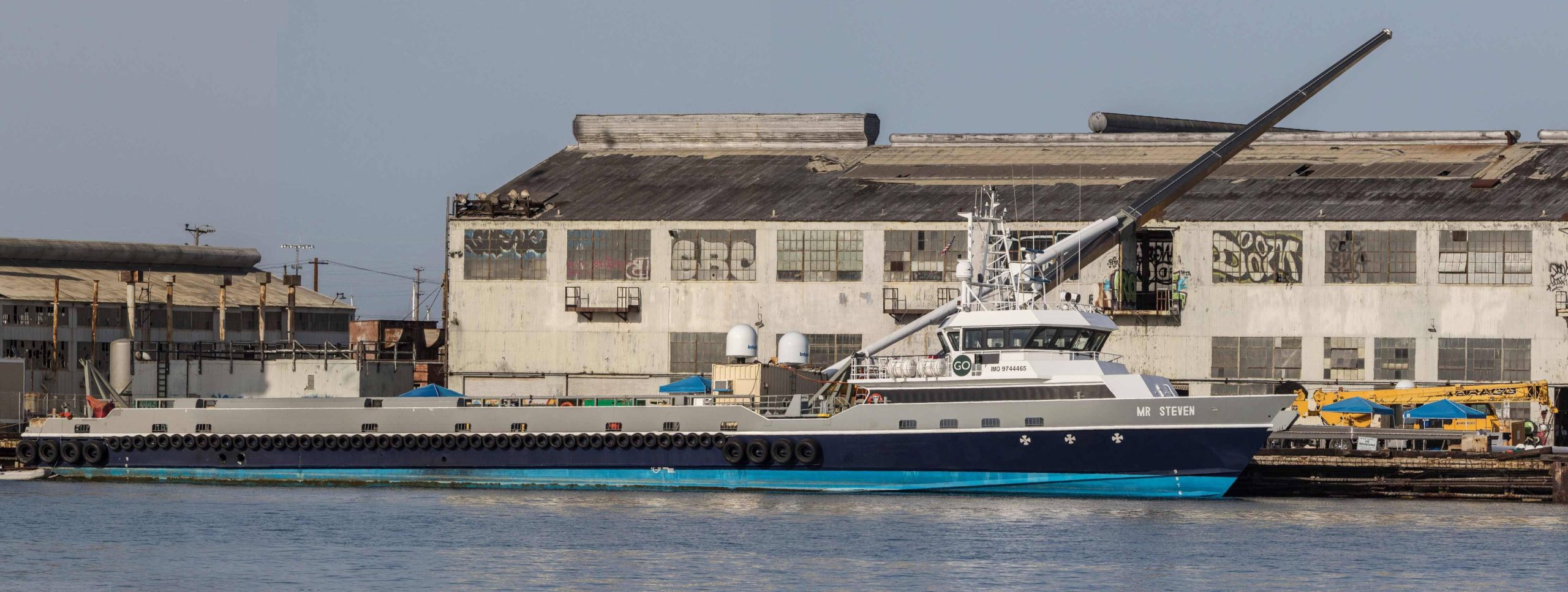
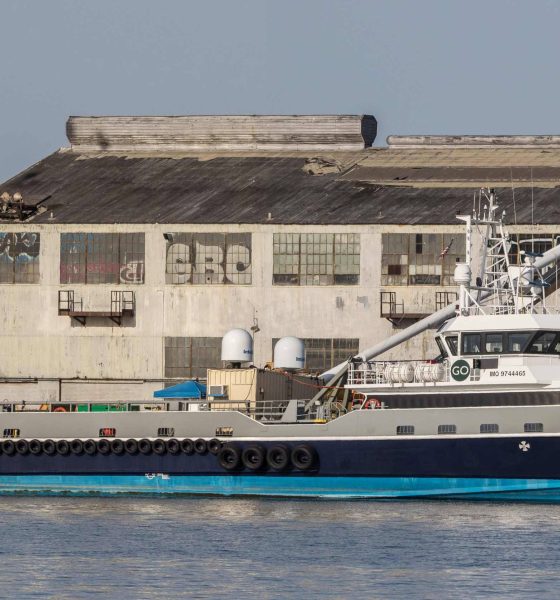
News
SpaceX’s Mr Steven gains upgraded arms to catch its first Falcon 9 fairings
SpaceX’s iconic Falcon 9 payload fairing recovery ship, known as Mr Steven, has been spotted in California’s Port of San Pedro having new arms installed with two cranes and a crew of SpaceX technicians. Aside from the sudden addition of dramatically different arm design, a large inflatable structure also took shape – seemingly overnight – right behind Mr Steven, the purpose of which is entirely unclear.
Incredibly, these massive new arms and their new equally large support struts and base plates have begun installation barely two weeks after Mr Steven took roost and had his old arms removed at SpaceX’s Berth 240 property. While the timeline of the arm and net upgrades – mentioned by CEO Elon Musk several weeks ago – was previously uncertain, the incredibly quick turnaround from old arm removal to new arm install suggests that SpaceX may, in fact, be aiming to have Mr Steven ready for recovery operations as early as Iridium-7, scheduled for launch on July 20th. In all likelihood, the fairing recovery vessel will be held up till the subsequent Vandenberg Air Force Base launch while a net with an area perhaps four times larger is custom-built for SpaceX.

A massive inflatable structure appeared out of nowhere at Berth 240 roughly four days after Teslarati photographer Pauline Acalin had last checked up on the facility. (Pauline Acalin)
Nevertheless, SpaceX’s speed rarely fails to surprise, and it’s entirely possible that a new, larger net was already ordered some time ago in preparation for the eventuality that Mr Steven’s first recovery mechanism was unsuccessful. Given the fact that at least two main arms and perhaps eight white, cylindrical struts have apparently been completed and are awaiting installation at Berth 240, it’s probable that the lead time on this new recovery mechanism stretches back at least several months, likely at least a month before Musk mentioned that Mr Steven would have its usable catching area grown “by a factor of [four]” in early June.
Yup, we are extending the net area by a factor of 4
— Elon Musk (@elonmusk) June 5, 2018
Closing the fairing recovery gap
With four times the net available to catch wayward Falcon 9 payload fairings, SpaceX may be able to finally close the gap between Mr Steven and the successful and routine recovery and reuse of the second of three main Falcon 9 (and Heavy) components. At roughly 10% of the total cost (not price) of a single-booster Falcon 9, the considerable effort being put into the recovery of carbon-composite payload fairings is in a way motivated more by manufacturing bottlenecks than by the money it will save SpaceX (somewhat less than $3m per half).
- Taken on Friday, these two photos show the new arm mounting brackets, installed on Mr Steven the week of July 2nd. (Pauline Acalin)
- Scarcely 48 hours later, an entirely new pear-shaped arm and two huge, circular struts were successfully installed, presumably the first of four sets. (Pauline Acalin)
- (Pauline Acalin)
SpaceX’s team of composite technicians and engineers will need to reliably fabricate as many as ~50 payload fairing halves in 2018, effectively one half each week
By recovering payload fairings before they touch the ocean surface, the company may – in one fell swoop – be able to dramatically reduce the operational expenditure required to sustain the annual production of dozens of Falcon fairings, each of which requires an inescapable and tediously slow stint in a massive autoclave, only a few of which can be squeeze into the company’s Hawthorne factory. As an example, SpaceX’s team of roughly 150 dedicated composite technicians and engineers will need to reliably fabricate as many as ~50 payload fairing halves – nearly a full half each week – to sustain SpaceX’s anticipated 2018 manifest of 24-28 launches, excluding three Cargo Dragon resupply missions that don’t need fairings.
While both Crew and Cargo Dragon spacecraft and trunks contain a large proportion of carbon fiber-composite structures, every composite Falcon 9 interstage that rolled off of the assembly line since February 2018 is part of a Block 5 booster and is thus expected to support a bare minimum of several missions on its own, functionally multiplying the useful output of any given production line even while the amount of work (and thus work-hours) is reduced. While Falcon 9 boosters – making up roughly 70% of the cost of the entire rocket – have been successfully upgraded to support several reuses each, SpaceX still has to produce a new payload fairing and upper stage for each launch. A spectacular Block 4 farewell earlier this month – complete with a recoverable booster expended to make way for Block 5 – simply served to emphasize the company’s desire to mitigate the expandability of both (currently) unreusable segments of Falcon 9.
- Meanwhile, the purpose of this massive inflatable ring is almost entirely unclear, as it would appear to be redundant with the initial installation of Mr Steven’s new recovery mechanism. (Pauline Acalin)
- Arm installation will presumably continue over the course of the week, hopefully reaching completion in time to recovery Iridium-7’s payload fairing. (Pauline Acalin)
If Mr Steven can recover even a small fraction – say 25% – of SpaceX payload fairings launched annually, the exact same level of effort (and thus capital) could support 25% more launches annually or reduce the work hours spent on fairing production by 25%. As it happens, SpaceX’s next-generation rocket (BFR) happens to be built (theoretically) almost entirely out of carbon-composites, from the propellant tanks to the spaceship’s delta wing.
Originally meant to focus on the wholly unexpected appearance of a giant inflatable structure at Berth 240, SpaceX’s breakneck pace of action abruptly recentered it on the equally unexpected installation of one the vessel’s first upgraded arms, meant to support a net that could be as much as four times larger than its predecessor. That symbolism on its own is a worthy representation of some of the best aspects of SpaceX’s world-class team of engineers and technicians, acting as a slightly more on-topic corollary to the equally rapid design, prototyping, fabrication, and testing of ad-hoc ‘submarines’ intended to help a number of Thai children currently trapped in a cave near the country’s border with Myanmar/Burma.

Mr Steven shows off the first of four new arms as a mysterious inflatable ring patiently sits astern. (Pauline Acalin)
Follow us for live updates, peeks behind the scenes, and photos from Teslarati’s East and West Coast photographers.
Teslarati – Instagram – Twitter
Tom Cross – Twitter
Pauline Acalin – Twitter
Eric Ralph – Twitter
News
Tesla offers tasty Supercharging incentive as Q3 push continues
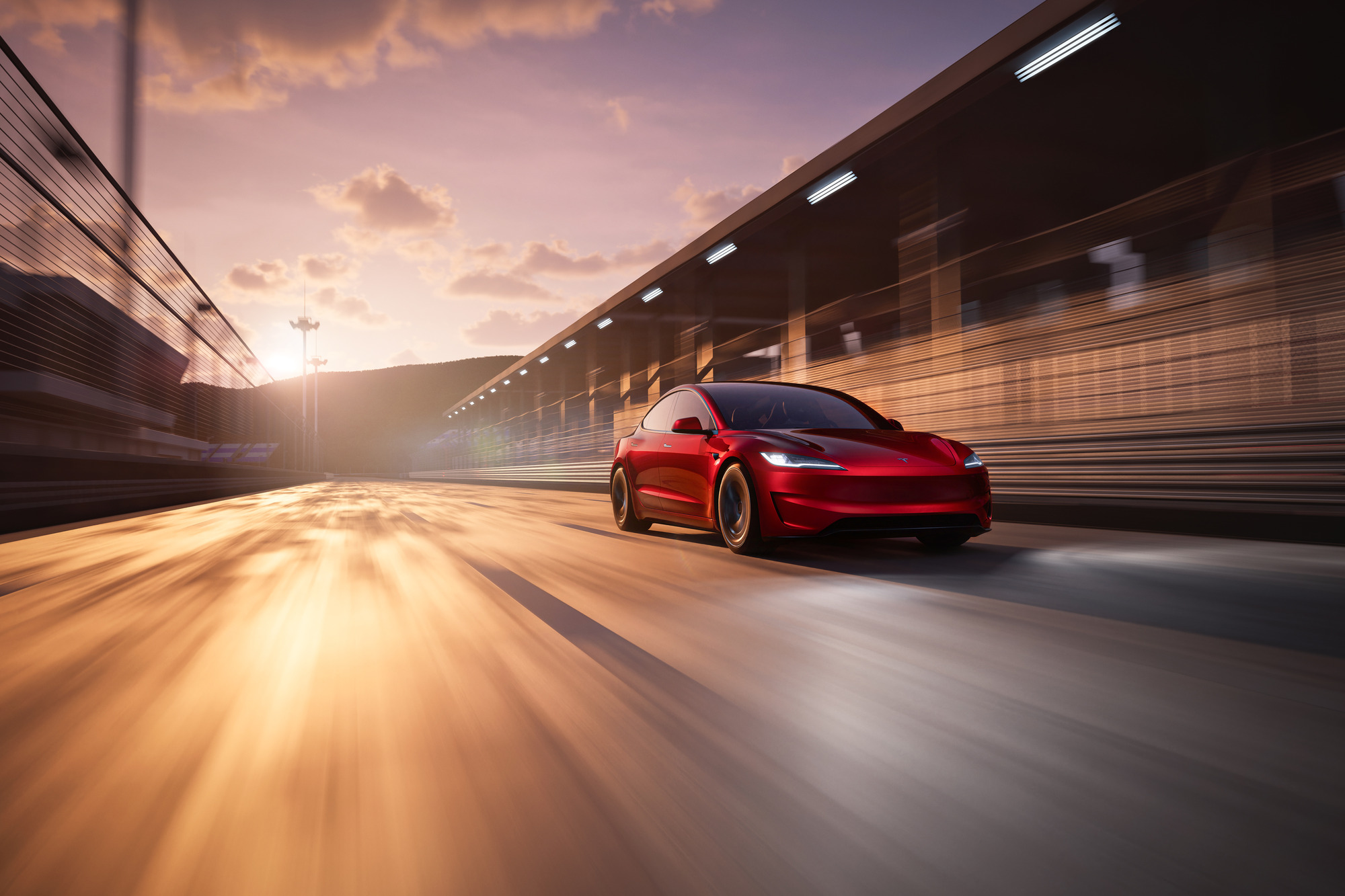
Tesla is offering a tasty Supercharging incentive on inventory Model 3 units in Canada as it continues to push sales in the third quarter.
In the United States, Tesla is preparing for the end of the $7,500 electric vehicle tax credit. While it is offering a multitude of incentives in the U.S. to help push sales of its vehicles before the credit goes away, it is not saving the deals for Americans exclusively.
Yesterday, the company announced it is now offering Free Supercharging for life on all Model 3 inventory in Canada, a massive incentive for those who would use the vehicle as a daily driver:
Unlimited road trips through Canada
Free Supercharging now on all Model 3 inventory 🇨🇦
— Tesla North America (@tesla_na) August 15, 2025
The deal would normally only apply to Superchargers located in Canada, meaning if a Canadian drove over the border into the United States and Supercharged, they would have to pay for it.
However, Tesla also confirmed that the charging deal would extend to the U.S. Canadians will be able to drive across the U.S. and Supercharge for free for the life of the vehicle.
Free Supercharging is such a great perk because the money an owner saves on charging factors directly into what they are saving if they were to own a gas car. While Supercharging and home charging are, on average, cheaper than filling up with gas, the savings are not massive.
When Supercharging is free, it can save consumers hundreds of dollars per month, especially if they plan to use the Tesla for their daily commute. Some people could fill their gas cars up two times a week to get to work, spending $80-$100 every five days on gas.
Tesla has been using incentives like this to push vehicles into customers’ hands. Q3 could be one of the best three-month spans in recent memory with the push it is making.
News
Tesla is preparing to take on autonomy’s final boss
India’s city streets are notorious for their complexity and congestion.
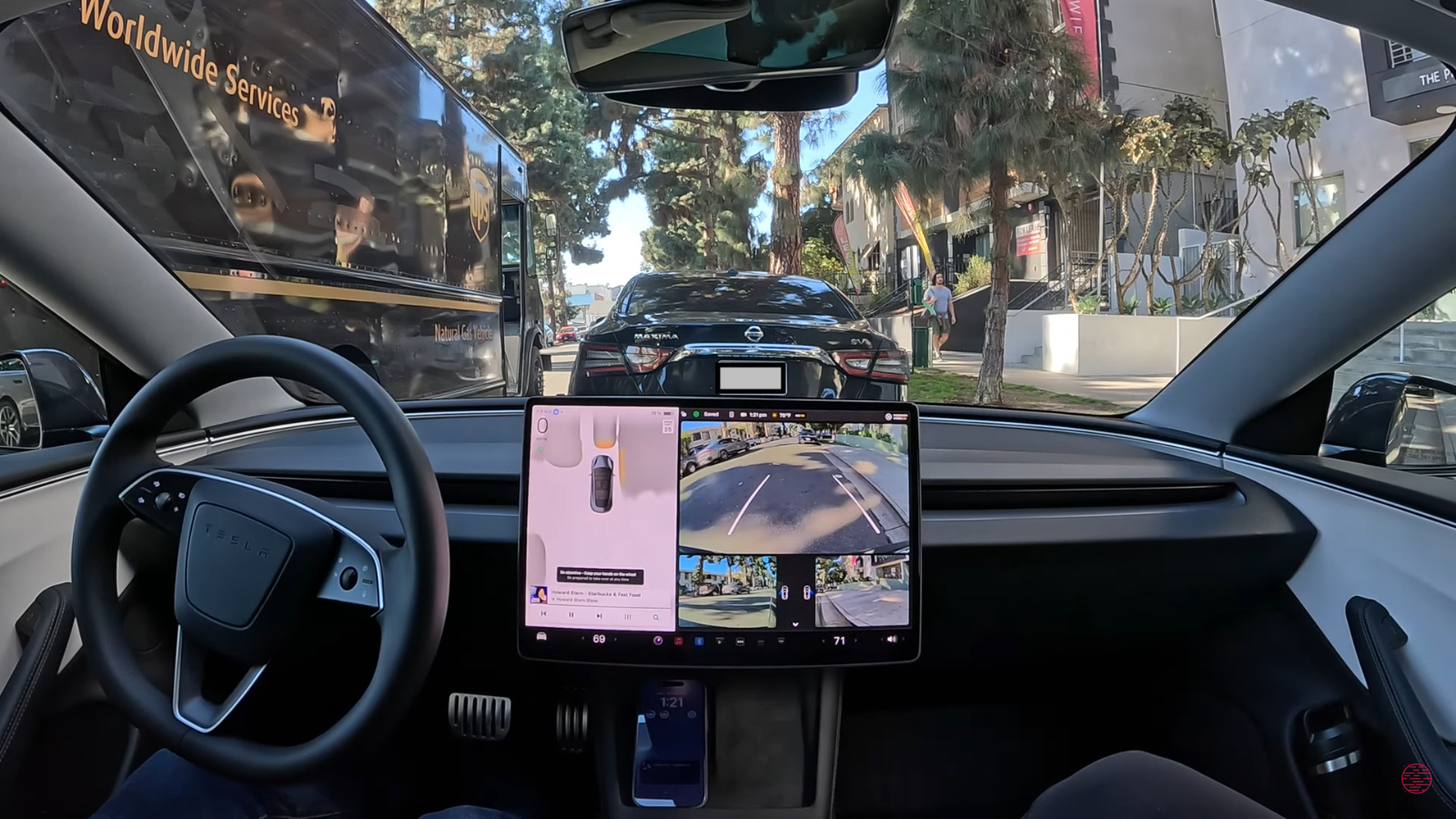
If there is any sign that Tesla is now confident about its self-driving program, it would be this. As could be seen on Tesla’s Careers page, the company is now hiring Autopilot Vehicle Operators in Delhi and Mumbai, India.
As far as real-world traffic is concerned, one could argue that India’s city streets are the final boss of autonomous driving systems due to their complexity and congestion.
Tesla job openings
As per Tesla in its recent job openings, Prototype Vehicle Operators will be responsible for driving an engineering vehicle for extended periods and conducting dynamic audio and camera data collection for testing and training purposes. In both its job listings for Mumbai and Delhi, Tesla noted that successful applicants will be gathering real-world data on the weekends and around the clock.
Considering the job openings in India, Tesla seems to be intent on rolling out its advanced driver-assist systems like FSD in the country. This is quite interesting, as Tesla is not hiring Prototype Vehicle Operators in other territories that recently launched, such as the Philippines. Perhaps Tesla intends to tackle FSD’s final boss of sorts before rolling out FSD in other territories.
FSD’s rollout
Tesla’s autonomous driving program uses the company’s Full Self-Driving system, which is currently available on vehicles in North America and China. Tesla, however, has a more advanced version of FSD called Unsupervised FSD, which is currently being used in vehicles that are part of the Robotaxi pilot in Austin and the Bay Area.
Elon Musk has also recently announced on X that Tesla will be releasing FSD V14 in the coming weeks. He also shared a number of improvements that can be expected from FSD V14. “The FSD release in about 6 weeks will be a dramatic gain with a 10X higher parameter count and many other improvements. It’s going through training & testing now. Once we confirm real-world safety of FSD 14, which we think will be amazing, the car will nag you much less,” Musk wrote in his post.
News
Tesla Sweden finally makes IF Metall union give up 600-day strike
Tesla and the union have opened the door to resolutions that do not involve a collective agreement.
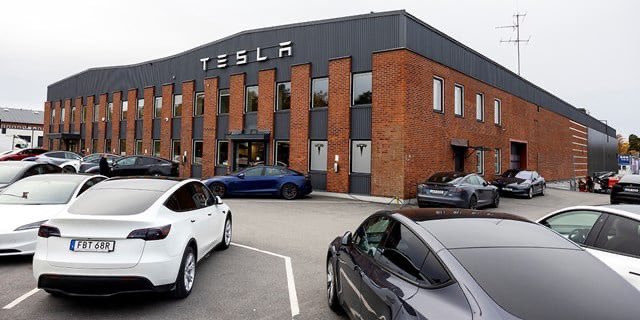
After nearly two years of industrial action and sympathy strikes, Swedish labor union IF Metall has stated that it is softening its stance in its dispute with Tesla. With this, Tesla and the union have opened the door to resolutions that do not involve a collective agreement.
Union chair Marie Nilsson told Sveriges Radio’s Ekot that while the preferred outcome remains a signed agreement, “other alternative solutions” are now on the table.
Union reconsiders rigid demands
The strike, which began over 600 days ago, has been marked by a series of strategic moves from both sides. IF Metall blocked Tesla’s access to license plates by targeting mail delivery, while Tesla bypassed the restrictions by importing vehicles in bulk through German ferries to Trelleborg, among other strategies.
Despite the high-profile tactics, the number of active strikers has been relatively small, just about 60 in total, as noted in a CarUp report. Tesla Sweden has also maintained that it does not intend to bow down to the union’s demands. Over the 600-day strike, Tesla Sweden has adapted its operations to get around the union and its allies’ strikes.
Possible paths to ultimate resolution
Nilsson, for her part, noted that IF Metall is now willing to explore alternatives, such as embedding industry-standard terms directly into Tesla’s employment contracts or shifting Tesla’s Swedish operations to a company that already has a collective agreement.
“You can do it in different ways. The easiest thing would be to sign a collective agreement. But when that is not possible, we have to find other alternative solutions as well, so we are open to discussion,” Nilsson stated.
IF Metall, if any, has acknowledged that Tesla has already improved working conditions in Sweden since the dispute began. Tesla Sweden has argued that its working conditions are already better than union standards, which is reportedly one of the reasons why very few company employees actually participated in IF Metall’s strike.
“There have been conversations throughout the journey where we compared our conditions. Tesla has adjusted details without going into details, they want to be a good employer, it’s about wages and conditions,” Nilsson stated.
-
Elon Musk1 week ago
Elon Musk teases crazy new Tesla FSD model: here’s when it’s coming
-
Elon Musk6 days ago
Elon Musk confirms Tesla AI6 chip is Project Dojo’s successor
-
News6 days ago
Tesla Model Y L reportedly entered mass production in Giga Shanghai
-
Elon Musk1 week ago
Tesla CEO Elon Musk details massive FSD update set for September release
-
Cybertruck6 days ago
Tesla’s new upgrade makes the Cybertruck extra-terrestrial
-
News4 days ago
Elon Musk reaffirms Tesla Semi mass production in 2026
-
Elon Musk1 week ago
Tesla ‘activist shareholders’ sue company and Elon Musk for Robotaxi rollout
-
News1 week ago
Elon Musk explains why Tesla stepped back from Project Dojo