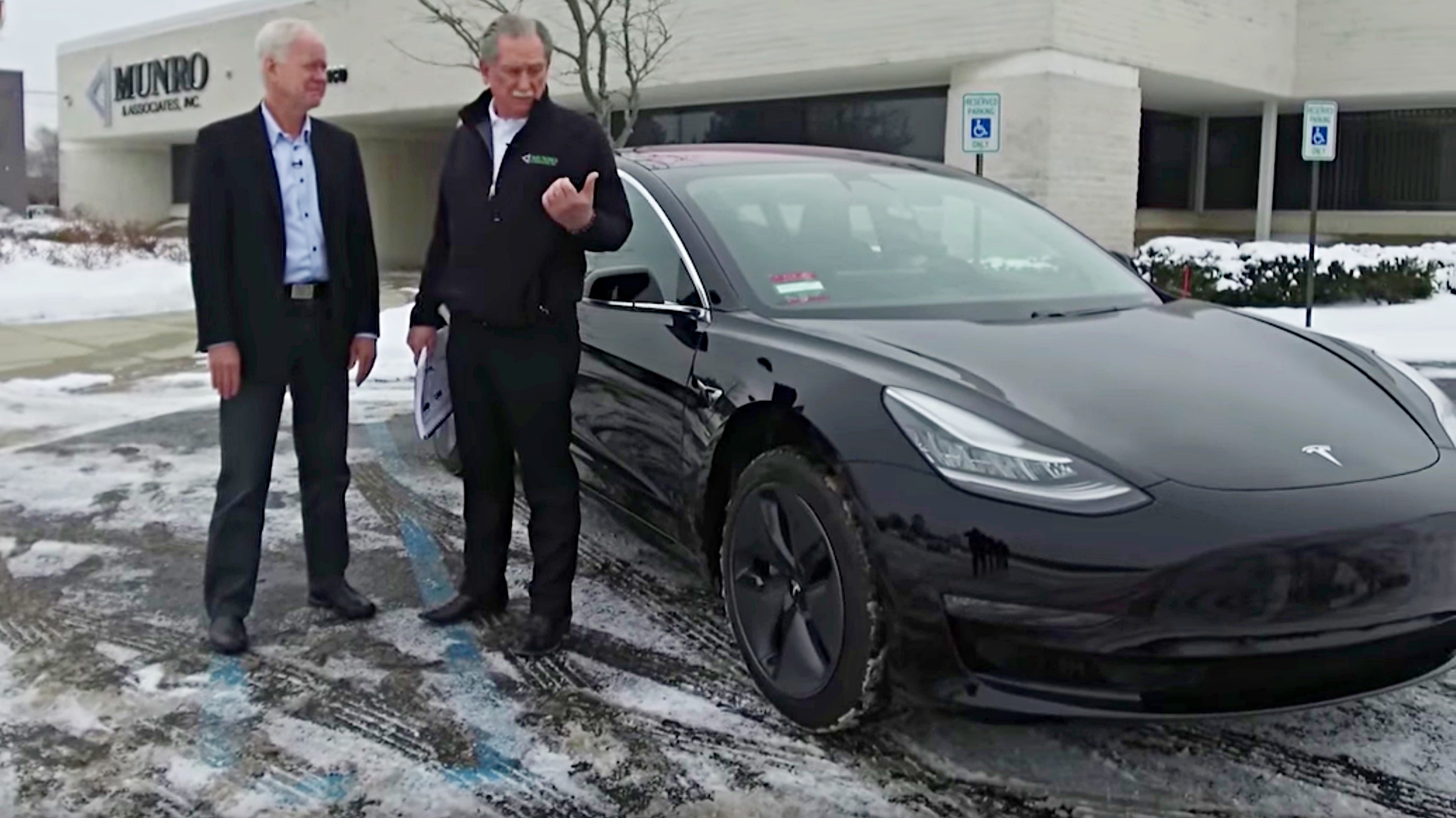
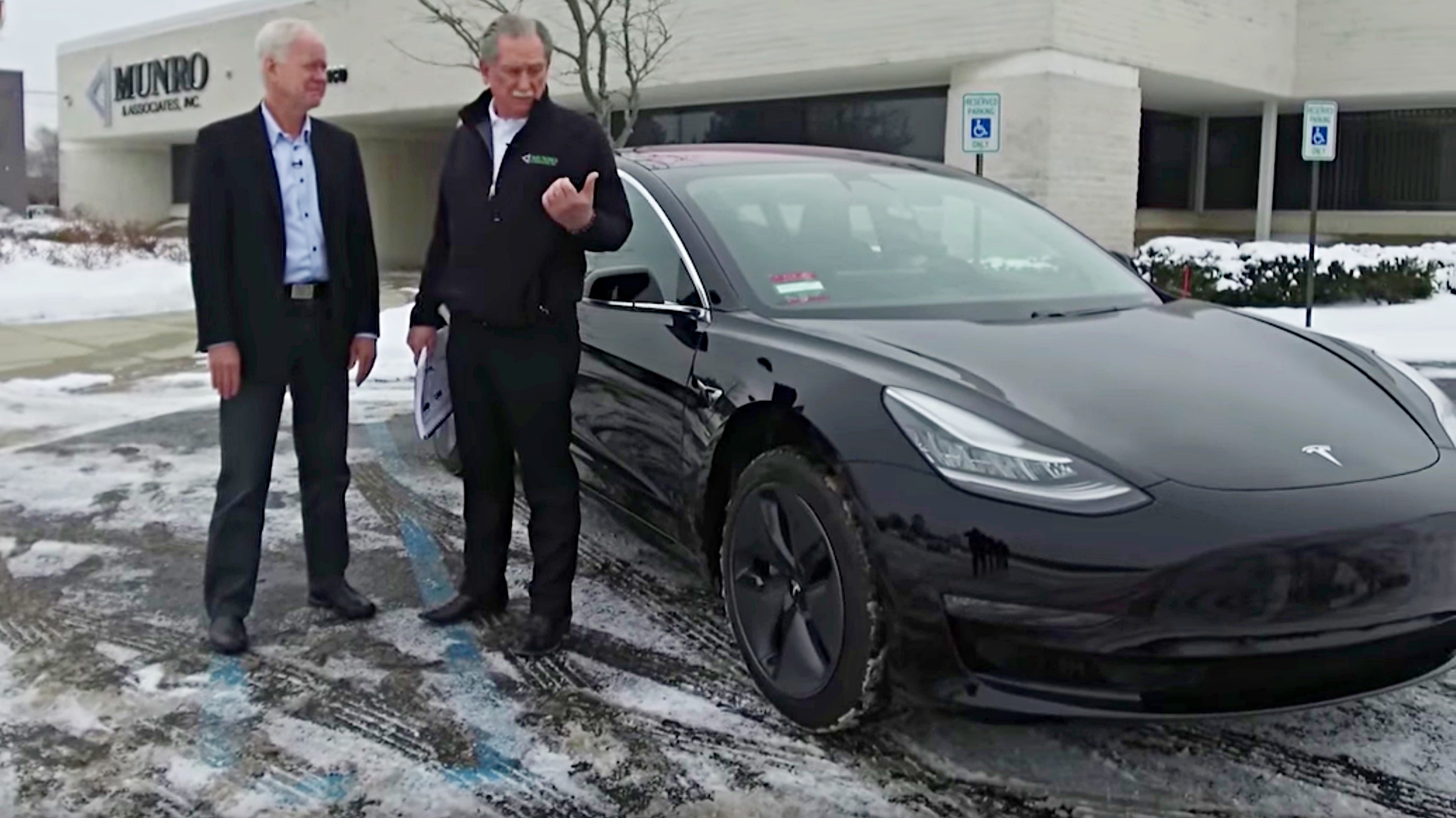
News
Tesla explains Model 3 build in response to Munro’s teardown analysis
Tesla has issued a response to Munro & Associates’ teardown analysis of the Model 3. Over the past couple of months, the teardown company, led by CEO Sandy Munro, has been hard at work probing every aspect of the Model 3, from its design and build quality to its electronics and driving performance. In a recent video, Sandy Munro discussed his company’s findings at length, reiterating his observations since his first Model 3 critique went online last February.
During his first video of the vehicle, Munro, a veteran of the automotive field, took particular issue with the way the Model 3 was assembled. According to the teardown specialist, the electric car was “terrible” in terms of build quality, and several of its design elements, such its lack of physical latches on the rear doors, were deeply flawed. Munro also took particular notice of the Model 3’s panel gaps, which were notable and inconsistent.
As noted in a recent Motor Trend article, Tesla has addressed Munro & Associates’ concerns about the vehicle. According to the Silicon Valley-based electric car company, the Model 3 that Munro analyzed was manufactured in 2017. Since then, Tesla noted that it has improved its production process, and continues to do so. The electric car maker further noted that it has been focusing on making the Model 3’s panel gaps more consistent, resulting in vehicles produced today having a standard deviation that’s comparable to some of the leading automotive brands in the industry today.
“The primary car evaluated by Munro was built in 2017. We have significantly refined our production processes since then, and while there’s always room for improvement, our data already shows that Model 3 quality is rapidly getting better.
Since we began shipping Model 3 last year, we have been very focused on refining and tuning both part and body manufacturing processes. The result being that the standard deviation of all gaps and offsets across the entire car has improved, on average, by nearly 40%, with particular gap improvements visible in the area of the trunk, rear lamps and rear quarter panel. Today, Model 3 panel gaps are competitive with Audi, BMW, and Mercedes models, but in the spirit of relentless improvement, we are working to make them even tighter.”
Apart from the Model 3’s build quality, Sandy Munro also noted in an Autoline After Hours episode that the Model 3’s frame is the heaviest in its class. According to Munro, Tesla could have saved a lot of weight had it followed BMW’s concept with the i3, which used a generous amount of carbon fiber to keep its weight down. In its response, Tesla noted that the car’s construction is key to ensuring the vehicle’s safety.
“The U.S. government found Model S and Model X to have the lowest probability of injury of any cars it had ever tested, and Model 3 was designed with the same commitment to safety. While there’s always room for refinement of cost and mass, which we are already improving, electric cars have unique safety requirements to prevent intrusion into the battery, and Model 3 was also designed to meet the latest small overlap front crash requirements that other reference vehicles may not have.
“We stand behind our physical crash testing and our computer simulations of it, which have been remarkably accurate, and the safety that they demonstrate. The safety of our customers is more important than any other metric.”
While Munro & Associates were critical of the Model 3’s weight and its build, the teardown specialist nonetheless admitted that they were impressed with the way the Model 3 performed on the road. According to Sandy Munro, everything about the Model 3 from its suspension, all the way to its battery pack, are industry-leading, and if Tesla had only ensured that its build quality was as good as its technology, it would have “mopped the floor with everybody.”
News
Tesla cleared in Canada EV rebate investigation
Tesla has been cleared in an investigation into the company’s staggering number of EV rebate claims in Canada in January.
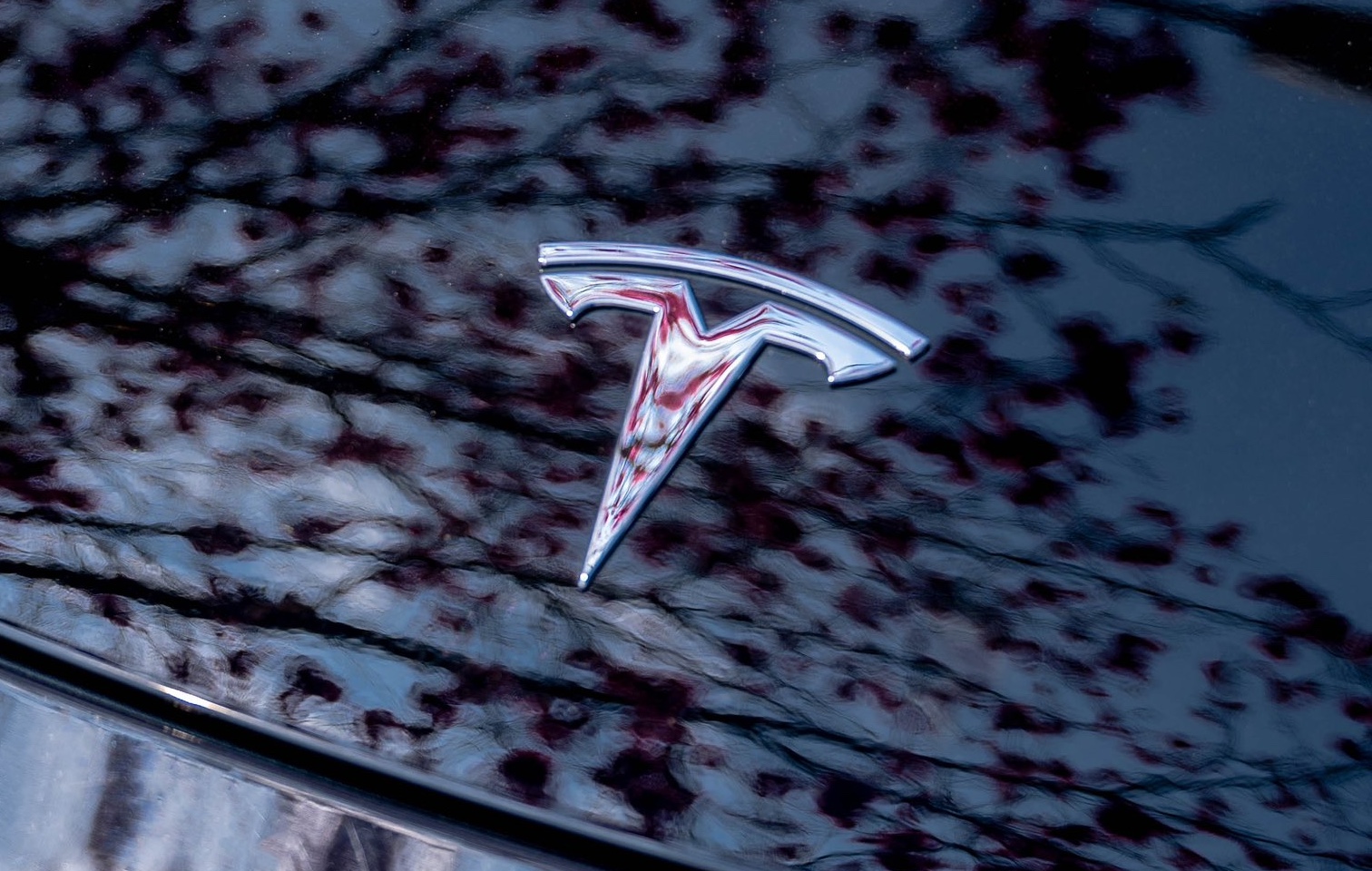
Canadian officials have cleared Tesla following an investigation into a large number of claims submitted to the country’s electric vehicle (EV) rebates earlier this year.
Transport Canada has ruled that there was no evidence of fraud after Tesla submitted 8,653 EV rebate claims for the country’s Incentives for Zero-Emission Vehicles (iZEV) program, as detailed in a report on Friday from The Globe and Mail. Despite the huge number of claims, Canadian authorities have found that the figure represented vehicles that had been delivered prior to the submission deadline for the program.
According to Transport Minister Chrystia Freeland, the claims “were determined to legitimately represent cars sold before January 12,” which was the final day for OEMs to submit these claims before the government suspended the program.
Upon initial reporting of the Tesla claims submitted in January, it was estimated that they were valued at around $43 million. In March, Freeland and Transport Canada opened the investigation into Tesla, noting that they would be freezing the rebate payments until the claims were found to be valid.
READ MORE ON ELECTRIC VEHICLES: EVs getting cleaner more quickly than expected in Europe: study
Huw Williams, Canadian Automobile Dealers Association Public Affairs Director, accepted the results of the investigation, while also questioning how Tesla knew to submit the claims that weekend, just before the program ran out.
“I think there’s a larger question as to how Tesla knew to run those through on that weekend,” Williams said. “It doesn’t appear to me that we have an investigation into any communication between Transport Canada and Tesla, between officials who may have shared information inappropriately.”
Tesla sales have been down in Canada for the first half of this year, amidst turmoil between the country and the Trump administration’s tariffs. Although Elon Musk has since stepped back from his role with the administration, a number of companies and officials in Canada were calling for a boycott of Tesla’s vehicles earlier this year, due in part to his association with Trump.
News
Tesla Semis to get 18 new Megachargers at this PepsiCo plant
PepsiCo is set to add more Tesla Semi Megachargers, this time at a facility in North Carolina.
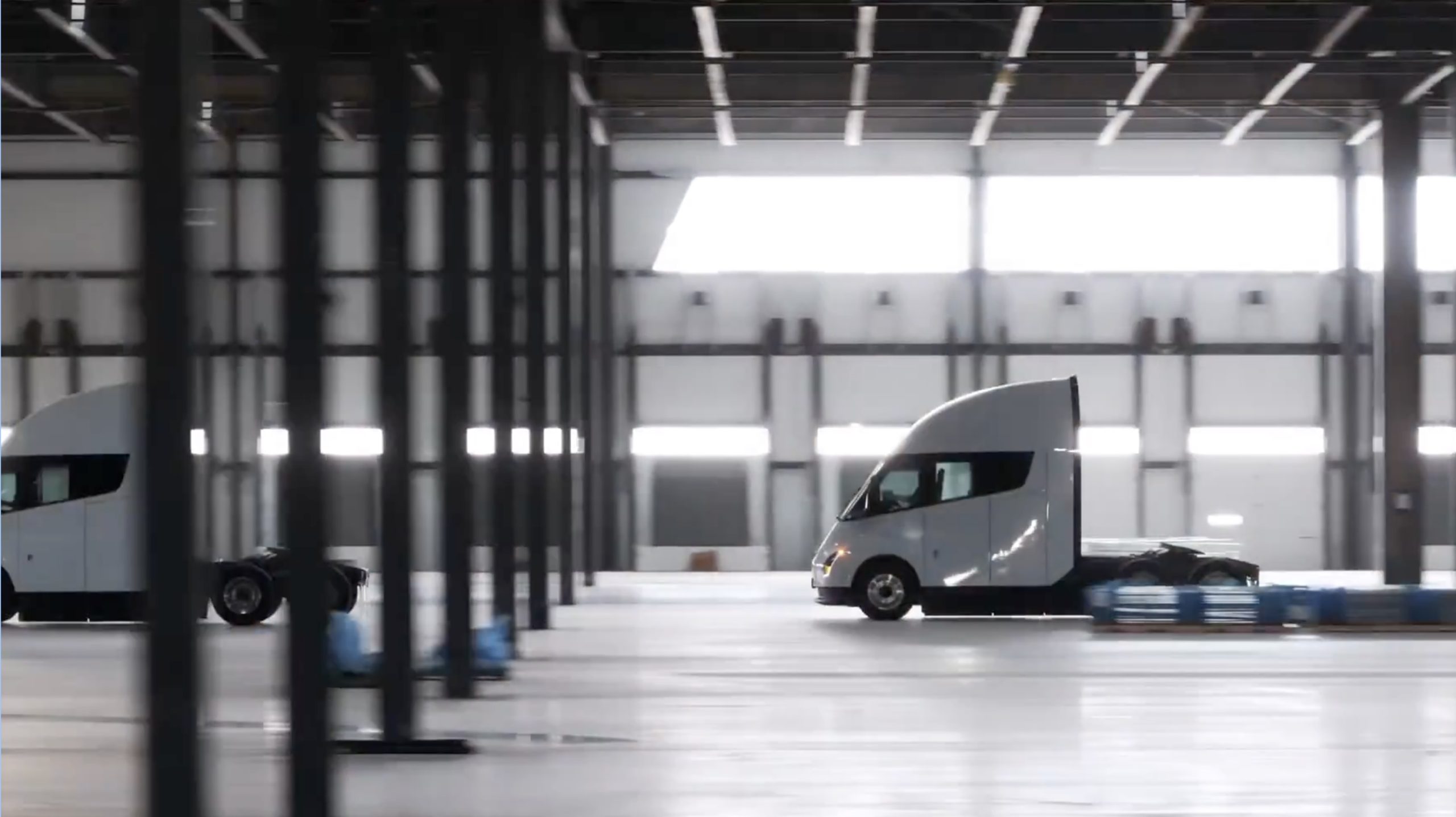
Tesla partner PepsiCo is set to build new Semi charging stations at one of its manufacturing sites, as revealed in new permitting plans shared this week.
On Friday, Tesla charging station scout MarcoRP shared plans on X for 18 Semi Megacharging stalls at PepsiCo’s facility in Charlotte, North Carolina, coming as the latest update plans for the company’s increasingly electrified fleet. The stalls are set to be built side by side, along with three Tesla Megapack grid-scale battery systems.
The plans also note the faster charging speeds for the chargers, which can charge the Class 8 Semi at speeds of up to 1MW. Tesla says that the speed can charge the Semi back to roughly 70 percent in around 30 minutes.
You can see the site plans for the PepsiCo North Carolina Megacharger below.
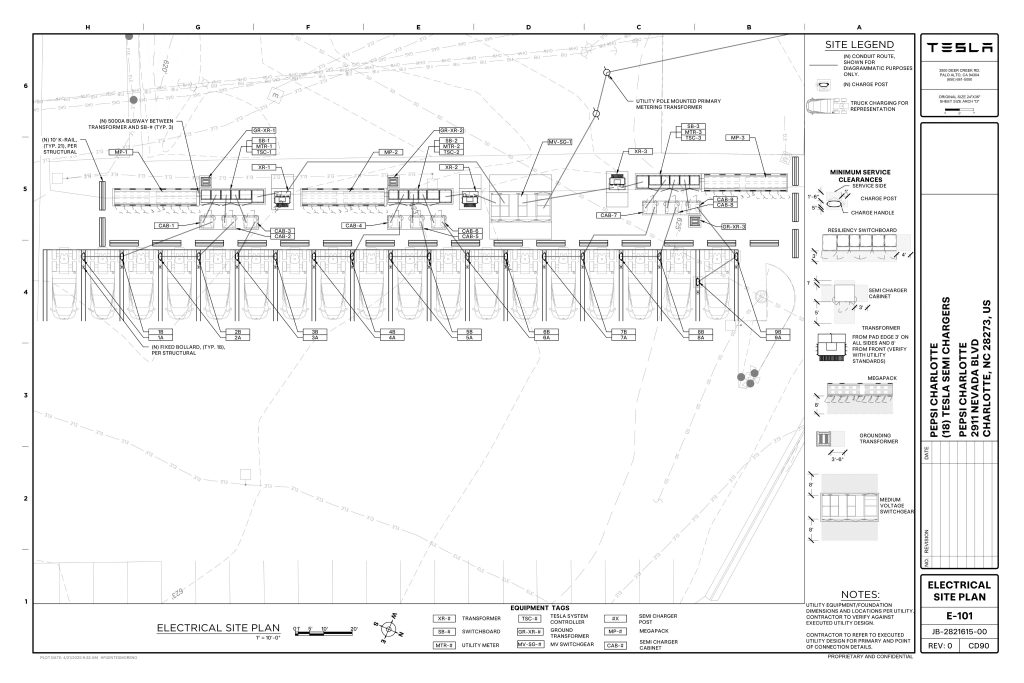
Credit: PepsiCo (via MarcoRPi1 on X)
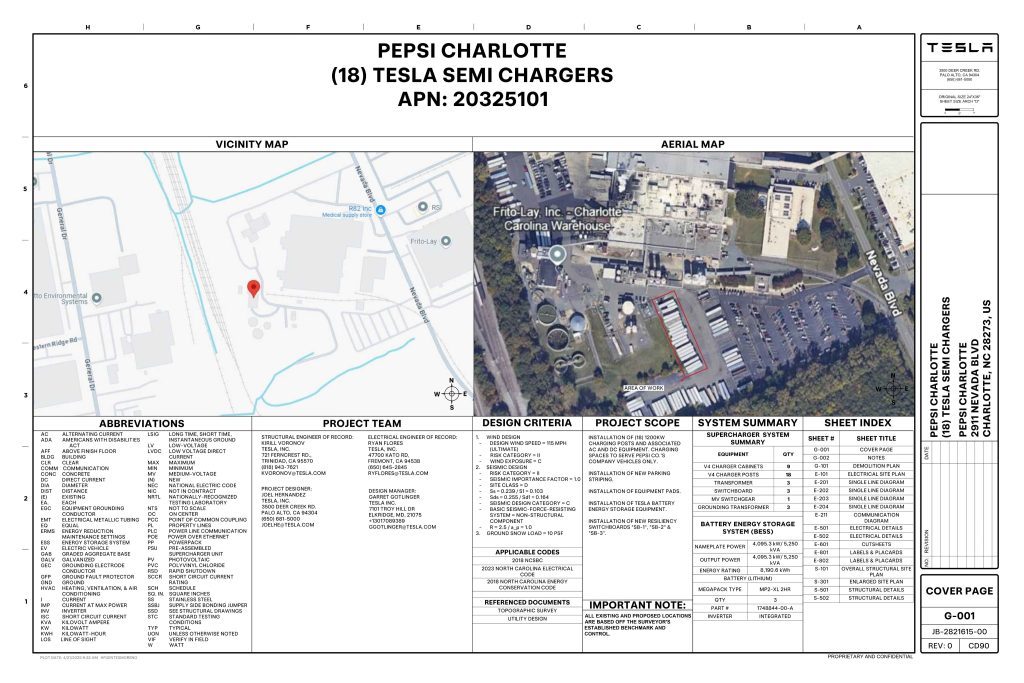
Credit: PepsiCo (via MarcoRPi1 on X)
READ MORE ON THE TESLA SEMI: Tesla to build Semi Megacharger station in Southern California
PepsiCo’s Tesla Semi fleet, other Megachargers, and initial tests and deliveries
PepsiCo was the first external customer to take delivery of Tesla’s Semis back in 2023, starting with just an initial order of 15. Since then, the company has continued to expand the fleet, recently taking delivery of an additional 50 units in California. The PepsiCo fleet was up to around 86 units as of last year, according to statements from Semi Senior Manager Dan Priestley.
Additionally, the company has similar Megachargers at its facilities in Modesto, Sacramento, and Fresno, California, and Tesla also submitted plans for approval to build 12 new Megacharging stalls in Los Angeles County.
Over the past couple of years, Tesla has also been delivering the electric Class 8 units to a number of other companies for pilot programs, and Priestley shared some results from PepsiCo’s initial Semi tests last year. Notably, the executive spoke with a handful of PepsiCo workers who said they really liked the Semi and wouldn’t plan on going back to diesel trucks.
The company is also nearing completion of a higher-volume Semi plant at its Gigafactory in Nevada, which is expected to eventually have an annual production capacity of 50,000 Semi units.
Tesla executive teases plan to further electrify supply chain
News
Tesla sales soar in Norway with new Model Y leading the charge
Tesla recorded a 54% year-over-year jump in new vehicle registrations in June.
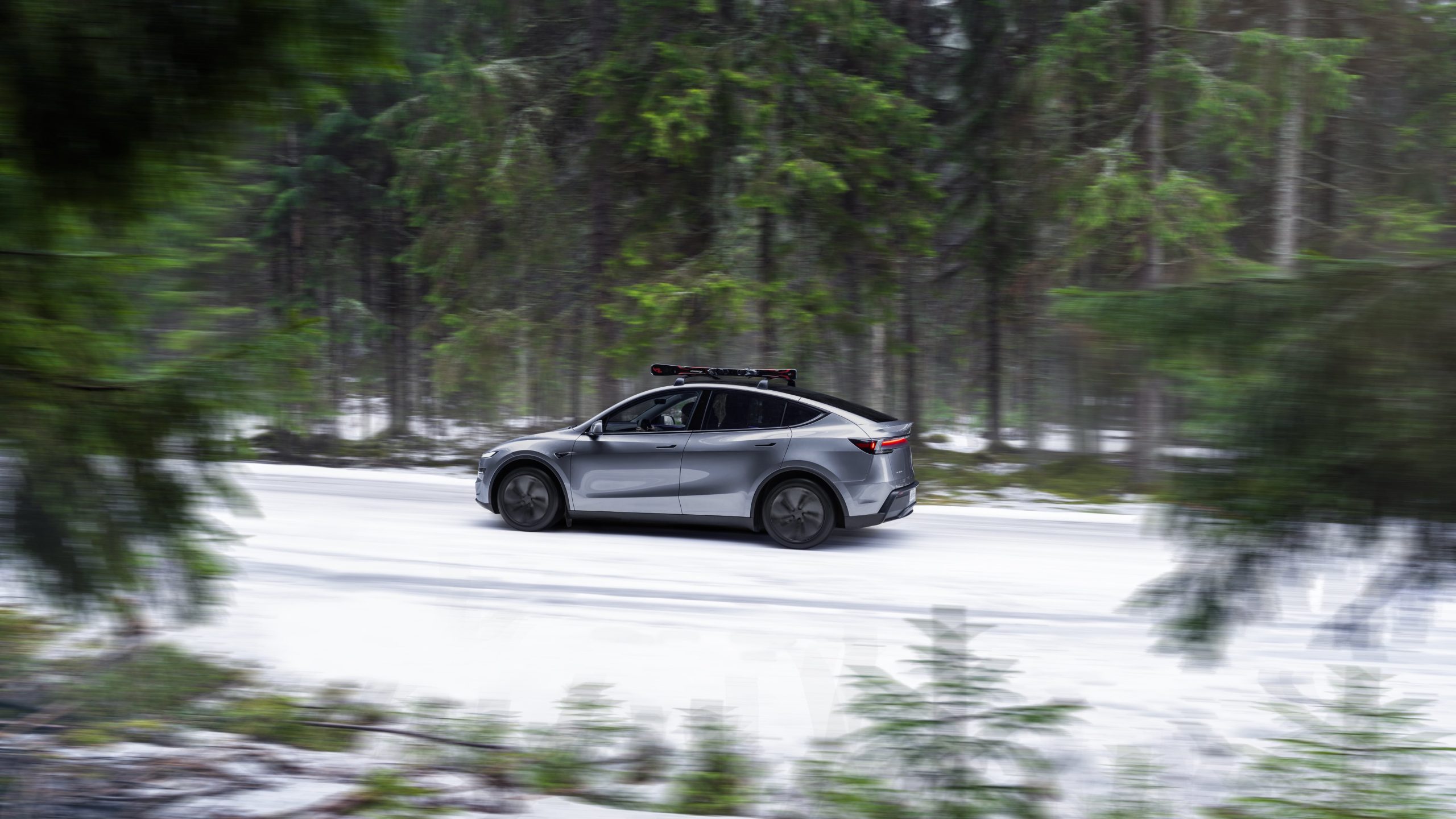
Tesla is seeing strong momentum in Norway, with sales of the new Model Y helping the company maintain dominance in one of the world’s most electric vehicle-friendly markets.
Model Y upgrades and consumer preferences
According to the Norwegian Road Federation (OFV), Tesla recorded a 54% year-over-year jump in new vehicle registrations in June. The Model Y led the charge, posting a 115% increase compared to the same period last year. Tesla Norway’s growth was even more notable in May, with sales surging a whopping 213%, as noted in a CNBC report.
Christina Bu, secretary general of the Norwegian EV Association (NEVA), stated that Tesla’s strong market performance was partly due to the updated Model Y, which is really just a good car, period.
“I think it just has to do with the fact that they deliver a car which has quite a lot of value for money and is what Norwegians need. What Norwegians need, a large luggage space, all wheel drive, and a tow hitch, high ground clearance as well. In addition, quite good digital solutions which people have gotten used to, and also a charging network,” she said.
Tesla in Europe
Tesla’s success in Norway is supported by long-standing government incentives for EV adoption, including exemptions from VAT, road toll discounts, and access to bus lanes. Public and home charging infrastructure is also widely available, making the EV ownership experience in the country very convenient.
Tesla’s performance in Europe is still a mixed bag, with markets like Germany and France still seeing declines in recent months. In areas such as Norway, Spain, and Portugal, however, Tesla’s new car registrations are rising. Spain’s sales rose 61% and Portugal’s sales rose 7% last month. This suggests that regional demand may be stabilizing or rebounding in pockets of Europe.
-
Elon Musk2 weeks ago
Tesla investors will be shocked by Jim Cramer’s latest assessment
-
Elon Musk2 days ago
xAI launches Grok 4 with new $300/month SuperGrok Heavy subscription
-
Elon Musk4 days ago
Elon Musk confirms Grok 4 launch on July 9 with livestream event
-
News1 week ago
Tesla Model 3 ranks as the safest new car in Europe for 2025, per Euro NCAP tests
-
Elon Musk2 weeks ago
A Tesla just delivered itself to a customer autonomously, Elon Musk confirms
-
Elon Musk1 week ago
xAI’s Memphis data center receives air permit despite community criticism
-
News2 weeks ago
Xiaomi CEO congratulates Tesla on first FSD delivery: “We have to continue learning!”
-
News2 weeks ago
Tesla sees explosive sales growth in UK, Spain, and Netherlands in June