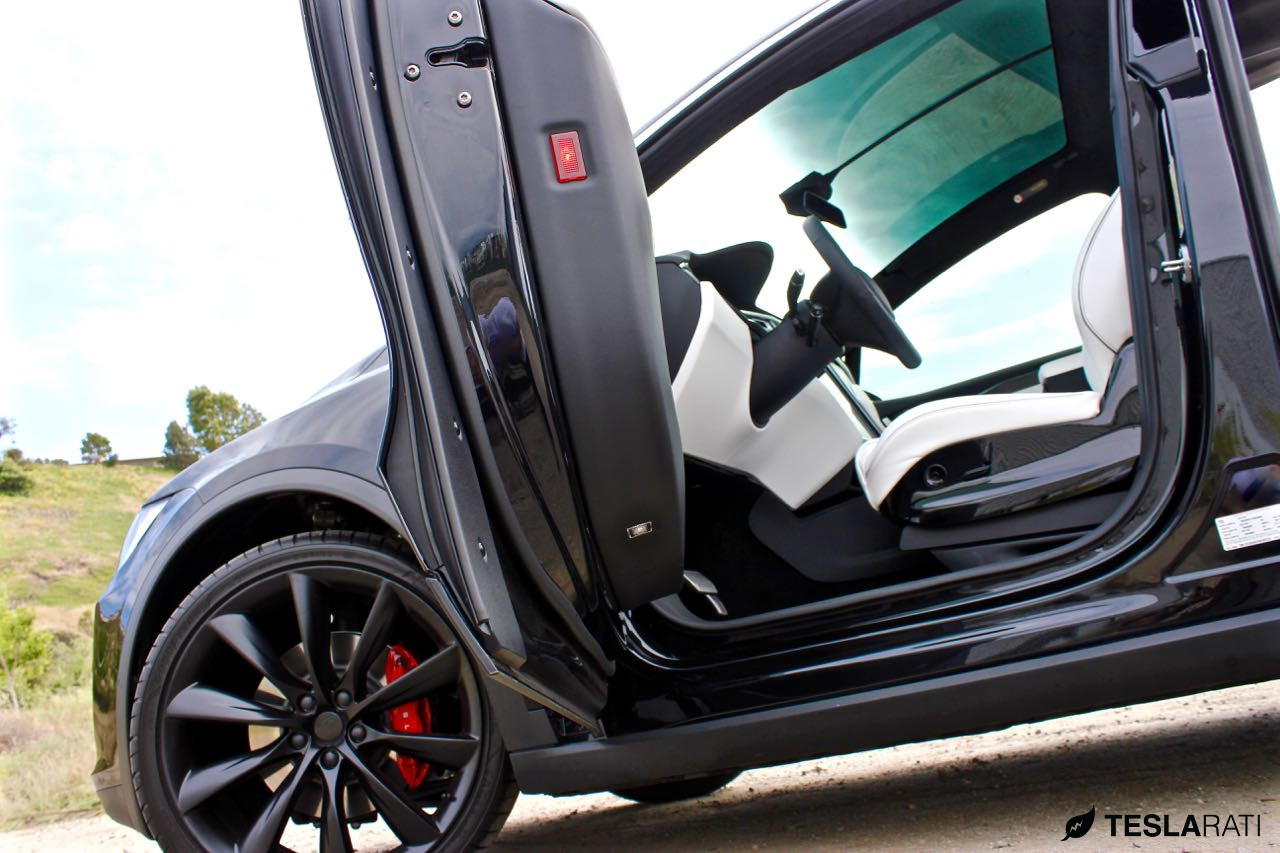
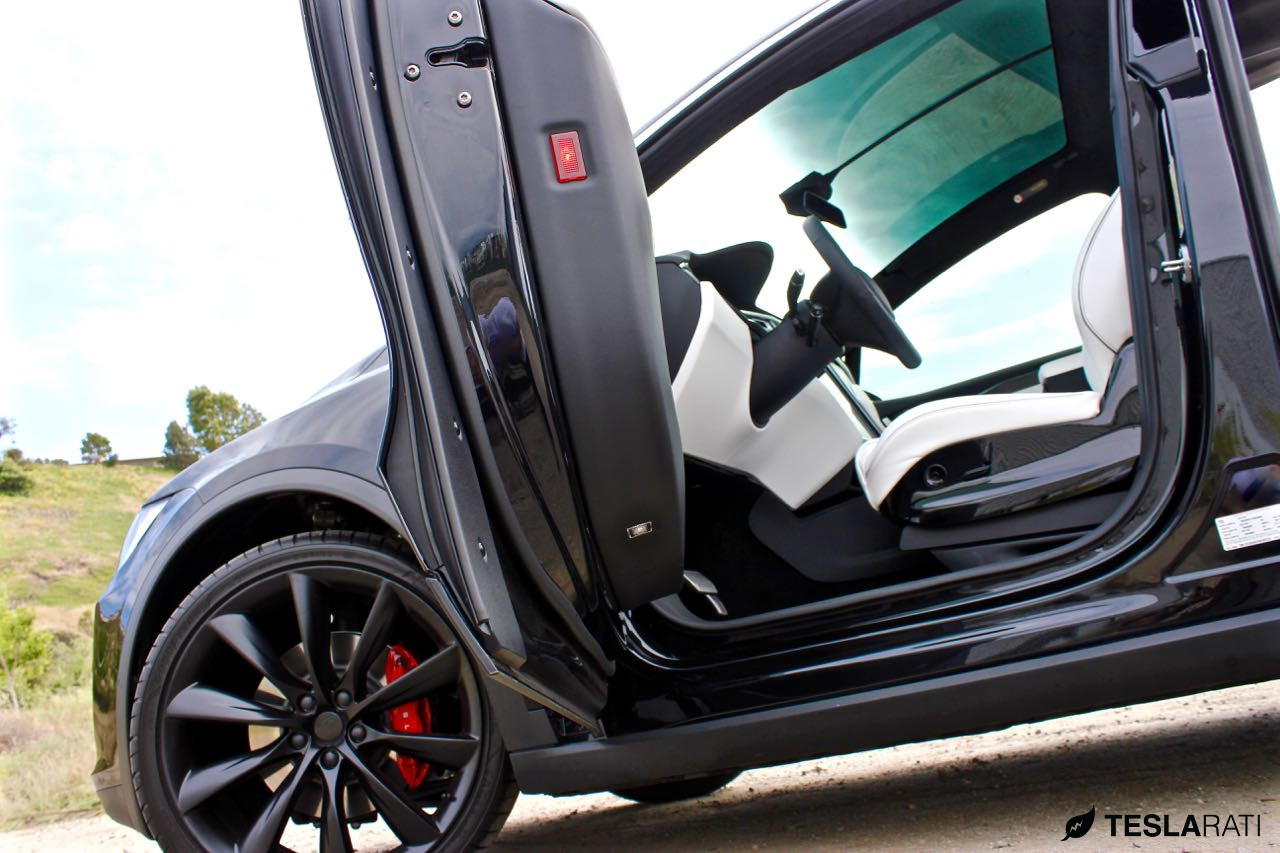
News
Tesla patents ‘fibrous foam architecture’, hinting at new seating material and interior trim to come
Tesla has submitted a patent application for a “fibrous foam architecture” with claims that the manufacturing technique for seats and interior trim would create a more efficient and environmentally-sustainable process.
The submitted patent explains that the current materials used for cushioning in traditional vehicle seats include foam made from polyurethane, a material that is not able to be recycled and may not be the most comfortable due to its lack of breathability. Manufacturing the foam is also a time-consuming and laborious process that involves the pouring and mixing of numerous chemicals, like polymer or epoxy, into a mold. After setting, this requires additional material to be trimmed and shaped, thereby creating unnecessary waste that Tesla’s fibrous foam architecture hopes to eliminate.
The background of the patent states, “Trim to foam assembly may include hog ring, hook and loop, and/or clipping methods. In such methods, alignment tolerances may need to be maintained, mating surface limitations may need to be met, trenches and stitches may need to be provided and so on. Glue application storage and handling may also be required. Current manufacturing processes may be labor-intensive and time-consuming.” This would improve the production and quality of backrests, armrests, leg-rests, and bolsters.
Tesla is looking to improve upon its vehicle’s interior, as it suggests “there is a need for an improved foam architecture and associated manufacturing process that overcome the aforementioned drawbacks.”
An improved foam structure for vehicle seating will provide a new, more comfortable, recyclable material for owners of Tesla electric cars. Tesla plans to use the stacking of multiple layers of different materials to make a less-laborious and more cost-effective seating option. The use of sustainable materials that can be recycled after use will appeal to the environmentally-conscious Tesla owner. The company unveiled 100% cruelty-free seat options in 2017 to its Model S and Model X, and would later offer the 100% vegan material for the Model 3 and the upcoming Model Y.
Tesla has continued to improve its vehicles in every way imaginable for its customers through OTA power updates and accessibility features while finding efficiencies in its design and manufacturing process to support a wider scale-out in production. The company is gearing up for the initial production of the Model Y in early 2020 and the first mass-production of the Model 3 from its Shanghai-based Gigafactory 3. Tesla announced during the Q3 earnings call, “trial production of Model 3 in Shanghai has begun, ahead of schedule. We are also ahead of schedule to produce Model Y and now expect to launch by summer 2020. Model Y equipment installation is underway in advance of the planned launch next year. We are moving faster than initially planned, using learnings and efficiencies gained from our Gigafactory Shanghai factory design.”
As Tesla begins to increase the rate of production of its fleet of vehicles, efficiency is a key factor in creating a lean and cost-effective manufacturing process. Tesla is set to begin production of the Model Y crossover in 2020 and will unveil its highly-anticipated Cybertruck on November 21.
The full details of Tesla’s patent application for a “Fibrous Foam Architecture” can be viewed here.
News
These Tesla, X, and xAI engineers were just poached by OpenAI
The news is the latest in an ongoing feud between Elon Musk and the Sam Altman-run firm OpenAI.
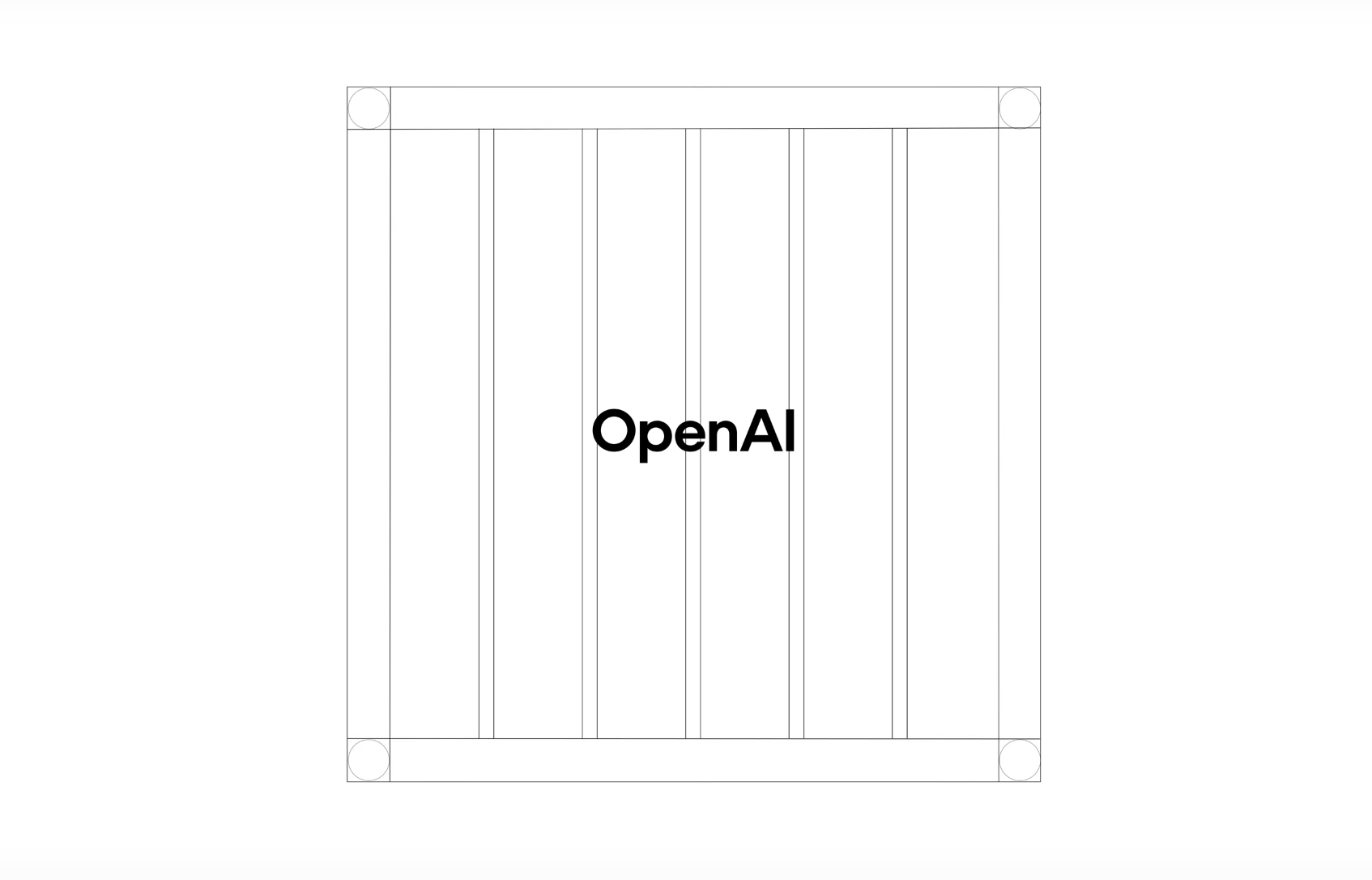
OpenAI, the xAI competitor for which Elon Musk previously served as a boardmember and helped to co-found, has reportedly poached high-level engineers from Tesla, along with others from xAI, X, and still others.
On Tuesday, Wired reported that OpenAI hired four high-level engineers from Tesla, xAI, and X, as seen in an internal Slack message sent by co-founder Greg Brockman. The engineers include Tesla Vice President of Software Engineering David Lau, X and xAI’s head of infrastructure engineering Uday Ruddarraju, and fellow xAI infrastructure engineer Mike Dalton. The hiring spree also included Angela Fan, an AI researcher from Meta.
“We’re excited to welcome these new members to our scaling team,” said Hannah Wong, an OpenAI spokesperson. “Our approach is to continue building and bringing together world-class infrastructure, research, and product teams to accelerate our mission and deliver the benefits of AI to hundreds of millions of people.”
Lau has been in his position as Tesla’s VP of Software Engineering since 2017, after previously working for the company’s firmware, platforms, and system integration divisions.
“It has become incredibly clear to me that accelerating progress towards safe, well-aligned artificial general intelligence is the most rewarding mission I could imagine for the next chapter of my career,” Lau said in a statement to Wired.
🚨Optimistic projections point to xAI possibly attaining profitability by 2027, according to Bloomberg's sources.
If accurate, this would be quite a feat for xAI. OpenAI, its biggest rival, is still looking at 2029 as the year it could become cash flow positive.💰 https://t.co/pE5Z9daez8
— TESLARATI (@Teslarati) June 18, 2025
READ MORE ON OPENAI: Elon Musk’s OpenAI lawsuit clears hurdle as trial looms
At xAI, Ruddarraju and Dalton both played a large role in developing the Colossus supercomputer, which is comprised of over 200,000 GPUs. One of the major ongoing projects at OpenAI is the company’s Stargate program,
“Infrastructure is where research meets reality, and OpenAI has already demonstrated this successfully,” Ruddarraju told Wired in another statement. “Stargate, in particular, is an infrastructure moonshot that perfectly matches the ambitious, systems-level challenges I love taking on.”
Elon Musk is currently in the process of suing OpenAI for shifting toward a for-profit model, as well as for accepting an investment of billions of dollars from Microsoft. OpenAI retaliated with a counterlawsuit, in which it alleges that Musk is interfering with the company’s business and engaging in unfair competition practices.
Elon Musk confirms Grok 4 launch on July 9 with livestream event
News
SpaceX share sale expected to back $400 billion valuation
The new SpaceX valuation would represent yet another record-high as far as privately-held companies in the U.S. go.
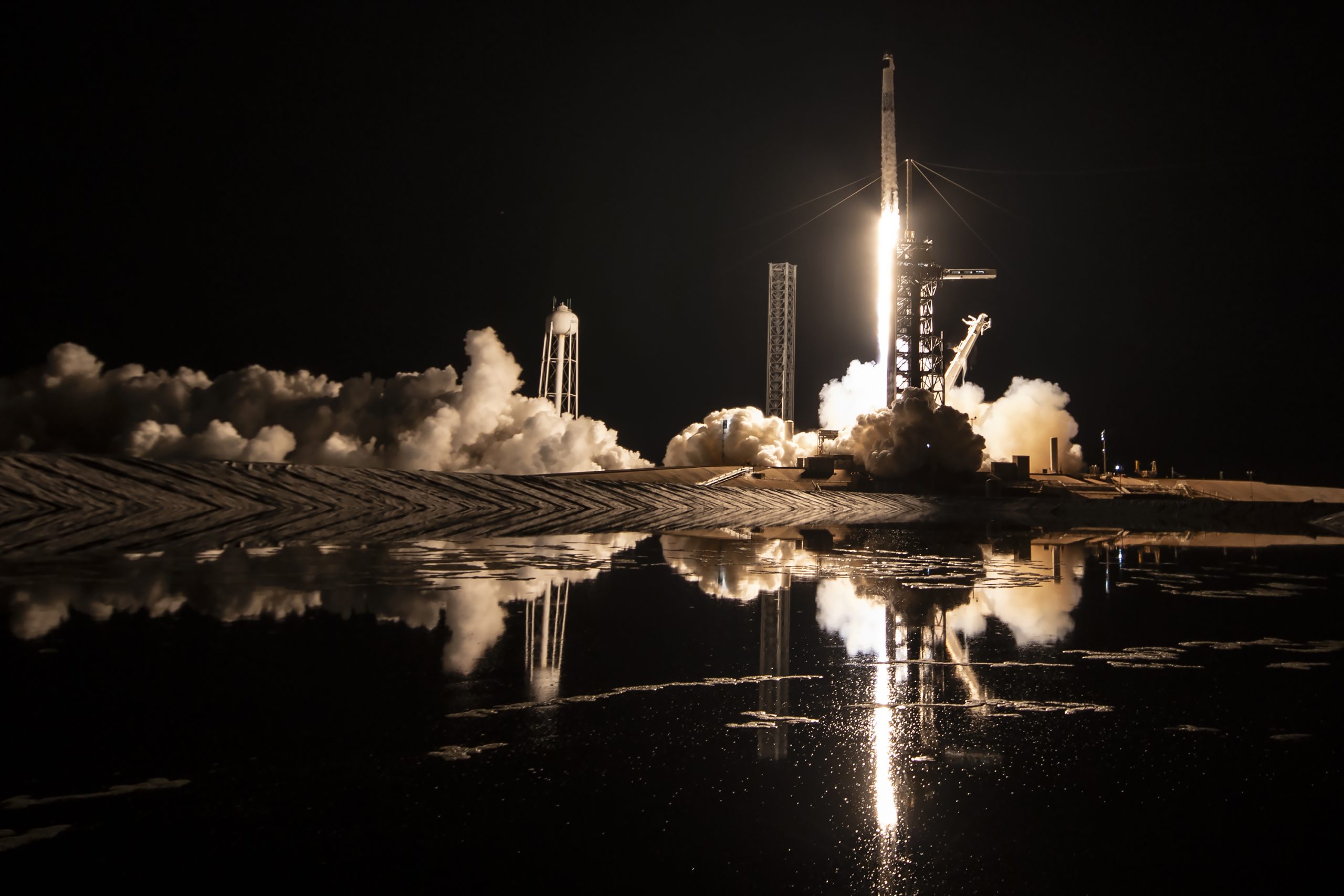
A new report this week suggests that Elon Musk-led rocket company SpaceX is considering an insider share sale that would value the company at $400 billion.
SpaceX is set to launch a primary fundraising round and sell a small number of new shares to investors, according to the report from Bloomberg, which cited people familiar with the matter who asked to remain anonymous due to the information not yet being public. Additionally, the company would sell shares from employees and early investors in a follow-up round, while the primary round would determine the price for the secondary round.
The valuation would represent the largest in history from a privately-owned company in the U.S., surpassing SpaceX’s previous record of $350 billion after a share buyback in December. Rivaling company valuations include ByteDance, the parent company of TikTok, as well as OpenAI.
Bloomberg went on to say that a SpaceX representative didn’t respond to a request for comment at the time of publishing. The publication also notes that the details of such a deal could still change, especially depending on interest from the insider sellers and share buyers.
Axiom’s Ax-4 astronauts arriving to the ISS! https://t.co/WQtTODaYfj
— TESLARATI (@Teslarati) June 26, 2025
READ MORE ON SPACEX: SpaceX to decommission Dragon spacecraft in response to Pres. Trump war of words with Elon Musk
SpaceX’s valuation comes from a few different key factors, especially including the continued expansion of the company’s Starlink satellite internet company. According to the report, Starlink accounts for over half of the company’s yearly revenue. Meanwhile, the company produced its 10 millionth Starlink kit last month.
The company also continues to develop its Starship reusable rocket program, despite the company experiencing an explosion of the rocket on the test stand in Texas last month.
The company has also launched payloads for a number of companies and government contracts. In recent weeks, SpaceX launched Axiom’s Ax-4 mission, sending four astronauts to the International Space Station (ISS) for a 14-day stay to work on around 60 scientific experiments. The mission was launched using the SpaceX Falcon 9 rocket and a new Crew Dragon capsule, while the research is expected to span a range of fields including biology, material and physical sciences, and demonstrations of specialized technology.
News
Tesla Giga Texas continues to pile up with Cybercab castings
Tesla sure is gathering a lot of Cybercab components around the Giga Texas complex.
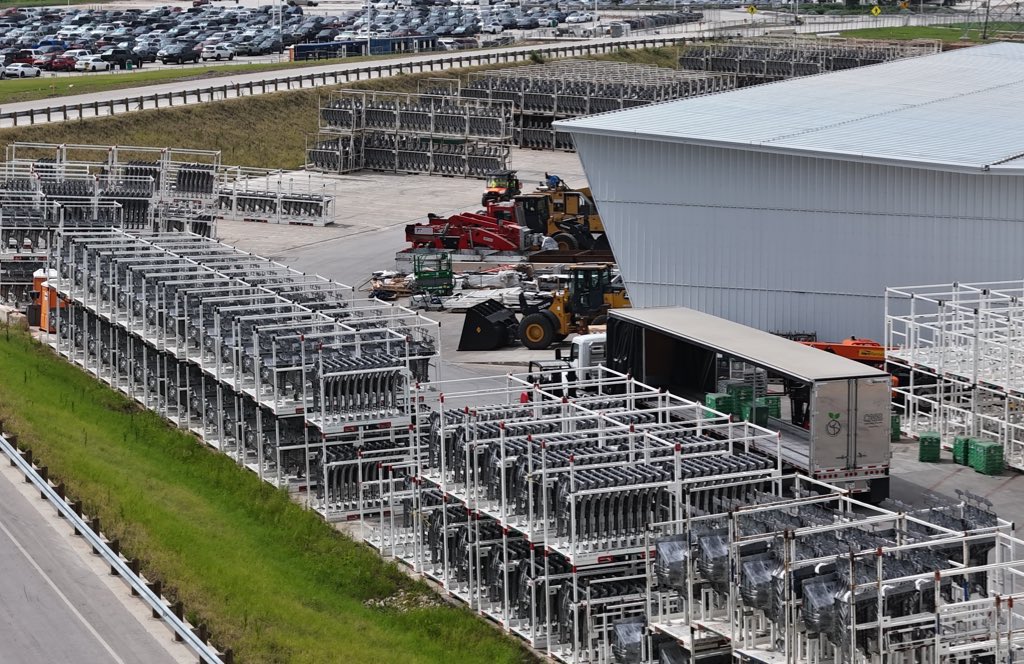
Tesla may be extremely tight-lipped about the new affordable models that it was expected to start producing in the first half of the year, but the company sure is gathering a lot of Cybercab castings around the Giga Texas complex. This is, at least, as per recent images taken of the facility.
Cybercab castings galore
As per longtime drone operator Joe Tegtmeyer, who has been chronicling the developments around the Giga Texas complex for several years now, the electric vehicle maker seems to be gathering hundreds of Cybercab castings around the factory.
Based on observations from industry watchers, the drone operator appears to have captured images of about 180 front and 180 rear Cybercab castings in his recent photos.
Considering the number of castings that were spotted around Giga Texas, it would appear that Tesla may indeed be preparing for the vehicle’s start of trial production sometime later this year. Interestingly enough, large numbers of Cybercab castings have been spotted around the Giga Texas complex in the past few months.
Cybercab production
The Cybercab is expected to be Tesla’s first vehicle that will adopt the company’s “unboxed” process. As per Tesla’s previous update letters, volume production of the Cybercab should start in 2026. So far, prototypes of the Cybercab have been spotted testing around Giga Texas, and expectations are high that the vehicle’s initial trial production should start this year.
With the start of Tesla’s dedicated Robotaxi service around Austin, it might only be a matter of time before the Cybercab starts being tested on public roads as well. When this happens, it would be very difficult to deny the fact that Tesla really does have a safe, working autonomous driving system, and it has the perfect vehicle for it, too.
-
Elon Musk1 week ago
Tesla investors will be shocked by Jim Cramer’s latest assessment
-
News2 weeks ago
Tesla Robotaxi’s biggest challenge seems to be this one thing
-
Elon Musk1 day ago
Elon Musk confirms Grok 4 launch on July 9 with livestream event
-
News2 weeks ago
Watch the first true Tesla Robotaxi intervention by safety monitor
-
News5 days ago
Tesla Model 3 ranks as the safest new car in Europe for 2025, per Euro NCAP tests
-
Elon Musk2 weeks ago
A Tesla just delivered itself to a customer autonomously, Elon Musk confirms
-
Elon Musk2 weeks ago
Elon Musk confirms Tesla Optimus V3 already uses Grok voice AI
-
Elon Musk2 weeks ago
xAI welcomes Memphis pollution results, environmental groups push back