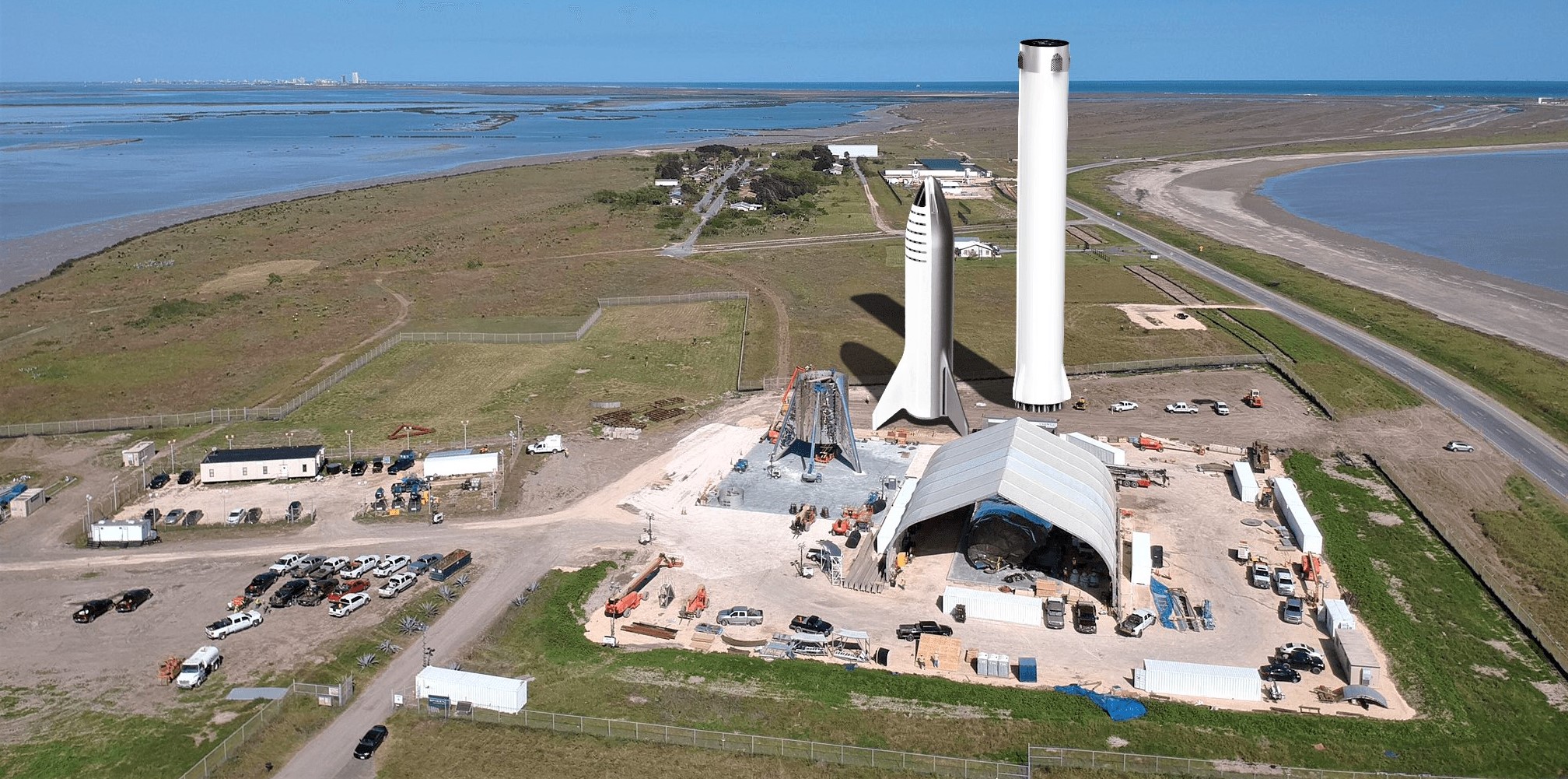
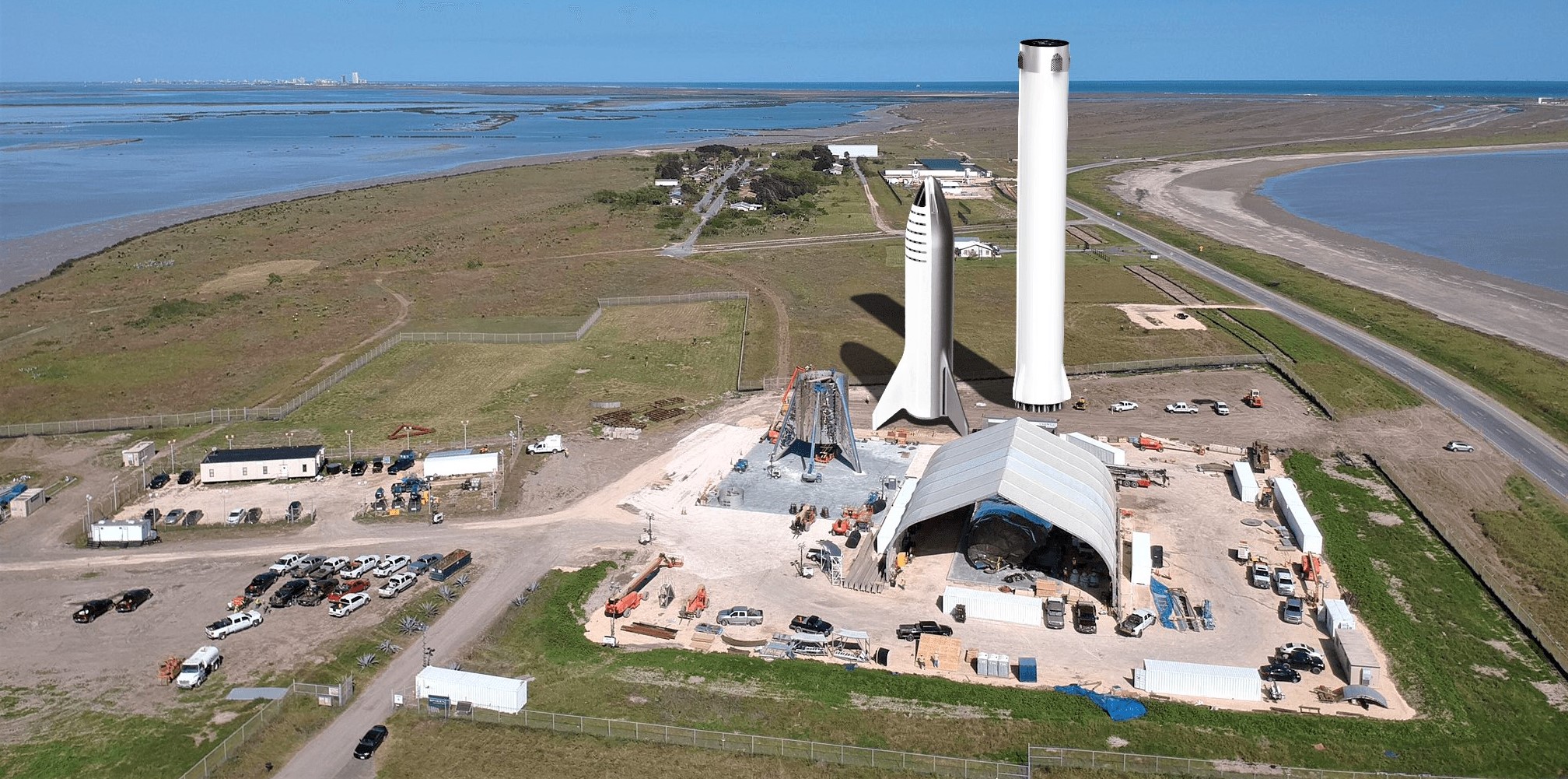
SpaceX
SpaceX will build and launch Starship/Super Heavy in Texas and Florida, says Musk
According to SpaceX CEO Elon Musk, the company has plans to both build and launch BFR’s Starship upper stages and Super Heavy boosters at facilities located in Boca Chica, Texas and Cape Canaveral, Florida.
Indicative of SpaceX and Musk’s rapidly evolving plans for the next-generation, ultra-reusable launch system, the to stainless steel over carbon composites appears to continue to have a range of trickle-down consequences (or benefits) throughout the rocket’s design, production, launch, and operations. Given the 3+ radical, clean-sheet design changes the BFR program has undergone in about as many years, it’s hard to definitively conclude much about the latest iteration. Nevertheless, Musk’s indication that stainless steel BFRs may now be built simultaneously at multiple locations suggests that the construction of steel Starships and Super Heavies could be radically easier (and cheaper) than their composite predecessors.
Over the last several months, SpaceX’s manufacturing plans for the massive Starship and Super Heavy vehicles have effectively been up in the air from a public perspective. Official statements provided in January suggested that the first prototypes would be built in-situ after word broke that SpaceX had prematurely terminated a lease with the Port of Los Angeles, where the company had – throughout 2018 – been planning to construct a dedicated seaside BFR factory.
Likely for a variety of reasons, all of which are unknown, SpaceX apparently no longer has a pressing need for dedicated traditional manufacturing facilities at this point in time. Instead, the company is relying extensively on the largely unprecedented practice of building its first suborbital and orbital Starship and Super Heavy vehicles outdoors, much to the visible discomfort of aerospace industry practitioners, followers, and fans alike.
At a bare minimum, SpaceX’s decision to fabricate and assemble large-scale methalox rocket stages with quite literally zero protection from the elements may be one of the most ‘nontraditional’ things the habitually disruptive company has ever done. At the opposite end of the spectrum, building rockets outside could be perceived as an unfathomably foolish endeavor, radically increasing the risk of dangerous manufacturing defects, foreign objects debris (FOD) mitigation, and – ultimately – major vehicle failures. From such an external perspective, wholly lacking any insight from SpaceX itself, it’s difficult to conclude much of anything.
On the one hand, a highly-disciplined adherence to the tenets of best aerospace industry practices and responsible engineering could probably mitigate the risks of en
Given that the production of orbital-class, super-heavy lift rockets has really only been attempted twice (Saturn V and Russia’s N1), both times with custom-built, environmentally-controlled factories, it’s likely that SpaceX is already suffering from the inherent uncertainty of the tasks at hand; forging new ground – especially in highly technical fields – is rarely easy or forgiving. Given the aforementioned challenges of building large and reliable rockets at all, challenges that regularly topple vehicles built in traditional factories, it will likely remain an open question if SpaceX can consistently build reliable, technologically-advanced rockets and spacecraft outside until those vehicles have quite literally proven themselves in orbit.
Toot Toot! Hopper is chomping at the bit today!
?@BocaChicaGal https://t.co/0ZEXcKOWwH pic.twitter.com/PEm7c12KTi— Chris B – NSF (@NASASpaceflight) March 18, 2019
Difficulties aside, it’s easy to understand why SpaceX (or maybe just Elon) is willing to at least attempt something that has never been done before. If the company could find a way to reliably build complex, high-performance rockets without the need for expensive factories, it could radically change the paradigm of rocketry by reducing the often eye-watering upfront costs of building giant launch vehicles. The ability to build rockets almost independently of dedicated factories or assembly facilities would also allow SpaceX to – as Musk said – build their vehicles where they launch, further minimizing the significant challenges and costs of transporting extremely large structures more than a couple of miles.
Regardless of the major challenges standing between SpaceX and its stainless steel Starship/Super Heavy aspirations, Elon Musk appears to be as confident as ever, frankly stating that Starship’s rate of progress “far exceeds” that of Falcon and Dragon. In other words, the apparent instability of the BFR program may actually end up being to its benefit, potentially resulting in a finished product that simultaneously takes less time to come to fruition and is ultimately much closer to its original design intent. At risk of putting the wrong words into Musk’s mouth, it seems that he believes that SpaceX might be able to arrive at a Starship/Super Heavy combo much closer to Falcon 9 Block 5 than Falcon 9 V1.0 and do so far sooner than most believe is possible.
Only time will tell. In the meantime, there will be plenty of fireworks, beginning as early as this week with the first static fire test – and potential hops – of SpaceX’s massive Starship Hopper. Stay tuned for updates!
Check out Teslarati’s Marketplace! We offer Tesla accessories, including for the Tesla Cybertruck and Tesla Model 3.
News
SpaceX launches Ax-4 mission to the ISS with international crew
The SpaceX Falcon 9 launched Axiom’s Ax-4 mission to ISS. Ax-4 crew will conduct 60+ science experiments during a 14-day stay on the ISS.
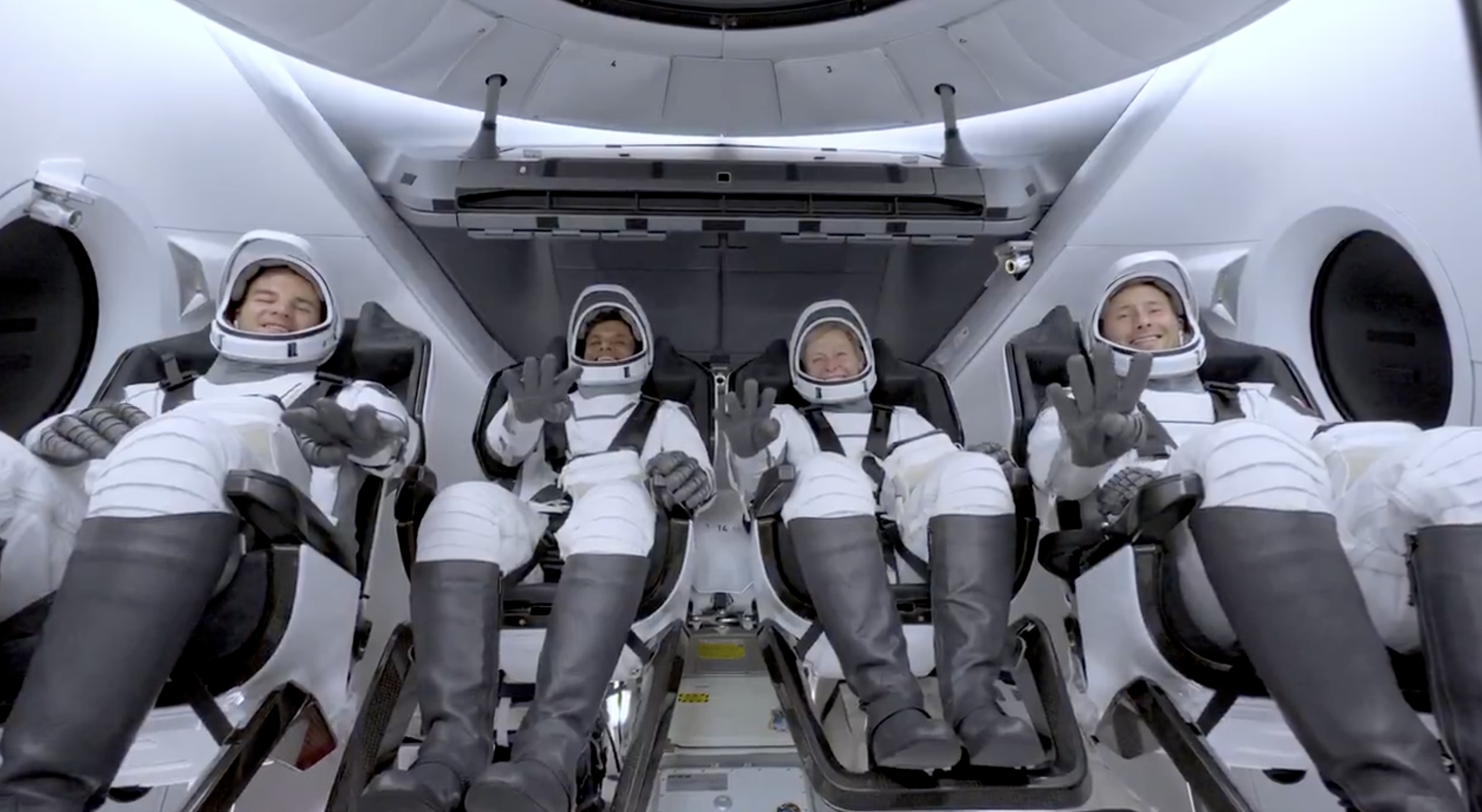
SpaceX launched the Falcon 9 rocket kickstarting Axiom Space’s Ax-4 mission to the International Space Station (ISS). Axiom’s Ax-4 mission is led by a historic international crew and lifted off from Kennedy Space Center’s Launch Complex 39A at 2:31 a.m. ET on June 25, 2025.
The Ax-4 crew is set to dock with the ISS around 7 a.m. ET on Thursday, June 26, 2025. Axiom Space, a Houston-based commercial space company, coordinated the mission with SpaceX for transportation and NASA for ISS access, with support from the European Space Agency and the astronauts’ governments.
The Ax-4 mission marks a milestone in global space collaboration. The Ax-4 crew, commanded by U.S. astronaut Peggy Whitson, includes Shubhanshu Shukla from India as the pilot, alongside mission specialists Sławosz Uznański-Wiśniewski from Poland and Tibor Kapu from Hungary.
“The trip marks the return to human spaceflight for those countries — their first government-sponsored flights in more than 40 years,” Axiom noted.
Shukla’s participation aligns with India’s Gaganyaan program planned for 2027. He is the first Indian astronaut to visit the ISS since Rakesh Sharma in 1984.
Axiom’s Ax-4 mission marks SpaceX’s 18th human spaceflight. The mission employs a Crew Dragon capsule atop a Falcon 9 rocket, designed with a launch escape system and “two-fault tolerant” for enhanced safety. The Axiom mission faced a few delays due to weather, a Falcon 9 leak, and an ISS Zvezda module leak investigation by NASA and Roscosmos before the recent successful launch.
As the crew prepares to execute its scientific objectives, SpaceX’s Ax-4 mission paves the way for a new era of inclusive space research, inspiring future generations and solidifying collaborative ties in the cosmos. During the Ax-4 crew’s 14-day stay in the ISS, the astronauts will conduct nearly 60 experiments.
“We’ll be conducting research that spans biology, material, and physical sciences as well as technology demonstrations,” said Whitson. “We’ll also be engaging with students around the world, sharing our experience and inspiring the next generation of explorers.”
SpaceX’s Ax-4 mission highlights Axiom’s role in advancing commercial spaceflight and fostering international partnerships. The mission strengthens global space exploration efforts by enabling historic spaceflight returns for India, Poland, and Hungary.
News
Starlink Cellular’s T-Mobile service to grow with third-party app data
From Oct 2025, T-Satellite will enable third-party apps in dead zones! WhatsApp, X, AccuWeather + more coming soon.
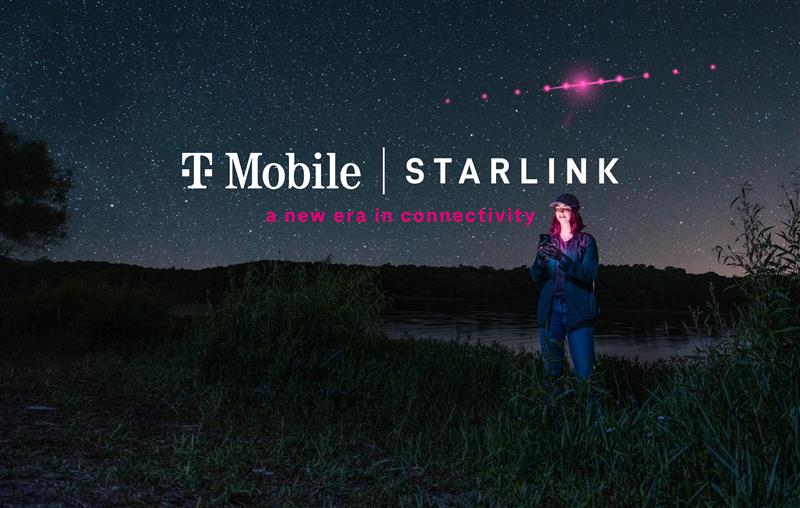
Starlink Cellular’s T-Mobile service will expand with third-party app data support starting in October, enhancing connectivity in cellular dead zones.
T-Mobile’s T-Satellite, supported by Starlink, launches officially on July 23. Following its launch, T-Mobile’s Starlink Cellular service will enable data access for third-party apps like WhatsApp, X, Google, Apple, AccuWeather, and AllTrails on October 1, 2025.
T-Mobile’s Starlink Cellular is currently in free beta. T-Satellite will add MMS support for Android phones on July 23, with iPhone support to follow. MMS support allows users to send images and audio clips alongside texts. By October, T-Mobile will extend emergency texting to all mobile users with compatible phones, beyond just T-Mobile customers, building on its existing 911 texting capability. The carrier also provides developer tools to help app makers integrate their software with T-Satellite’s data service, with plans to grow the supported app list.
T-Mobile announced these updates during an event celebrating an Ookla award naming it the best U.S. phone network, a remarkable turnaround from its last-place ranking a decade ago.
“We not only dream about going from worst to best, we actually do it. We’re a good two years ahead of Verizon and AT&T, and I believe that lead is going to grow,” said T-Mobile’s Chief Operating Officer Srini Gopalan.
T-Mobile unveiled two promotions for its Starlink Cellular services to attract new subscribers. A free DoorDash DashPass membership, valued at $10/month, will be included with popular plans like Experience Beyond and Experience More, offering reduced delivery and service fees. Meanwhile, the Easy Upgrade promotion targets Verizon customers by paying off their phone balances and providing flagship devices like the iPhone 16, Galaxy S25, or Pixel 9.
T-Mobile’s collaboration with SpaceX’s Starlink Cellular leverages orbiting satellites to deliver connectivity where traditional networks fail, particularly in remote areas. Supporting third-party apps underscores T-Mobile’s commitment to enhancing user experiences through innovative partnerships. As T-Satellite’s capabilities grow, including broader app integration and emergency access, T-Mobile is poised to strengthen its lead in the U.S. wireless market.
By combining Starlink’s satellite technology with strategic promotions, T-Mobile is redefining mobile connectivity. The upcoming third-party app data support and official T-Satellite launch mark a significant step toward seamless communication, positioning T-Mobile as a trailblazer in next-generation wireless services.
News
Starlink expansion into Vietnam targets the healthcare sector
Starlink aims to deliver reliable internet to Vietnam’s remote clinics, enabling telehealth and data sharing.

SpaceX’s Starlink expansion into Vietnam targets its healthcare sector. Through Starlink, SpaceX seeks to drive digital transformation in Vietnam.
On June 18, a SpaceX delegation met with Vietnam’s Ministry of Health (MoH) in Hanoi. SpaceX’s delegation was led by Andrew Matlock, Director of Enterprise Sales, and the discussions focused on enhancing connectivity for hospitals and clinics in Vietnam’s remote areas.
Deputy Minister of Health (MoH) Tran Van Thuan emphasized collaboration between SpaceX and Vietnam. Tran stated: “SpaceX should cooperate with the MoH to ensure all hospitals and clinics in remote areas are connected to the StarLink satellite system and share information, plans, and the issues discussed by members of the MoH. The ministry is also ready to provide information and send staff to work with the corporation.”
The MoH assigned its Department of Science, Technology, and Training to work with SpaceX. Starlink Vietnam will also receive support from Vietnam’s Department of International Cooperation. Starlink Vietnam’s agenda includes improving internet connectivity for remote healthcare facilities, developing digital infrastructure for health examinations and remote consultations, and enhancing operational systems.
Vietnam’s health sector is prioritizing IT and digital transformation, focusing on electronic health records, data centers, and remote medical services. However, challenges persist in deploying IT solutions in remote regions, prompting Vietnam to seek partnerships like SpaceX’s.
SpaceX’s Starlink has a proven track record in healthcare. In Rwanda, its services supported 40 health centers, earning praise for improving operations. Similarly, Starlink enabled remote consultations at the UAE’s Emirati field hospital in Gaza, streamlining communication for complex medical cases. These successes highlight Starlink’s potential to transform Vietnam’s healthcare landscape.
On May 20, SpaceX met with Vietnam’s Ministry of Industry and Trade, announcing a $1.5 billion investment to provide broadband internet, particularly in remote, border, and island areas. The first phase includes building 10-15 ground stations across the country. This infrastructure will support Starlink’s healthcare initiatives by ensuring reliable connectivity.
Starlink’s expansion in Vietnam aligns with the country’s push for digital transformation, as outlined by the MoH. By leveraging its satellite internet expertise, SpaceX aims to bridge connectivity gaps, enabling advanced healthcare services in underserved regions. This collaboration could redefine Vietnam’s healthcare infrastructure, positioning Starlink as a key player in the nation’s digital future.
-
Elon Musk1 week ago
Tesla investors will be shocked by Jim Cramer’s latest assessment
-
News2 weeks ago
Tesla Robotaxi’s biggest challenge seems to be this one thing
-
News2 weeks ago
Watch the first true Tesla Robotaxi intervention by safety monitor
-
Elon Musk2 weeks ago
A Tesla just delivered itself to a customer autonomously, Elon Musk confirms
-
News2 weeks ago
Tesla Robotaxi rollout proves that Elon Musk still delivers, even if it’s late
-
Elon Musk2 weeks ago
xAI welcomes Memphis pollution results, environmental groups push back
-
Elon Musk2 weeks ago
Elon Musk commends Tesla team on successful Robotaxi launch
-
Elon Musk2 weeks ago
Elon Musk confirms Tesla Optimus V3 already uses Grok voice AI