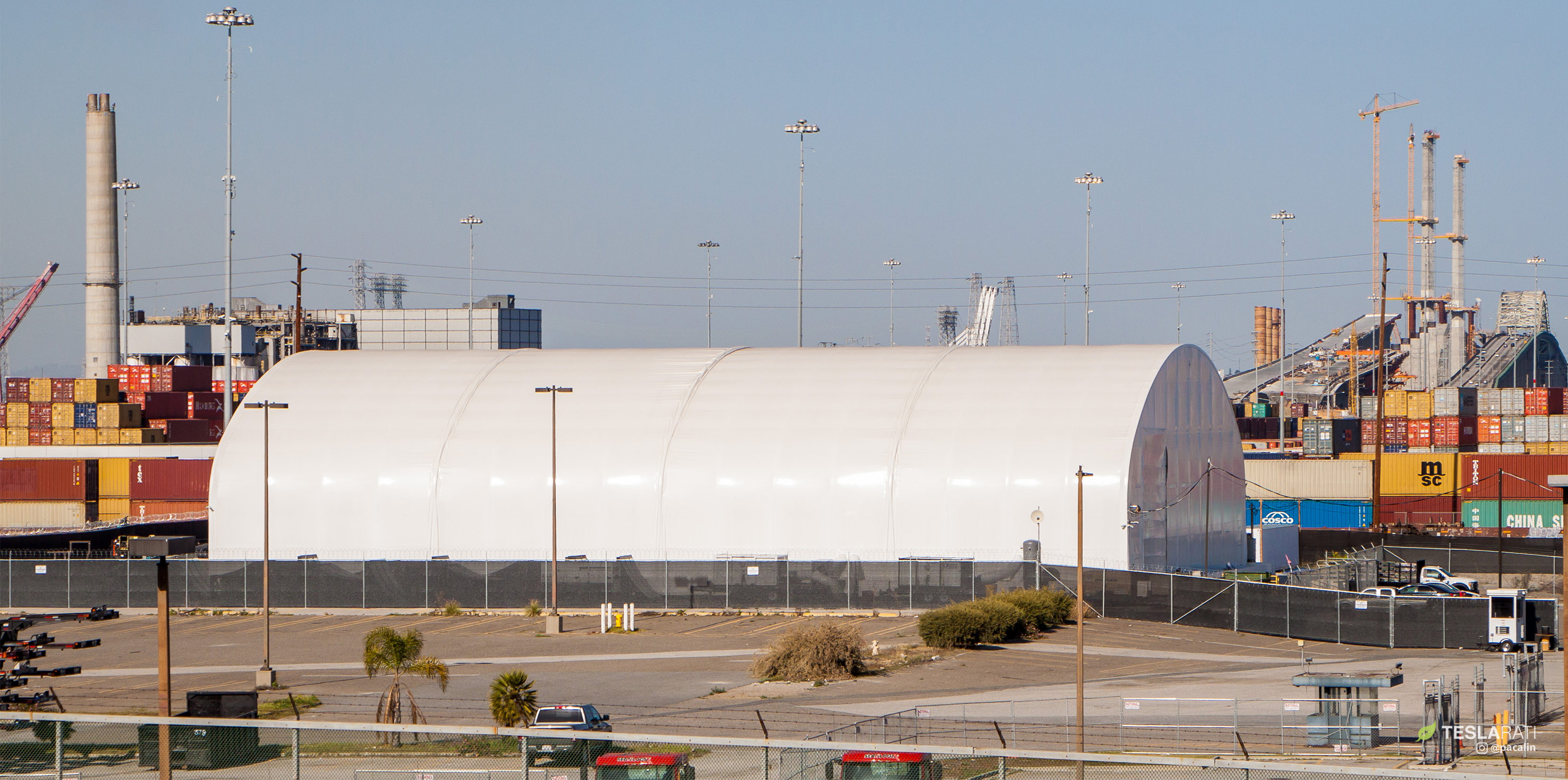
News
SpaceX’s BFR Mars rocket tooling makes rare appearance in LA Port tent
After nearly ten weeks hidden inside the company’s Port of Los Angeles tent, SpaceX’s main BFR manufacturing tooling made another brief appearance on July 1, showing off a new support structure and equipment that enables the entire device to spin and easily lay down layers of carbon fiber to construct the first Mars rocket prototype propellant tanks.
Based on photos taken of the large composite production equipment – known as a mandrel – in April 2018, as well as a photo released by CEO Elon Musk around the same time, it appears either that major modifications were made in the past two months or that an entirely new tool has been delivered to the dockside tent over the same period of time. Given that the shipment of the first hardware and its arrival at Port LA itself managed to slip beneath the eyes of local observers, there certainly is no reason that the same thing couldn’t be repeated. The mandrels and other production tooling SpaceX has acquired from Ascent Aerospace are likely shipped to their final destination disassembled.
- SpaceX’s first major BFR and BFS fabrication tooling, likely being stored temporarily in a tent at Port of San Pedro. Note the tent framework at the top. (Elon Musk)
- Images corroborated the location of the giant mandrel tool inside the Port of San Pedro tent, April 2018. (Pauline Acalin)
- SpaceX may well already be fabricating propellant tanks and structural components for the first Mars spaceship prototype in a giant tent at Port of San Pedro. July 1st. (Pauline Acalin)
- BFR prepares for launch as the sun sets over the upgraded LC-39A, built off a concept of the future modifications included in SpaceX’s 2016 and 2017 video updates. At the request of a friend, artist David Romax put together a truly jaw-dropping collection of concept art featuring SpaceX’s BFR rocket and its Cargo and Crew spaceships. (Gravitation Innovation/David Romax)
- At the request of a friend, artist David Romax put together a truly jaw-dropping collection of concept art featuring SpaceX’s BFR rocket and its Cargo and Crew spaceships. (Gravitation Innovation/David Romax)
More relevant, however, is the probability that SpaceX will need more than a single mandrel to produce BFR ship and booster prototypes on anything faster than geological timescales. In fact, if (very) rough size estimates produced from Musk’s shared photo are correct, two (or even three) 16-meter long mandrels would almost perfectly mesh to create the Spaceship’s own massive 48-meter length, although the reality would be far more complex than a simple feat of 1+1+1 thanks to the complex front and rear shapes of the BFR upper stage.
Two mandrels would also ensure that SpaceX is able to rapidly prototype, test, and re-prototype BFR hardware while the company refines designs and moves into full-scale flight hardware production and flight testing, at least at the prototype phase. Recently, several BFR and Mars rocket-focused job postings were spotted with specific requirements related to composite-composite and composite-metal joining, a young but rapidly advancing subset of skills necessary to efficiently and economically produce massive structures primarily made up of composite materials.
- Tons of industrial equipment is now installed outside the tent, ranging from HVAC, power, and unknown fluid hookups, as well as an aerospace-grade Quincy air compressor. July 1. (Pauline Acalin)
- Unidentified tooling stored outside of the BFR tent, May 2018. These are most likely stands for completed composite parts and mold structures for composite production. (Pauline Acalin)
- April 2018. (Pauline Acalin)
Boeing’s 787 program, composed of 50% composites, is a strong example with each fuselage broken into a number of smaller segments that are later joined together with tolerances on the order of 1/5000 of an inch to avoid damage to the composite sandwich structures within. Long-lived, reliable, and resilient segmented composite structures are thus well-established as a viable solution, although Boeing is one of precious few entities able to lay claim to such mass-production successes. Ultimately, SpaceX does not need to start from scratch (even if they could, or still may) in order to successfully build the ultra-reusable Mars rocket they aspire to.
- Shown is the forward fuselage of the 787 on a mandrel for composite weaving and layup.(Boeing)
- Artist David Romax’s jaw-dropping rendition of a BFR burning to Mars orbit. The craft’s various curves and hull complexities will likely rely on cutting-edge composite joining tech to function. (Gravitation Innovation)
Follow us for live updates, peeks behind the scenes, and photos from Teslarati’s East and West Coast photographers.
Teslarati – Instagram – Twitter
Tom Cross – Twitter
Pauline Acalin – Twitter
Eric Ralph – Twitter
Elon Musk
Tesla reveals it is using AI to make factories more sustainable: here’s how
Tesla is using AI in its Gigafactory Nevada factory to improve HVAC efficiency.
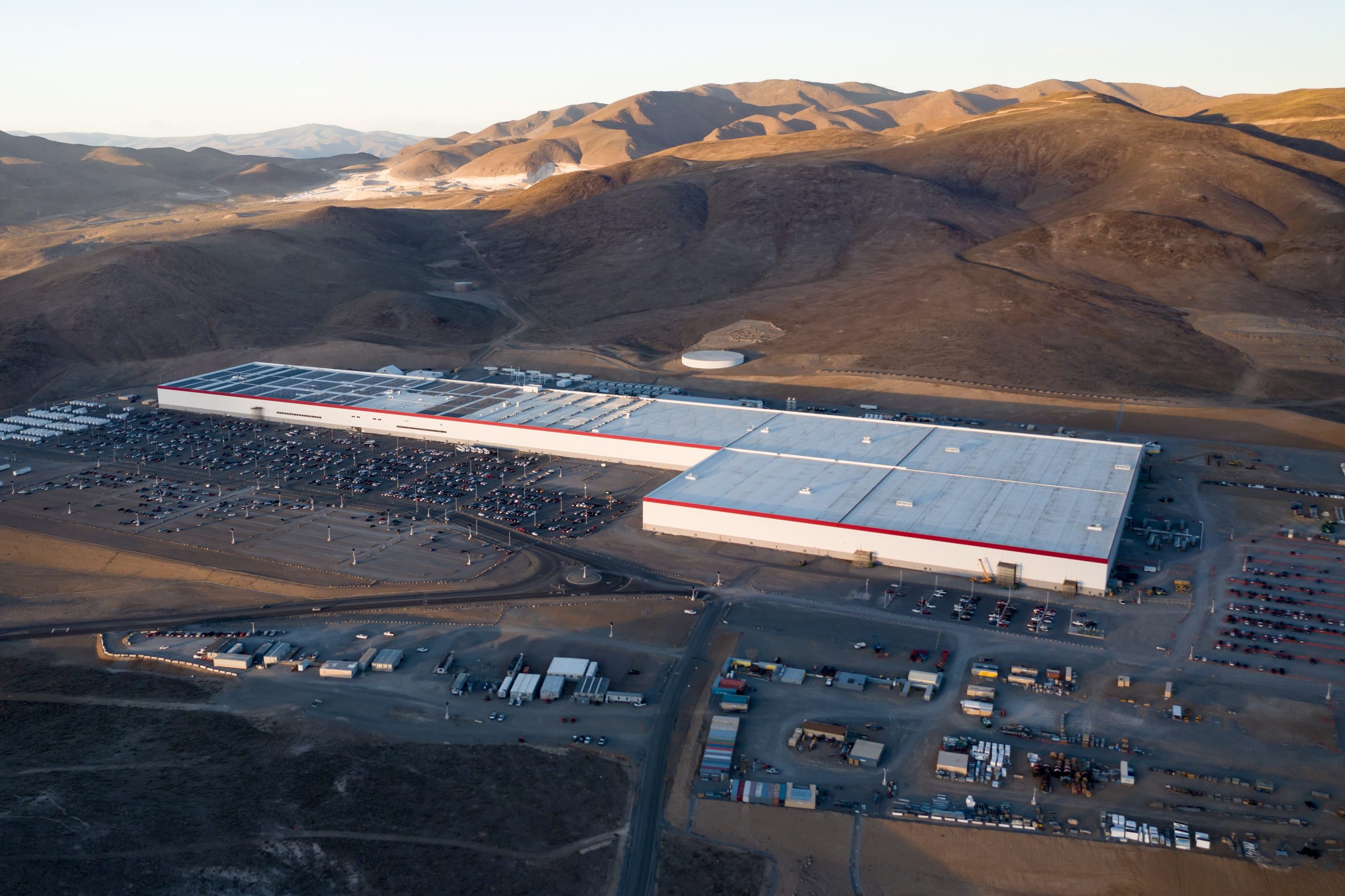
Tesla has revealed in its Extended Impact Report for 2024 that it is using Artificial Intelligence (AI) to enable its factories to be more sustainable. One example it used was its achievement of managing “the majority of the HVAC infrastructure at Gigafactory Nevada is now AI-controlled” last year.
In a commitment to becoming more efficient and making its production as eco-friendly as possible, Tesla has been working for years to find solutions to reduce energy consumption in its factories.
For example, in 2023, Tesla implemented optimization controls in the plastics and paint shops located at Gigafactory Texas, which increased the efficiency of natural gas consumption. Tesla plans to phase out natural gas use across its factories eventually, but for now, it prioritizes work to reduce emissions from that energy source specifically.
It also uses Hygrometric Control Logic for Air Handling Units at Giafactory Berlin, resulting in 17,000 MWh in energy savings each year. At Gigafactory Nevada, Tesla saves 9.5 GWh of energy through the use of N-Methylpyrrolidone refineries when extracting critical raw material.
Perhaps the most interesting way Tesla is conserving energy is through the use of AI at Gigafactory Nevada, as it describes its use of AI to reduce energy demand:
“In 2023, AI Control for HVAC was expanded from Nevada and Texas to now include our Berlin-Brandenburg and Fremont factories. AI Control policy enables HVAC systems within each factory to work together to process sensor data, model factory dynamics, and apply control actions that safely minimize the energy required to support production. In 2024, this system achieved two milestones: the majority of HVAC infrastructure at Gigafactory Nevada is now AI-controlled, reducing fan and thermal energy demand; and the AI algorithm was extended to manage entire chiller plants, creating a closed-loop control system that optimizes both chilled water consumption and the energy required for its generation, all while maintaining factory conditions.”
Tesla utilizes AI Control “primarily on systems that heat or cool critical factory production spaces and equipment.” AI Control communicates with the preexisting standard control logic of each system, and any issues can be resolved by quickly reverting back to standard control. There were none in 2024.
Tesla says that it is utilizing AI to drive impact at its factories, and it has proven to be a valuable tool in reducing energy consumption at one of its facilities.
Elon Musk
Tesla analysts believe Musk and Trump feud will pass
Tesla CEO Elon Musk and U.S. President Donald Trump’s feud shall pass, several bulls say.
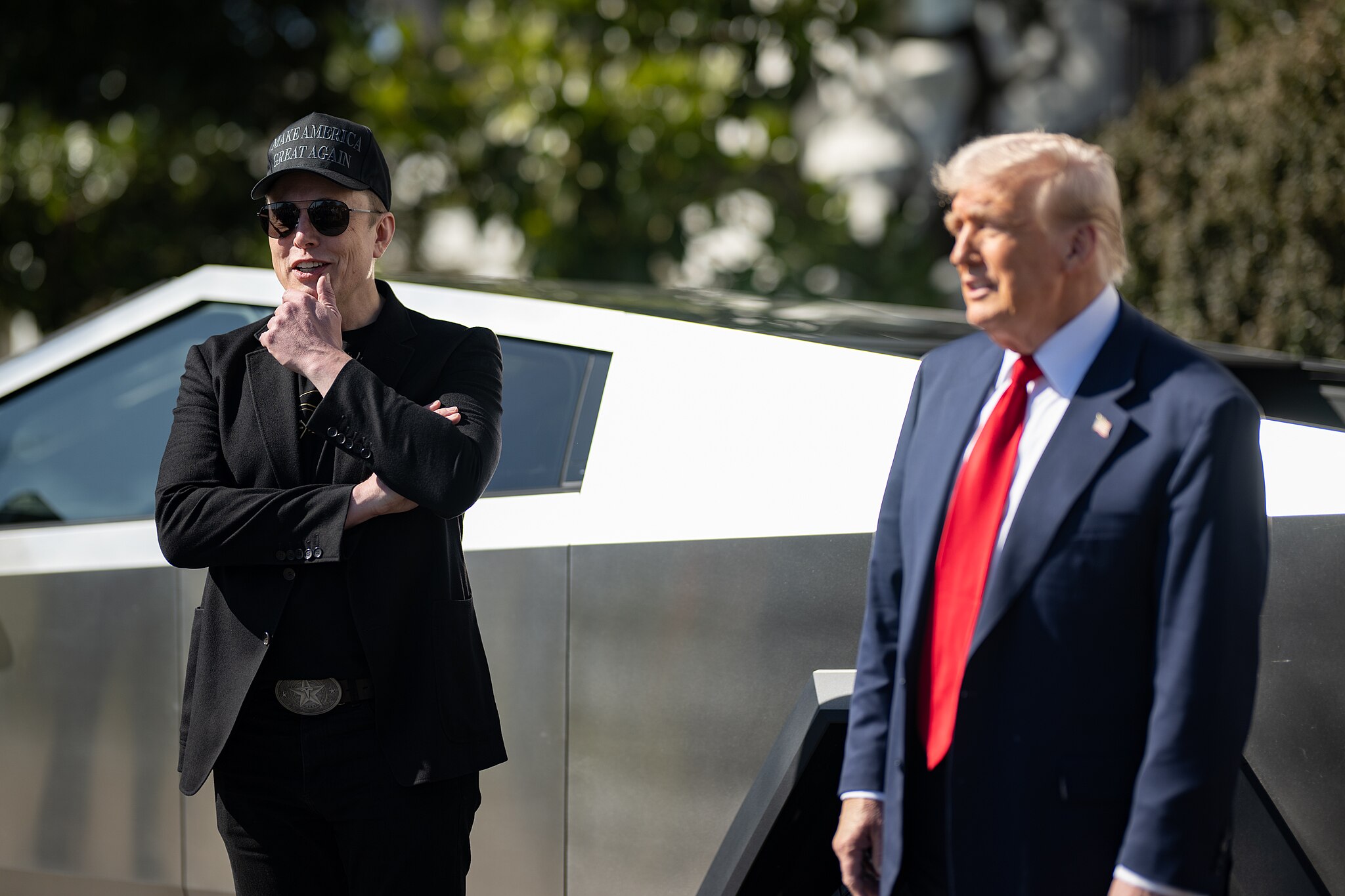
Tesla analysts are breaking down the current feud between CEO Elon Musk and U.S. President Donald Trump, as the two continue to disagree on the “Big Beautiful Bill” and its impact on the country’s national debt.
Musk, who headed the Department of Government Efficiency (DOGE) under the Trump Administration, left his post in May. Soon thereafter, he and President Trump entered a very public and verbal disagreement, where things turned sour. They reconciled to an extent, and things seemed to be in the past.
However, the second disagreement between the two started on Monday, as Musk continued to push back on the “Big Beautiful Bill” that the Trump administration is attempting to sign into law. It would, by Musk’s estimation, increase spending and reverse the work DOGE did to trim the deficit.
Every member of Congress who campaigned on reducing government spending and then immediately voted for the biggest debt increase in history should hang their head in shame!
And they will lose their primary next year if it is the last thing I do on this Earth.
— Elon Musk (@elonmusk) June 30, 2025
President Trump has hinted that DOGE could be “the monster” that “eats Elon,” threatening to end the subsidies that SpaceX and Tesla receive. Musk has not been opposed to ending government subsidies for companies, including his own, as long as they are all abolished.
How Tesla could benefit from the ‘Big Beautiful Bill’ that axes EV subsidies
Despite this contentious back-and-forth between the two, analysts are sharing their opinions now, and a few of the more bullish Tesla observers are convinced that this feud will pass, Trump and Musk will resolve their differences as they have before, and things will return to normal.
ARK Invest’s Cathie Wood said this morning that the feud between Musk and Trump is another example of “this too shall pass:”
BREAKING: CATHIE WOOD SAYS — ELON AND TRUMP FEUD “WILL PASS” 👀 $TSLA
She remains bullish ! pic.twitter.com/w5rW2gfCkx
— TheSonOfWalkley (@TheSonOfWalkley) July 1, 2025
Additionally, Wedbush’s Dan Ives, in a note to investors this morning, said that the situation “will settle:”
“We believe this situation will settle and at the end of the day Musk needs Trump and Trump needs Musk given the AI Arms Race going on between the US and China. The jabs between Musk and Trump will continue as the Budget rolls through Congress but Tesla investors want Musk to focus on driving Tesla and stop this political angle…which has turned into a life of its own in a roller coaster ride since the November elections.”
Tesla shares are down about 5 percent at 3:10 p.m. on the East Coast.
Elon Musk
Tesla scrambles after Musk sidekick exit, CEO takes over sales
Tesla CEO Elon Musk is reportedly overseeing sales in North America and Europe, Bloomberg reports.
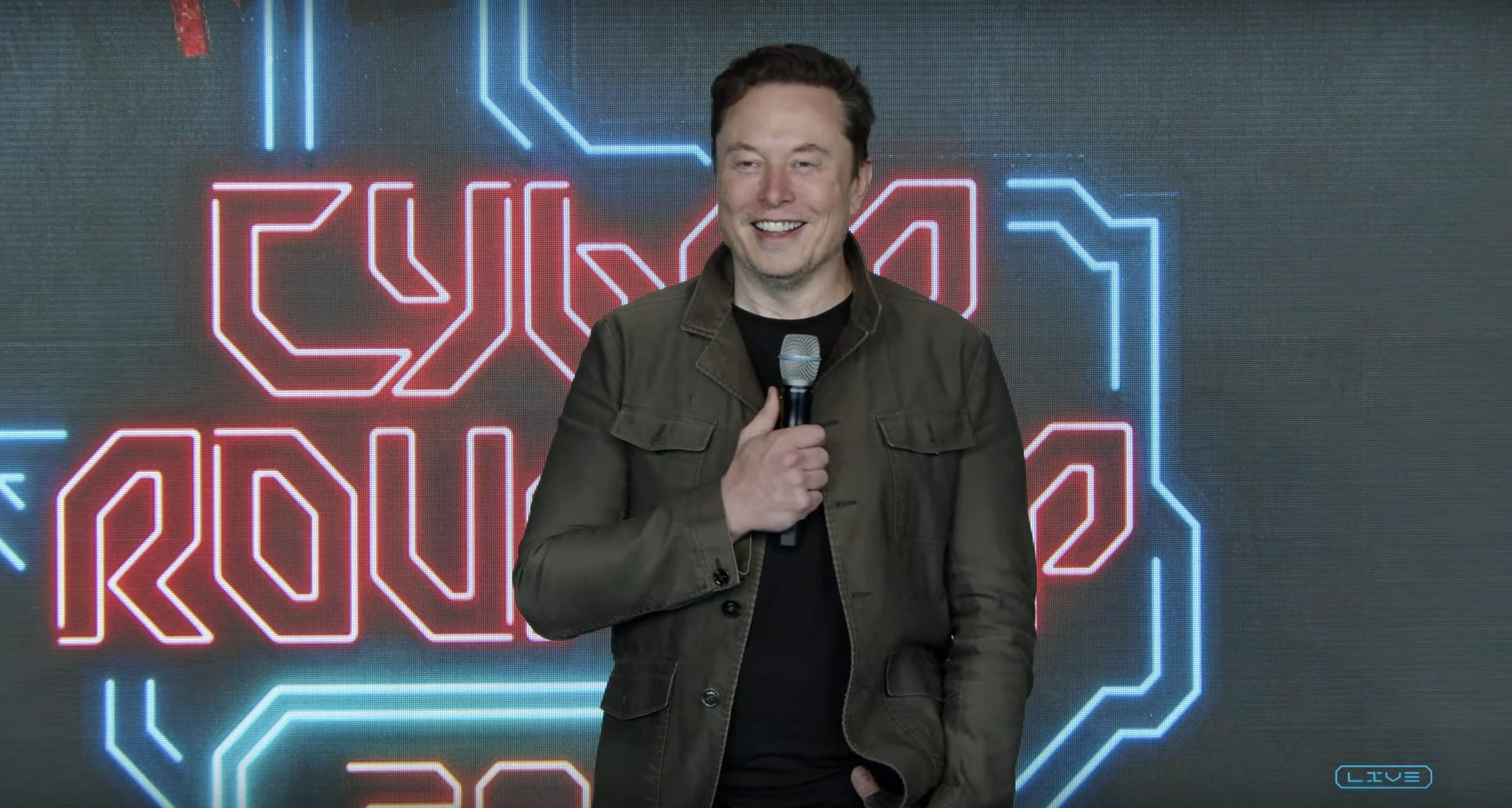
Tesla scrambled its executives around following the exit of CEO Elon Musk’s sidekick last week, Omead Afshar. Afshar was relieved of his duties as Head of Sales for both North America and Europe.
Bloomberg is reporting that Musk is now overseeing both regions for sales, according to sources familiar with the matter. Afshar left the company last week, likely due to slow sales in both markets, ending a seven-year term with the electric automaker.
Tesla’s Omead Afshar, known as Elon Musk’s right-hand man, leaves company: reports
Afshar was promoted to the role late last year as Musk was becoming more involved in the road to the White House with President Donald Trump.
Afshar, whose LinkedIn account stated he was working within the “Office of the CEO,” was known as Musk’s right-hand man for years.
Additionally, Tom Zhu, currently the Senior Vice President of Automotive at Tesla, will oversee sales in Asia, according to the report.
It is a scramble by Tesla to get the company’s proven executives over the pain points the automaker has found halfway through the year. Sales are looking to be close to the 1.8 million vehicles the company delivered in both of the past two years.
Tesla is pivoting to pay more attention to the struggling automotive sales that it has felt over the past six months. Although it is still performing well and is the best-selling EV maker by a long way, it is struggling to find growth despite redesigning its vehicles and launching new tech and improvements within them.
The company is also looking to focus more on its deployment of autonomous tech, especially as it recently launched its Robotaxi platform in Austin just over a week ago.
However, while this is the long-term catalyst for Tesla, sales still need some work, and it appears the company’s strategy is to put its biggest guns on its biggest problems.
-
Elon Musk1 day ago
Tesla investors will be shocked by Jim Cramer’s latest assessment
-
News6 days ago
Tesla Robotaxi’s biggest challenge seems to be this one thing
-
News2 weeks ago
Tesla’s Grok integration will be more realistic with this cool feature
-
Elon Musk2 weeks ago
Elon Musk slams Bloomberg’s shocking xAI cash burn claims
-
News2 weeks ago
Tesla China roars back with highest vehicle registrations this Q2 so far
-
News2 weeks ago
Texas lawmakers urge Tesla to delay Austin robotaxi launch to September
-
News2 weeks ago
Tesla dominates Cars.com’s Made in America Index with clean sweep
-
Elon Musk1 week ago
First Look at Tesla’s Robotaxi App: features, design, and more