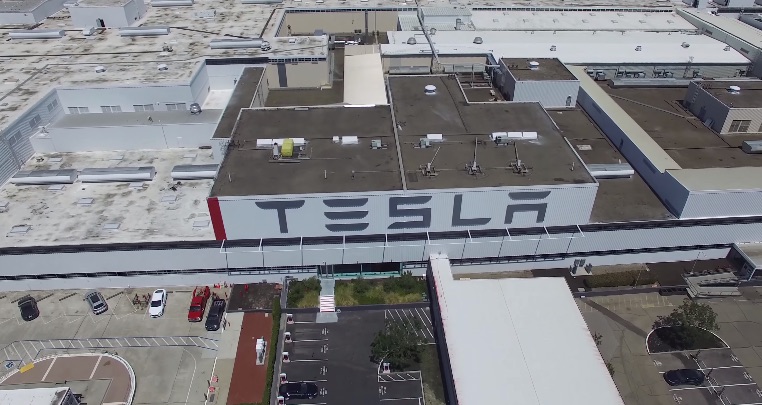
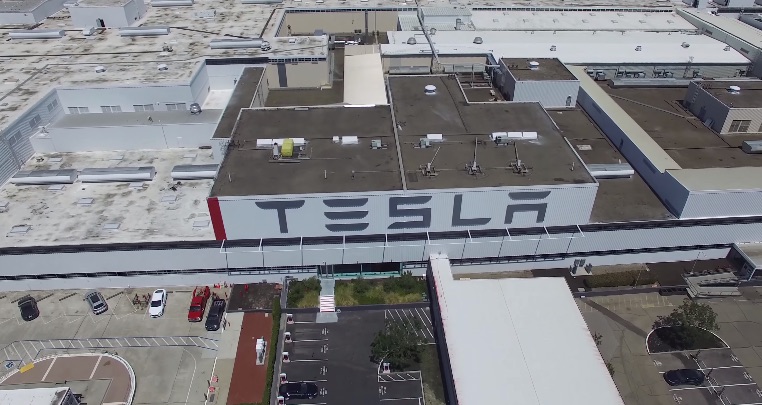
News
Tesla emphasizes factory safety, preempts possible smear campaign by auto union
Tesla released a blog post Sunday evening that reemphasizes the company’s goal to become the safest auto factory in the world. The post comes after the United Auto Workers Union (UAW) attempted to rally support earlier this year from Fremont factory workers in favor of unionizing.
Tesla states that it has received several media inquiries over allegations about safety at its Fremont, California factory. The well-timed nature of the inquiries, and similarity in topic, led Tesla to believe that the UAW was spreading anti-Tesla propaganda to the media in an attempt to provoke a response from the public, and from Tesla employees. In typical fashion, Tesla acted quickly and took to the offensive to defend the company’s approach to manufacturing, and maintaining the health and safety of its employees. The company has gone as far as forming dedicated Ergonomics Teams that have exclusive focus on “improving health and safety and reducing ergonomic risk for current and future production”.
“We are building entirely new vehicles from the ground up, using entirely new technology, production, and manufacturing methods, and ramping them at high volume. Getting this right is extremely difficult, and we deeply appreciate the hard work that all our employees do to help us achieve what most regard as impossible.” says Tesla through its blog post.
Tesla notes that in just 15 years, the company has become the largest manufacturing employer in California with over 10,000 production jobs in the Fremont factory and surrounding Bay Area.
Tesla has a proven track record of putting safety first as made evident by the award-winning safety ratings for its Model S and Model X. Vehicles have taken the brunt of the impact for their occupants, have swerved to avoid accidents and have even accelerated to avoid accidents. The innovative safety features Tesla has built into its vehicles is unsurpassed in the automotive world.
Though Tesla’s safety record to date is already better than industry-average, according to its press release, the company indicates that it continues to learn and apply new production processes aimed at improving employee well-being. Among the improvements are:
- Added 3rd shift to the manufacturing schedule to cut overtime because the employees asked for it and it was the right thing to do.
- Hired dedicated Ergonomist and established an Ergonomics team to ensure that current and future Tesla manufacturing lines are ergonomically friendly for employees.
- Model 3 has been designed with manufacturing employee ergonomics in mind. The Tesla Ergonomics Team works closely with design and engineering teams to catch ergonomics issues before they happen and proactively drive these improvements back into the design of the equipment and the car. Yes, you heard that right. Tesla will redesign the car if it is resulting in ergonomically challenging situations for its manufacturing employees.
- Established safety teams in every department which meets regularly to ensure safety is a top focus in its manufacturing operating departments.
These changes are not just skin deep and the company is seeing the results of the changes already. Tesla says it has collectively reduced 52% in lost time incidents and a 30% reduction in recordable incidents in the first quarter of 2017 versus the same period last year. These more granular metrics support an improvement in the industry standard Total Recordable Incident Rate (TRIR) which at the end of Q1 2017 was 4.6, a full 32% better than the industry standard of 6.7.
Anyone who has worked in an industry where safety is important can tell you that a culture of safety awareness is built day by day, month by month over many years. Tesla has a demonstrated history of superior results. The steps it has outlined to drive further improvements at the factory are evidence of a continued focus on safety and its employees.
The full post from the Tesla Blog reads as follows:
Creating the Safest Car Factory in the World
Earlier this year, the United Automobile Workers (UAW) announced it was attempting to organize workers in Tesla’s Fremont factory. The latest phase of their campaign involves a concerted and professional media push intended to raise questions about safety at Tesla.
We have received calls from multiple journalists at different publications, all around the same time, with similar allegations from seemingly similar sources about safety in the Tesla factory. Safety is an issue the UAW frequently raises in campaigns it runs against companies, and a topic its organizers have been promoting on social media about Tesla.
Some of the publications who have contacted us have rejected covering this “story” because they understand it is a misleading narrative based on anecdotes, not facts. However, there will likely be a few publications that choose to publish stories regardless, so we want to make sure the public also has the facts. Watch for these articles to downplay or ignore our actual 2017 safety data and to instead focus on a small number of complaints and anecdotes that are not representative of what is actually occurring in our factory of over 10,000 workers.
First, some context is important. The difficulty of starting a successful U.S. car company cannot be overstated, as evidenced by the fact that Ford is the only other U.S. car company to have never gone bankrupt. We are attempting to break this trend in order to fulfill our mission of accelerating the world’s transition to sustainable energy.
We are building entirely new vehicles from the ground up, using entirely new technology, production, and manufacturing methods, and ramping them at high volume. Getting this right is extremely difficult, and we deeply appreciate the hard work that all our employees do to help us achieve what most regard as impossible. While we still have a long way to go, in less than 15 years, we have become California’s largest manufacturing employer, creating more than 10,000 high-quality production jobs in the Bay Area, many of which had previously disappeared with the closure of NUMMI under the stewardship of the UAW.
As we work to achieve our mission, nothing is more important to us than protecting the health and safety of our employees. As we look at our safety record in prior years, we realize that we have not been perfect. No car factory is perfect, but particularly given that Model S and X were the first cars we built at more than tiny volumes, we fully acknowledge that they were not designed for ease of manufacturing – far from it. As would be expected, we have since learned many lessons, including how to improve the production process for the well-being of our colleagues.
Here are just some of the improvements that we have made:
- Historically, depending on production needs, some Tesla employees have worked significant amounts of overtime because it was necessary for the company to survive. However, working overtime can be challenging for employees and their families. Last year, we added a third shift to reduce the overtime burden on each team member and to improve safety. We did this because our employees asked for it, and because it was the right thing to do.
- As a result of this change, the average amount of hours worked by production team members has dropped to about 42 hours per week, and the level of overtime decreased by more than 60%. We hired our first dedicated Ergonomist in 2013, and in 2015 established an Ergonomics Team exclusively focused on improving health and safety and reducing ergonomic risk for current and future production.
- In addition to improving the process of building Model S and X, Model 3 has been designed specifically with ergonomics in mind. Our ergonomics team has worked hand-in-hand with our engineers on the design process. As just one example, we created simulations that showed us where reaching or bending by employees was most likely to occur, which in turn allowed us to redesign the equipment and the car to eliminate these issues as much as possible.
- Each department now has a Safety Team that meets regularly to increase safety awareness and recommend improvements, many of which have already been implemented.
- We are continuing to establish health and safety management procedures to scale with our operational growth.
The third shift, ergonomic improvements and increased safety awareness have collectively led to a 52% reduction in lost time incidents and a 30% reduction in recordable incidents from the first quarter of 2016 to the first quarter of 2017. In addition, through the end of Q1 2017, the factory’s total recordable incident rate (TRIR), the leading metric for workplace safety, is 4.6, which is 32% better than the industry average of 6.7. This data shows that there has been a dramatic improvement in employee safety, we are now significantly better than industry-average, and we continue to improve each day. A few anecdotes in a factory of over 10,000 people can always be given, but these are the facts.
Tesla’s safety record is much better than industry average, but it is not enough. Our goal is to have as close to zero injuries as humanly possible and to become the safest factory in the auto industry. We will get there by continuing to ask our employees to raise safety concerns and to keep proposing ideas that make things even better.
The alternative is to stop improving and to instead do what the rest of the industry, including the UAW, has always done. But being industry average would make our safety 32% worse. We care too much about our team to go backwards.
Elon Musk
Tesla board reveals reasoning for CEO Elon Musk’s new $1 trillion pay package
“Yes, you read that correctly: in 2018, Elon had to grow Tesla by billions; in 2025, he has to grow Tesla by trillions — to be exact, he must create nearly $7.5 trillion in value for shareholders for him to receive the full award.”
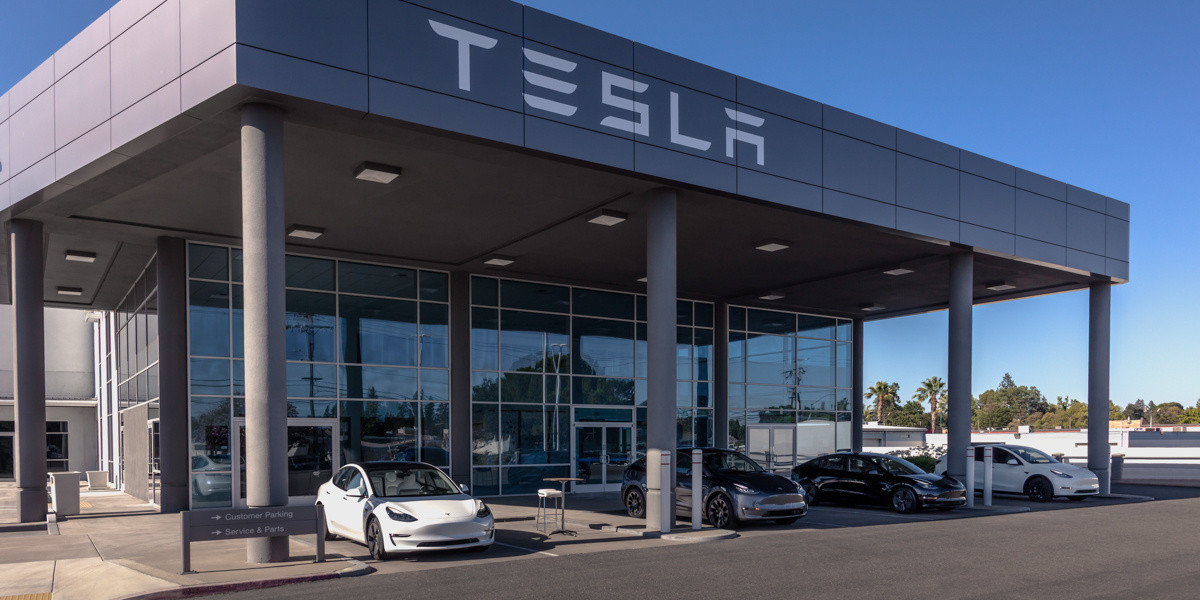
Tesla’s Board of Directors has proposed a new pay package for company CEO Elon Musk that would result in $1 trillion in stock offerings if he is able to meet several lofty performance targets.
Musk, who has not been meaningfully compensated since 2017, completed his last pay package by delivering billions in shareholder value through a variety of performance-based “tranches,” which were met and resulted in the award of billions in stock.
Elon Musk’s new pay plan ties trillionaire status to Tesla’s $8.5 trillion valuation
However, Musk was unable to claim this award due to a ruling by the Delaware Chancery Court, which deemed the payout an “unfathomable sum.”
Now, the company is taking steps to ensure Musk gets paid, as the Board feels that it is crucial to retain its CEO, who has been responsible for much of the company’s success.
This is not a statement to undermine the work of all of Tesla’s terrific employees, but a ship needs to be captained by someone, and Musk has proven he is the right person for the job.
The Board also believes that, based on a statement made by the company in its proxy, various issues will be discussed during the upcoming Shareholder Meeting.
Robyn Denholm and Kathleen Wilson-Thompson recognized Musk’s contributions in a statement, which encouraged shareholders to vote to approve the payout:
“We’re asking you to approve the 2025 CEO Performance Award. In designing the new performance award, we explored numerous alternatives. Ultimately, the new award aims to build upon the success of the 2018 CEO Performance Award framework, which ensure that Elon was only paid for the performance delivered and incentivized to guide Tesla through a period of meteoric growth. The 2025 CEO Performance Award similarly challegnes Elon to again meet a series of even more aspirational goals, including operational milestones focused on reaching Adjusted EBITDA targets (thresholds that are up to 28 times higher than the 2108 CEO Performance Award’s top Adjusted EBITDA milestone) and rolling out new or expanded product offerings (including 1 million Robotaxis in commercial operation and delivery of 1 million AI Bots), all while growing the company’s market capitalization by trillions of dollars.
Yes, you read that correctly: in 2018, Elon had to grow Tesla by billions; in 2025, he has to grow Tesla by trillions — to be exact, he must create nearly $7.5 trillion in value for shareholders for him to receive the full award.
In addition to these unprecedented performance milestones, the 2025 CEO Performance Award also includes innovative structural features, born out of the special committee’s considered analysis and extensive shareholder feedback. These features include supercharged retention (at least seven and a half years and up to 10 years to vest in the full award), structural protections to minimize stock price volatility due to administration of this award and, thereafter, incentives for Elon to participate in the Board’s continued development of a framework for long-term CEO Succession. If Elon achieves all the performance milestones under this principle-based 2025 CEO Performance Award, his leadership will propel Tesla to become the most valuable company in history.”
Musk will have a lot of things to accomplish to receive the 423,743,904 shares, which are divided into 12 tranches.
However, the Board feels he is the right person for the job, and they want him to remain the CEO. This package should ensure that he stays with Tesla, as long as shareholders feel the same way.
News
Tesla Robotaxi app download rate demolishes Uber, Waymo all-time highs
After two and a half months of testing with a group of hand-picked Tesla influencers and some media, the company has officially launched Robotaxi rides in both Austin, Texas, and the California Bay Area to the public.
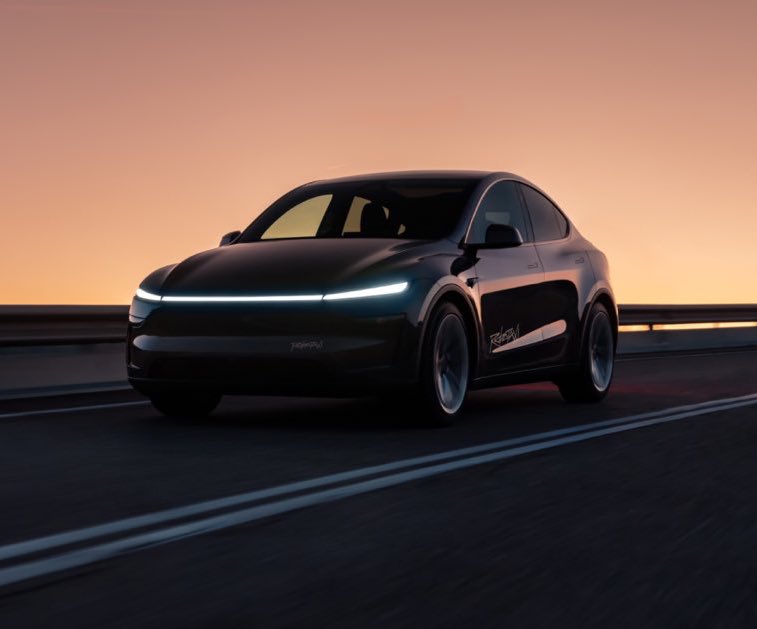
Tesla launched its Robotaxi app to the general public yesterday, and the number of downloads is a testament to the platform’s high demand for testing.
After two and a half months of testing with a group of hand-picked Tesla influencers and some media, the company has officially launched Robotaxi rides in both Austin, Texas, and the California Bay Area to the public.
Tesla Robotaxi makes major expansion with official public app launch
Downloading the app is available to iOS users, so if you have an iPhone, you can get it and join the waitlist. Tesla has not yet launched the Robotaxi app for the Android platform, but did hint that it would be coming soon.
The testing phase with the group Tesla selected has gone well. In Austin, the City has only listed one “Safety Concern” with Robotaxi during the testing phase. For the most part, things have gone extremely well, and riders have had good things to say.
Tesla is still operating with some safeguards in place, such as Safety Monitors and Safety Drivers, but these are precautionary and temporary; CEO Elon Musk has said they should be removed by the end of the year.
Elon Musk says Tesla will take Safety Drivers out of Robotaxi: here’s when
Even still, Tesla Robotaxi is something that many people want to experience, and the app downloads prove it.
The Tesla Robotaxi app was downloaded at a rate that exceeded all rolling 30-day periods of both Uber and Waymo, according to Brett Winton of ARK Invest. Tesla’s Robotaxi’s first day on the App Store exceeded Uber’s by 40 percent and Waymo’s best download day ever by six times:
Today’s Tesla Robotaxi App downloads outpaced Uber across all rolling 30 day periods by 40% and bested Waymo’s best download day ever by >6x pic.twitter.com/s9s1XTsUu2
— Brett Winton (@wintonARK) September 5, 2025
The surge in downloads is a good indication of how in demand the Robotaxi suite was, as many people within the community had vocalized their requests to try the platform, but Tesla was not ready to expand it beyond its handpicked group.
The expansion of the program will result in more rides, provided Tesla continues to expand its fleet of vehicles. It has already admitted many of those who were initially placed on the waitlist.
News
Elon Musk’s xAI expands to Seattle with salaries up to $440,000
The move was announced by the artificial intelligence startup and Elon Musk on social media platform X.
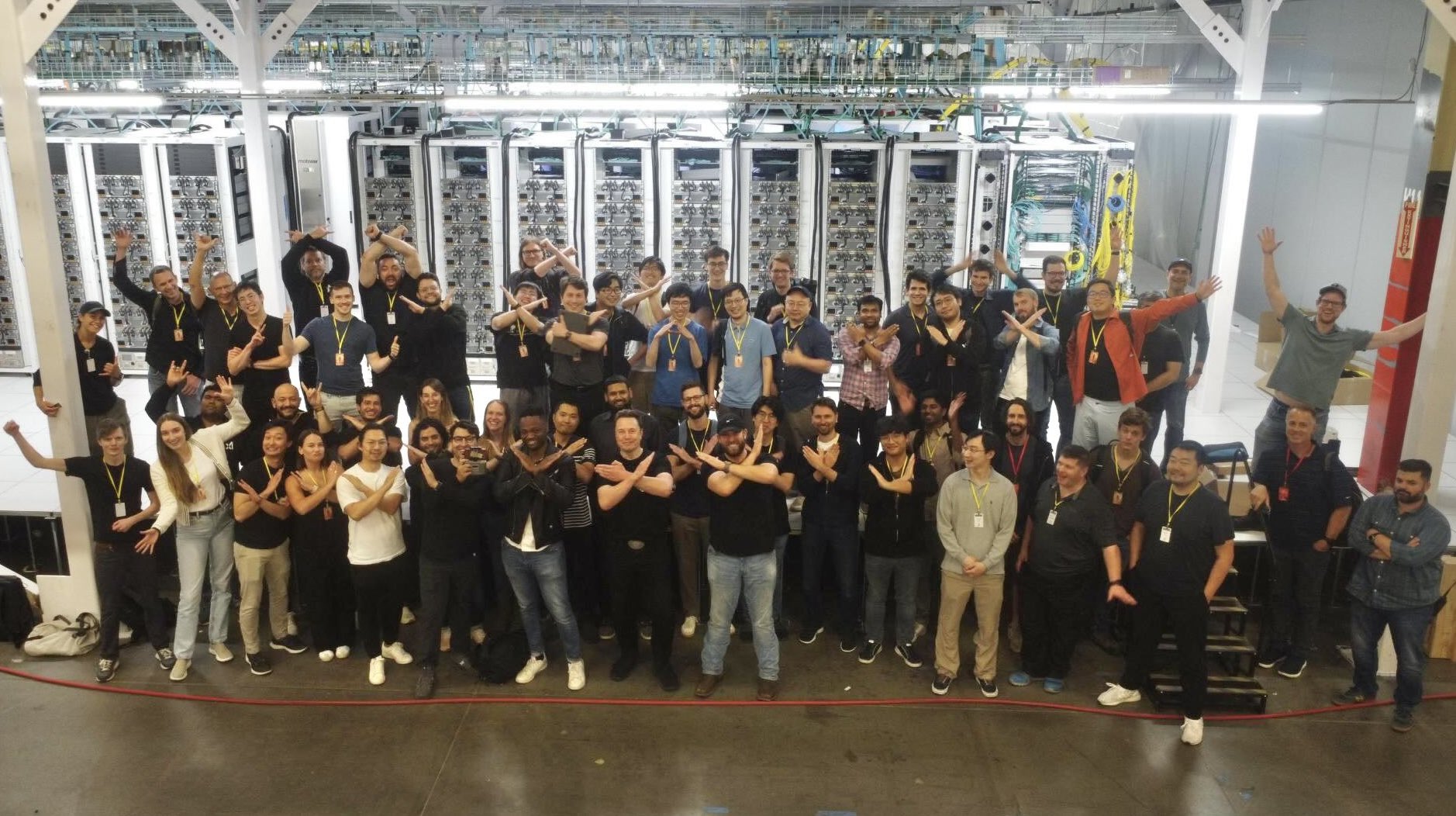
Elon Musk’s artificial intelligence startup xAI is opening a new office in Seattle as it accelerates its global expansion.
The move was announced by the artificial intelligence startup and Elon Musk on social media platform X. xAI is also hiring for its first positions in the new site.
New Seattle office
As could be seen on xAI’s Careers webpage, the Seattle office is currently hiring for three engineering roles. Each of the three technical roles tied to the new site carry salaries ranging from $180,000 to $440,000.
The new office adds to xAI’s growing presence, which now spans San Francisco, Austin, London, Dublin, New York, and Memphis. The Seattle-based roles focus on video and image generation systems, signaling Musk’s intent to challenge rivals like OpenAI and Meta in generative AI.
Pressures and challenges
Seattle also places xAI within reach of Microsoft’s headquarters in Redmond. Microsoft has emerged as a central player in the AI race through its multibillion-dollar partnership with OpenAI, making xAI’s move into the region notable. The competition for AI specialists has pushed salaries higher across the industry, with filings showing OpenAI staff earning up to $530,000 and Anthropic engineers as much as $690,000 annually, as noted by Insider.
The startup has also seen some high-profile departures in recent months, including cofounder Igor Babuschkin and general counsel Robert Keele. Still, xAI continues to grow aggressively, and its Grok large language model has been gaining momentum among mainstream users. Work also continues to be underway to further build out the company’s Colossus supercomputer cluster. Reports have also suggested that xAI has moved into San Francisco offices in the Mission District, a site Musk initially leased during OpenAI’s early years.
-
News6 days ago
Tesla is overhauling its Full Self-Driving subscription for easier access
-
Elon Musk1 week ago
Elon Musk shares unbelievable Starship Flight 10 landing feat
-
Elon Musk1 week ago
Elon Musk reveals when SpaceX will perform first-ever Starship catch
-
Elon Musk1 week ago
SpaceX Starship Flight 10 was so successful, it’s breaking the anti-Musk narrative
-
Elon Musk2 days ago
Tesla’s next-gen Optimus prototype with Grok revealed
-
News4 days ago
Tesla appears to be mulling a Cyber SUV design
-
News1 week ago
Tesla expands crazy new lease deal for insane savings on used inventory
-
News1 week ago
Tesla talks Semi ramp, Optimus, Robotaxi rollout, FSD with Wall Street firm