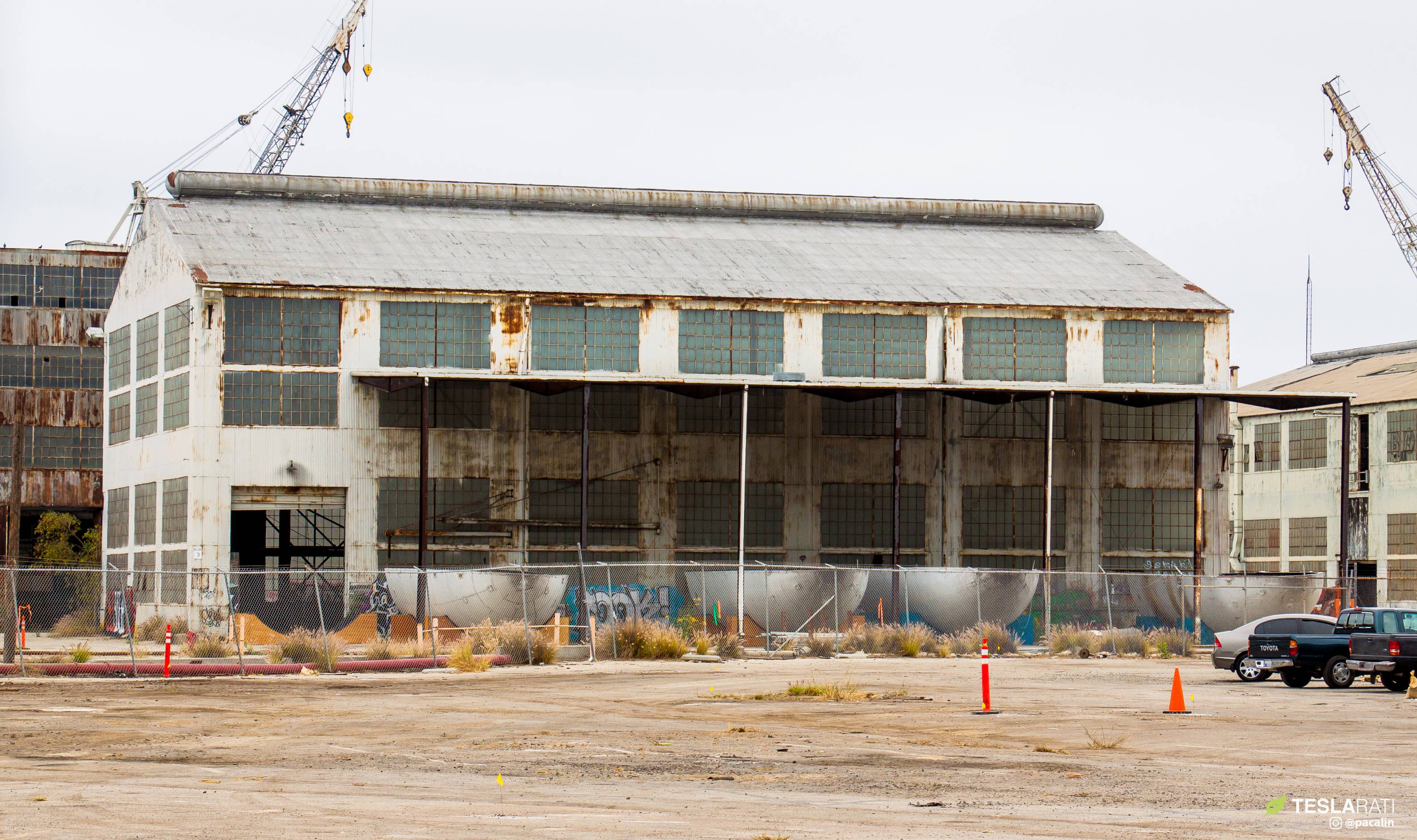
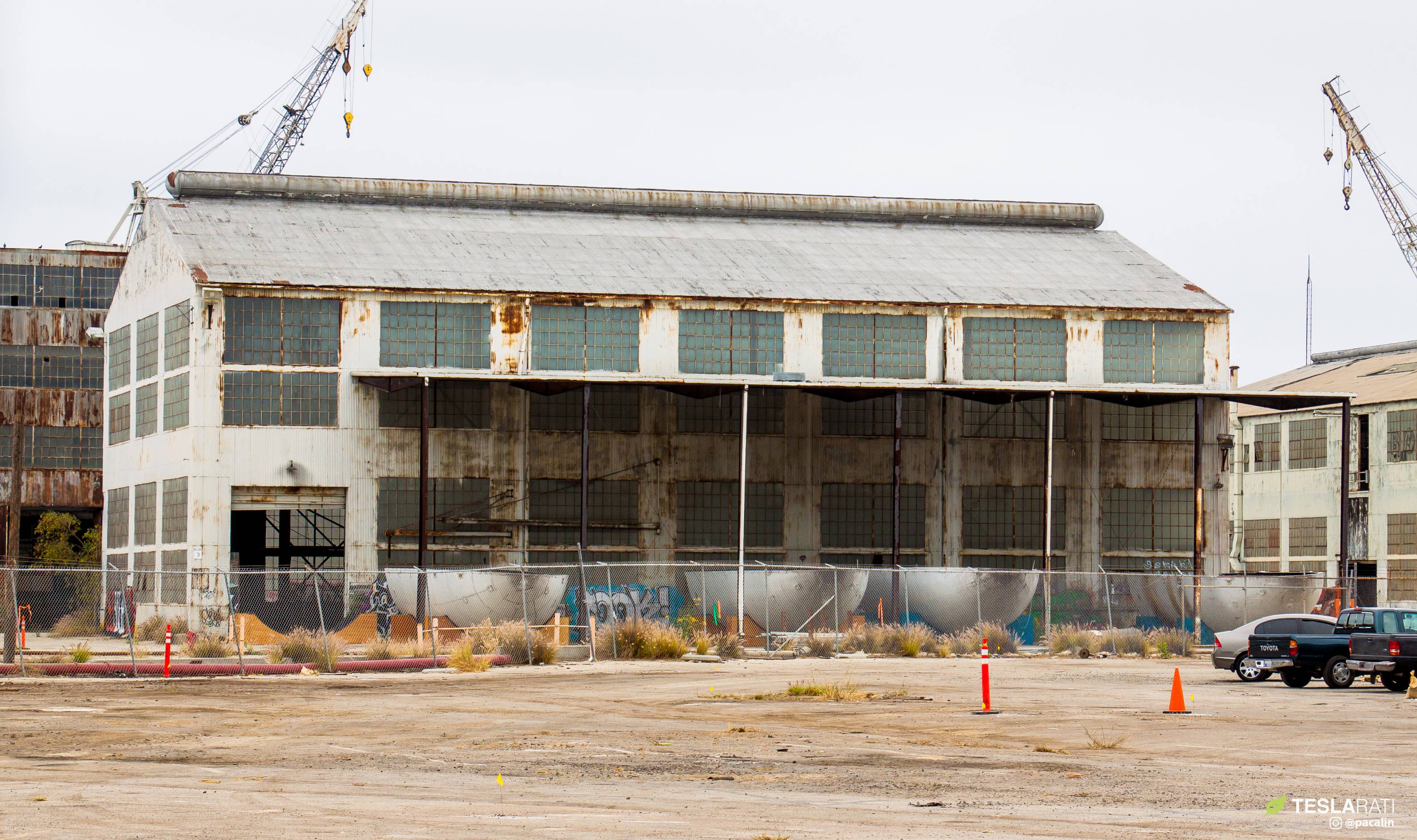
News
SpaceX resurrects California Starship factory plan just one year after abandoning it
Just nine months after scrapping temporary Starship facilities built at a Los Angeles port, the company has unexpectedly reconsidered that decision, restarting talks to build a steel Starship factory in California.
In March 2018, nearly two years ago, the public first became aware of SpaceX’s plans to build a Starship factory in Port of Los Angeles. Begun while Starship was still known as BFR (Big Falcon Rocket) and designed to be built almost entirely out of carbon-fiber composites, the company’s first in-house effort to build its next-generation rocket began in an unassuming tent erected on port property around December 2017. Unintentionally foreshadowing the future of both Tesla Model 3 and SpaceX Starship production, that temporary tent was completed in just a month or two and officially began supporting BFR prototype production in April 2018.
In December 2018, CEO Elon Musk rebranded BFR as Starship and revealed that SpaceX would take the extraordinary step of redesigning the fully-reusable rocket to use stainless steel instead of carbon fiber. One year after SpaceX began building carbon fiber hardware, Musk moved quickly to make the radical move to steel permanent, literally scrapping its BFR prototype tent and abandoning its lease of a separate facility that was meant to host a more permanent composite Mars rocket factory in the near future. Now, almost exactly a year canceling its Port of LA factory, SpaceX has returned with plans to build and finish new port-based Starship production facilities just a few months from now.
Completed in September 2018, the closest SpaceX ever got to producing its 2017 BFR iteration was a large ring-like composite structure, also known as a barrel section. Measuring some 9m (30 ft) wide and 4-6m (12-20 ft) long, both 2016, 2017, and 2018 variants of SpaceX’s next-generation fully-reusable rocket would have been assembled from a number of similar components — all to be built out of carbon composites with giant mandrels (a bit like inverse molds).
While it’s more than likely that SpaceX could have managed the feat, building a reusable orbital spacecraft like Starship out of carbon fiber posed a vast array of challenges. When Musk revealed that SpaceX would move from carbon fiber to steel in December 2018, the CEO went into some detail to explain several of those challenges and why the major change was thus worth the substantial body of work it would force the company to scrap and redo from scratch.
The two biggest hurdles for BFR were quite simple. From a technical perspective, carbon fiber is dramatically less temperature-resistant than most metals (especially steel), meaning that despite it offering a much higher strength-to-weight ratio on paper, almost every inch of the spaceship and booster’s exposed surfaces would have to be insulated. For Starship, this would be exceptionally challenging given that the spacecraft must fundamentally be able to survive numerous orbital-velocity reentries with little to no refurbishment in between. While a steel Starship would still need a proper heat shield on its windward half, the other half of its steel hull could likely be almost entirely unshielded thanks to the fact that most steels remain structural sound at much higher temperatures.
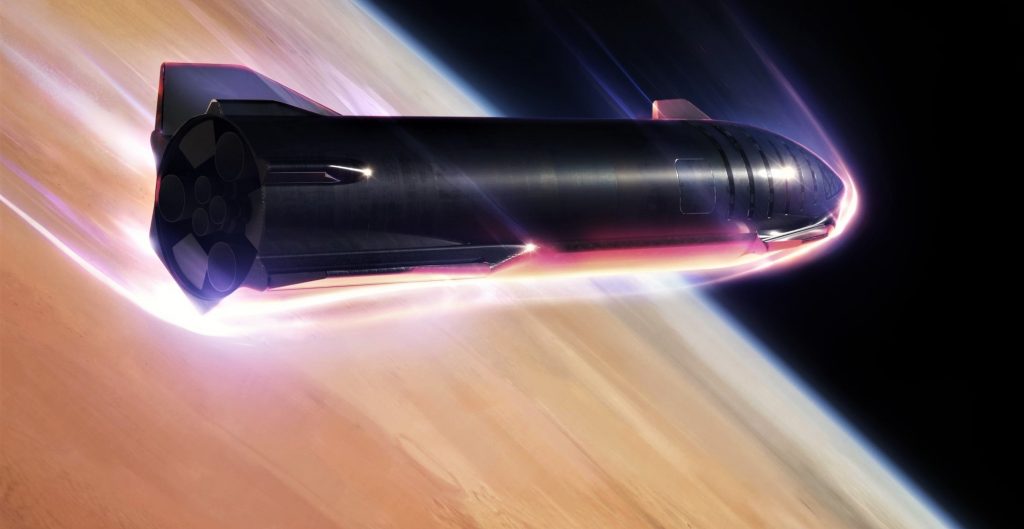
Beyond the “delightfully counterintuitive” technical properties that could make a steel Starship as light or even lighter than the carbon composite alternative, Musk also noted that a huge motivator for the switch was the fact that the cutting-edge composites SpaceX would have to buy were incredibly expensive. In September 2019, Musk stated that composites would have cost some $130,000 per ton, whereas a ton of the stainless steel SpaceX is now using can be purchased for just $2500. In simpler terms, from a material cost perspective, steel Starships and Super Heavy boosters could cost an incredible 50 times less than their carbon composite twins.
Port Factory 2.0
For now, it’s unclear exactly what SpaceX foresees for Starship’s newly re-proposed Port of LA factory. The same primary constraint remains: there is still no affordable way to ship full-scale 9m-diameter Starship hardware by road. The most likely explanation for the resurrected interest in port facilities is that SpaceX still wants to keep some major aspects of Starship manufacturing within reach of California’s vast aerospace talent pool, as well as the company’s own California headquarters, situated just 20 or so miles from Port of LA.
At the same time, SpaceX probably has all the space it could possibly want at its Hawthorne, CA headquarters after a massive Triumph facility was recently vacated, meaning that any intentional expansion in Port of LA is probably motivated by the need to transport massive rocket parts from California to Texas and Florida. Daily Breeze also reports that “SpaceX would manufacture its…Starship spacecraft and…Super Heavy [booster] on the property” if it receives approval, seemingly implying interest in full-scale rocket production at its prospective port factory.
Regardless of whether SpaceX wants to build smaller Starship subcomponents (i.e. nose cones, header tanks, fins, plumbing, crew compartments, etc.) or complete spaceships and boosters, the company is seemingly far more eager to get port facilities in place, this time around. Specifically, SpaceX told a city council member that it wanted to get a Port of LA facility up and running just 90 days after it expressed new interest in the concept.
To do so, SpaceX will copy the methods used to create both Tesla’s General Assembly 4 factory addition and its own massive Starship production space in South Texas, relying on Sprung Instant Structures to erect a massive semi-permanent tent or two in an extremely short period of time. Unfortunately, because of how abruptly SpaceX abandoned its Port of LA factory lease, the company will have to repeat the permitting and environmental review process from scratch, making it very unlikely that it will be able to begin construction within the next month or two.
Regardless, SpaceX certainly remains as agile as ever. Stay tuned for updates on this surprise resurgence of plans for a Port of LA Starship factory.
Check out Teslarati’s Marketplace! We offer Tesla accessories, including for the Tesla Cybertruck and Tesla Model 3.
Elon Musk
Tesla begins expanding Robotaxi access: here’s how you can ride
You can ride in a Tesla Robotaxi by heading to its website and filling out the interest form. The company is hand-picking some of those who have done this to gain access to the fleet.
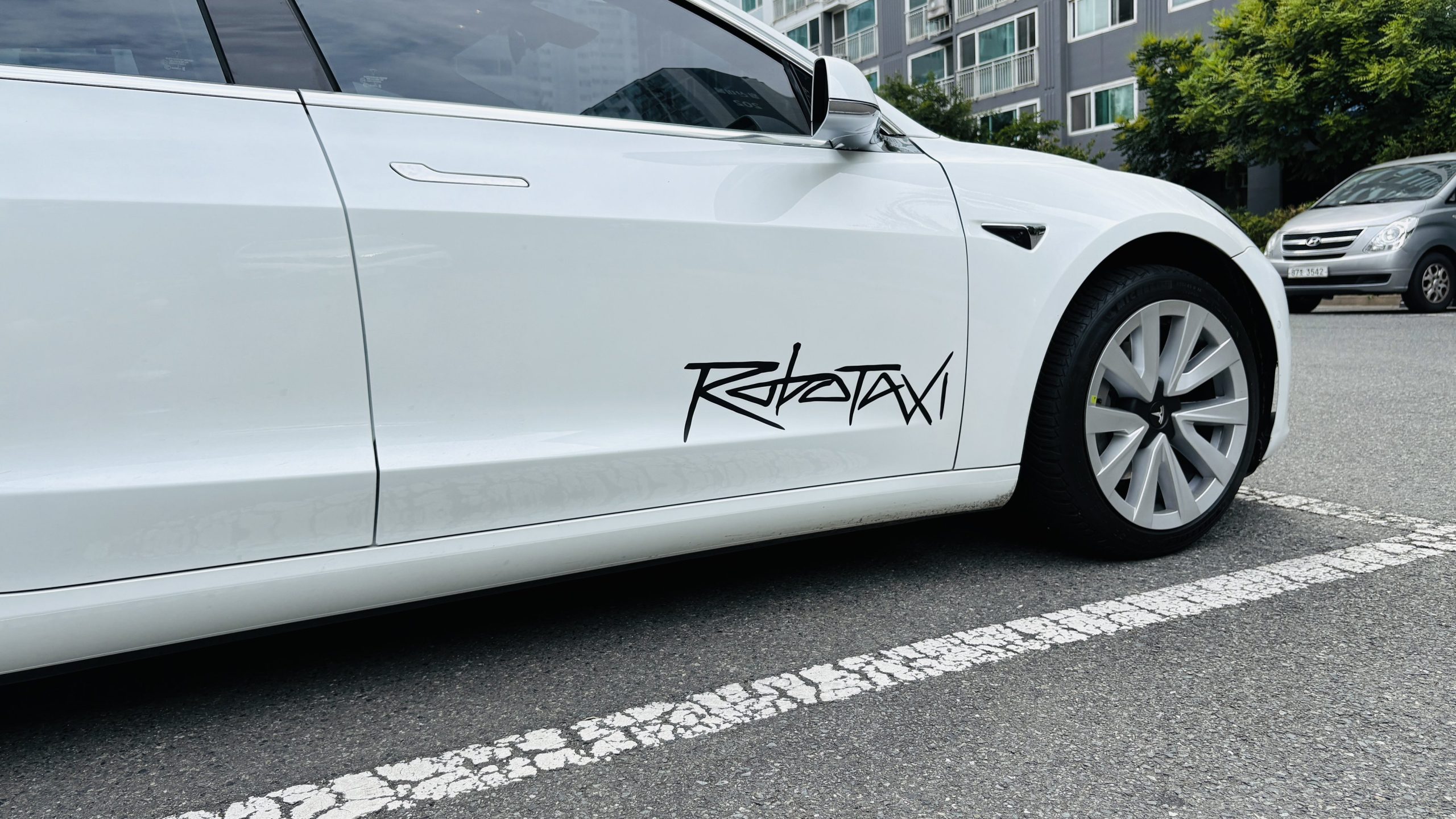
Tesla has begun expanding Robotaxi access beyond the initial small group it offered rides to in late June, as it launched the driverless platform in Austin, Texas.
The small group of people enjoying the Robotaxi ride-hailing service is now growing, as several Austin-area residents are receiving invitations to test out the platform for themselves.
The first rides took place on June 22, and despite a very small number of very manageable and expected hiccups, Tesla Robotaxi was widely successful with its launch.
Tesla Robotaxi riders tout ‘smooth’ experience in first reviews of driverless service launch
However, Tesla is expanding the availability of the ride-hailing service to those living in Austin and its surrounding areas, hoping to gather more data and provide access to those who will utilize it on a daily basis.
Many of the people Tesla initially invited, including us, are not local to the Austin area.
There are a handful of people who are, but Tesla was evidently looking for more stable data collection, as many of those early invitees headed back to where they live.
The first handful of invitations in the second round of the Robotaxi platform’s Early Access Program are heading out to Austin locals:
I just got a @robotaxi invite! Super excited to go try the service out! pic.twitter.com/n9mN35KKFU
— Ethan McKanna (@ethanmckanna) July 1, 2025
Tesla likely saw an influx of data during the first week, as many traveled far and wide to say they were among the first to test the Robotaxi platform.
Now that the first week and a half of testing is over, Tesla is expanding invites to others. Many of those who have been chosen to gain access to the Robotaxi app and the ride-hailing service state that they simply filled out the interest form on the Robotaxi page of Tesla’s website.
That’s the easiest way you will also gain access, so be sure to fill out that form if you have any interest in riding in Robotaxi.
Tesla will continue to utilize data accumulated from these rides to enable more progress, and eventually, it will lead to even more people being able to hail rides from the driverless platform.
With more success, Tesla will start to phase out some of the Safety Monitors and Supervisors it is using to ensure things run smoothly. CEO Elon Musk said Tesla could start increasing the number of Robotaxis to monitors within the next couple of months.
Elon Musk
Tesla analyst issues stern warning to investors: forget Trump-Musk feud

A Tesla analyst today said that investors should not lose sight of what is truly important in the grand scheme of being a shareholder, and that any near-term drama between CEO Elon Musk and U.S. President Donald Trump should not outshine the progress made by the company.
Gene Munster of Deepwater Management said that Tesla’s progress in autonomy is a much larger influence and a significantly bigger part of the company’s story than any disagreement between political policies.
Munster appeared on CNBC‘s “Closing Bell” yesterday to reiterate this point:
“One thing that is critical for Tesla investors to remember is that what’s going on with the business, with autonomy, the progress that they’re making, albeit early, is much bigger than any feud that is going to happen week-to-week between the President and Elon. So, I understand the reaction, but ultimately, I think that cooler heads will prevail. If they don’t, autonomy is still coming, one way or the other.”
BREAKING: GENE MUNSTER SAYS — $TSLA AUTONOMY IS “MUCH BIGGER” THAN ANY FEUD 👀
He says robotaxis are coming regardless ! pic.twitter.com/ytpPcwUTFy
— TheSonOfWalkley (@TheSonOfWalkley) July 2, 2025
This is a point that other analysts like Dan Ives of Wedbush and Cathie Wood of ARK Invest also made yesterday.
On two occasions over the past month, Musk and President Trump have gotten involved in a very public disagreement over the “Big Beautiful Bill,” which officially passed through the Senate yesterday and is making its way to the House of Representatives.
Musk is upset with the spending in the bill, while President Trump continues to reiterate that the Tesla CEO is only frustrated with the removal of an “EV mandate,” which does not exist federally, nor is it something Musk has expressed any frustration with.
In fact, Musk has pushed back against keeping federal subsidies for EVs, as long as gas and oil subsidies are also removed.
Nevertheless, Ives and Wood both said yesterday that they believe the political hardship between Musk and President Trump will pass because both realize the world is a better place with them on the same team.
Munster’s perspective is that, even though Musk’s feud with President Trump could apply near-term pressure to the stock, the company’s progress in autonomy is an indication that, in the long term, Tesla is set up to succeed.
Tesla launched its Robotaxi platform in Austin on June 22 and is expanding access to more members of the public. Austin residents are now reporting that they have been invited to join the program.
Elon Musk
Tesla surges following better-than-expected delivery report
Tesla saw some positive momentum during trading hours as it reported its deliveries for Q2.
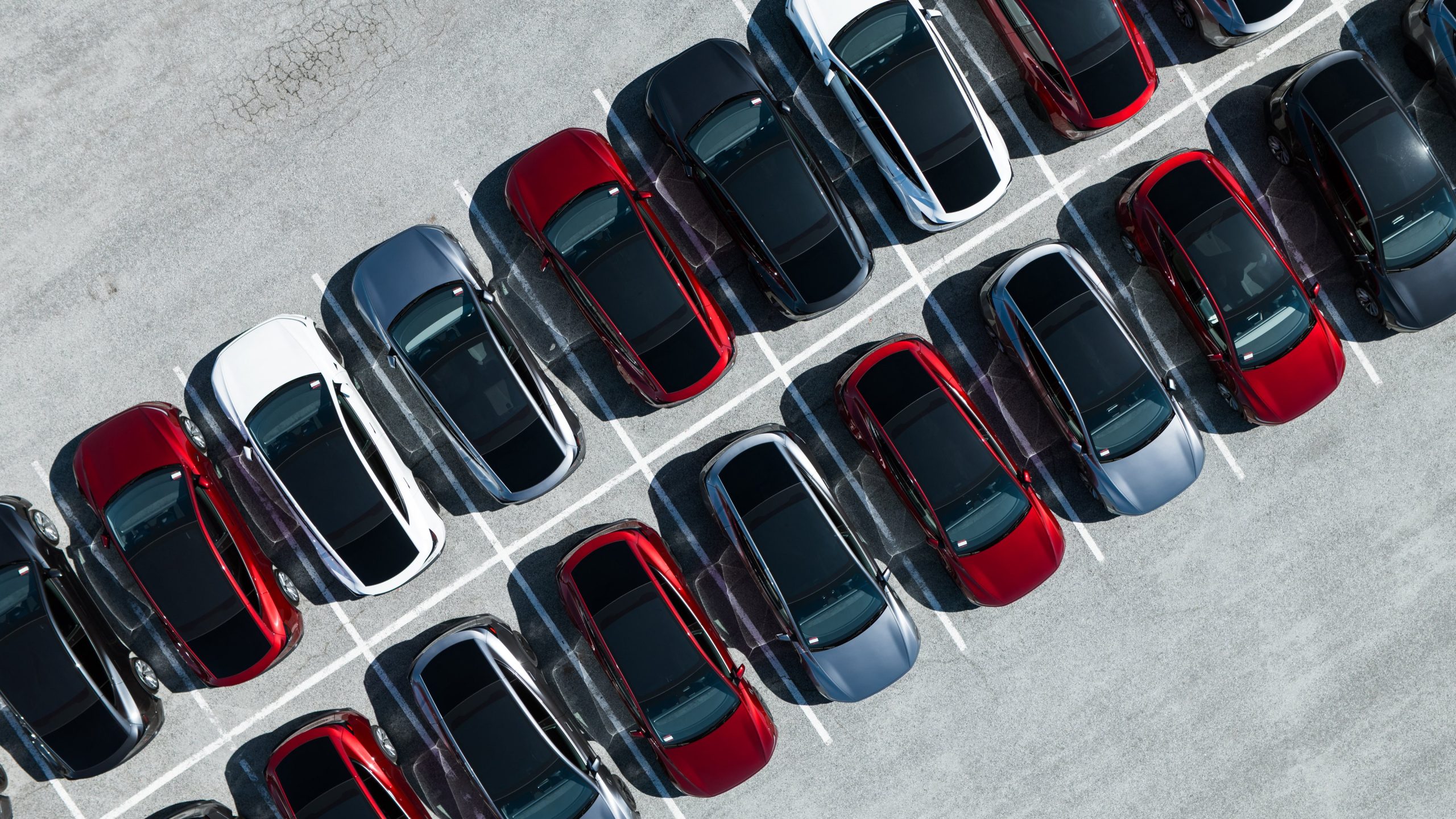
Tesla (NASDAQ: TSLA) surged over four percent on Wednesday morning after the company reported better-than-expected deliveries. It was nearly right on consensus estimations, as Wall Street predicted the company would deliver 385,000 cars in Q2.
Tesla reported that it delivered 384,122 vehicles in Q2. Many, including those inside the Tesla community, were anticipating deliveries in the 340,000 to 360,000 range, while Wall Street seemed to get it just right.
Tesla delivers 384,000 vehicles in Q2 2025, deploys 9.6 GWh in energy storage
Despite Tesla meeting consensus estimations, there were real concerns about what the company would report for Q2.
There were reportedly brief pauses in production at Gigafactory Texas during the quarter and the ramp of the new Model Y configuration across the globe were expected to provide headwinds for the EV maker during the quarter.
At noon on the East Coast, Tesla shares were up about 4.5 percent.
It is expected that Tesla will likely equal the number of deliveries it completed in both of the past two years.
It has hovered at the 1.8 million mark since 2023, and it seems it is right on pace to match that once again. Early last year, Tesla said that annual growth would be “notably lower” than expected due to its development of a new vehicle platform, which will enable more affordable models to be offered to the public.
These cars are expected to be unveiled at some point this year, as Tesla said they were “on track” to be produced in the first half of the year. Tesla has yet to unveil these vehicle designs to the public.
Dan Ives of Wedbush said in a note to investors this morning that the company’s rebound in China in June reflects good things to come, especially given the Model Y and its ramp across the world.
He also said that Musk’s commitment to the company and return from politics played a major role in the company’s performance in Q2:
“If Musk continues to lead and remain in the driver’s seat, we believe Tesla is on a path to an accelerated growth path over the coming years with deliveries expected to ramp in the back-half of 2025 following the Model Y refresh cycle.”
Ives maintained his $500 price target and the ‘Outperform’ rating he held on the stock:
“Tesla’s future is in many ways the brightest it’s ever been in our view given autonomous, FSD, robotics, and many other technology innovations now on the horizon with 90% of the valuation being driven by autonomous and robotics over the coming years but Musk needs to focus on driving Tesla and not putting his political views first. We maintain our OUTPERFORM and $500 PT.”
Moving forward, investors will look to see some gradual growth over the next few quarters. At worst, Tesla should look to match 2023 and 2024 full-year delivery figures, which could be beaten if the automaker can offer those affordable models by the end of the year.
-
Elon Musk2 days ago
Tesla investors will be shocked by Jim Cramer’s latest assessment
-
News1 week ago
Tesla Robotaxi’s biggest challenge seems to be this one thing
-
Elon Musk2 weeks ago
Elon Musk slams Bloomberg’s shocking xAI cash burn claims
-
News2 weeks ago
Texas lawmakers urge Tesla to delay Austin robotaxi launch to September
-
Elon Musk1 week ago
First Look at Tesla’s Robotaxi App: features, design, and more
-
Elon Musk2 weeks ago
Tesla Robotaxis are becoming a common sight on Austin’s public roads
-
Elon Musk2 weeks ago
xAI’s Grok 3 partners with Oracle Cloud for corporate AI innovation
-
Elon Musk2 weeks ago
SpaceX President meets India Minister after Starlink approval