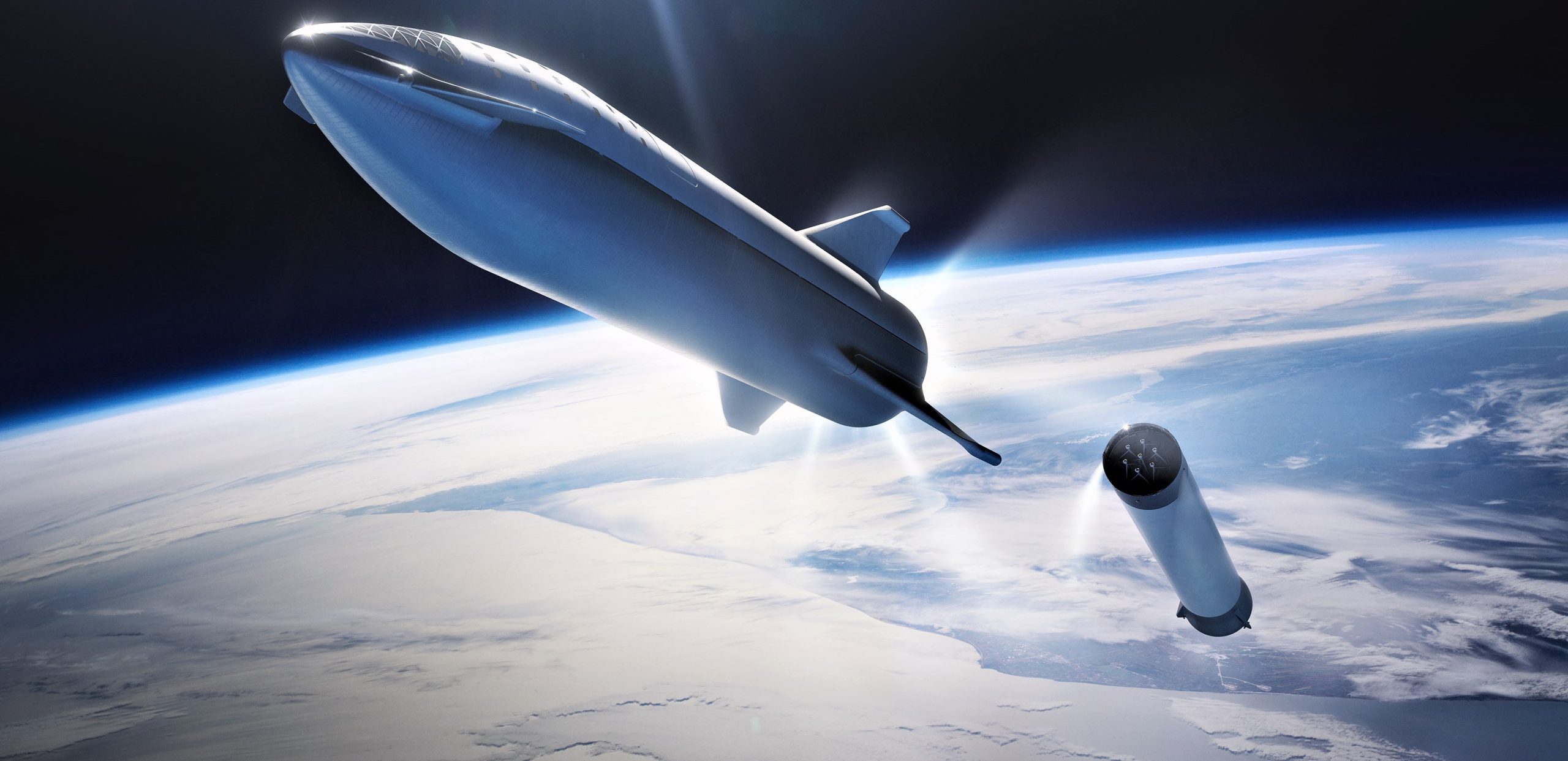
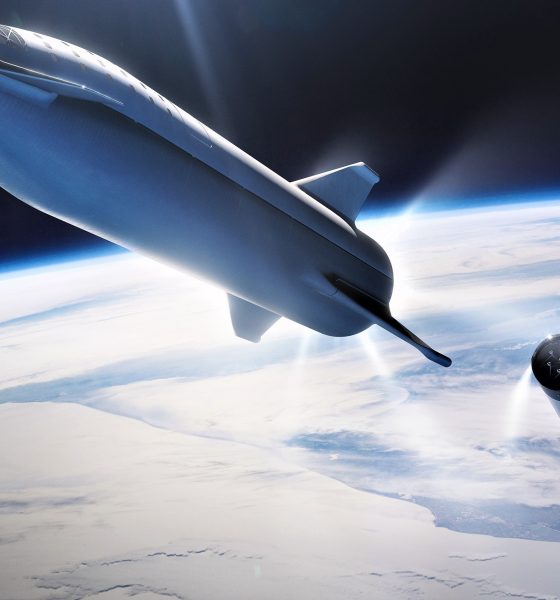
News
SpaceX CEO Elon Musk explains Starship’s ‘transpiring’ steel heat shield in Q&A
Speaking in a late-December 2018 interview with Popular Mechanics’ editor-in-chief, SpaceX CEO Elon Musk shared considerable insight into the thought processes that ultimately led him to – in his own words – “convince” his team that the company’s BFR rocket (now Starship and Super Heavy) should pivot from an advanced composite structure to a relatively common form of stainless steel.
Aside from steel’s relative ease of manipulation and affordability, Musk delved into the technical solution he arrived at for an advanced, ultra-reusable heat shield for Starship – build it out of steel and use water (or liquid methane) to wick reentry heat away.
When going to ~1750 Kelvin, specific heat is more important than latent heat of vaporization, which is why cryogenic fuel is a slightly better choice than water
— Elon Musk (@elonmusk) January 22, 2019
Although there has been some successful experimental research done on “transpirational” heat shields (relying on the heat capacity of vaporizing liquids or gases to soak up thermal energy during orbital rocket reentries), Musk is by no means wrong when he says that a stainless steel sandwich-hulled spaceship regeneratively cooled by microscopic holes and liquid water or propellant “has never been proposed before”. While the basic concept probably arose somewhere over the last 50-100 years, it does not appear that any serious theoretical or experimental research has been conducted to explore transpiration-cooled metallic heat shields, where metallic thermal protection systems (TPS) are already fairly exotic and unproven in the realm of modern aerospace.
“Very easy to work with steel. Oh, and I forgot to mention: [SpaceX’s high-quality] carbon fiber is $135 a kilogram, 35 percent scrap, so you’re starting to approach almost $200 a kilogram. [301] steel is $3 a kilogram.” – Elon Musk
While Musk’s solution could dramatically simplify what is needed for Starship’s high-performance heat shield, a stainless steel sandwich on half of Starship offers another huge benefit: the spacecraft can still gain many of the mass ratio benefits of stainless steel balloon tanks (metal tanks so thin that they collapse without positive pressure) while retaining structural rigidity even when depressurized. At the end of the day, Musk very well might be correct when he states that a stainless steel Starship can ultimately be more mass-efficient (“lighter”) than a Starship built out of advanced carbon composites, a characteristic he rightly describes as “counterintuitive”.
- Starhopper and SpaceX’s spartan assembly facilities are pictured here, showing the inside of the aft section and a completed tank dome. (Austin Barnard)
- Starship has been shown with actuating fins and canard wings since SpaceX’s September 2018 update. (SpaceX)
What does Science™ have to say?
Based on research done in the 2010s by German space agency (DLR), a porous thermal protection material called Procelit 170 (P170) – 91% aluminum oxide and 9% silicon oxide – was cooled from a peak heat of ~1750 C (3200 F) to ~25 C (75 F) during wind tunnel testing, demonstrating that an average of 0.065 kg (~2.3 oz) of water per second would be needed to cool a square meter of P170 to the same degree, assuming a heating rate of around 200 kW/m^2. Given that 300-series stainless steels have a comparatively huge capacity for radiating heat at high temperatures, will be dramatically thinner than Procelit in any given Starship use-case, and will not need to be cooled all the way to 25C/75F during hot operations, the DLR-derived number is barely relevant without another round of wind tunnel tests focused on metallic thermal protection systems. Still, it allows for the creation of a sort of worst-case scenario for BFS/Starship’s water-cooled shield.
Assuming that the windward side of Starship’s regeneratively cooled heat shield has roughly the same surface area as half of a cylinder, 800 m^2 (8600 ft^2) will have to be actively cooled with water, translating to a water consumption rate of approximately 52 kg/s (115 lb/s) if the entire surface is being subjected to temperatures around ~1750 C. That is, of course, a grossly inaccurate generalization, as aerodynamic surfaces dramatically shape, dissipate, and concentrate airflows (and thus heat from friction) in complex and highly specific ways. Much like NASA’s Space Shuttle or DLR’s theoretical SpaceLiner, the reality of reentry heating is that that heat typically ends up being focused at leading edges and control surfaces, which thus require uniquely capable versions of thermal protection (TPS). Shuttle used fragile reinforced carbon-carbon tiles at those hotspots, while DLR was exploring water cooling as a viable and safer alternative for SpaceLiner.
- Starship’s first full-scale prototype is being rapidly assembled in South Texas. (NASASpaceflight – bocachicagal)
- Starship’s first full-scale prototype is being rapidly assembled in South Texas. (NASASpaceflight – bocachicagal)
- Meanwhile, giant 9m-diameter tank domes are being assembled and welded together a few hundred feet away from Starhopper. (NSF – bocachicagal)
- SpaceX’s Starhopper seen in a January render and a January photo. (SpaceX/Elon Musk)
- BFS seen standing vertically on the pads of its tripod fins. (SpaceX)
- A NASA team—via a US Navy aircraft—captured high-resolution, calibrated infrared imagery of Space Shuttle Discovery’s lower surface in addition to discrete instrumentation on the wing, downstream, and on the Boundary Layer Transition Flight Experiment protuberance. In the image, the red regions represent higher surface temperatures. (NASA)
Aside from heat flux, it’s also unclear when or how long the cooling system will need to be supplied with water during potential Starship reentries. At worst, the spacecraft would need to supply a constant 50+ kg/s throughout a 5+ minute (600+ second) regime of high-velocity, high-drag reentry conditions. Assuming that Starship will need to rely heavily on aerobraking to maintain efficient interplanetary operations, it might have to perform 2+ active-cooling cycles per reentry, potentially requiring a minimum of 15 tons of water per reentry. Given that SpaceX intends (at least as of September 2018) for Starship to be able to land more than 100 tons on the surface of Mars, 15t of water would cut drastically into payload margins and is thus likely an unfeasibly large mass reserve or any given interplanetary mission.
“You just need, essentially, [a stainless-steel sandwich]. You flow either fuel or water in between the sandwich layer, and then you have [very tiny] perforations on the outside and you essentially bleed water [or fuel] through them … to cool the windward side of the rocket.” – SpaceX CEO Elon Musk (Popular Mechanics, December 2018)
The assumptions needed for the above calculations do mean that 30T is an absolute worst-case scenario for a regeneratively-cooled Starship reentry, given that SpaceX may only have to vigorously cool a small fraction of its windward surface and will likely be able to cut more than half of the water needed by allowing Starship’s steel skin to heat quite a lot while still staying well below its melting point (likely around 800C/1500F or higher). This also fails to account for the fact that a regeneratively-cooled stainless steel heat shield would effectively let SpaceX do away with what would otherwise be a massive and heavy ablative heat shield and mounting mechanism. Perhaps the benefits of stainless steel might ultimately mean that carrying around 10-30T of coolant is actually performance-neutral or a minimal burden when all costs and benefits are properly accounted for.
Probability at 60% & rising rapidly due to new architecture
— Elon Musk (@elonmusk) December 27, 2018
Musk clearly believes with almost zero doubt that a stainless steel Starship and booster (Super Heavy) is the way forward for the company’s BFR program, and he has now twice indicated that the switch away from advanced carbon composites will actually “accelerate” the rocket’s development schedule. For now, all we can do is watch as the first Starship prototype – meant to perform short hop tests ASAP – gradually comes into being in South Texas.

News
Tesla analyst compares Robotaxi to Waymo: ‘The contrast was clear’
“In short, robotaxi felt like a more luxurious service for half the cost and the driving felt more human-like.”
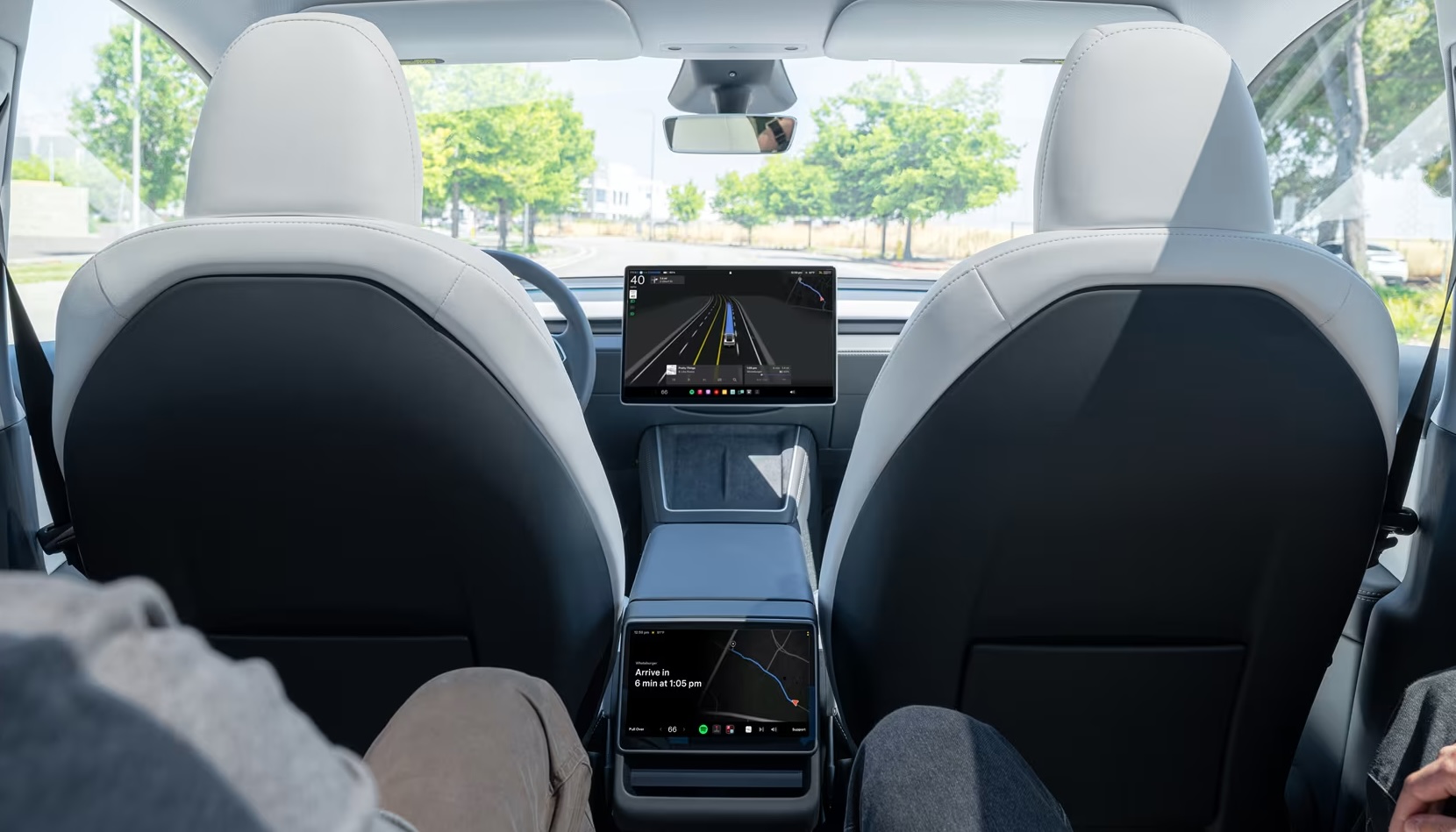
Tesla analyst Jed Dorsheimer of Wall Street firm William Blair compared the company’s Robotaxi platform to Waymo’s driverless ride-sharing program, and had a clear-cut consensus over which option was better in terms of rider experience.
Dorsheimer visited Austin recently to ride in both Tesla’s Robotaxi ride-sharing program and Waymo, which has operated slightly longer than Tesla has in the city. Tesla started rides on June 22, while Waymo opened its vehicles to the public in March.
A Tesla Model Y L Robotaxi is a legitimate $47k Waymo killer
The analyst gave both platforms the opportunity to present themselves, and by the end of it, one was better than the other in terms of rider experience. However, he noted that both platforms gave safe and smooth rides.
Overall, there was a tremendous difference in the feel and environment of each option.
Tesla Robotaxi vs. Waymo
Dorsheimer said that Tesla’s first big advantage was vehicle appearance. Robotaxi uses no external equipment or hardware to operate; just its exterior cameras. Meanwhile, Zoox and Waymo vehicles utilize LiDAR rigs on their vehicles, which made them “stick out like a sore thumb.”
“In contrast, the robotaxis blended in with other Teslas on the road; we felt inconspicuous flowing with the traffic,” he added.
The next big victory went in the way of Robotaxi once again, and it concerned perhaps the most important metric in the ridesharing experience: price.
He continued in the note:
“Confirming our thesis, robotaxi was half the price of Uber, showing its ability to win market share by weaponizing price.”
In terms of overall performance, Dorsheimer noted that both platforms provided safe and “top-notch” experiences. However, there was one distinction between the two and it provided a clear consensus on which was better.
He said:
“In Austin, we took multiple robotaxi and Waymo rides; the contrast was clear. Aside from the visual difference between each pulling up to the curb, the robotaxi was comfortable and familiar, and it felt as though a friendly ghost chauffeur was driving our personal car. Driving was smooth and human-like, recognizing and patiently waiting for pedestrians, switching into less crowded lanes, patiently waiting to execute a safe unprotected turn, and yet, discerning and confident enough to drive through a light that just turned yellow, so as not to slam on the brakes.
Waymo also provided a top-notch service, and we did not encounter any safety concerns, but if we were to be overly critical, it felt more … robotic. In the cabin, you have to listen to an airline-esque preamble on Waymo and safety protocols, and during the ride, you can hear all the various spinning lidar sensors spooling up and down with electronic whizzing sounds.”
Tesla Robotaxi provides an experience that seems to be more catered toward a realistic ride experience. You can control the music, the cabin temperature, and transitioning your travel from one vehicle to the next during a trip will continue your entertainment experience.
If your first trip ends in the middle of a song, your next trip will pick up the music where it left off.
Meanwhile, Waymo’s experience sounds as if it is more focused on rider expectations, and not necessarily providing a ride that felt catered to the occupants. Still, what’s important is that both platforms provided safe rides.
Dorsheimer ended the note with one last tidbit:
“In short, robotaxi felt like a more luxurious service for half the cost and the driving felt more human-like.”
News
Tesla offers new deal on used inventory that you won’t want to pass up
Tesla opened up lease deals on used Model 3 and Model Y inventory in California and Texas on Tuesday, marking the first time it has launched the option on pre-owned cars.
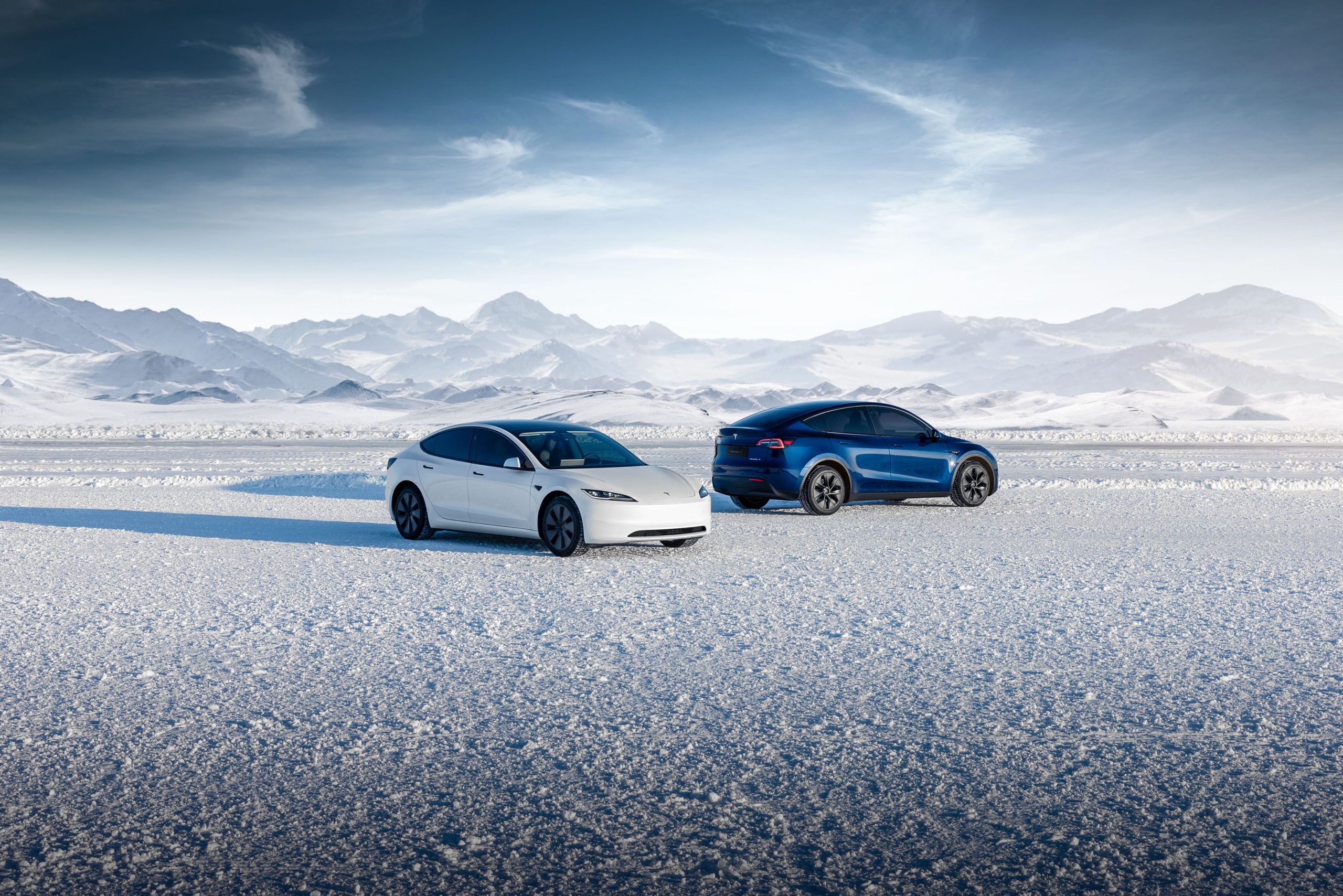
Tesla is offering a new deal on its used vehicle inventory that consumers looking for a great deal won’t want to pass up.
Traditionally, Tesla has not allowed potential car buyers to lease its used inventory. The only two options were to buy with cash or finance it through Tesla or a bank.
However, with the elimination of the $7,500 new and $4,000 used EV tax credits, Tesla is breaking its own rules and is now offering lease deals on its used vehicle inventory, but only in a couple of states, as of right now.
Tesla is ready with a perfect counter to the end of US EV tax credits
Tesla opened up lease deals on used Model 3 and Model Y inventory in California and Texas on Tuesday, marking the first time it has launched the option on pre-owned cars.
The deals are tremendous and can cost as little as $0 down and under $225 per month for some vehicles.
Lease a Pre-Owned Model 3 or Y
As low as $0 down & $225/month
Now available in CA & TX https://t.co/LRYRIZP8VZ
— Tesla North America (@tesla_na) August 19, 2025
Tesla also allows customers to buy the vehicle at the end of their lease deal, which enables some really great ways to end up an owner of the car you plan to drive for the next two or three years.
The lease deal also helps Tesla rid itself of older vehicles that might not be of future use to the company. It formerly planned to use leased vehicles in its eventual Robotaxi fleet, but many of the cars in its used inventory have Hardware 3, which is less capable than Hardware 4, which is installed in the new Model 3 and Model Y.
More importantly, Tesla is giving people yet another way to be in the market for a Tesla before the tax credit ends on September 30.
Elon Musk
Tesla Model Y L might not come to the U.S., and it’s a missed opportunity
The Model Y L has a variety of big changes that would be advantageous for the U.S. market, including a longer wheelbase, more comfortable seats, a third row that appears to be more spacious than Tesla’s six-seat Model Y that it previously offered, B-Pillar vents for rear passengers, and more.
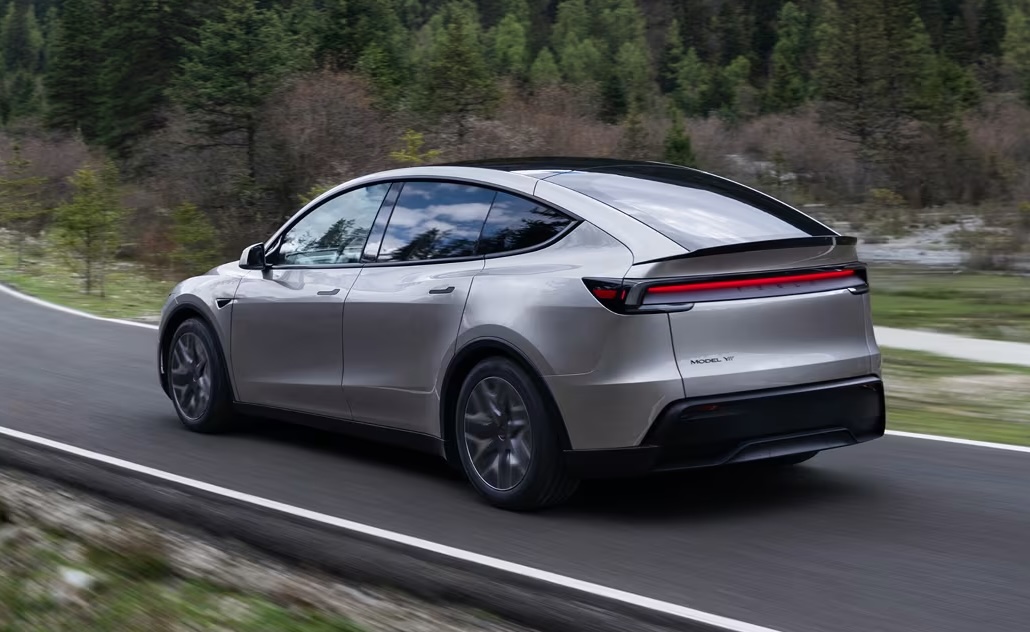
Tesla’s new Model Y L might not come to the U.S., CEO Elon Musk said this morning.
It’s a missed opportunity, and I’m not the only one who feels this way.
In the past, I have personally written a handful of articles about what Tesla owners have been wanting in the United States: a full-sized SUV, or at least a vehicle that is larger than the Model Y but less of a crossover than the Model X.
Tesla is missing one type of vehicle in its lineup and fans want it fast
The only thing that Tesla has announced that even slightly matches this sort of idea is the Robovan, which is, optimistically, several years off because it lacks a steering wheel and pedals and will require Full Self-Driving to be fully autonomous.
Even if Tesla launches FSD next year, it will take a year or two to figure out manufacturing, go through regulatory hurdles with the EPA, and eventually enter mass production for customers.
The Model Y L has a variety of big changes that would be advantageous for the U.S. market, including a longer wheelbase, more comfortable seats, a third row that appears to be more spacious than Tesla’s six-seat Model Y that it previously offered, B-Pillar vents for rear passengers, and more.
However, Musk said it won’t come to the U.S. until next year, and that it “might not ever, given the advent of self-driving in America.”
This variant of the Model Y doesn’t start production in the US until the end of next year.
Might not ever, given the advent of self-driving in America.
— Elon Musk (@elonmusk) August 20, 2025
To be blunt, I’m not sure if I truly believe that Musk thinks the Model Y L won’t come to the U.S. Some believe he said this to not Osborne Effect Model Y sales here, which seems more likely than anything.
Tesla Model Y L gets disappointingly far production date in the United States
People have been buying the Model Y for two years more than any other car in the world. To act as if many families would not appreciate the extra space seems very strange; a big complaint with the Model Y is that it simply does not fit larger families.
If you have four kids, you’re forced into the Model X, which might be too expensive for some families, as it starts at $79,990.
While Tesla’s focus is undoubtedly on autonomy, it is important to remember that some people still really enjoy the act of driving their cars. Tesla has worked very hard to create a fun and sporty driving experience, especially in the new Model Y. Many consumers, including myself, like to take advantage of that.
Autonomy might eventually take over human driving completely, but in the near term, it does not seem as if that is the case. Even if someone were interested in never driving again, this longer and more spacious Model Y L would be an ideal option for American families that need the room for at least six passengers.
Quite a few big names in the Tesla community share this sentiment:
I’m a little surprised by this.
I think the Model Y L would sell extremely well in North America, even with the advent of self-driving. Americans love their larger SUVs. Bigger families here want the Model Y L. There is a need in North America for larger all-electric SUVs at a… https://t.co/v7D1IpCnET
— Sawyer Merritt (@SawyerMerritt) August 20, 2025
More than likely, Musk does not want to announce a more attractive option than the current Model Y, as many consumers would likely wait a year or two for the L in an effort to have more space.
In all honesty, I see the Model Y L coming to the United States, as it truly fits the bill as an ideal car for the modern American family.
-
Elon Musk2 weeks ago
Elon Musk teases crazy new Tesla FSD model: here’s when it’s coming
-
Elon Musk2 weeks ago
Elon Musk confirms Tesla AI6 chip is Project Dojo’s successor
-
News2 weeks ago
Tesla Model Y L reportedly entered mass production in Giga Shanghai
-
Elon Musk2 weeks ago
Tesla CEO Elon Musk details massive FSD update set for September release
-
Cybertruck2 weeks ago
Tesla’s new upgrade makes the Cybertruck extra-terrestrial
-
News1 week ago
Elon Musk reaffirms Tesla Semi mass production in 2026
-
News2 weeks ago
Elon Musk explains why Tesla stepped back from Project Dojo
-
News2 weeks ago
Tesla Model 3 filings in China show interesting hardware addition